Challenging Glass 6
Conference on Architectural and Structural Applications of Glass
Louter, Bos, Belis, Veer, Nijsse (Eds.), Delft University of Technology, May 2018.
Copyright © with the authors. All rights reserved.
ISBN 978-94-6366-044-0, https://doi.org/10.7480/cgc.6.2114
Authors:
Emmanuel Barrois - Barrois Glass workshop
Yvan Belletre - Barrois Glass workshop
Artur Bechtloff - Ferro GmbH
The economy globalizes. The industries concentrate. The productions become uniform. Cultural specificities disappear. About architecture and glass in architecture, it is the same phenomenon. Is this movement good or not? It is too late to ask the question. This dynamic is irreversible. Nevertheless, in certain cases, on certain projects, it is possible to bring more esthetic, sensibility, humanity and culture. The 100 years of Ferro’s experience in material science provide such base for creativity with outstanding material solutions like s1de ONE and LustReflex. Since 20 years, the Barrois Glass studio works to create bridges between crafts and industry with the objective in esthetic, sensibility, humanity and culture.
Associate the rigor and the efficiency of the industry with the creativity and the sensibility of crafts. A decade of s1de ONE projects proving the durability at challenging environmental conditions is reviewed. The latest material developments and application technologies providing new opportunities for creativity is shown. The three outstanding projects—La canopée les Halles in Paris, Le frac in Marseille, Le musée de la Romanité in Nimes— are presented in detail. Those projects were all studied with the objective to work otherwise.
1.s1de ONE Enamels to Obtain Outstanding Design at Buildings
Ferro’s s1de ONE enamels allow architects and designers multiple options in designing the exterior surface of buildings. The unique properties of s1de ONE enamels that enable the use on the buildings surface is their very high chemical and weathering durability. Due to that outstanding weathering resistance Ferro is able to warranty the stability of the surface against fading of the color shade for more than 10 years. First projects built in 2007 illustrate that durability.
For architects and designers, buildings decorated with these enamels provide the possibility to vary their color by illumination of the buildings surface with colored light. Such enamels also enable the architect to control the reflection of the glass surface and to achieve unique visual effects.
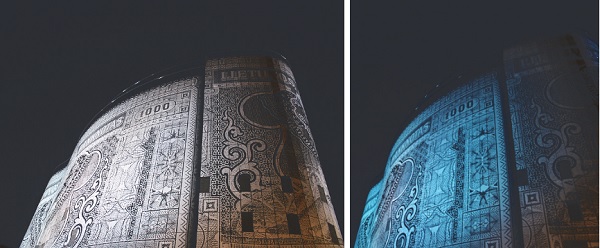
s1de ONE can be used in designs to imitate materials like Aluminum, wood or stone, and at the same time stimulate the use of the glass, an easy-to-process, flexible construction material. Innovation in the development of application technologies provide further design opportunities that were once limited, costly or impossible to achieve. Only the s1de ONE inks for digital application technology achieve such special effects at high brilliance of colors and flexibility in design. Through Ferro’s digital printer company Dip-Tech, the needed technology for such new opportunities is provided.
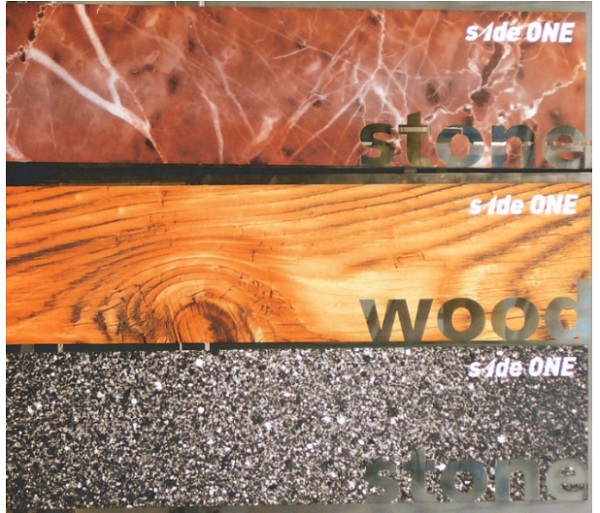
Leading architects welcome such new opportunities to realize their projects all around the globe. From New York to Tokyo, from London to Milan, from Paris to Moscow.
2.The Iconic Projects of Atelier Barrois
2.1.Canopy of Halles, Paris
The Halles Forum of Paris is an iconic place of the capital, a site dedicated to trades which span generations. It is also a space of wandering into the density of the 1st arrondissement, only a few streets from the Centre Pompidou, the National Museum of Modern Art.
Through this project, the architect Mr. Patrick Berger wanted to reinforce the image of the initial Halles Forum as a space for shared walks, conviviality and the promotion of social ties.
One of the first desires for this project was to create a continuous, open and protected public space in order to preserve a visual and physical fluent connection between the project and its surroundings. The mega structure of the Canopy and its glass roof was the obvious answer to reach these objectives.
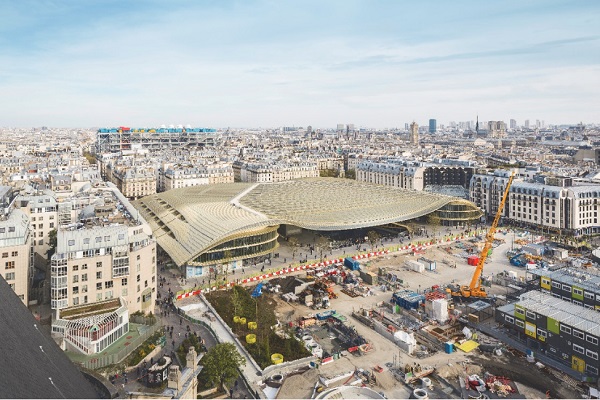
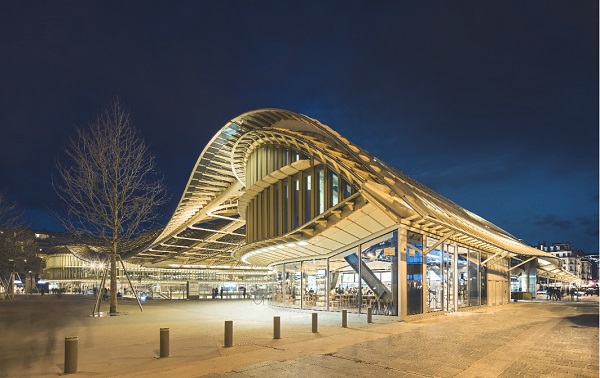
Emmanuel Barrois Studio has worked closely with the architect Patrick Berger to elaborate the rigorous glass product of the Canopy. It has to care about the whole aesthetic, technical and functional constraints.
Which atmosphere should create this immense glass roof?
Which level of sunlight should it generate?
Which lighting ambiance under it? Warm, welcoming, colored?
If the metallic structure of the Canopy defines its skeleton, the glass itself is its skin, its flesh, its identity. In this way, the glass coloration, its transparency, its translucency, its opacity, its texture, its reflection, its sparkle and its composition are all the topics which have been considered, explored and prototyped by Emmanuel Barrois Studio.
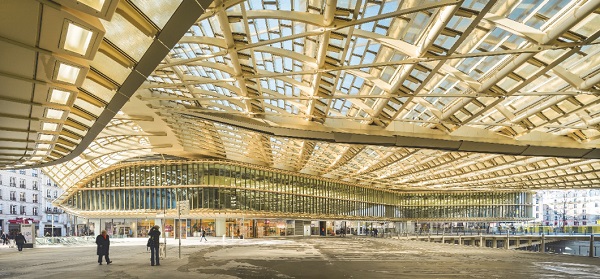
Right from the start, in order to reach a very light and transparent yellow color, E. Barrois Studio was looking for an industrial product which can be compared to a certain aesthetic treatment coming from the craftsmanship world. Nowadays, the glass colored treatments are made by layers or organic pigments which are not sustainable enough. Furthermore, such materials have a low plastic and aesthetic quality. So, the Studio had to find a mineral treatment for the glass which would be able to provide the high quality level required. Besides, the enamels used in the glass industry are generally translucent and thus unsuitable for the project. Some rare transparent enamels do exist but their use is very delicate and their sustainability is uncertain. E. Barrois Studio had to find a new product, affordable, and which must be implemented to a big scale by an industrial provider.
In collaboration with the Ferro teams, we chose the product LustReflex. This product has been used only in a few ways. Almost unknown by the glass industry, it has never been considered for major architectural application in France.
n the craft of glass, the lusters have existed for centuries. The method is to apply a liquid solution containing metal organic solutions on the glass. Then, this metallic or metal oxide nano layer is revealed by the toughening firing of the glass. The LustReflex by Ferro is an industrial version of this ancestral and handcraft technique.
It was clear that this product was appropriate to achieve our aesthetic and normative goals. Finally, it is a delicate mix between the LustReflex gold and the LustReflex silver which led us to reach the perfect color, its transparency and the light metallic effect desired.
Some parts of the building are dedicated to technical elements, so they had to be hidden by the canopy. On different zones, in addition of the LustReflex located inside the laminated glass, we added a semi-transparent screen print frame applied with the enamel Ferro s1de ONE etch. In this way, we had to determinate two different degrees of translucency. Right above the people, the glass product is 85% transparent and 15% translucent. At the opposite, the glass parts above the technical elements are 15% transparent and 85% translucent.
The last ingenious work on the glass was its light relief. The geometry of the Canopy is complex and the glass panels of the roof are lightly inclined. In these conditions, the risk to see the apparition of raindrop marks on the glass was real. In order to prevent this phenomenon and to minimize the glass maintenance, we decided to apply a light lines design in relief on the outer face of the glass. This versatile linear graphic design serve to visually eliminate these raindrop traces.
Today, when the sunlight is low-angled, the design and the relief treated with the LustReflex make the Canopy of Halles sparkle. From the landscaped public space, there are millions of reflections livening up the horizon.
Under the glass roof, the vast esplanade became a convivial place, people stroll and meet in a warm, light environment.
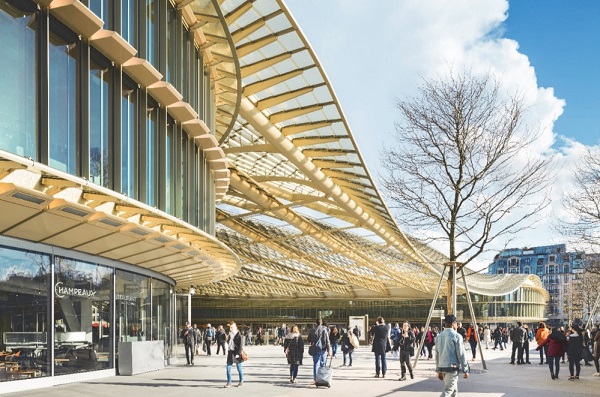
After 15 months of research, applications, many thoughts and tested solutions, and about 200 square meters of prototypes for 9 different options, we finally found and validated this innovative glass product. The process of production developed by E. Barrois Studio was later prescribed by the architect during the public tender. The firm AGC Vertal (Lyon, France) has finally produced the 24 000 square meters of glass of the Canopy.
That is how a skilled and rigorous craftsmanship is able to influence and interact with the industry. From the research and the experimentation at a small scale to the big scale production.
2.2.Museum of the Romanity, Nimes
The Museum of the Romanity is located in the historical heart of the city of Nimes, sixty kilometers away from the Mediterranean Sea. This building is right in front of the famous Arenas of Nimes, classified on the UNESCO World Heritage Site.
The Museum's vocation is to reveal and to explain the Roman civilization which is the origin of the city of Nimes. This is the reason why it must maintain an intimate dialogue with these close Arenas and further with the Roman culture.
To materialize this idea, the Studios of Portzamparc, architects of the project, wanted to cover the building with a drape which represents the Roman toga. This double glass skin follows a smooth and complex geometry. Plenty of small squares are designed on the glass pieces to recall the Roman mosaic art.
The Emmanuel Barrois Studio has studied, developed and produced the glass elements of this complex glass skin. Many constraints have been considered to move towards an aesthetic, functional and technical coherency.
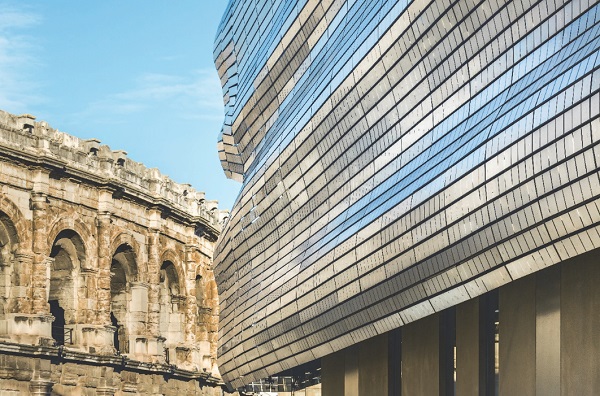
In collaboration with the architects, the engineering consultants RFR in Paris has studied the modeling geometry of the facade and they define the dimensions of one glass module which makes 1500 x 200 mm. About 7000 glass slides have been necessary to complete the 2300 square meters of the facade. The glass elements are overlapped and fixed side by side on a secondary metallic structure which ensures the whole slides to give a fluent visual aspect.
A glass facade has always to care about the light reflection on its surface. Because the Museum is located in front of the Arenas, and to avoid a violent relationship between the two monuments, it was essential to master and decrease the brightness of the glass. For this reason, the squares reminding the Roman mosaic have been treated with the enamel Ferro s1de ONE.
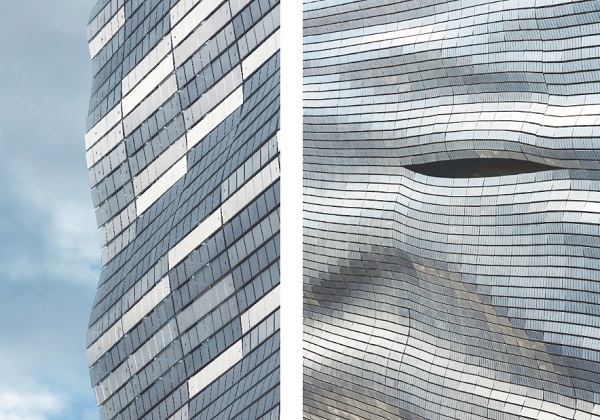
This glass skin has also to think about the luminous flux going through it. In order to protect the art pieces inside the Museum, the entering light should be soft and diffuse. The enamel veil willing the glass is like a filter in the same way of a textile. Moreover, after the care of the technical constraints, the aesthetic of the product must be defined. The decision was made by the architects to hide any frames or secondary graphic elements thanks to the white enamel squares. Furthermore, the level of translucency has to be 90%, so 10% of transparency. To obtain this result, the squares have to be composed by a solid white color of enamel Ferro s1de ONE and perforated by holes of 0,8 mm diameter. This small diameter allows to make the holes visually imperceptible. However, the existing industrial tools for the screen-print of enamel on glass are not able to reach this level of definition. Moreover, the latest print technologies on glass were at that time incompatible with the Ferro s1de ONE enamel.
The Emmanuel Barrois Studio has drawn its inspiration from specific know-how to realize the project. One of the ancestral technics from the ceramic industry is an indirect serigraphy called the chromography. We have worked hard with ceramic specialists to adapt it to the glass in order to obtain the high precision required. Once the tests tried with this technic, they were analyzed, validated and warranted by the labs of Ferro.
Then, the whole 7000 glass slides have been treated with the enamel Ferro s1ide ONE by the E. Barrois Studio. Finally, the slides have been tempered and laminated by the firm Dania Vitrage in the North of France.
The group HEFI which specializes in facades, was in charge of the installation of the glass elements on the metallic structure, which they also developed.
Today the glass veil is setting. It filters the light from outside. On the outdoor surface, the glass flakes respond to the sunlight like the mosaic elements would. Depending on the time, the season, the climate, this glass skin changes its aspects. The whole facade creates a contemporary, smooth and subtle dialogue with the arenas.
At the sunset, the artificial lighting offers new effects, new images, new colors and lights.
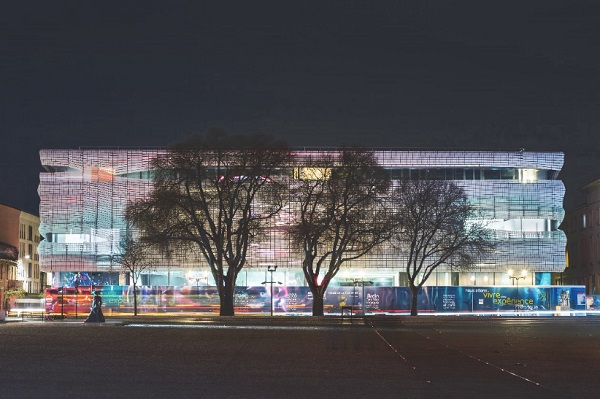
This realization results of the intimate collaboration between the architect, the engineers, the facade firm HEFI, Emmanuel Barrois Studio and the German laboratory of the enamel producer Ferro.
This glass skin shows an approach which targets the perfection. The project testifies also that the industry way of thinking can be compatible with the sensitivity and the how-know from the craftsmanship.
2.3.Museum of the FRAC, Marseille
The FRAC is a Museum of contemporary art which was created during Marseille European capital in 2016. In this context, the city wanted to show its cultural interest through a strong architectural building.
The project of the Japanese architect, Kengo Kuma has been chosen because of its sensitive and particular facade. On a complex plot, the architect has imagined a building covered by a double glass skin composed of 1700 panels, like a pixelation of white enameled glass.
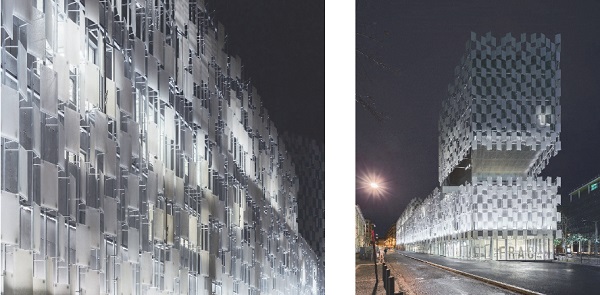
Regarding the scale of the city, these glass panels should seamed identical in order to provide a general lecture of the building. However, Kengo Kuma places importance on the craftsmanship and sensitive materials. For this reason, regarding the human scale, he wanted all the panels different.
The industrial processes are made for uniformed and mass production. To realize 1700 similar glass panels but at the same time all different from each other needed a very specific approach inappropriate to the industry. It has to include a craftsmanship procedure into the reflection and the production process.
So, after the analysis of the normative and economic constraints of the project, it appears clearly that the glass panels should be realized in industrial glass, enameled, tempered and laminated.
In the production process, the only moment we could inject an atypical intervention was the time of the enameling of the glass. This intervention has been decided and it will be applied by hand. Before the start of the construction site, technical and plastic research has been conducted. After many tests, a marginal technic has been settled to create an enamel rain on the panels. In this intention the enamel Ferro s1de ONE has been chosen in order to respect the whole technic regulations.
First of all, a specific color has been elaborated. It is a white color with a warm tonality. Then, 5 to 6 million enamel tears have been dropped on the glass, by hand, drop by drop.
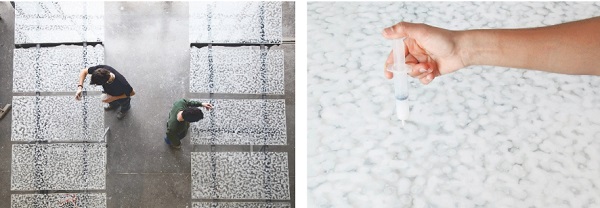
Once this step is done, the glass panels follow a classical industrial cycle such as the thermal quenching and the lamination operations. These steps have been realized by the factory BGT in Germany and the glass panels have been fixed to the secondary metallic structure by the firm HEFI. At the end, those panels respect the entire technical regulations required.
- Aesthetically, the glass material creates an infinity of textures and light diffusions. This double glass skin lets a soft and filtered light, which protects the art pieces directly exposed to the strong Mediterranean sunlight.
- To conclude, paradoxically, it is in an industrial technical context and full of obligations that a craftsmanship intervention takes place. It creates new architectural freedoms spaces respecting the whole constraints and norms.
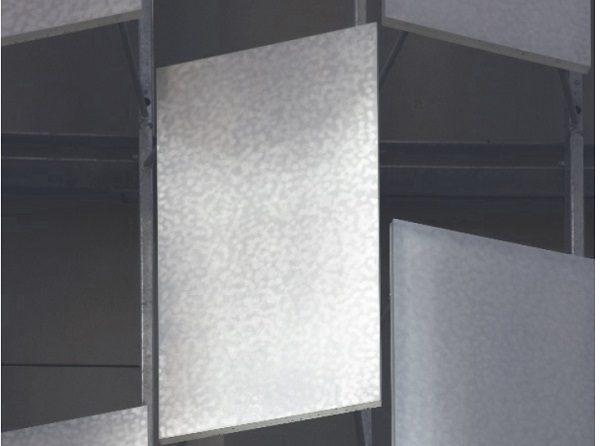
3.Outlook to New Material Opportunities
Architects are always looking for new materials, surface properties and opportunities to create new designs. Such quest drives ongoing development at Ferro. As one result, Ferro is now able to extend the s1de ONE range with the matt versions of the enamels. Such special matt versions of the enamels achieve a very low gloss value of 15 to 20 gloss units at 60° angle only compared to more than 85 gloss units for the standard s1de ONE products, at identical firing conditions.
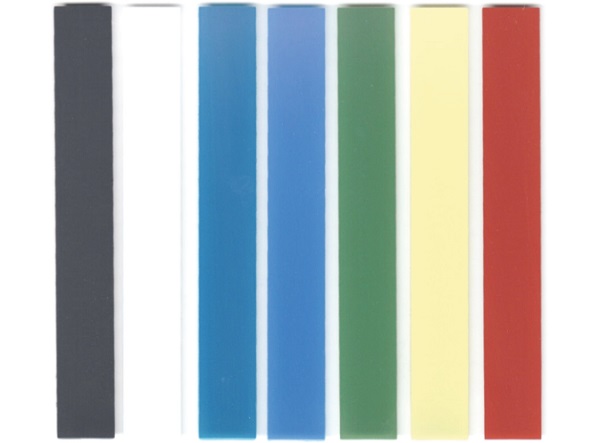
With these matt enamels it is now possible for the architect to create a coating on the glass surface which has similar look and touch like natural stone keeping the advantages of glass as material for cladding. By the compatibility of the matt and glossy shades of s1de ONE, Ferro is able to provide architects and designers with individual specified gloss level in between the 20 and 85 gloss units at 60° angle for all standard shades as well as for mixtures of these in the RAL, Pantone or NCS color ranges.