Article Information
- Digital Object Identifier (DOI): 10.47982/cgc.9.560
- Published by Challenging Glass, on behalf of the author(s), at Stichting OpenAccess.
- Published as part of the peer-reviewed Challenging Glass Conference Proceedings, Volume 9, June 2024, 10.47982/cgc.9
- Editors: Christian Louter, Freek Bos & Jan Belis
- This work is licensed under a Creative Commons Attribution 4.0 International (CC BY 4.0) license.
- Copyright © 2024 with the author(s)
Authors:
- Joan Tarrús - sedak GmbH & Co. KG
- Julian Hänig - sedak GmbH & Co. KG
Abstract
This paper reveals the new manufacturing possibilities for spherical and some organic geometries, taking advantage of state-of-the-art equipment for tempering and heat strengthening. Free forms in architecture have become increasingly prevalent with the advancement of computer-aided design. Glass is an essential building material and we have seen it used in outstanding structures, façades, skylights and other applications. On some occasions, desired geometries have been achieved by projecting flat triangular complex layouts while in other cases, the design team may have pushed for curved glass with smooth surfaces. In the realm of flat glass, tempering has been the most efficient practice to increase the glass strength. However, when it comes to doubly curved glazing, the options are limited to slumped laminated configurations due to known constraints in load-bearing capacity. While architects continue to explore challenging geometries, and engineers search for technical solutions to meet the demands of each new project, the industry has come up with the daring project-based solutions to meet the most demanding requirements. New developments in the construction industry, such as The Henderson tower by Henderson Land in Hong Kong and the L'Oréal's Innovation Centre in Paris, are pushing the boundaries and verifying the new manufacturing possibilities. Double curved and spherical tempered glass design measuring up to 6.5 m x 3.6 m is now a reality.
1.Introduction
Driven by computational design, architects and designers increasingly desire curved glass with complex geometries for free-form façades. The use of curved glass, instead of triangular planar glass panels, significantly enhances the visual appearance. A common practice for achieving high optical quality and mechanical performance is cold bending, either through lamination or on-site bending, to shape the glass (Rahimzadeh et al. 2023, Feirabend et al. 2021, Eekhout et al. 2010, Laurs et al. 2020, Muja et al.2022). However, for complex curvatures such as multiple radii or double curvatures, the choice is limited to gravity bent slumped glass (Fuldhuth et al. 2011, Fildhuth et al. 2018). A mould is required to slump the glass into each geometry at high temperature. Annealed glass has lower strength compared to tempered glass, resulting in limited resistance to loads. Chemical strengthening can increase structural load-bearing performance, but is elaborate and costly to produce (Zaccaria et al. 2021).
New thermal bending manufacturing techniques now allow for the creation of double curved and spherical geometries up to 6.5 m x 3.5 m while maintaining the high resistance of thermally tempered glass (Fig. 1). Hence, high strength biaxial and spherical curved glass for large-scale façade glazings are feasible. This enables extensive design possibilities and efficient workflows from design to manufacturing, as well as efficient use of the glass.
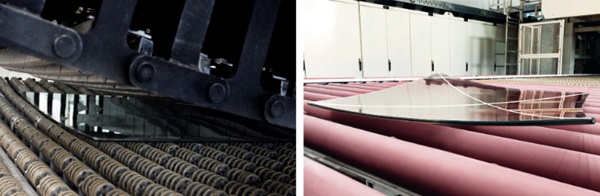
This paper introduces different bending techniques for glass bending and their corresponding design limits. It then provides an overview of the new bending tempering equipment and its manufacturing capabilities. This includes a discussion of thermal tempering options, suitable quality assessment methods and workflow suggestions, as well as a classification of the technology. At hand of two different façade projects with visually striking double curved glass made by sedak, the practical application is presented. Finally, further potential and developments are discussed.
2. State of the Art: Glass Bending
To achieve smooth and continuous surfaces in glass facades, monolithic, laminated, or insulating units of double-curved glass are employed. The techniques for glass bending are classified in either cold or hot bending of glass.
Cold bending of glass offers opportunities to obtain single and double curvatures of the highest optical quality, as the glass is bent from its initial flat state. Two techniques are utilised to hold the glass in the desired shape: lamination bending and on-site (assembly) bending. In general, tempered glass is required to withstand the elevated permanent stresses introduced by the cold bending.
Hot bending is a process that involves heating the glass beyond its glass transition temperature to soften and shape it. This can be achieved through thermal bending, which requires the use of a bending furnace to machine-bend the glass into shape, or through controlled sinking onto a mold.
2.1. Lamination Bending
In lamination bending (Fig. 2), the glass undergoes a temporary cold-bending process onto a substructure and subsequently laminated by means of an autoclave process. The interlayer takes the shear loads of the glass tending back to the initial flat state. Springback effects and flattening over time due to viscoelastic creep of the interlayer after the lamination need to be considered in the design stage (Fildhuth 2015). Afterwards, the glass panels can be further processed into double or triple insulating glass units. The cold bending process is applicable to a wide range of coatings and printings at large geometries (3.6 m x 20m) and can be refined by further integrated designs (Fig. 3). The glass offers high optical quality due to minimal surface distortions. However, the curvature is limited by the glass layout, strength and mechanical requirements in application. A general rule of thumb for the minimal bending radii can be defined as 1.500 times the glass thickness of each ply.
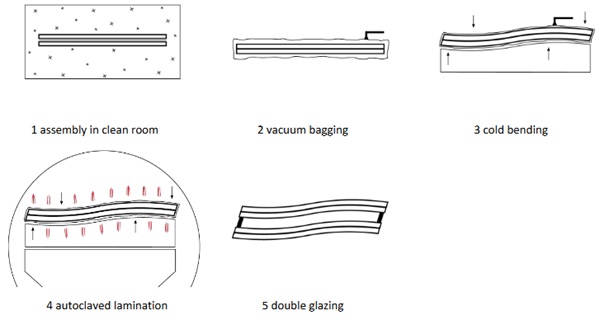
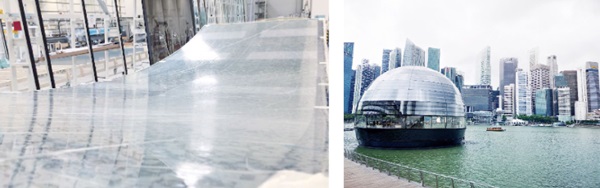
2.2. On-Site (Assembly) Bending
Another possibility is to bend the glass panels on a substructure at ambient temperatures (assembly bending) and keep the position by either mechanical fixings or adhesive joints for fixation (Fig. 4). This is a fast and cost efficient method to achieve complex free form geometries. (Rahimzadeh et al. 2023, Muja et al. 2022, Eckhout et al. 2010, Gavriil et al. 2020).
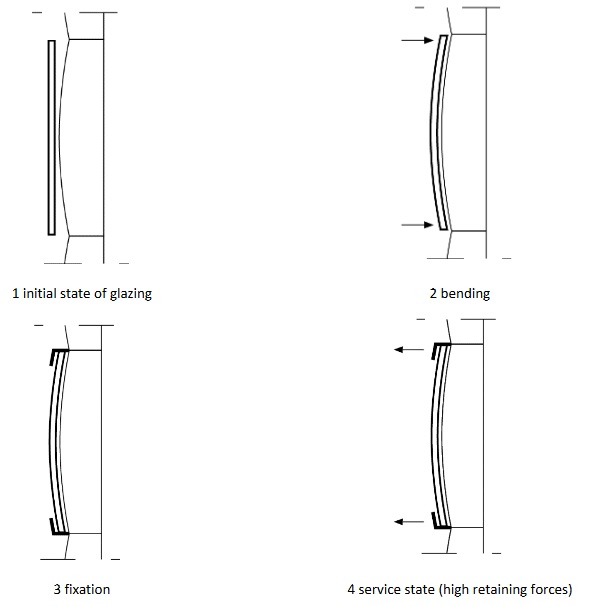
The curvatures are limited by the glass layout, geometry and strength. The frame and all connections need to be designed for the permanent high restoring loads from the glass. Additionally, buckling phenomena need to be investigated at increased bending. Low optical distortions lead to a very homogenous surface (Fig. 5).
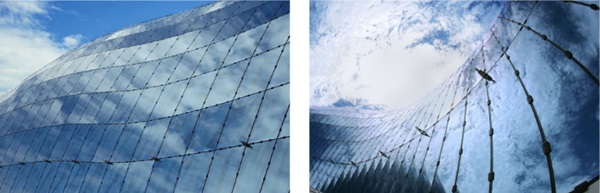
2.3. Thermal Bending
Thermal bending is done during the prestressing of the glass in a tempering furnace (Fig. 6). The glass is heated up above the glass transition temperature, afterwards machine-bent in the desires shape and then rapidly cooled down. For this purpose, the transport rollers in the shaping and cooling area of the quenching system are adjustable. Afterwards, the glass is cooled by air in an oscillating movement of the glass on the rollers. Hence, tempered glass in heat strengthened (EN 1863-1) or fully tempered glass quality (EN 12150-1) is produced. Conventionally, this method is applied for glass with uniaxial curvatures (Fig. 7) and can be processed in sizes up to 3.6 m x 18 m. The arc length and geometries are limited by the geometry, thickness and configuration of the bending equipment.
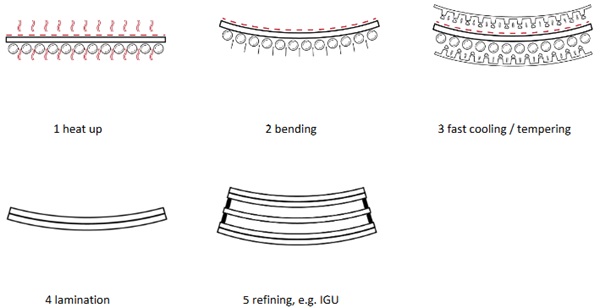
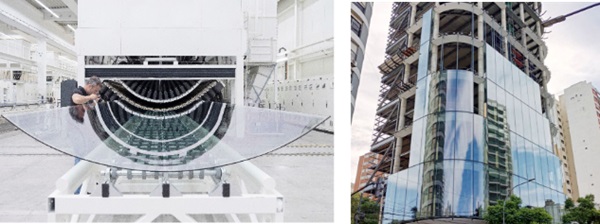
2.4. Gravity Bending
In gravity bending, the float glass is placed on a temperature resistant mould and heated above the glass transition temperature (Fig. 8). The dead-load gently pushes the glass by sinking (concave) or laying down (convex) onto a mould. Afterwards it is cooled down in a controlled slow process to minimise residual glass stresses. This process allows for a wide range of geometrical shapes without visible anisotropies or roller waves. After bending, the glass can be further processed into laminated and refined into insulating glass units (Fig. 9). Accurate customised moulds are required for good optical qualities and minimum tolerance deviations. This makes it time-consuming as well as costly when varying geometries are requested.
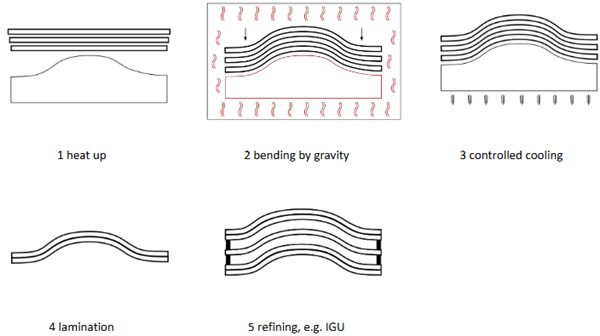
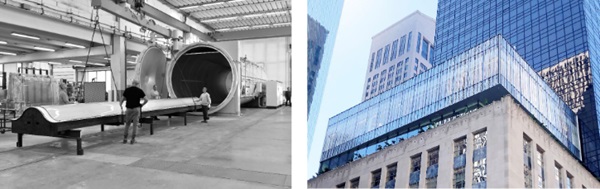
3. New Bending Tempering Equipment: Double Curvature and Spherical Glasses
Whilst in flat glass processing heat strengthening has been the most efficient practice to provide safety glass, when it comes to double curved glazings, the choice has become limited to gravity bentlaminated glass configurations. Due to the lower initial mechanical strength and high effort for prestressing by chemical strengthening, techniques that are more effective are desired.
A new bending equipment at sedak (Fig. 10) allows for double curved and spherical bent temperedglasses in geometries up to 6.5 m x 3.6 m. Clear, low iron, tinted, patterned, enamelled glass as well ason- and offline coatings can be processed in thicknesses between 6–15 mm.
The high mechanical strength due to tempering allows for thinner glass design, complex shapes and optimized series productions for innovative free-form glass façades with various geometries.
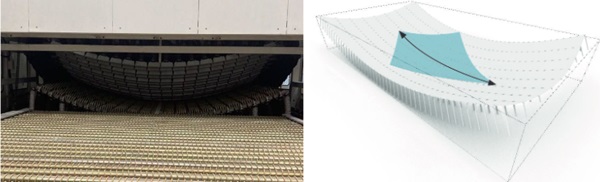
3.1. Geometries of Bending
Conventional bending tempering equipment allows for single curvature only. The new bending tempering equipment permits double curvatures and spherical shapes of bending. The glass dimensions range from 1.2 m x 0.8 m up to 6.5 m x 3.6 m. The maximum bending depth (height of rise) of the bending equipment amounts to 800 mm in length and 400 mm in width. In accordance, the minimal achievable radii result in 4250 mm and 7000 mm, respectively (Fig. 11).
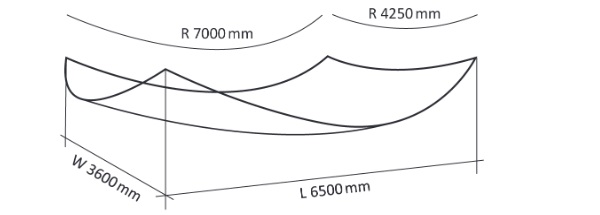
3.2. Processing: Bending, Tempering, Laminating, Refining
The bending equipment reveals tempered glass quality (either heat strengthened or fully tempered glass). The glass is oscillating on rollers in the desired geometry after the heating process. During the oscillation process, the glass is cooled down by air to temper the glass. The bending shape and size of the glass specify the oscillating process and settings of the bending furnace.
Individual parameters are investigated to tighten tolerances, achieve best optical properties and reduce roller waves. After bending, the glass can be further processed into a laminate and refined to double or triple insulating glass units (Fig. 12). In order to meet the tolerances for assembly, the panels can be bend in alignment to the individual radii and distances within the glass layout. This is dependent on the individual curvatures, glass build-up and glazing geometry.
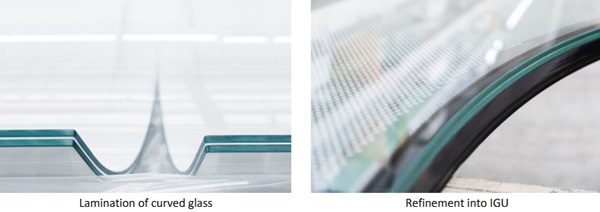
3.3. From Design to Manufacturing
Computer Aided Design CAD enables designers and engineers to make design adjustments quickly and easily. Outputs from parametric workflows can be directly linked to production platforms that manage resources and planning, or handle manufacturing units. At sedak, parametric approaches are used in the tendering phase for production capabilities to translate the glazing designs into the production setup (Fig. 13). Furnace simulations allow a quick and accurate evaluation of production skills. Where necessary, consultations are arranged at an early design stage to discuss design adjustments with architects and clients to optimise production.
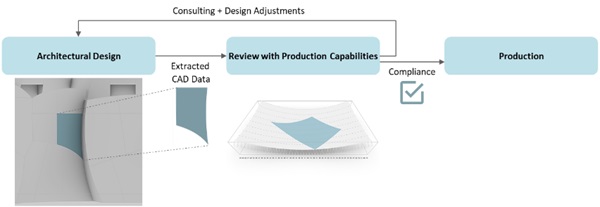
As parametric design models are refined within these platforms, they provide greater control, simplify complex interdependencies and close the loop on feedback mechanisms that improve the efficiency of the overall workflow. Collectively, these compounding effects can save material, time and cost from early design through to assembly.
3.4. Quality Assessment Methods
As of yet, the industrial standards (ISO 11485) or guidelines (Bundesverband Flachglas 2017) define tolerances and bending limits only for uniaxial bent glass according to geometrical parameters. Hence, individual consultations are required between clients and manufacturer in order to meet the design and construction requirements. However, an assessment tool is required in order to control the tolerances and maintain shape accuracy. Three different quality assessment methods were investigated and their suitability for the application with double curved glass panels evaluated (see Table 1).
Optical 3D laser scanning allows a complete inspection of the glass using either handheld or fixed equipment. The technique allows direct conversion of the point cloud to a best-fit plane to create a representative surface scan. The glass must be non-transparent and non-reflecting in order to obtain reliable points. The transparent glass is therefore temporarily masked. This method provides the highest accuracy and resolution, which can also be used to inspect for roller waves and local distortions. The equipment is comparatively expensive and complex, but allows accurate CAD evaluation of different glass shapes.
A full contour mould in high precision is an alternative option to measure deviations from the target geometry. The measurement of the distance between the glass and the contour mould allows for a quick and accurate assessment of the geometry. This method is very suitable for repetitive geometries.
Contour sheets for assessment are a minimalistic and easy method to have a direct measurement after the bending process. It can be employed to further optimize bending and tempering parameters in the furnace. However, the method is often insufficient for precise evaluation of the total panel.
Table 1: Overview and evaluation of different quality and shape assessment methods for application with double curved glass panels.
Based on the optical 3D laser scanning method a workflow is proposed in order to provide a reliable certifiable report (Fig. 14). It describes the successive steps for a CAD assisted true-to-shape production report. It is based on the full 3D scanning of each produced glass panel and its comparison to the provided 3D-CAD-Model. Based on an automated deviation report analysis to the best-fit plane, the geometry is automatically assessed and either approved or complained at hand of the defined tolerances. If the glass panel failed the tolerances, it needs to be either reproduced or approved by a special agreement with the involvement of the client.
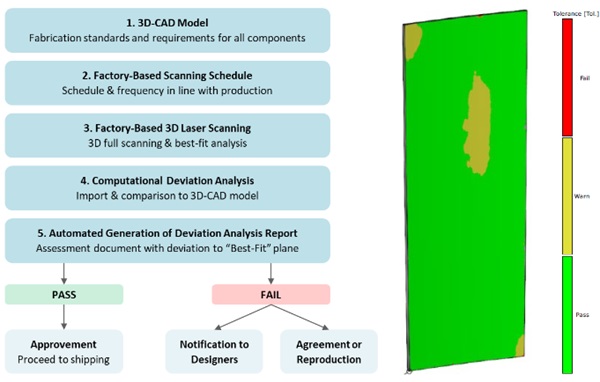
The workflow proposal allows for quality safe production and automated reporting. Hence, the overall glass production and approval is faster, safer and more efficient. Furthermore, it allows for proof based adjustments in order to gain highest precision and optical quality.
4. Projects
4.1. The Henderson, Hong Kong
The recent glass production for “The Henderson” in Hong Kong was a landmark project for uptake of the new bending tempering equipment at sedak (Fig. 15). Highest production quality and parametric tools were required to implement the innovative workflow for bending of more than 650 double and cylindrical curved panels. Different coatings have been implemented in the glass build-up. All glasses are tempered low iron glasses with a panel size range from 2 m x 2 m up to 5 m x 2 m with single anddouble curvature. The complex build-up combines four coatings to achieve the desired visual appearance from in- and outside
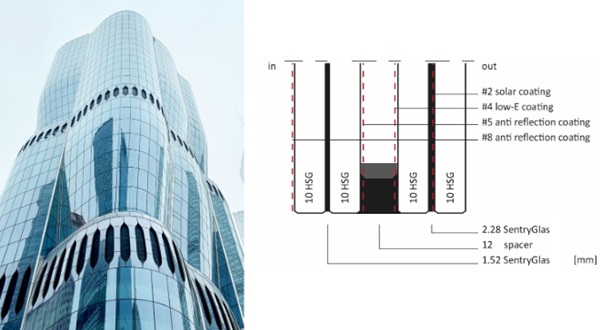
The Zaha Hadid Architects’ design employed the outstanding capabilities of double curved thermal glass bending leading to a unique 190 m high glass façade echoing organic forms of the natural word.
4.2. L'Oréal's Innovation Centre, Paris
Launched during Paris Fashion Week, the “L'Oréal's Innovation Centre” reveals a lamella type meshed of 574 m² curved glass façade in the courtyard of the L'Oréal Headquarter (Bover et al. 2023). With the use of the sedak bending tempering equipment and know how, Bellapart implemented a very innovative façade design. 3D parametric modelling taking into account bending capabilities allowed for targeted coordination between design and manufacturing. Rhomboid shaped panel design was employed, which allowed for tighter curvatures and highest optical quality.
All 188 curved glazings (quadrilateral shaped, triangular shaped and spherical shaped) are tempered and fritted laminated insulating glass units and consist of 2x 8 mm laminated heat strengthened glass.A Low-E coating paired with a digital frit lead to the desired appearance (Fig. 16).
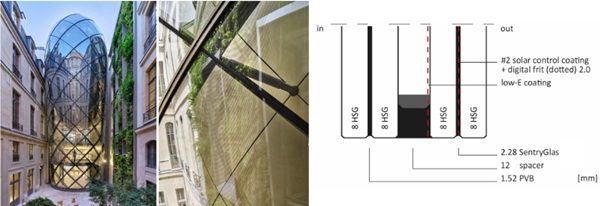
5. Summary, Conclusions, Outlook
Computational design paired with the new bending tempering equipment extends the boundaries for complex free-form glass façades. Innovative curved glass manufacturing capabilities enhance the visual appearance compared to projected polygonal façade geometry. Furthermore, a thinner glass design allows for material downstream and weight reduction.
This paper introduces the current state of the art for glass bending and explains the different manufacturing techniques, their limits, and related refinement capabilities in production. The focus is set on the new bending and tempering equipment that from now on allows for double curved and spherical shaped glazings. The panel size ranges up to 6.5 m x 3.6 m with radii 4250 mm and 7000 mm, respectively. Production capabilities are presented by shape visualisations. Different suitable quality assessment methods describe the complexity of quality assessment. Innovative workflows areproposed that lead to automated, quality safe and speed-up production.
At hand of two outstanding projects "The Henderson", Hong Kong and "L'Oréal's Innovation Centre", Paris, the new opportunities for innovative curved glass façades are demonstrated. The glass's high strength and geometric stiffness after thermal bending pushes for complex geometries and thinner, more sustainable glass design. Double curved and spherical tempered glass design for innovative façades is now a reality.
The innovative workflows from design to manufacturing and subsequent quality assessment methods are consecutively adapted and optimized to close the loop between designers and manufacturer. The newly developed data structures for sharing geometry in a control CAD model automate processes due to production based design. To increase efficiency, these workflows will be integrated into all upcoming projects in early design stage. This enables the realization of optimized double curved glass façades with highest efficiency in design, production and installation.
References
Bover, A., Martinez, A. Guitart, N.: Case of study: Glass façade of l’Oréal headquarters. In: Glass Structures & Engineering (2023) 8 (2023). pp. 513–525 https://doi.org/10.1007/s40940-023-00242-z
Bundesverband Flachglas: Guideline on thermally curved glass for building applications. BF-Bulletin 09/2011 (2017).
Eekhout, M., Niderehe, S.: The Cold Bent Glass Roof of the Victoria & Albert Museum, London. In: Challenging Glass 2 (2010). https://doi.org/10.7480/cgc.2.2312
Feirabend, S., Starz, F., Bechmann, R., Kloker, S., Eckardt, P.: Repositioning Messeturm–Maximum Transparency. In: Glass Structures & Engineering (2021) 6 (2021). pp. 331–337 https://doi.org/10.1007/s40940-020-00140-8
Fildhuth, T., Knippers, J.: Considerations Using Curved, Heat or Cold Bent Glass for Assembling Full Glass Shells. In: Engineered Transparency 2012, Berlin: Ernst & Sohn (2012). https://doi.org/10.13140/2.1.1621.7604
Fildhuth, T., Knippers, J.: Double Curved Glass Shells from Cold Bent Glass Laminates. In: Glass Performance Days 2011 (2011). pp. 316–322.
Fildhuth, T., Schieber, R., Oppe, M.: Design and Construction with Curved Glass. In: Engineered Transparency 2018, Berlin: Ernst & Sohn (2018). pp. 369–381. https://doi.org/10.1002/cepa.937
Fildhuth, T.: Design and Monitoring of Cold Bent Lamination-Stabilised Glass. In: Institut für Tragkonstruktionen und Konstruktives Entwerfen: Forschungsbericht 39 (2015). http://dx.doi.org/10.18419/opus-118
Gavriil, K. Guseinov, R. Perez, J., Pellis, D., Henderson, P., Rist, F., Pottmann, H., Bickel, B.: Computational Design of Cold Bent Glass Façades. In: ACM Trans. Graph., Vol. 39, No. 6, Article 208 (2020). https://doi.org/10.1145/3414685.3417843
Laurs, M., Schaaf, B., Di Biase, P., Feldmann, M.: Numerical and Experimental Investigations on the Inherent Stress State of Cold-bent Glass. In: Challenging Glass 7 (2020). https://doi.org/10.7480/cgc.7.4503
Muja, E., Hänig, J., Rooprai, M., Ingo, S., Weller, B.: Cold Bent Laminated Glass Application – Numerical Research. In: Engineered Transparency 2021, Berlin: Ernst & Sohn (2021). pp. 191–206. https://doi.org/10.1002/cepa.1857
Neugebauer, J.: Applications for curved glass in buildings. In: Journal of Facade Design and Engineering 2 (2014). pp. 67–83. https://doi.org/10.3233/fde-150016
Rahimzadeh, K., Levelle, E.: (Not) pushing the envelope: achieving the world’s largest cold bent façade with computation and 3- dimensional framing. In: Glass Structures & Engineering (2023) 8. pp. 495–512 https://doi.org/10.1007/s40940-023-00235-y