Article Information
- Digital Object Identifier (DOI): 10.47982/cgc.9.481
- Published by Challenging Glass, on behalf of the author(s), at Stichting OpenAccess.
- Published as part of the peer-reviewed Challenging Glass Conference Proceedings, Volume 9, June 2024, 10.47982/cgc.9
- Editors: Christian Louter, Freek Bos & Jan Belis
- This work is licensed under a Creative Commons Attribution 4.0 International (CC BY 4.0) license.
- Copyright © 2024 with the author(s)
Authors:
- Sebastián Andrés López - Universität Siegen
- Thorsten Weimar - Universität Siegen
Abstract
Glass remains a popular material in architectural and engineering applications for the building envelope. However, meeting the increasing demands on façade elements while implementing all requests is an unrealisable challenge for monolithic glass. Therefore, laminated safety glass, which is a combination of at least two glass panes and an interlayer, can be a solution for more and more applications in the building sector with enhanced requirements on safety, such as splitter bonding in the broken state. Furthermore, the European standards permit the use of glazing plastic material in the cross-section of laminated safety glass. In response to this specification, a composite panel made of thin glass and polycarbonate is proposed as an alternative to laminated safety glass. The multi-layer cross-section is designed to be lightweight with a slim nominal thickness for security glazing, and to possess advantageous structural-physical attributes.
This paper presents a further possibility of the favourable combination of both materials. The results of a research project at the Chair of Building Structure at Universität Siegen indicate that the integration of smart layers in the cross-section of a laminated safety glass made of thin glass and polycarbonate is a promising approach for further investigation. This leads to the development of a switchable composite panel with improved luminous and solar characteristics. The smart element is laminated between two polycarbonate sheets using polyurethane interlayers during an autoclave process. It is essential that the composite panel passes climatic stress tests for durability at high temperature and in humidity, which are fundamental requirements for further research as laminated glass and laminated safety glass. This paper identifies the necessary materials for a minimal cross-section through experimental standard tests to fulfill the requirements of laminated safety glass with adjustable luminous and solar characteristics.
1. Introduction
The design of multifunctional façades includes a wide range of requirements, like protection from weather, sun, heat, fire and noise, and security, energy, design, media, and interaction. The concept of a polyvalent wall involves the adaptively adjustable properties between two glass panes, considering environmental boundary conditions (Davies 1981; Knaack 2014). In fact, the implementation of all these properties in a monolithic glass pane is currently unrealisable. Laminated safety glass and insulated glass (IG) or vacuum insulating glass (VIG) are suitable for using in building envelopes due to their favourable properties in terms of safety, noise, or heat protection.
Furthermore, the solar characteristics can be regulated by installing smart layers between the glass panes of laminated glass (Casini 2018; Slack 2023). The glazing element can adjust the protection to individual requirements by providing variable sun protection and regulating the light transmittance intensity based on the season or time of day. However, when additional requirements such as fall protection (DIN 18008-4) or active safety (EN 356; EN 1063) are implemented, laminated safety glass becomes thick and heavy, particularly if used in insulated glass. According to (EN ISO 12543-1), plastic glazing materials such as polymethyl methacrylate (PMMA) and polycarbonate (PC) are permitted in the cross-section of laminated safety glass, resulting in a reduction of the nominal thickness and the dead load (Weimar 2021a).
This paper presents an overview of the initial stages of developing a switchable laminated safety glass made of thin glass, polycarbonate, and polyurethane interlayers. The development process starts with a comprehensive study of the suitability of the materials and an investigation of their compatibility. To determine the optimal cross-section as laminated safety glass, the pendulum test (EN 12600) using a multitude of polycarbonate sheets and laminates, is evaluated. This will provide an indication of the resulting polycarbonate layer thickness. Following preliminary experiments through measurement and testing of the solar and luminous characteristics (EN 410) and thermorheological behaviour of interlayers, the cross-section is developed. Conventionally, the composite panel of thin glass and polycarbonate is produced using liquid adhesives in a cold bonding process. The research project deals with the production of a plane-parallel composite panel using a warm bonding process in an autoclave for more automation. Overall, the multilayer system must meet the requirements for laminated safety glass (EN 14449; EN ISO 12543-4).
2. Laminated Safety Glass and Composite Panels
Laminated safety glass is regulated by test methods for climatic durability and mechanical strength (EN ISO 12543-3; EN 14449). In addition, laminated safety glass demonstrates passive safety through post-breakage behaviour and splitter bonding (EN ISO 12543-1). This standard also allows the use of polymethyl methacrylate and polycarbonate sheets in the cross-section. The market offers laminates of glass and polymethyl methacrylate, for example (NEEROGLAS 2020). However, a post-breakage behaviour is not possible to ensure using polymethyl methacrylate due to the brittle behaviour of the plastic sheet and glass pane. Consequently, the field of application is limited to usage with no requirements on passive safety (Hänig 2023). Composite panels made of polycarbonate and glass have been well-known for approximately 15 years as described by (Weimar 2011; Polygard Attack; SiLATEC). Recent research focuses on implementing thin glass in composite panels with polycarbonate to create a lightweight and slim laminated safety glass with improved properties in terms of security, heat and noise protection compared to conventional laminated safety glass (Weimar 2021b; Andrés López 2024). Further processing to insulated glass (IG) or in combination with vacuum insulating glass (VIG) demonstrates the novel potential of this material combination (Weimar 2021; Weimar 2024).
3. Smart Glass with Switchable Elements
Smart glass is created by adding switchable elements to a multi-layer system. These elements provide controllable glazing that primarily affects sun protection, anti-glare protection, thermal protection and light transmittance. The glazing is either self-sufficient or can be individually controlled. Smart glass enables the selective adjustment of luminous and solar characteristics, including light transmittance, reflection properties and solar heat gain coefficient (SHGC), to prevent sunlight and heat from entering through the glazing while remaining transparent and to offer privacy by making the glass opaque. The advantage of smart glass is its ability to adjust properties as needed, regardless of the weather conditions. In contrast to conventional sun protection glazing, smart glass does not always darken the room and provides higher energy efficiency. However, depending on the type of the implemented switchable system, disadvantages such as slow response times for colour or discolouration or the need for electricity may occur. The most common technologies for reactive elements are thermochromism, e.g. thermochromic and thermotropic layers, photochromism, e.g. photochromic layers, electrochromism, e.g. gasochromic, electrochromic and combinations, and liquid crystals, e.g. polymer-dispersed liquid-crystal (PDLC) and suspended-particle devices (SPD). (Husser 2017; Casini 2018; Slack 2023)
4. Material Selection and Cross-Section Development
Laminated safety glass has to pass the tests for climatic durability and mechanical strength as well as demonstrate post-breakage behaviour and protection against injuries. It is important to note, that not all interlayer types adhere to glass and polycarbonate in the same way, and the switchable layer adds further complexity to the material selection for a smart thin glass-polycarbonate composite panel. At the beginning of the cross-section development, the primary consideration is whether to use a symmetrical or asymmetrical structure. If an asymmetrical cross-section is chosen, all tests must be conducted twice on both sides. Furthermore, the location of the smart layer must be determined based on technical and economic factors. This results in a symmetrical composition with one switchable layer situated between two polycarbonate sheets. Various possible cross-sections are illustrated in Figure 1.
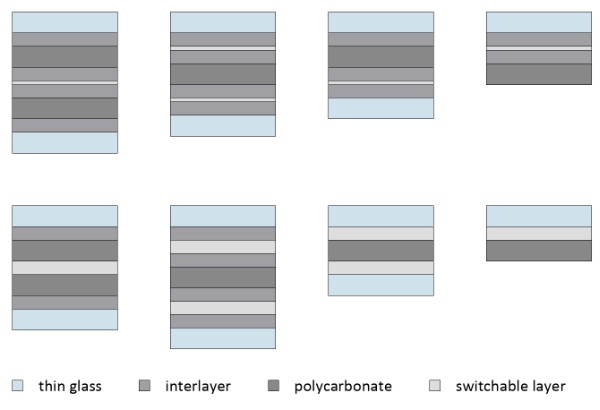
Thin glass typically has a nominal thickness range of 2.0 mm to 0.5 mm. It can be either annealed glass, such as (Optiwhite 2020) or (Microwhite 2020), or chemically pre-stressed glass, such as (Falcon 2020). In consideration of economic factors and market availability, the recommended option is the annealed glass (Microwhite 2020) with a nominal thickness of 1.0 mm and border edges.
There are two standard polycarbonate products available, namely (Lexan 2018) and (Exolon 2021), both of which have nearly identical material properties. In preliminary experiments at a temperature of (27,7±0,4) °C and humidity of (46,4±3,7) % RH of the pendulum test according to (EN 12600), various polycarbonate sheets and laminates are conducted by the pendulum with a mass of 50 kg to determine the minimal cross-section for a 2(B)2 classification with a drop height of 450 mm. Table 1 presents the results of the pendulum test with the successful drop height without failure. Overall, the failure is because of sliding of the material from the supporting without penetration of the pendulum. Two polycarbonate sheets of 2 mm from the product (Exolon 2021) or (Lexan 2018) are selected for the optimal cross-section of the composite panel.
Table 1: Results of the pendulum tests of polycarbonate sheets (PC) (Lexan 2018, Exolon 2021) and laminated polycarbonate with a thermoplastic polyurethane interlayer (TPU) (Dureflex A4700 2021).
The interlayer for the lamination has to adhere to polycarbonate, thin glass and the smart layer. Polyvinylbutyral (PVB), ethylene vinyl acetate (EVA) and stiff interlayers like SentryGlass do not show satisfactory results or are unable to adhere to polycarbonate. Thermoplastic polyurethane interlayers are typically used to guarantee a high adhesive to polycarbonate and glass (Scheider 2016). Two thermoplastic polyurethane interlayers are analyzed using thermomechanical analysis in a NetzschDMA 242 to determine their properties. Figure 2 shows the storage modulus E’, loss modulus E’’, and loss factor tan δ at 1 Hz in the tensile test for the thermorheological simple thermoplastic polyurethane polymers (Dureflex A4700 2021) and Krystalflex PE 399 (Krystalflex PE399 2022). The glass transition temperature Tg ranges from approximately -50 °C to -45 °C, and the storage modulus E’ and loss factor tan δ show a small deviation. The typical temperature range for polymer interlayers in glazing varies between -20 °C and +60 °C (EN 16613). For both interlayer products, the glass transition temperature is outside this range. Furthermore, the storage modulus is low, which allows a high flexibility in the viscous state to compensate the different thermal expansion coefficients of polycarbonate and thin glass. Consequently, both interlayers are suitable for the composite panel.
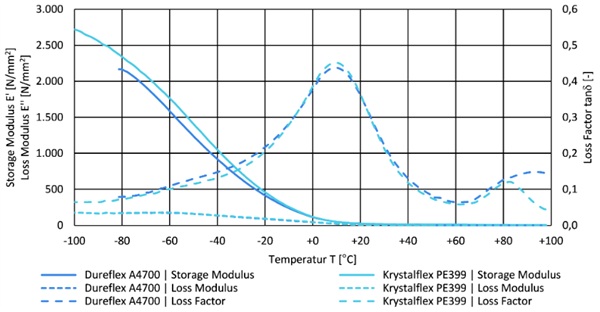
The performance of the smart thin glass-polycarbonate composite panel is evaluated based on the light transmittance value and the difference in the solar heat gain coefficient (SHGC). Four panels with dimensions of 80 mm by 80 mm are tested using the PerkinElmer Lambda1050+ spectrometer to measure the luminous and solar characteristics (EN 410). The specimen information is presented in table 2, and the transmission curve is shown in figure 3.
Table 2: Information about the specimens for spectroscopy. Annealed glass (AG) (Microwhite 2020), thermoplastic polyurethane (TPU) (Krystalflex PE399 2022), polycarbonate (PC) E (Exolon GP 2021) or L (Lexan 9030 2018) and polymer dispersed liquid crystal (PDLC) foil in grey or white (dutchPOD 2020).
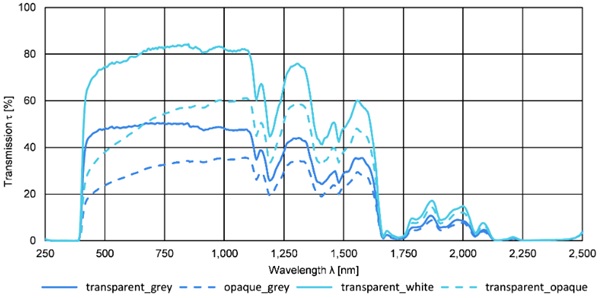
Table 3 shows the results for light transmittance τVIS and solar heat gain coefficient (SHGC) in accordance with (EN 410). SK_E_white has the highest light transmittance at 76,4 % and a solar heat gain coefficient (SHGC) of 71,6 % in the transparent mode. When the smart composite panel is switched to the opaque mode, the light transmittance is reduced by 34,2 % and the solar heat gain coefficient (SHGC) by 19,5 %. Similar results are observed for specimens with (Lexan 2018). In terms of material selection, the white switchable polymer-dispersed liquid-crystal (PDLC) foil (dutchPOD 2020) offers higher light transmission and differences in the solar heat gain coefficient (SHGC). While the grey foil is the optimal choice in terms of solar heat gain coefficient (SHGC), the lower light transmittance is not to be overlooked in the transparent state. Therefore, the white foil will be used in the cross-section.
Table 3: Measured values of spectroscopy. Top value is the transparent state, the bottom value the opaque state.
The preliminary experiments of the pendulum test on polycarbonate, the thermomechanical analysis for the interlayer and the measurements on the luminous and solar characteristics for the smart layer implemented in the cross-section lead to the material selection and the determination of the minimal cross-section required for smart thin glass-polycarbonate composite panels for further research on durability, mechanical strength, structural and post-breakage behaviour. The final cross-section will have a composition of
Annealed Glass (Microwhite 2020) | Polyurethane (Krystalflex PE399 2022) | Polycarbonate (Exolon 2021) | Polyurethane (Krystalflex PE399 2022) | white Polymer-Dispersed Liquid-Crystal (PDLC) | Polyurethane (Krystalflex PE399 2022) | Polycarbonate (Exolon 2021) | Annealed Glass (Microwhite 2020).
5. Production Process
(Thin) Glass-polycarbonate composite panels are typically manufactured via a cold lamination process utilising a multi-component adhesive. A liquid resin is filled between the plastic sheet and the glass pane, which hardens through a chemical reaction, time duration or ultraviolet radiation. Once the hardening process is completed, the next layer of adhesive and plastic sheet or glass pane can be added. The cold process is preferred due to the different thermal coefficients of thermal elongation between glass and polycarbonate. Polycarbonate shows a coefficient of 70 x 10⁻⁶ 1/K which is approximately 7 times higher than the thermal elongation of glass of 9 x 10⁻⁶ 1/K. Conversely, manual manufacturing is more expensive because of the lack of automation. The presented smart composite panel of thin glass and polycarbonate is produced in an autoclave with interlayer foils. This requires a significant investment of time and resources for the first preparation, handling, and machine setting. Therefore, a multitude of composite panels with different adjustments are produced and analysed in the autoclave. Figure 4 illustrates some of the test outcomes. By the help of the zebra test, local distortions during the production can be visualised to change the parameters of the autoclave process. Even if the multilayer system is produced without error, the thin glass is fragile and fractures during the post-processing or transportation. Further investigation is required to identify the cause of fracture. Potential solutions include higher edge finishing or higher nominal thicknesses of the annealed glass, chemically pre-stressing of glass, or the use of a special spacer during the autoclave process next to the edges. Nevertheless, the thin composite panel with nominal thicknesses of approximately 11 mm to 12 mm needs a careful handling in the following stages. Despite the challenges that arise during the production process, like optimising the autoclave settings in response to preparation, handling, temperature, pressure and time, defect-free composite panels are the result of the final adjustments.

6. Composite Analysis
The composite of glass and glazing plastic material must achieve the same tests as a glass-glass composite for the classification as laminated safety glass. Therefore, (EN ISO 125434-4) describes the test method for durability. Three specimens each measuring 200 mm by 300 mm have to pass the storage at (+100±2) °C for 2 h, at (+50±5) °C with nearly 100 % RH for 14 d, and at (+45±5) °C for 2,000 h under radiation. The tests are carried out at the laboratory of the Chair of Building Structure at Universität Siegen. The specimens pass the tests if no blisters, delamination or haze are observed in the interlayer. The mechanical strength is tested through the ball drop test (EN 14449) and the pendulum test (EN 14449; EN 12600). During the ball drop test a 1,063 g steel ball falls from a height of 4,000 mm onto the 500 mm by 500 mm square specimens without an initial impulse and should not penetrate the composite panel. The pendulum test as soft impact investigates the behaviour of the specimen with dimensions of 876 mm by 1,938 mm being dropped from 190 mm, 450 mm or 1,200 mm. The classification of the composite panel depends on the type of fracture pattern and drop height. Table 4 describes the test conditions for the dimension and the cross-section of the specimens for climatic durability and mechanical strength.
Table 4: Results of the composite analysis of smart thin glass-polycarbonate composite panels (EN 14449; EN ISO 12543-4) with a nominal thickness of 11.5 mm of two outer annealed thin glass panes (Microwhite 2020), two inner polycarbonate sheets (Exolon 2021), and a smart polymer-dispersed liquid-crystal (PDLC) (dutchPOD 2020) foil sandwiched between the polycarbonate sheets with the interlayer (Krystalflex PE399 2022)
The experimental investigation shows satisfying results with no appearance of defects during climatic durability, no penetration during the ball drop test and a pendulum classification of at least 2(B)2 (EN 14449; EN ISO 12543-4). The test under radiation has not been completed yet. Table 5 provides a summary of the test results of the composite analysis.
Table 5: Results of the composite analysis of smart thin glass-polycarbonate composite panels (EN 14449; EN ISO 12543-4).
7. Conclusion and Further Work
Thin glass-polycarbonate composite panels are used as laminated safety glass and security glazing due to their advanced properties. In addition to providing security and heat protection, a polyvalent wall can integrate a range of additional applications. This paper presents the initial stages of a research project on smart composite panels produced in a warm autoclave process. The paper concludes with the development of a cross-section that passes the test as laminated safety glass.
The selection and development of materials for the minimal cross-section are based on preliminary experiments involving polycarbonate sheet thickness, interlayer selection and the performance of smart layers. To determine the materials and cross-section for further structural analysis, thermomechanical analysis, spectroscopic measurements, and pendulum tests are conducted. The final minimum cross-section with nominal thicknesses of 11.5 mm consists of two outer annealed thin glass panes, two inner polycarbonate sheets, and a smart polymer-dispersed liquid-crystal (PDLC) foil sandwiched between the polycarbonate sheets. All components are laminated with a thermoplastic polyurethane interlayer in an autoclave. The climatic durability of this cross-section is tested at high temperature and under humidity. The radiation testing is not yet complete, and the results will be made available once the test is finished. The composite panels made of switchable thin glass and polycarbonate combine the advantageous properties of both materials. The use of lightweight and thin laminated safety glass with controllable luminous and solar characteristics is proposed as an alternative to conventional smart glass. This solution makes retrofitting easier, allows to build slimmer substructures and improves thermal protection. Figure 5 presents the smart composite panel in both its transparent and opaque states.
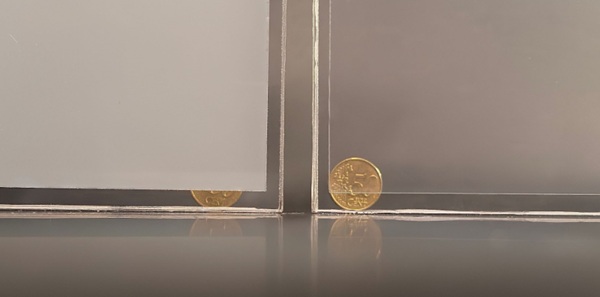
Further investigation into this topic will involve the analysis of the structural and post-breakage behaviour, as well as the impact of shear transfer and numerical modelling. The research requires to value the impact of higher energy absorption and heating resulting from the use of materials with different thermal elongation coefficients in one cross-section for façade elements of the building envelope. To achieve this, it is necessary to conduct experimental tests under thermal load to verify numerical results.
Acknowledgements
The research project was funded by the German Federal Ministry of Economic Affairs and Climate Action as part of Zentrales Innovationsprogramm Mittelstand (ZIM). Special thanks go to the cooperation partner KRD Coatings GmbH for constructive cooperation and providing of numerous specimens.
References
Andrés López, S.: Contribution to the Application of Thin Glass and Polycarbonate in Structural Engineering. PhD Thesis. Universität Siegen (preparing for publication)
Casini, M.: Active dynamic windows for buildings: A review. In: Renewable Energy 119, pp. 923-934. (2018)
Davies, M.: A Wall for All Seasons. In: RIBA Journal 88, pp. 55-57. London (1981)
DIN 18008-4: Glass in Building - Design and construction rules - Part 4: Additional requirements for barrier glazing. Berlin, Beuth (2013)
Dureflex A4700. Covestro AG. Datasheet (2021)
dutchPOD® dutchPOD®. Qdel B.V. Datasheet (2020)
EN 356: Glass in building - Security glazing - Testing and classification of resistance against manual attack. Berlin, Beuth (2000)
EN 410: Glass in building - Determination of luminous and solar characteristics of glazing. Berlin, Beuth (2011)
EN 1063: Glass in building - Security glazing - Testing and classification of resistance against bullet attack. Berlin, Beuth (2000)
EN 12600: Glas im Bauwesen - Pendelschlagversuch - Verfahren für die Stoßprüfung und Klassifizierung von Flachglas. Berlin, Beuth (2003)
EN 14449: Glass in building - Laminated glass and laminated safety glass - Evaluation of conformity/Product standard. Berlin, Beuth (2005)
EN 16613 Glass in building - Laminated glass and laminated safety glass - Determination of interlayer viscoelastic properties. Berlin: Beuth (2019)
EN ISO 12543-1: Glass in building - Laminated glass and laminated safety glass - Part 1: Vocabulary and description of component parts. Berlin, Beuth (2022)
EN ISO 12543-2: Glass in building - Laminated glass and laminated safety glass - Part 2: Laminated safety glass. Berlin, Beuth (2022)
EN ISO 12543-4: Glass in building - Laminated glass and laminated safety glass - Part 4: Test methods for durability. Berlin, Beuth (2022)
Exolon GP. Exolon Group NV. Datasheet (2021)
Falcon Glass. AGC Europe GmbH. Datasheet (2020)
Hänig, J.: Development of Thin Glass-Plastic-Composite Panels for the Building Industry. PhD Thesis. Technische Universität Dresden (2023)
Husser, M.; Haase, W.: Adaptive Verglasungssysteme. Einsatzbereiche, energetische und tageslichttechnische Evaluierung, Regelungsstrategien. Abschlussbericht. In: Fraunhofer Informationszentrum Raum und Bau: Informationsdienst Bauforschung aktuell: Fraunhofer IRB Verlag. Band F3044. (2017)
Knaack, U; Klein, T.; Bilow, M.; Auer, T.: Fassaden. Prinzipien der Konstruktion. Birkhäuser Verlag GmbH. Basel (2014)
Krystalflex PE 399. Huntsman Corporation. Datasheet (2022)
LexanTM 9030. Saudi Basic Industries Corporation (SABIC). Datasheet (2018)
NEEROGLAS®. KRD Engineering & Service GmbH. Datasheet (2020)
MicrowhiteTM. Pilkington Group Limited. Datasheet (2020)
OptiwhiteTM. Pilkington Deutschland AG. Datasheet (2020)
Polygard Attack. Vetrotech Saint-Gobain Deutschland. https://www.vetrotech.com/de-de/polygard-attack
Slack, A.; Massard, R.: Dynamic Glass – What is needed? In: Glass Performance Days 2023. Conference Proceedings Book. Page 221-225. (2023)
SILATEC. SiLATEC Sicherheits- und Lamiantglastechnik GmbH. https://www.sicherheitsglas.de/einbruchsicheres-glas/
Schneider, J.; Kuntsche, J.; Schula, S.; Schneider, F.; Wörner, J.: Glasbau. Berlin: Springer-Verlag (2016)
Weimar, T.: Research on Glass-Polycarbonate Composite Panels. PhD Thesis. Technische Universität Dresden (2011)
Weimar, T.; Andrés López, S.; Hahn, C.: Entwicklung von Verbundtafeln aus innovativem Dünnglas und Polycarbonat. In: Fraunhofer Informationszentrum Raum und Bau: Informationsdienst Bauforschung aktuell: Fraunhofer IRB Verlag. Band F3077 (2018)
Weimar, T.; Andrés López, S.; Vuylsteke, L.: Innovative Sicherheitssonderverglasungen aus Dünnglas und Polycarbonat. In: Stahlbau. 90. Jahrgang (2021). Heft 7. Seite 498-506. https://doi.org/10.1002/stab.202100029
Weimar, T.; Andrés López, S.; Hahn, C.: Dünnglas-Polycarbonat-Verbundtafeln. Untersuchungen zu linien- und punktförmig gelagerten Dünnglas-Polycarbonat-Verbundtafeln. BBSR-Online-Publikation 28/2021, Bonn (2021b)
Weimar, T.; Hammer, C.; Reißaus, H.; Hahn, C.: Vakuumisolierglas mit Sicherheitsanforderungen. Entwicklung von Vakuum-Isolierglas mit passiven und aktiven Sicherheitsanforderungen. BBSR-Online-Publikation. Bonn (2024)