Article Information
- Digital Object Identifier (DOI): 10.47982/cgc.9. 650
- Published by Challenging Glass, on behalf of the author(s), at Stichting OpenAccess.
- Published as part of the peer-reviewed Challenging Glass Conference Proceedings, Volume 9, June 2024, 10.47982/cgc.9
- Editors: Christian Louter, Freek Bos & Jan Belis
- This work is licensed under a Creative Commons Attribution 4.0 International (CC BY 4.0) license.
- Copyright © 2024 with the author(s)
Authors:
- Andreas Komm - seele GmbH, Germany
- Markus Bruckner - seele GmbH, Germany
- Anna-Maria Heinz - seele GmbH, Germany
Abstract
The organic design and seamlessly reflective surface of “The Henderson” establish it as a landmark in Hong Kong. With its all-glass façade and a height of 210 m, the skyscraper designed by Zaha Hadid Architects offers spectacular panoramic views. Particularly noteworthy is the “Banquet Hall” on the top floor, distinguished by its fully glazed roof and engineered by Eckersley O’Callaghan. Large-format, coated and curved glass panes with the best possible technical specification in terms of thickness and minimal dimensional tolerances counterbalance architectural aesthetics and structural resilience. Engineered, manufactured and installed by seele, they serve as effective shields against solar radiation and glare, seamlessly complementing the organic architecture. Collaborative efforts focused on maximizing the transparency of the building envelope as interdisciplinary teams navigated challenges in structural engineering, design aesthetics and compliance with strict regulatory standards of the building authorities in Hong Kong. Thanks to targeted investigations, advancements in glass construction technology and engineering innovation, a procedure was developed that ensured optimum bearing of the panoramic glass panes. This project contributes to the safety and durability of high-rise glass structures to withstand extreme conditions and showcases the transformative potential of bold design concepts, rigorous testing, and international collaboration. The result is a visually stunning and structurally outstanding masterpiece.
1.General
Hong Kong's skyline is characterised by high-rise buildings due to the high population density and the limited amount of buildable space in the metropolis. However, one new building stands out: with a height of 190 m and 39 storeys, “The Henderson” finds its place next to some of the most remarkable skyscrapers in the architecture world – the new construction becomes an “icon among icons”.
Zaha Hadid Architects designed the office building as a homage to the Bauhinia x blakeana, known as the Hong Kong orchid, whose five-petalled flower adorns the flag of the Special Administrative Region. Consequently, rounded, organic shapes characterise the architecture of “The Henderson”. They are extend on the building envelope.
seele was responsible for the design, manufacturing and installation of the façade on floors 0 to 5 as well as 37 and 38. The structural design for the top of the tower, the so-called “Banquet Hall”, was carried out in collaboration with Eckersley O'Callaghan. This area in particular required maximum transparency in order to provide visitors with a spectacular view of Hong Kong.
For this reason, seele developed an 883 sqm all-glass construction for the façade and the roof consisting of 167 curved roof panes. “The Henderson” not only fulfils an aesthetic, representative purpose as an architectural icon in the financial district, but also has to meet the strict requirements of the local building authorities with regard to the structural integrity of the building in a typhoon-prone climate.
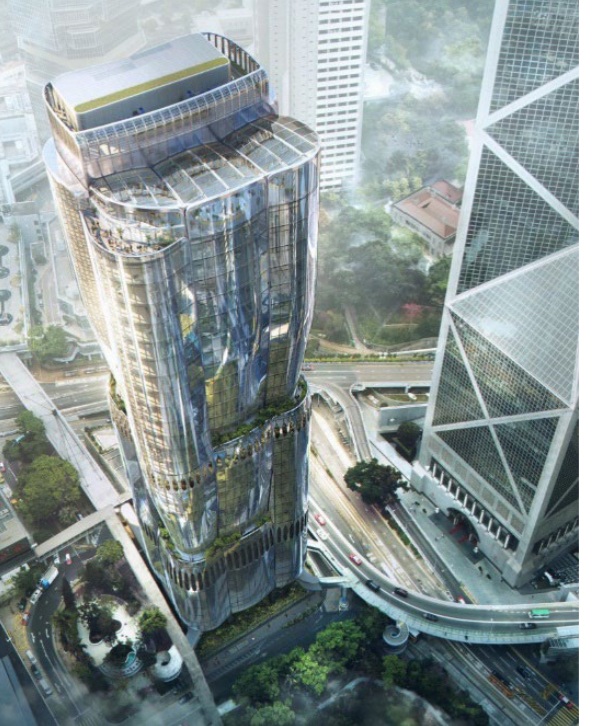
2. Structural Design
The building envelope of the “Banquet Hall” is divided into three distinct sections: the roof, the surrounding façade and the door systems providing access to the outdoor area. The roof structure consists of 123 insulated glass units (IGU) panes supported by 119 glass fins, spanning a total area of 545 sqm. The vertical façade, covering an area of 437 sqm, consists of 26 façade panes and the terrace door glazing of 18 glass units.
2.1. Wind Loads
Given the skyscrapers location in a typhoon-prone area, meticulous attention was devoted to assessing potential wind loads on the structure. Cermak Peterka Petersen Wind Engineering and Air Quality Consultants conducted a comprehensive wind assessment in a wind tunnel (Fig. 2), considering the surrounding area within a radius of 570 m. The turnable model is a development of appropriate boundary layer profiles in accordance with the “Code of Practice on Wind Effects in Hong Kong” (Hong Kong Buildings Department 2004). The assessment resulted in a maximum load of 6.9 kN/sqm along the roof edge and an average load of 4.5 kN/sqm across the roof and façade.
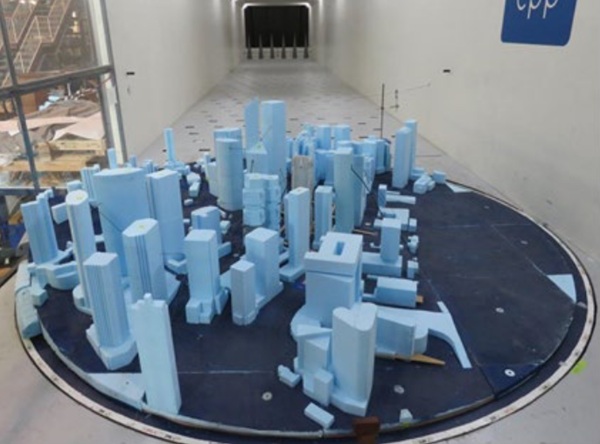
2.2. Bearing of the Roof Panes
The structural engineers determined the load sharing between the panes of an IGU by their relative stiffness. In order to take into account internal pressure changes within the cavity, the wind load on each pane is increased by 25%. The uniformly distributed live load is distributed between the outer and inner glass pane. The outer glass panes bear the concentrated live load (Fig. 3).
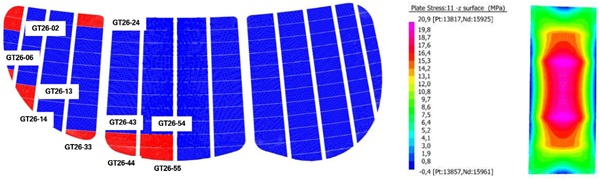
2.3. Bearing of the Glass Fins
All roof glass panels are linearly supported at all edges, resting on steel beams on the short sides and on glass fins on the long sides. The fins are designed for dead load, wind loads and roof live loads. The live loads are for maintenance use only. Figure 4 (Fig. 4) shows the structural model for the roof fins. The model includes all fins. The fins are modelled with beam elements, and they are supported by nodal supports (fixed in all directions) at both ends.
The glass fins have moment releases around the major and minor axis at both ends. The torsional rotation is fixed. Depending on the roof geometry, all glass fins have a deep and a high end. The deep ends are fixed in all local translational direction. The high ends have a release in the local axial direction.
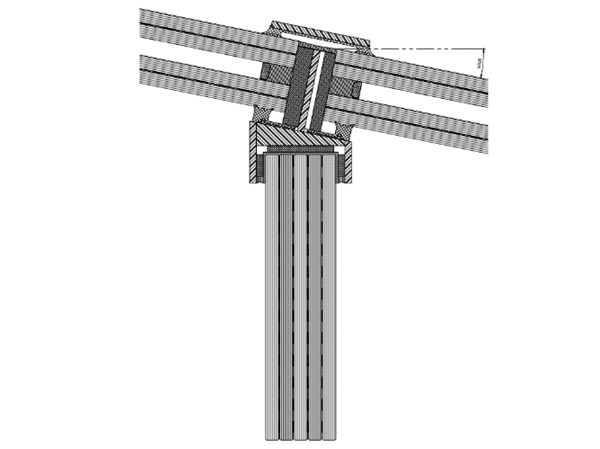
3. Glass Design
3.1. Vertical Façade
The vertical façade of the “Banquet Hall” consists of a glass door system and 36 cylindrically curved glass panes measuring 7.6 m x 2.1 m. Most of these are 6-pane laminates made of toughened heat-soaked safety glass. The particularly strict regulations of the building authorities in Hong Kong became apparent here, as 50% of the toughened safety glass panes had to be subjected to the heat soak procedure under external supervision by an authorized inspection body.
Despite their size and the high wind loads on the top floor, the façade panes are only supported on the two short sides, at the top and bottom, in order to achieve an organic shape and a design that is as seamless as possible. For this reason, seele fitted the glass panes at the factory with stainless steel profiles at the top and bottom using SG silicone adhesive. The high degree of prefabrication meant that the geometries of the cylindrically curved façade panes and 3D-moulded stainless steel profiles could be perfectly matched. The profiles were welded from sheet metal using templates.
The vertical façade is fully coated with Reflective Coating 20% Silverstar Sunstop NSP 50T as solar protection and an anti-reflective coating Luxar F on the inside.
3.2. Glass Roof
The roof of “The Henderson” was crafted with an all-glass construction, featuring 123 cylindrically curved glass panes, each delicately supported on four sides by a total of 119 glass fins. Each pane is 3.6 m long, 1.4 m wide, with a build-up of 2 x 12 mm + 16 + 2 x 12 mm with SG interlayer. In total, the insulated roof glazing spans an area of 545 sqm.
These roof panes, owing to their smaller dimensions and robust framing along all edges, as well as the reduced wind loads experienced compared to the façade, are engineered to be thinner at 67 mm.
Similar to the façade panes, the roof panes are coated for solar control and anti-reflection properties. Additionally, a dark grey dot pattern is incorporated between the second and third glass layer to improve solar control. This pattern is directly printed on the interlayer.
3.4 m long glass fins support the insulating glass panes of the roof. The glass fins are made from 5 layers of 12 mm thick, fully tempered flat glass.
4. Testing
To facilitate global acceptance of products and services across national borders, the International Laboratory Accreditation Cooperation (ILAC) harmonizes existing Mutual Recognition Arrangements (MRAs) among Recognised Regional Cooperation Bodies. Leveraging this framework, seele conducted testing of components destined for installation in Hong Kong at its own testing facility in Gersthofen, Germany. The functionality of the unique façade construction (Fig. 5) was validated with two full-scale Performance Mock-Ups (PMUs). seele conducted the following test program:
- Air permeability test
- Water penetration test
- Structural performance test
- Pendulum impact test
- Hurricane test
The tests, which are particularly important for overhead glazing in special constructions, were carried out in accordance with the specifications of Technical Note 66: ‘Safety and fragility of roof glazing: Guidance on Specification’ issued by the Centre for Window and Cladding Technology (CWCT TN 66). When testing the wind resistance of the roof, for example, a characteristic wind pressure of 100% was applied at +4.41 kN/sqm for the positive test and -6.93 kN/sqm for the negative test. When testing the structural performance, loads of up to 150% of the specified values were applied.
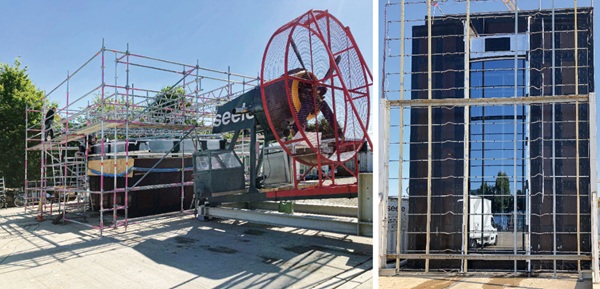
5. Glass Fabrication
sedak (in Gersthofen, Germany) manufactured both the façade glass and the IGU roof glass. For “The Henderson” project, the majority of the glass underwent thermal bending (Fig. 6). sedak’s advanced furnaces enable bending and tempering along one, two, or three axes within a single production cycle. Specifically for this project, sedak bent double-curved glass within a furnace equipped to handle double curved and spherical bent tempered glasses with dimensions up to 6.5 m x 3.6 m.
In the process of bending tempered and heat-strengthened glass, the initial step involves heating the flat glass pane and shaping it into a curved form by rolling it on a bed of rollers before subjecting it to thermal toughening. The specific curvature of each pane is determined by the configuration of the rollers, which are mounted on flexible shafts. For instance, the tower's top façade comprises double-curved hot-bent glass panes, some up to 7.6 m long, while single-curvature bent glass panes are used on the roof. These components, along with glass beams, integrate delicately into the steel structure provided by others to withstand high wind loads, necessitating 6-ply laminated glass. Meanwhile, the entrance area features an all-glass façade reaching heights of up to 11 m, composed of glass laminates up to 7 x 15 mm thick. To ensure quality control, all panels underwent optical 3D laser scanning. This involves full 3D scanning of each glass panel produced and comparing it to the 3D CAD Model. This meticulous approach underscores the commitment to achieving the highest production quality for over 650 double and cylindrical curved panels, incorporating various coatings to achieve the desired visual appearance both from the inside or outside.
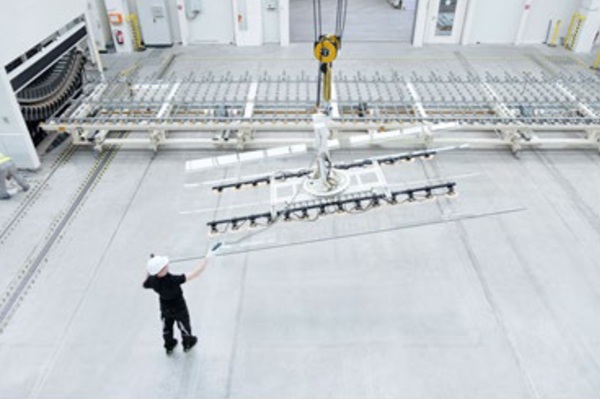
6. Installation
An interim storage facility served as a crucial node in the supply chain, facilitating just-in-time delivery of the glass panes and essential materials to the construction site amidst the densely built-up urban landscape. This strategic approach ensured streamlined construction logistics, enabling efficient progress despite the challenging environment.
seele installed the components at a height of 200 m above ground (Fig. 7). The glass panes weighing up to 3 t were lifted to the tower top in transport crates. The precision required for this operation mandated low wind speeds, necessitating careful scheduling to ensure optimal conditions.
Once at the top, seele installation personnel placed and installed the glass panels. Special attention was required during the installation phase following the disassembly of the tower crane. At this stage, the building maintenance unit (BMU) took over the lifting and installation duties. Remarkably, the time taken for the BMU to transport materials from the ground floor to the tower top was only 10 min., under-scoring the effectiveness of this approach in expediting construction activities at height.
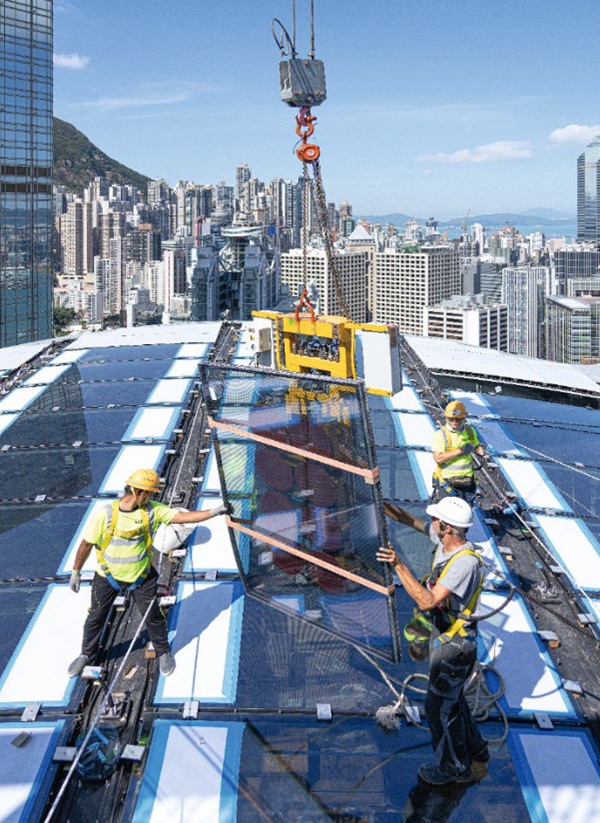
7. Conclusion
With its iconic facade, “The Henderson” ascends into the Hong Kong sky with “Banquet Hall” serving as the crowning highlight of this remarkable new structure. Positioned around 200 m above ground level, the facade, characterized by its slim joints, offers visitors an awe-inspiring panorama of the city's skyline. Additionally, the glass roof construction ensures an unobstructed view of the sky (Fig. 8).
The realization of Zaha Hadid Architects' design, distinguished by its organically curved shapes and maximum transparency, demanded the utmost precision in both construction and production processes, meticulously carried out in the seele plants. It was also a major engineering task to fulfil the strict climatic and structural requirements for a building in Hong Kong, compliance with which is strictly monitored by the local building authorities across national borders and time zones.
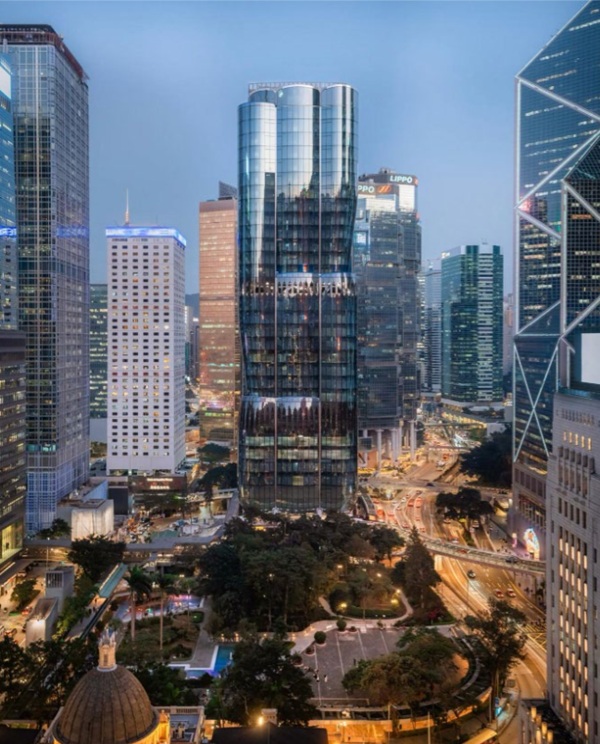
Acknowledgements
seele looks forward to the official opening of “The Henderson“ in late summer 2024 in Hong Kong's financial district. The celebrations mark the successful completion of this prestigious construction project, also dubbed as an “icon amongst icons". We would therefore like to thank Zaha Hadid Architects for the design, which bridges the gap between futuristic technology and a close visual connection to nature. Additionally, the authors would like to thank the developer Century Base Development Ltd. and its parent company, the Henderson Land Group, for realizing such an exceptional project. The productive collaboration with Eckersley O’Callaghan regarding structural and geotechnical engineering significantly supported seele in the realization of this landmark project. Despite the pandemic, a skyscraper has emerged in Hong Kong in just three years of construction, setting new standards – an achievement made possible only through strong international partnerships with a large number of committed parties.
References
Centre for Window and Cladding Technology: Technical Note No 66 — Safety and fragility of glazed roofing: guidance on specification. CWCT, Bath (2010)
CPP Cermak, Peterka, Petersen Wind Engineering and Air Quality Consultants: Final Report – Façade Pressure Wind Tunnel Tests for: Two Murray Road Hong Kong. St. Peters (2019)
The Government of the Hong Kong Special Administrative Region: Code of Practice on Wind Effects in Hong Kong 2004. Buildings Department Hong Kong. https://www.bd.gov.hk/doc/en/resources/codes-and-references/code-and-design-manuals/windcode2004.pdf (2004). Accessed 13 May 2024