Interlayer modulus influences the stress laminated glass experiences under load. The determination of interlayer modulus data is complex, and until recently the design engineer would rely in most cases on interlayer modulus properties as determined on the foil, as published by the interlayer producers. Recently, standards or approvals have become available that provide guidance for interlayer modulus data for different interlayer product categories as either fixed values for a certain load scenario, or more generic material models.
Data for regular PVB and structural PVB products are available from e.g. prEN 16113 (2017), Dutch standard NEN 2608 (2014/2019), Norwegian standard NS3510 (2015) and German national approvals as associated with use of DIN 18008 (2011-2016). This work aims to provide an overview of the different PVB modulus values available for each of the interlayer categories in the different existing standards and other sources in a normative framework. With the work in CEN/TC250/ SC11 on a Eurocode for structural glass progressing, this will remain an active area for development for the foreseeable future. A consistent approach to the representation of interlayer modulus properties would support the internationally active design engineer.
Introduction
When reviewing interlayer modulus properties in different standards it is important to have some understanding of how interlayer properties are determined. Interlayer modulus properties are most frequently determined through measurements on the interlayer film directly using some form of dynamic mechanical analysis (DMA).
Data are collected at various temperatures, over a range of frequencies e.g. typically in a 0.1 to 100 Hz range, see e.g. ISO 6721 (Plastics - Determination of dynamic mechanical properties) [1], or specifically for interlayers in prEN 16613 (Determination of interlayer mechanical properties) [2]. Some specific recommendations have been made based on a comparison of different methodologies for interlayer materials [3, 4, 5], and references cited therein.
As interlayers are viscoelastic materials, the modulus of the material is a function of time (load duration) and temperature. The combined results of the measurements are translated to a so-called master curve of the material at a specific temperature using time-temperature superposition. This allows the determination of interlayer modulus values under load durations that far exceed the frequency domain over which the measurements took place.
For this approach to be valid, it is important that the materials are rheologically simple, and no combination of physical processes, such as moving through both a glass-transition and melting temperature, should take place during the measurement or in the time-temperature range to which the properties are transposed [6]. Particular to interlayers, Schneider et al. [7] concluded that poly(vinylbutyral) (PVB) materials are rheologically simple in contrast to some other interlayer materials e.g. poly(ethylene-co-vinylacetate) or poly(ethyleneco-methacrylic acid).
Alternatively, interlayer properties can be determined through mechanical studies on laminated glass specimens. The most widely used methods are four-point bending, normalized under EN 1288-3 [8] or torsion relaxation experiments [9-11]. As with DMA, results at different temperatures need to be obtained. The translation of measured deflection (in bending) or reduction in force (in torsion) to interlayer modulus can either be done analytically, or through the use of finite element models. A comparison of methods and their sensitivity as pertaining to interlayers is provided in references [12, 13].
Whichever methodology is chosen, the determination of interlayer modulus properties is relatively complex, as methodology, experimental parameters and equipment settings, and methodology of data treatment, all need to be executed with care. It has been suggested that a balanced approach would comprise DMA of the interlayer, in combination with a determination on laminated glass [14].
The output of the modulus determination as a function of time and temperature can take the form of tabular listed values or as a fitted model of the general Maxwell/Prony series type in combination with a temperature shift function. The latter has the advantage of being able to provide values for any load scenario within the validity range considered. Some more effort from the user for evaluation is required. Some publications provide both for user convenience.
For the selection of applicable load scenario’s, Eurocode 1991 “Actions on structures” provide primary guidance of the type of actions to be applied. National annexes and/or glass standards often provide guidance for the typical duration of loads associated with the evaluation of kmod to calculate the design load resistance of the glass. These can be used as the relevant duration of the action with the regards to the selection of applicable interlayer modulus.
With regards to dealing with relevant temperature for the load scenario under consideration, practices vary widely. In some countries the design load is applied at a fixed temperature, in other countries the design load is applied on the maximum temperature of the glass in a conservative approach. In some cases, the design load of the glass can be varied with temperature as a function of climatic conditions. As an example, a relationship between maximum wind speed (and therefore pressure) and temperature in Germany has been established and can be used in glass design.
Results and discussion
Before different standards or guidance documents can be compared, their scope, expression of interlayer properties, type of interlayer properties recognized, and calculation models to be used must be understood.
Standard review
prEN 16612 Glass in building — Determination of the lateral load resistance of glass panes by calculation
This draft standard [15] has undergone major changes in scope since publication of the first enquiry version in 2013. At the time, the key phrase in the scope simply read “This European Standard gives the principles of determining the load resistance of glass”. No restrictions were provided for use type, load type or type of fixing used. After processing of the comments on the 2017 enquiry version, the latest version of the scope known to the author – and expected to go to formal vote later this year – is:
This European Standard gives a method of determining the design value of the bending strength of glass. It gives: — the general method of calculation, and — guidance for lateral load resistance of linearly supported glazed elements used as infill panels; Examples of lateral loads are wind loads and snow loads and self weight of sloping glass and climatic loads on insulating glass units. This standard covers those infill panels that are in a class of consequence lower than those covered in EN 1990.
Many glass applications, where interlayer properties are most important for structural performance (cantilevered glass, point-fixed glazing), are thus excluded from the proposed scope of prEN16612. Classification of use types in consequence classes is a national competency, but applications where specific structural calculations are required, are unlikely to be deemed as being below the consequence classes of EN 1990.
Another major change in prEN16612 from 2013 to 2017 was that the simplified method for effective thickness calculation has been moved to an informative annex. In addition, the number of stiffness families has been reduced from 4 to 3, as in Table 1.
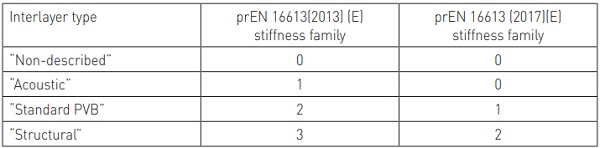
Climate load scenarios and wind storm load scenarios have been added to both prEN 16613 and prEN 16612. The Mediterranean wind gust load scenario has been altered, with the applicable temperature increased from 30 °C to 35 °C, along with a change of the modulus criterion. The modulus criterion for personal loads (crowds) has been changed. An overview of the load scenarios currently comprised in the draft standards and the minimum values of the interlayer modulus required to classify for a certain default shear transfer coefficient are listed in Table 2.
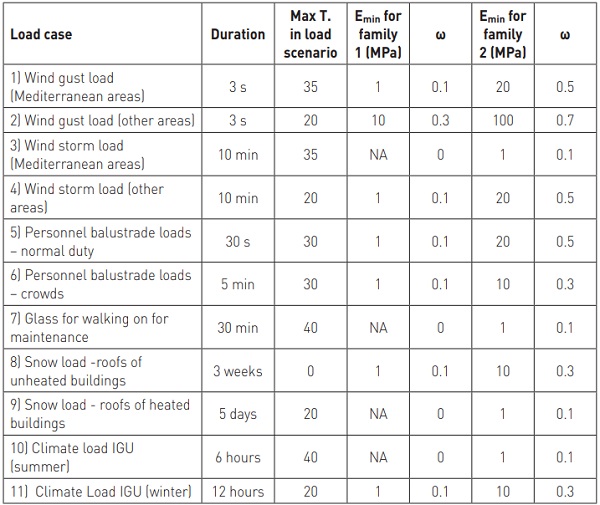
The list comprises only a limited number of modulus number relevant for determination (1, 10, 20 and 100 MPa), and an equal number of default shear transfer coefficients associated (0.1, 0.3, 0.5 and 0.7). Shear transfer coefficients can also be directly calculated from the interlayer modulus, e.g. as per ASTM 1300 annex X9 [16]. Key variables include glass and interlayer thickness, and minimum dimension of the pane. The results for different configurations can be plotted, along with the implied correlation between shear transfer coefficient and modulus from Table 2 (Figure 1).
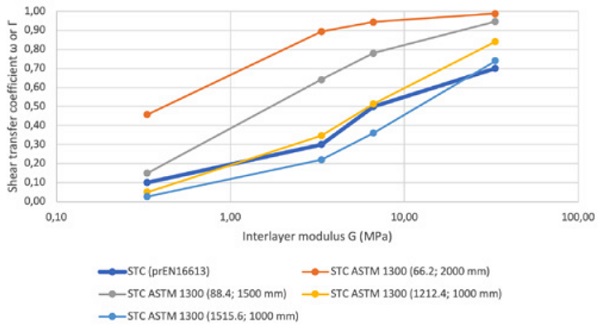
Thus, the default ω listed are conservative for configurations that are thinner than a 1212.4 configuration and have a short side larger than 1000 mm. This covers most of the glass for which a detailed dimensioning effort is undertaken. However, this element of conservatism is lost when the values for interlayer modulus as determined according to prEN 16613 are used directly in e.g. FEM modelling.
Although the future importance of prEN 16612 is reduced as a result of the changes to the scope, it remains an important source for consensus load scenarios, and guidance given for interlayer properties.
DIN 18008 and associated National approvals
German standard DIN 18008 Glass in building – Design and construction rules and its various parts cover a wide range of glass applications and types [17]. Some parts deal with specific clamping types (linear supported, point-fixed), some parts with glass with a specific function (barrier glazing, walkable glazing, occasionally accessible glass). In principle, favorable shear interaction between the individual panes in laminated glass cannot be taken into consideration when determining stresses and deformations for laminated glass and laminated safety glass under DIN 18008.
Under the former German national framework, up until 2016, properties not covered under a German standard could be claimed for a product if a National approval was released by the German Building Institute for that product, based on impartial data. This includes the use of shear transfer for glass design based on either an approval for the laminated glass or the interlayer itself. These approvals will expire in 2020 and cannot be renewed.
In the earlier approvals, interlayer properties that could be used for design were published in a tabular format for specific load scenarios. The last two approvals of this type issued, both for stiff PVB products, contained a Prony series for which the relevant value of the design modulus could be calculated for any load scenario [18, 19]. For conventional PVB types, allowed values only comprised a modulus value for wind load based on a correlation analysis. This singular value is hard to compare to other standards, as it is valid for German climatic conditions only
The modulus values provided through national approvals can be used for design directly, provided that the listed quality criteria are met. Any calculation models that reliably covers the structural conditions can be used, including geometrically non-linear models. In practical terms, finite element modelling is used mostly.
NEN 2608 – Glass in building: requirements and determination method
Dutch standard NEN 2608 [20] provides requirements and calculation methods for load resistance and deflection of soda lime glass predominantly statically loaded glass. Shear interaction through interlayers can be accounted for based on the interlayer properties.
The calculation of the shear contribution follows a rather circuitous route in which initially different shear transfer coefficients are calculated based on the interlayer properties for stress and deflection, followed by a calculation of effective thickness for stress and deflection. The calculation of the shear transfer coefficients is a function of the aspect ratio and the clamping type of the glass under consideration.
At the time of writing, this standard is the only standard to contain Prony series for interlayer materials such as conventional PVB and ionomer interlayers. These can be traced back to scientific publications [21. 22]. NEN 2608 is scheduled for revision in 2019, and it is expected that a material model for stiff PVB types is included. This model has been used for the calculation of modulus values represented in this article.
Since for the calculation method, the main requirements in the Dutch standard are that they are appropriate and sufficiently accurate, in practice the interlayer modulus as derived from the material models provided is directly inserted in to FEM type software.
NS 3510: Safety glass in construction works Requirements for design and classes in various application areas
Norwegian standard NS 3510 [23] provides a basis for the design and use of safety glass in construction works. Shear interaction through interlayers can be accounted for based on the interlayer properties as listed in tabular format for a number of load scenarios. Interlayer categories recognized are conventional and stiff PVB types, as well as ionomer interlayers. The values are intended for direct use in FEM software, taking into account non-linear effects, provided that the software has been proven to deliver consistent results with experimentation.
Standard comparison
The format and intended use of the sources listed above can be summarized as in Table 3.
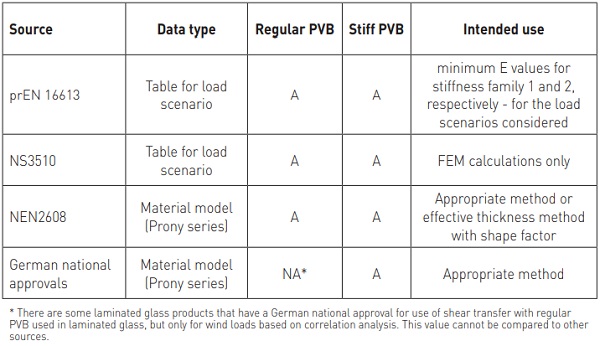
As the data in prEN 16613 and NS 3510 are only available in tabular format, only specific load scenario’s that are common to both standards can be compared. prEN 16613 was used as the basis as this standard has the widest range of load scenarios. The following five load scenarios were selected: wind gust loads (3s, 20 °C), live loads for barriers for noncrowded areas (30 s, 30 °C) and areas where crowds can occur (5 min, 30 °C) and snow loads for heated (5 days, 20 °C) and unheated buildings (3 weeks, 0 °C).
Even with this limited selection, actual load scenarios can be slightly different. For the conditions chosen, NS 3510 for live loads on barrier glass only applies to glass used inside buildings, and the duration of snow loads in Norway are understandably longer (1 week, respectively 3 months). It was assumed that conventional PVB would be classified as a stiffness family 1 interlayer, and a stiff PVB type as a stiffness family 2 interlayer for the cases considered, based on supplier data. If these smaller differences are overlooked, the comparisons as in Tables 4 and 5 can be compiled.
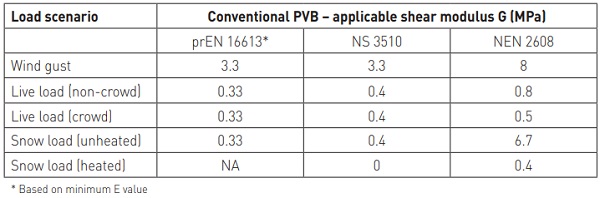
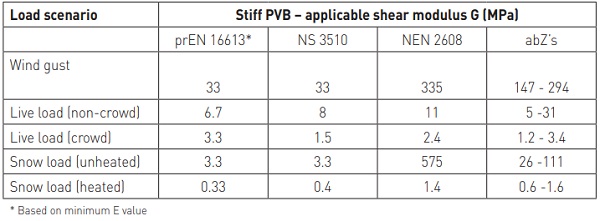
Bearing in mind that modulus vs. duration curves are typically plotted on a log-log scale, the design modulus values of the two different PVB interlayer type are in a relatively narrow range irrespective of the data source in a number of cases, e.g. for live loads.
In some cases, the absolute difference between data sources may be relatively large, but the behavior of the glass laminate won’t be affected as the modulus numbers all indicate relatively stiff behavior/efficient shear coupling, e.g. for wind gust loads. For snow loads on heated buildings, an exact understanding of the size, thickness, degree of sloping and intended glass configuration is needed to evaluate if the modulus numbers listed would influence the design.
Relevance of data
While any difference in numbers can be potentially confusing, it is important to understand in which range and for which configurations the modulus numbers become more critical for glass design to avoid spending excessive time on which number is most credible.
Therefore, three different cases where evaluated for development of stress and deflection using a FEM non-linear approach with the interlayer modulus as primary variable. The three different cases were:
1) 66.2, 4-side supported, uniform load 1 kPa, 3000 mm (h) * 2000 mm (w) (e.g. a façade window)
2) 1212.2, 2-side supported, uniform load 1 kPa, 3000 mm (h) * 2000 mm (w) (e.g. a shopping mall window)
3) 88.4, single side supported, 0.75 kN/m line load (0.5 kN/m* 1.5) op top edge, height 1100 mm using two elastic line supports for clamping at 10 and 90 mm height, width 1500 mm (e.g. a cantilevered balustrade).
The glass thickness and load were chosen to result in a stresses and deflections in a realistic range. The resulting stresses and deflections are represented in Figure 2.
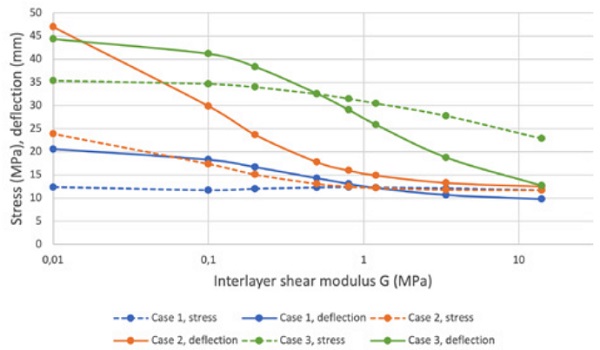
In case 1 (four-side support), the maximum stress the glass pane experiences is hardly dependent on the interlayer modulus, as stresses are effectively redistributed due to membrane effects. The location of maximum stress in the pane is a function of interlayer modulus, but a detailed discussion is beyond the scope of the current article. There is some dependence of the deflection on the interlayer modulus, but deflections are relatively limited for the dimensions of the glass pane. Above a value of 1 MPa for shear modulus, further reduction of deflections and stresses becomes increasingly incremental.
In case 2 (two-side support), the development of stress and deflection with interlayer modulus is more pronounced. Interlayer stiffness can significantly contribute to controlling the effects of load on glass. As with case 1), above a value of interlayer shear modulus of 1 MPa, further changes tend to become incremental, but even between 0.5 and 1 MPa stress and deflection development start to level off significantly.
Case 3 (single side support) is most sensitive to interlayer modulus increases, and both stress and deflection continue to drop up until the 10 MPa range. This case is most sensitive to choices in relevant temperature and duration, and data source.
Having a good understanding of the relevance of the exact interlayer modulus value on glass laminate behavior, as well as the variation of behavior that occurs as a function of clamping type helps in putting different values in perspective.
As a final consideration, it is important to note that commercial flat glass is only sold in a finite number of thicknesses. This has the tendency to mitigate relatively small differences in glass design as a result of differences in interlayer modulus. As an example, consider a symmetric laminate where using a certain interlayer modulus value, results in a minimum calculated thickness of 8.4 mm for the individual glass panes.
The calculation is repeated using another, and more conservative number, for the interlayer modulus value resulting in a minimum single glass pane thickness of 10.1 mm. In both cases, the configuration would need to be specified in nominal 10 mm glass to guarantee the desired performance.
Path forward
Even with a good understanding of glass laminate behavior as a function of interlayer modulus properties, dealing with different sources and values of interlayer modulus for a single material for a given load scenario is unsatisfactory. The development of a Eurocode glass might offer the opportunity to include a single source of modulus data for glass design for common categories of interlayer materials.
The data should preferably have the format of a Prony-series with temperature shift function to be able to deal with a large number of load scenarios. For user-friendliness, the number of elements should be reasonable for the use (e.g. 10-12) and some tables based on the material models selected could be added. The scope of the model in terms of maximum and minimum duration, as well as the applicable temperature domain should be clearly defined.
Conclusion
Interlayer modulus determination and use will be the subject of continued normative development. On one hand, there is a responsibility of the design engineer to have a high-level understanding of the effects of interlayer modulus of glass laminate behavior under load. On the other hand, representatives of academic and test institutes, building authorities and industry should collaborate in a normative framework to provide material models that are both safe for design and readily available for all interested, without the need to cross reference various sources.
References
[1] International Organization for Standardization: ISO 6721-1 Plastics – Determination of Dynamic Mechanical Properties_Part 1-12 (2011).
[2] European Committee for Standardization: prEN 16613 Glass in Building – Determination of interlayer mechanical properties (2013, 2017).
[3] Kuntsche, J.; Schuster, M.; Schneider, J.; Langer, S.: Viscoelastic properties of laminated glass interlayers – theory and experiments. In: Proceedings Glass Performance Days (Tampere Finland), 2015, pp. 143-147.
[4] Zhang, P., Stevels, W., Haldeman, S., Schimmelpenningh, J.: Shear modulus measurements of structural PVB interlayer and prEN 16613. In: Proceedings Glass Performance Days (Tampere Finland), 2015, pp. 148-152.
[5] Stevels, W.; D’Haene, P.; Zhang, P.; Haldeman, S.: A comparison of different methodologies for PVB interlayer modulus characterization. In Proceedings Challenging Glas 5, Bos, F.; Louter, C.; Belis, J. (eds), Gent, 2016.
[6] Ferry, J.D.: Viscoelastic properties of polymers. 3rd Ed. Wiley, New York, 1980.
[7] Schneider, J.; Kuntsche, J.; Schuster, M.: Mechanical behavior of polymeric interlayers. In: Proceedings Glas im konstruktiven Ingenieurbau 14 (Munich Germany), 2016, Chapter 16.
[8] European Committee for Standardization: EN 1288-3 Glass in building -- Determination of the bending strength of glass -Part 3: Test with specimen supported at two points (four point bending) (2000).
[9] Kasper, R.: Tragverhalten von Glasträgern. Dissertation RWTH Aachen, Aachen Germany 2003.
[10] Callewaert, D., Belis, J., Van Impe, R., Lagae, G., Vanlaere, W.: Refined set-up for pure torsion of laminated glass. In: Proceedings Glass Performance Days (Tampere Finland), 2007, pp. 118-121.
[11] Stevels, W.M.: Effect of different sources of interlayer modulus data for glass design: the structural PBV case. In: Proceedings Glass Performance Days (Tampere Finland), 2017, pp. 393-396.
[12] Botz, M.; Kraus, M.A.; Siebert, G.: Sensitivity analysis for the determination of the interlayer shear modulus in laminated glass using a torsional test, Glass Structures and Engineering, 3 (2018), pp. 355-372.
[13] Botz, M.; Kraus, M.A.; Siebert, G.: Experimental determination of the shear modulus of polymeric interlayers used in laminated glass. In: Proceedings GlassCon Global 2018, pp.31- 38.
[14] Siebert, G.; Botz, M.; Kraus, M.A.: Comparison of LSG according to German and European standards. In: Proceedings of Engineered Transparency 2018, pp. 111-120.
[15] European Committee for Standardization: prEN 16612 Glass in Building – Determination of the load resistance of glass panes by calculation and testing (2013, 2017).
[16] ASTM International: ASTM E1300 -12a: Standard Practice for determining the load resistance of glass in buildings (2012).
[17] Deutsches Institut für Normung: DIN 18008 parts 1-6 Glass in building – Design and construction rules, parts 1-6 (as of 2010).
[18] German building institute: VerbundSicherheitsglas aus der Produktfamilie Saflex DG mit Schubverbund. Generic building approval Z-70.3-230, Berlin 2016
[19] German building institute: VerbundSicherheitsglas mit der PVB-Folie TROSIFOL ES mit Schubverbund Z-70.3-236, Berlin 2016
[20] Nederlands Normalisatie-instituut: NEN 2608 Vlakglas voor gebouwen - Eisen en Bepalingsmethode (2013) and revised version in preparation.
[21] Bennison, S.J.; A. Jagota, A.: Smith, C.A.: Fracture of glass/PVB Laminates in biaxial flexure, J. Am. Cer. Soc., 1761-1770, 1999.
[22] De Vogel, K.: Temperature effects on torsional behavior of glass/ionomer laminates Master Thesis University of Gent Belgium (2008).
[23] Standard Norge: NS 3510 Sikkerhetsruter i byggverk – Krav til prosjektering og klasser for ulike bruksomrader (2015) (“Safety glass in construction works - Requirements for design and classes in various application areas”)