Creative opportunities may be endless with the use of bent glass, but require careful consideration – and team coordination – in order to achieve results that balance aesthetic and performance objectives.
Bent glass can be an efficient choice for structural glazing applications. The material offers high load resistance, and the curved shape minimizes deflections. Bent tempered glass also offers excellent mechanical strength and durability against temperature variations. While recent improvements in glass manufacturing technology have made the product safer and less expensive, bent glass remains a custom material.
Bent glasses are not available in standard sizes and curves must be shaped to the specifications of the project. While any glass installation requires careful handling, bent glass exacerbates the challenge. Typical glass suction cups cannot be used on curved glass. Instead, special suction cups with a deeper well offer a better grip around the glass radius.
TYPES OF BENT GLASS
Annealed bent glass most frequently appears in windows and showcases when the need for safety glass is minimal. Toughened bent glass, which is stronger and more shock resistant, commonly appears in staircases and other interior applications. Only laminated bent glass offer glass retention after breakage and may be used in both interior and exterior applications. Bent glass properties can be customized with different colors and finishes.
Coatings – such as Low-E – cannot be applied to glass after it has been bent. Instead, different hard and soft coating methods must be performed before curving. Even Insulating Glass Units (IGUs) can be constructed with bent glass for improved acoustical and thermal performance. Typically, the maximum bending angle is one half of a circle. Glass can be curved in a factory using a hot bending process or cold bent during installation.
BENT GLASS MANUFACTURING
Hot Bending uses heat to create the curved shape and amounts to 95 percent of all glass bending. This can be done with a heat treatment bending quench. Within a specially configured part of the heat-treatment production line, the quench mechanically establishes a constant-radius form. Alternatively, glass can be slump bent. Various types of steel molds are used for slumping the flat glass into desired shapes. Glass is placed on top of a pre-heated mold and then placed into a kiln. At about 600° C, the glass begins to melt and bend, melding into the shape of the mold. The kiln is very slowly cooled down, completing the bending glass.
Cold Bending forces flat glass into a curved position during installation. The process uses external stressing to convert the glass into out-of-plane geometry and constrain it in that state permanently using the glazing framing system. Cold bending can be performed after glass has been tempered, providing the glass with the properties of safety glazing.
Lamination Bending combines hot and cold bending with lamination. Using an autoclave process, the glass sandwich of sheets and interlayers is bent using heat and pressure. The laminated glass fulfills safety glazing requirements while offering flexible shapes. However, laminated bent glass is susceptible to the spring effect, in which the glass straightens slightly after the autoclave process with added subtle glass relaxation over time.
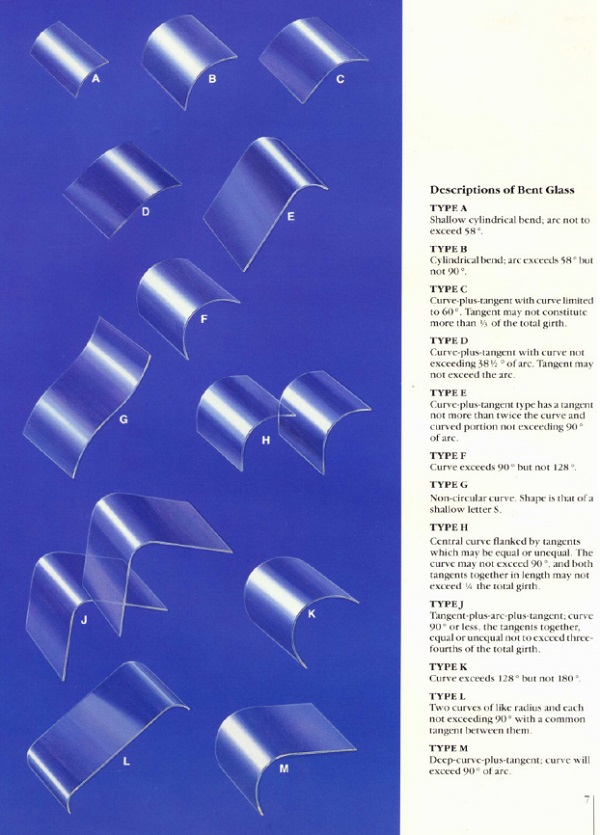
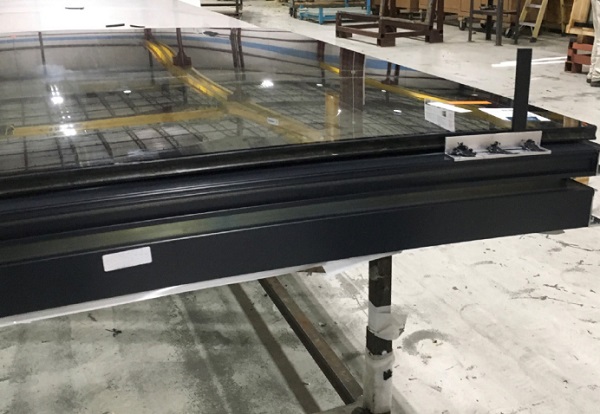
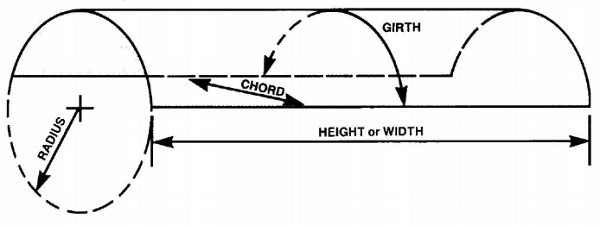
MEASURING BASICS
Specialty fabricator Bent Glass Design in Hatboro, Pa., offers architectural, laminated, and specialty glass bent or curved into any shape, including sharp bends up to 90 degrees and compound bends for complex shapes. Careful measuring and dimensioning are required for bent glass. The company suggests the following:
Unlike the length and width dimensions required to order flat glass, the fabrication of curved glass requires precise dimensions of the shape of the glass. There are two ways to describe the shape. The first consists of the girth, height or width, and radius dimensions. When the radius is not known, the chord and depth dimensions can be provided. A flexible tape measure is needed to measure the outside girth. A flat measurement is used to measure the height/width, inside chord, and inside depth. A hardboard or mylar template is required with all the dimensions noted above if an accurate radius dimension cannot be provided.
Bent Glass Design offers additional guidance and works directly with architectural and glazing teams to provide technical design assistance for bent glass projects.
BENT GLASS ISSUES
AGI asked its member glazing contractors and affiliates to provide insights into the challenges of working with bent glass. All agreed the product provides ample opportunities for creativity in design and effective construction. Yet there was consensus around the primary issues of concern:
TOP 5 BENT GLASS ISSUES
1. Lead Time
2. Tolerances
3. Adjacencies
4. Distortion
5. Coordination
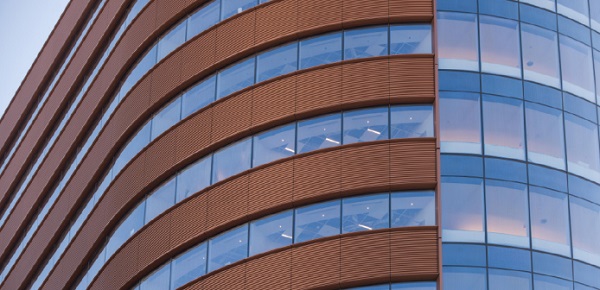
LEAD TIME
National Glass and Metal Co. Inc. President Joe Clabbers cites long lead times as a primary issue of concern. Depending on the product’s composition, lead times can range from 6-8 weeks for locally sourced glass or as many as 20+ weeks for overseas products.
TOLERANCES
National Project Manager John Norwood emphasizes that tight tolerances are a compounding issue with bent glass. You must consider the dimensions of the curved piece of glass and its associated framing. When working with a pressure wall or other system with a uniform gasket dimension, the glazier may need to use a wet seal to allow for added dimensional tolerance between the glass and metal.
When installing curved glass into metal framing, care must be taken not to put undue pressure on the glass. If radii are not exactly aligned, stresses can lead to future breakage. Vice President Stephen Strauss of CMS Strauss Glass advises dimensioning properly to consider pocket setup, direction, and measuring both sides of the curve. “If you are measuring from the inside or the outside, you’ll have a different dimension,” he explains. “You must specify both dimensions when you order.”
ADJACENCIES
According to Clabbers, adjacent materials have a direct impact on the installation and performance of bent glass. Substrates above and below windows are a particular concern. When substrates need to be blended with glass or structural steel, issues can arise. “The substrate must precisely correlate with the curves and segments,” he says. “High points of the segments sometimes don’t match the radius of the glass.” Clabbers advises advance planning and coordination to overcome substrate issues.
Strauss adds that when installing laminated glass railings, the interlayer binder should also be considered. Typical polyvinyl butyral (PVB) binder, which is appropriate for interior railings, will not withstand exterior elements. Instead SentryGlas® ionoplast interlayer must be used instead. This element needs to be considered early, as laminated glass must be “sandwiched” with all interlayers and binders before being bent.
Wiss Janney Elstner (WJE) Senior Associate and Building Enclosure Consultant Dana Landis, PE, recommends design professionals pay careful attention to glazing spacers. Typical aluminum spacers used in flat Insulating Glass Units (IGUs) may not accommodate the curve of bent glass. Instead, warm edge spacer bars can be used. These are less thermally conducive than metal spacers and result in a more energy efficient sealed glazing unit.
These keep the panes of glass apart and maintain the integrity of the air gap that insulates a building from heat loss through windows. However, Landis warns, the spacer could change the visual appearance of a building. “For example, coordinating the color of the spacers is important if using both metal and warm edge spacers.” The spacers and framing of two adjacent systems – such as for a curved and a flat system side-by-side – should be coordinated so the systems blend seamlessly in envelope integrity and appearance.
Adjacent flashings can also be cause for concern. Metal in straight segments must be aligned with curved segments. With glazed IGUs, the curve of the aluminum extrusion may not match the curve of the glass. Additional tolerances can be built into structural sealants to accommodate differences in the curves.
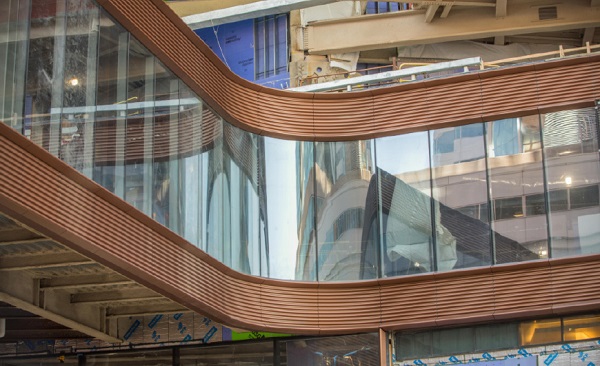
DISTORTION
Roller wave distortion describes the subtle waving pattern in glass that has gone over rollers during the heat treatment and bending process. Anisotropy, sometimes called iridescence, describes the manifestation of patterns and colorful areas due to stress differences within the glass created during heat treatment - both the heating and cooling processes.
According to Landis, most people don’t notice the effect these have on finished glass. However, anisotropy becomes more apparent in polarized light – or through the lenses of polarized sunglasses - or at different time of day. In this case, the effect can be a rainbow glare or a reflected series of lines. “It’s an inherent effect that happens during tempering,” she explains. “We can control it but can’t avoid it.”
Glass pieces can be run through the tempering oven in the same direction, for example, so that any visual distortion is consistent for all pieces of glass for one facade. Design teams and fabricators should discuss in advance the maximum dimension for glass pieces to go through the oven to coordinate a consistent direction for glass to be heat treated and bent. Visual mockups should also be provided to evaluate the distortion and use as a baseline for comparison during production.
COORDINATION
From proper measurement of curves to mitigating tolerance risks to ensuring anisotropy and roller wave distortion don’t negatively impact a project’s aesthetics, design teams working with bent glass benefit from advance communication and coordination. Strauss recalls a project with a dramatic half-circular showcase. When the curved pieces arrived on site, they included four inches of straight flat pieces at the end of each curve. The flat pieces accommodated the manufacturer’s clamps used when the pieces of glass were bent. This detail – and the associated time and cost to correct – could have been avoided with advance discussion.
ADDITIONAL RESOURCES
For more information about bent glass:
Expert Series: Bent Glass by Guardian Glass
Bent Glass Overview by Bent Glass Design, Inc.
CASE STUDY:
Penn Medicine Pavilion | Philadelphia, Pa.
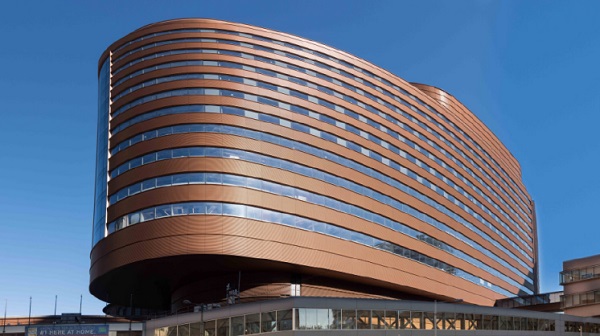
The Hospital of the University of Pennsylvania’s new 1.5-million-sf, 17-story inpatient facility features curved glass exterior cladding in a combination of unitized curtain wall and pressure wall systems along with monolithic back-painted glass.
The team included AGI member National Glass and Metal Co., Inc., which performed some of the exterior glazing scope. National President Joe Clabbers described the long lead times for bent glass, increased pre-project planning, and close tolerances as the primary issues of concern. “CAD and REVIT were helpful in coordination to make sure all of the radii matched,” he explained. Project Manager John Norwood added that in addition to carefully documenting radii when using bent glass, designers must be mindful of manufacturing restrictions that limit radius angles. “Early communication with the manufacturer will help make sure you are specifying the correct products and understand the limitations.”
For this project, European manufacturer Interpane provided coated glass to Cricursa for bending. Wiss Janney Elstner (WJE) Senior Associate Dana Landis, PE, provided building enclosure consulting and commissioning for the Pavilion. Her WJE team worked with Enclos, the glazing contractor responsible for the tower portion of the building, and with National. “We worked through issues related to aesthetics, determining which direction the glass would go through the ovens to limit vision distortion, and ensuring the different glazing systems matched in terms of visual and performance requirements.”