Challenging Glass 6
Conference on Architectural and Structural Applications of Glass
Louter, Bos, Belis, Veer, Nijsse (Eds.), Delft University of Technology, May 2018.
Copyright © with the authors. All rights reserved.
ISBN 978-94-6366-044-0, https://doi.org/10.7480/cgc.6.2182
Author:
Michael Kothe - Thiele Glas Werk GmbH, Germany
Laminated safety glass with structural PVB interlayer is suitable for a variety of challenging applications in building construction and façade design. Especially in areas with increased static requirements, stiffer interlayer materials are preferred to standard PVB films. This results in a reduction in the number of glass panes or pane thicknesses while maintaining comparable properties. The attainment of relevant safety properties in combination with advantages in both processing and economic terms often allows a more reasonable application than the use of appropriate laminated glass with ionomer interlayers. A new filter factory of a well-known medical technology company is currently being built in Wilsdruff on the outskirts of Dresden.
The company's own competence campus is glazed with large-format glass elements. The new building of the Wilsdruff filter factory represents the first application of large-format laminated safety glass panes with structural PVB interlayer under the approach of the shear coupling in Germany. Both the pane sizes of 7.25 m x 2.40 m and the type of two-sided linear support of the façade panes are extraordinary and unique in Germany in this combination. Based on the material properties of the PVB film, the advantages of such elements are demonstrated. It can be seen that projects such as the Wilsdruff filter factory can only be realized in this form by using stiffer interlayers. This project thus demonstrates the possibilities of using such laminated safety glass and thus helps to increase the acceptance of architects, planners and building owners.
1.Introduction
Structural PVB-based interlayer, i. e. rigid or stiffer PVB films have been available on the market for structural glass construction applications for several years. The aim was to close a gap between the conventional used PVB interlayer and the high-strength, ionomer-based interlayer in order to be able to offer components that can be meaningfully used both constructively and economically. However, these structural PVB interlayer with their range of properties do not meet the requirements of the German building regulations list for interlayer materials for the production of laminated safety glass (cf. Bauregelliste (BRL), A 1.11.14, Annex 11.8 (DIBt 2015)).
For this reason, market entry in Germany was delayed and only possible under increased expense compared to other European countries. Only the granting of a general type approval (allgemeine bauaufsichtliche Zulassung .. abZ) by the German Institute for Building Technology (Deutsches Institut für Bautechnik .. DIBt) for the use of such interlayer in the production of laminated safety glass in 2014 made it possible to make more extensive use of such components in a more extensive way (DIBt 2014). The most important areas of application that can be realized with these products include projects in which the need for high system stiffness and residual load-bearing capacity of laminated safety glass made of toughened glass is desired and demanded.
The approach of the shear modulus as a property of the interlayer material used in the construction of glass components is prohibited in accordance with the German design and construction regulations for glass in civil engineering (DIN 18008-1:2010) and requires a general type approval. Other European countries already have more advanced standards for glass calculation and dimensioning, where shear force transmission can be used as a function of material properties. This is the case, for example, in Italy (UNI TR 11463), Belgium (NBN S 23-002-2), the Netherlands (NEN 2608) and Norway (NS 3510). With the draft standard prEN 16612:2017 (prEN 16612:2017), a European standard is also inprocess of being developed.
Previously, national approvals were granted in Germany for specific material combinations of laminated glass with defined interlayer materials to use defined moduli values for defined load scenarios. Until recently, there was no general type approval for PVB films with approach of shear coupling. This changed in 2016 with the granting of a general type approval for the use of moduli values with PVB films of the Saflex®-DG series (DIBt 2016a) and the Trosifol®-ES series (DIBt 2016b) for structural glass construction applications.
This article describes the use of PVB interlayers, such as Saflex®-DG interlayers, for applications in structural glass construction as laminated safety glass with an approach of shear coupling. Using the example of a completed engineering project, the filter factory Wilsdruff, the advantages of glass dimensioning and possible applications in these areas are explained, taking into account the special features of German building law.
2.Structural PVB interlayer
2.1.Comparison with conventional PVB interlayer for building construction
Structural PVB films are tough, resistant interlayer made of pre-plasticized polyvinyl butyral. They have been developed for applications requiring a high degree of stiffness and a high adhesion to the glass surface. These requirements cannot be met by standard PVB. In contrast to conventional interlayer materials, structural PVB films such as the Saflex®-DG or Trosifol®-ES series have outstanding properties when used in structural glass construction.Even after the breakage of one or more glass panes of a laminated glass unit, glazing with structural PVB films are able to guarantee a residual load bearing capacity under high loads, at low or high temperatures (Eastman 2012).
Table 1: Comparion of typical properties of conventional and structural PVB films1
1 .. data collected from technical data sheets of different PVB film manufacturers
Areas of application in structural glass construction using structural PVB films are in particular applications with free glass edges, walk-on glazing and glazing that prevent falling, as well as balcony parapets or point-fixed elements. In all cases, even in the event of glass breakage, increased demands are made on safety. Due to the higher stiffness of the intermediate layer, the laminated glass panes can bear a higher load at the same glass thickness or be designed with the same load with reduced glass thickness.
For the glass refiner, the use of this material requires little extra effort. The structural films are also supplied in rolls, just like conventional films, and can therefore be integrated into existing systems and processes without additional resetting times.
2.2.Thermal properties
The analysis of thermomechanical properties shows a good comparison between the different interlayer materials. The material properties such as stiffness and glass transition temperatures can be determined by means of dynamic-mechanical analysis (Kothe 2013). The following diagram (Fig. 1) shows the stiffness characteristics in a temperature range from - 50 °C to + 100 °C for a conventional PVB and structural PVB film. The different material stiffness over the temperature profile in the manner of the storage moduli (as part of the modulus of elasticity) and the different glass transition areas are clearly visible.
The storage module and thus the material stiffness of the Saflex® DG41 film is 40 % higher at low temperatures (< 0 °C) compared to conventional film. The glass transition area, the temperature range at which significant changes in properties take place, begins with the conventional PVB film already from about +10 °C, and with the stiffer PVB film from about +25 °C. The glass transition temperature, determined from the maxima of the loss factor tanδ (dotted curve), is with +42 °C for the structural PVB film also significantly above the value of the conventional PVB film with +29 °C.
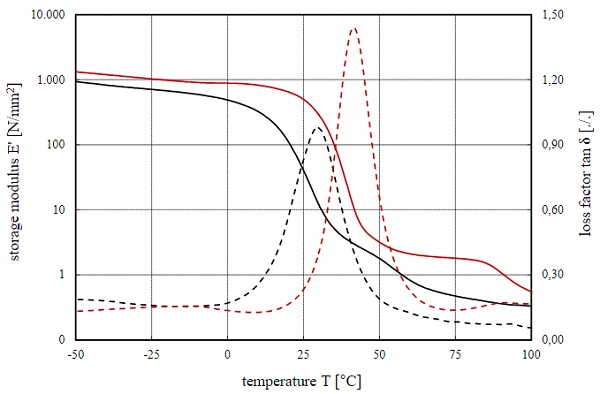
2.3.Edge stability
A frequent problem with laminated safety glass is the compatibility of different materials in contact with each other or the effects of environmental influences. These interactions can lead to changes in material characteristics that cause optical defects or even impair the functionality of the glazing. The most common environmental influences are those affecting open edges of the laminated safety glass or the contact of sealants with the interlayer.
Considering the effects of external environmental influences, such as heat and moisture on the edge of a laminated safety glass, there are significant differences between conventional and structural PVB films. The following diagram (fig. 2) shows the dependency of the edge stability number (ESN) over a total weathering period of four years. The edges are exposed to early morning dew, fog and rain as well as high temperatures and UV radiation during the course of the day.
The edge stability number (ESN) describes the weighted percentage error length, whereby the weighting increases with increasing penetration depth. The highest ESN is 2,500 and is equivalent to influencing the entire edge length with a penetration depth of 0.25 in (approx. 6.4 mm). The lower the ESN, the better the edge stability under the prevailing conditions. An ESN of less than 500 indicates outstanding edge stability (Stevels and Haller 2017).
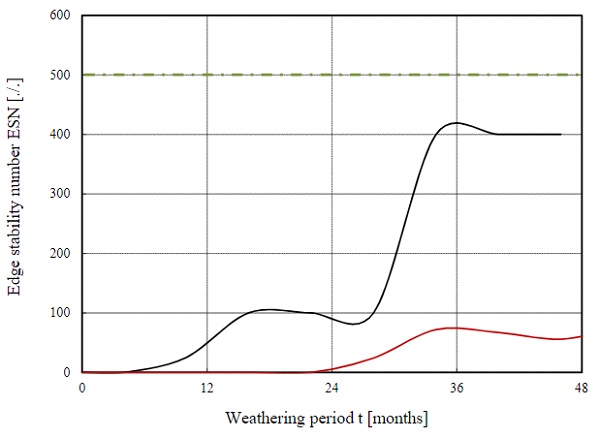
The difference in edge stability between conventional and structural PVB film can be clearly seen in figure 2. Both test specimens have been exposed to weathering over a prolonged period of time. However, it can be seen that the edge stability of the Saflex®-DG film is considerably better compared to conventional films.
2.4.Residual load-bearing capacity
An outstanding feature of laminated safety glass compared to monolithic glazing is the residual load-bearing capacity in case of glass breakage. This is guaranteed by the fact that the single fragments adhere to the interlayer, interlock with each other and thus create a composite effect. The larger the individual fragments are, the greater is the residual load-bearing capacity. For this reason, laminated safety glass made of float glass or heat-strengthened glass, which breaks in large parts, should be used especially for applications in safety-relevant areas such as fall protection, walk-on glazing or overhead glazing.
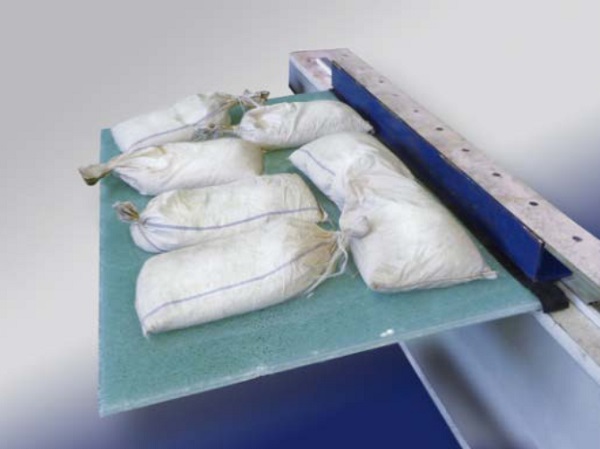
In addition to glass, however, the choice of the interlayer material also influences the behaviour in case of glass breakage. The mechanical properties of the films depend to a large degree on the ambient temperature (see section 2.2). Here, structural PVB films can also demonstrate their advantages over conventional films (see Fig. 3). The higher stiffness is guaranteed over a wider temperature range and leads to lower deformations in the event of failure and thus to a higher residual load bearing capacity (Singh and Stelzer 2015).
3.Filter factory Wilsdruff – project example
3.1.Starting point
At the site in Wilsdruff, Saxony, Germany, Europe's most modern dialyzer manufacturing facility is being built on behalf of a major German medical device manufacturer. During the first phase of construction, this filter factory is to become the flagship of the entire corporate group and be prepared for a campus-like expansion. Thus, the entrance area is already assigned both for aesthetic and representative tasks in addition to its function as a space enclosure (see Fig. 4).
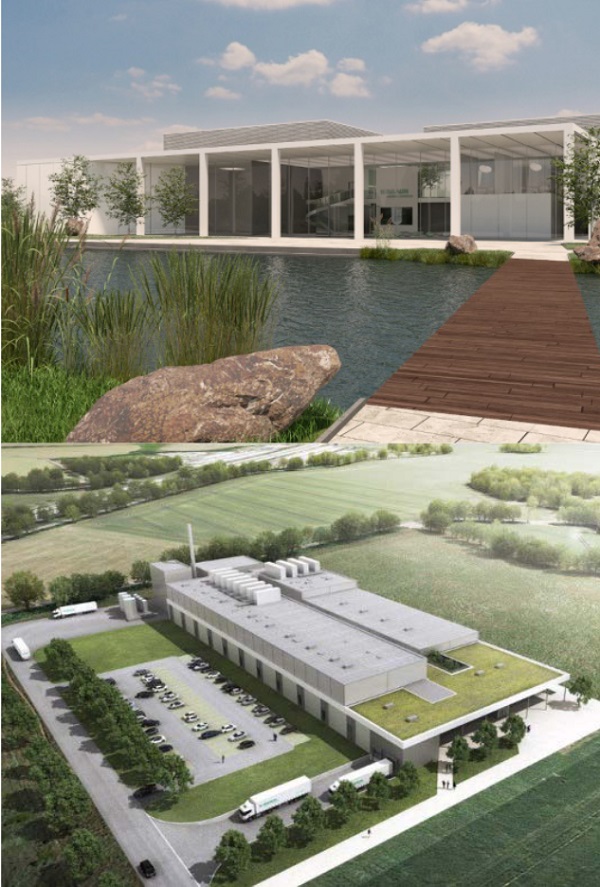
For the planner, the challenge of this project was the requirement that there should be no vertical supporting elements in the form of facade posts. Thus, the individual glass panes with dimensions of approx. 7.25 m x 2.40 m had to span over the long side with only two-sided bearings. Even single-pane glazing is a demanding task for such spans, and it becomes a challenge for insulating glass. However, it is not the glass stresses that are the difficulty, but rather the large deformations lead to additional loads on the edge seal of the insulating glazing and thus to potential problems with the durability of the components.
3.2.Requirements for the use of structural PVB interlayer with shear coupling
In Europe, there are currently no uniform, harmonized standards that regulate the construction with glass, glass design and dimensioning. A number of attempts are being made and significant progress has been made with the draft standard prEN 16612. However, a schedule for an introduction is currently not predictable. This means that it is currently the sovereignty of the individual states to determine how and if an interlayer actually contributes to the load resistance of a laminated safety glass and whether it is taken into account in a design. Since the interlayer material has viscoelastic properties, its tensile and shear modulus depends on temperature and time. This means that an approach is only possible if the existing conditions and load influences on the structure are known.
According to the German standard for design, dimensioning and construction for glass (DIN 18008), it is not possible to take into consideration the film properties for the load resistance without a separate approval. This meant that a general building authority approval had to be obtained via the DIBt. In order to create comparable conditions for film manufacturers, criteria were published which have to be determined in detail by means of tests on materials and laminated glass. These include, among other things, the module values of the interlayer materials, the module values of the laminates, ensuring adequate quality control and the module values that can be used for calculation, that taking into account for the safety concept (Stevels and Haller 2017).
3.3.Planning, construction and realization
The use of structural PVB films with the approach of shear coupling has some positive features. On the one hand, glass deformation can be significantly reduced with the same glass structure. If the deformation of the glazing is not problematic even without rigid interlayer, the total thickness of the glazing can be reduced by using stiffer PVB films. On the other hand, due to an improved stress utilization of the glazing, it may be possible to completely avoid prestressed glass. Further advantages are the improvement of the residual load-bearing capacity of overhead glazing and cantilevered structures such as columns.
However, experience has shown that the fundamental purpose of the application is not to reduce the glass structure, but rather to reduce the occurring deformations. This is accompanied by an improvement in the durability of the composite and in the optical quality. As these optimizations can already be achieved with a low coupling effect, structural PVB films such as the Saflex®-DG series can also be used.
3.4.Quality requirements and quality control
The use of glazing with structural PVB interlayer using the approach of shear coupling requires not only high-quality production but also extensive production monitoring. This is regulated in detail by the general type approval issued by the DIBt and includes tests by the manufacturer of the interlayer material as well as by the manufacturer of the laminated safety glass.
The moisture content of the interlayer and shrinkage is determined regularly in the production plant of PVB films and the pummel test is carried out on a test laminate, whereby previously defined limits must be achieved. In the case of glass refiners, the laminate quality is checked regularly by testing at high temperatures and by determining the film moisture or the pummel value. In addition, samples for ball drop tests can be demanded.
As production quality is not only ensured by means of in-house production control, but also by means of an external monitoring system, reserve samples are provided for testing within this context. At the same time, the glass refiners are supported from interlayer suppliers in the form of regular checks on laminates from production to check typical film and laminate properties by testing adhesion, laminate moisture or the general processing quality by means of bake and boil test.
3.5.Production and on-site installation
The processing of Saflex®-DG41 film can be carried out in both the nip-roll and vacuum bag process. The parameters used are not significantly different from those of conventional PVB films. For this reason, structural PVB interlayercan be processed on the same equipment and with the same machinery tools. There is no need for time-consuming changeover times when switching production. As a result, standard products and products with increased requirements can be produced in parallel. The following autoclaving process is also carried out under the same process parameters as for laminated safety glass with conventional PVB film at a temperature of 130-140 °C, 10-14 bar pressure and holding times that are adapted to the glass structures (see Saflex®-DG series or Trosifol®-ES series product description).
The glass of the filter factory Wilsdruff is a double insulating glass (TG-THERM®sun) consisting of a double laminated safety glass (TG-PROTECT® DG-S) as an inner pane and a triple laminated safety glass(TG-PROTECT® DG-S) as an outer pane. So, both the nip-roll and the vacuum bag process have been used to produce the laminated glass. After the production of the double insulating glazing, the metal profiles were then bonded to the step of the insulating glass with an injection mortar. These metal profiles are then used to assemble the glasses with the substructure on site at a later stage. Figure 5 shows the finished insulating glass units with the attached metal profile.
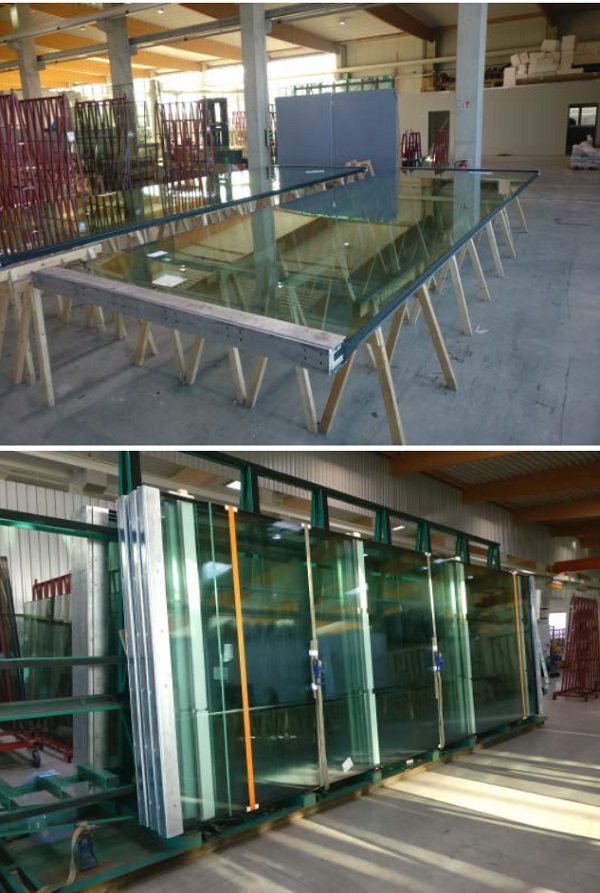
The insulating glass units were delivered to the construction site on internal loading racks and unloaded (see Fig. 6). Due to the high weight of the individual insulating glass units of more than 2.5 t per element, special lifting technology with heavy-duty vacuum suckers was used to lift the glazing into the façade and hold it in place for installation on site (see Fig. 7). The glazing elements were then attached to the substructure and the joints were sealed with a suitable silicone sealant.
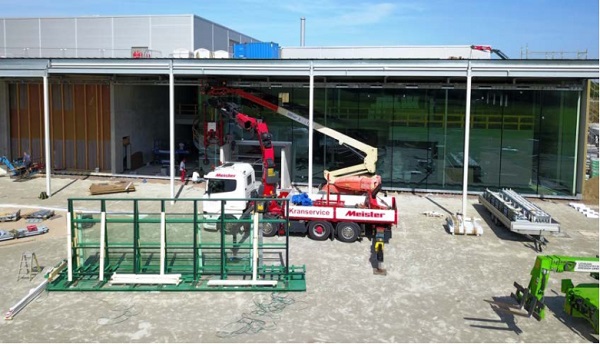
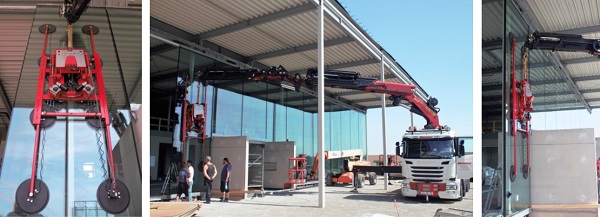
4.Summary
Due to their range of properties, structural PVB films are suitable for use in challenging projects in structural glass construction. In addition to a reduction of the maximum deformation with identical glass thickness, the maximum glass stresses can also be reduced by using rigid PVB interlayer. This may avoid the use of prestressed glass. The possibility of using a shear coupling for laminated safety glass results in a further reduction of deformations. Thus, a more reasonable dimensioning of the glazing is possible according to the installation situation and the expected loads.
The example of the project filter factory Wilsdruff shows that projects with glass panes in XXL format can also be realized with the use of structural PVB films and that it is not necessarily required to use ionomer interlayer such as SentryGlas®. This offers the glass processor the opportunity to make use of established and proven production techniques and to make better use of production capacity. Customers can be offered tailor-made products and solutions for a variety of special applications. Finally, architects and planners also have more room for flexibility in the design, construction and dimensioning of future building projects.
Acknowledgement
The author would like to thank Mr. Matthias Haller, Solutia Deutschland, Mr. Wim Stevels, Eastman Chemical Company and Mr. Frank Fischer, glasfaktor Ingenieure, for their constructive collaboration and support in writing this publication. This text has only been made possible by the contribution of know-how and a constant dialogue. In addition, Mr. Matthias Mehner from the façade contractor Metallbau Quosdorf made it possible to accompany and document the installation of the glazing on the construction site.
References
Deutsches Institut für Bautechnik: DIBt Mitteilungen Bauregelliste A, Bauregelliste B und Liste C, Ausgabe 2015/2. Berlin, DIBt, 2015.
Deutsches Institut für Bautechnik: Allgemeine bauaufsichtliche Zulassung Z 70.3-202 – Verbund-Sicherheitsglas mit einer Verbundfolie der Produktfamilie SAFLEX DG. Berlin, 2014.
DIN 18008-1:2010-12 – Glas im Bauwesen - Bemessungs- und Konstruktionsregeln - Teil 1: Begriffe und allgemeine Grundlagen (Glass in Building - Design and construction rules - Part 1: Terms and general bases). Berlin, Beuth, 2010.
prEN 16612:2017-12 – Glass in Building - Determination of the lateral load resistance of glass panes by calculation . Draft. Berlin, Beuth, 2015.
Deutsches Institut für Bautechnik: Allgemeine bauaufsichtliche Zulassung Z 70.3-230 – Verbund-Sicherheitsglas aus der Produktfamilie SAFLEX DG mit Schubverbund. Berlin, 2016.
Deutsches Institut für Bautechnik: Allgemeine bauaufsichtliche Zulassung Z 70.3-236 – Verbund-Sicherheitsglas mit der PVB-Folie TROSIFOL ES mit Schubverbund. Berlin, 2016.
Eastman: Designed for Strength – Saflex® DG Advanced Structural Interlayer. Technical Bulletin – Eastman Chemical Company, 2012.
Kothe, M.: Alterungsverhalten von polymeren Zwischenschichtmaterialien im Bauwesen (Ageing Behavior of Polymeric Interlayer Materials in Civil Engineering). Dissertation, Technische Universität Dresden, 2013.
Stevels, W., Haller, M.: Glasdesign mit steifen PVB-Folien für den konstruktiven Glasbau: Eine aktuelle Perspektive. In: Glasbau 2017. Berlin, Ernst & Sohn, 2017, pp. 385-395.
Singh Rooprai, M., Stelzer, I.: Post Breakage Strength Testing for Overhead Laminated Glass Applications. Technical Bulletin – Kuraray. Troisdorf, 2015.
Neugebauer + Rösch Architekten: Kompetenzcampus B.Braun bei Dresden. Projektbeschreibung. www.neugebauer-roesch.de, accessed 04.01.2018.