Source: Glass Structures & Engineering
Authors: Menandros Ioannidis, Faidra Oikonomopoulou, Telesilla Bristogianni, Marcel Bilow & Anna Maria Koniari
DOI: https://doi.org/10.1007/s40940-024-00264-1
Abstract
Glass casting displays great forming potential allowing for the realisation of three-dimensional glass elements of virtually any shape and size, as showcased in glass art. Disposable mould technology seems to be ideal for the fabrication of such customised and complex geometries, including for architectural and structural cast glass components deriving from structural topology optimization, since it offers great shape freedom and cost effectiveness. However, currently, glass casting on disposable moulds faces the major drawback of a resulting rough and opaque glass surface quality, requiring considerable post-processing to yield a glossy, smooth surface. This in turn results in a compromised dimensional accuracy and on increased time and production costs. If the surface remains unprocessed, it can greatly affect not only the visual but also the mechanical properties of the cast glass element. Aim of this research is to improve the surface quality of complex glass components cast in disposable moulds, directly during demoulding, reducing in this way the need for post-processing.
To achieve this the research focuses on exploring ways to pre-process disposable moulds. In specific, the research focuses on series of kiln-cast laboratory experiments at various maximum firing temperatures / annealing schedules involving the use of two different types of disposable moulds, 3D-printed sand moulds and silica plaster moulds (Crystalcast®), and the application of refractory coatings, coating combinations and protective layers. The experimental work conducted thus far indicates that the best results are obtained at the lowest maximum temperature tested (870 °C), with the combination offering the best finishing quality to be a synthetic (ceramic) sand mould coated with Crystalcast® and Zirkofluid® (6672, 1219). Scaling-up of the kiln-cast prototypes unveils a complex correlation between the maximum dwell time at the maximum firing temperature and the casting effectivity/ performance of mould materials and coatings.
1 Introduction
Glass is an optically transparent, durable, and infinitely recyclable material ideal for architectural and structural applications in the built environment. Laminated float glass is predominately used for structural applications. Characteristic and distinct examples of such structures are the Centre Administratif (Brunet Saunier Architecture 1995), the Yurakucho canopy (Rafael Viñoly Architects, 1997) (Lusas), the House laminata (Kruunenberg Van der Erve Architecten, 2001) (Divisare), the Apple Store at Fifth Avenue NY (Bohlin Cywinski Jackson 2011) (renovated 2011), Steve Jobs Theater (Foster + Partners, 2017) (EOC) and the Skywalk for Bründl Sports (Blocher Partners, 2021); (Seele 2020). While these applications are redundant and safe, they are governed by the 2-dimensionality of the float glass panes (Oikonomopoulou et al. 2015).
Latest developments in fabrication methods of glass, such as 3D printing of glass (Klein et al. 2015; Inamura et al. 2018) and casting of glass (Oikonomopoulou et al. 2018a, 2018b, 2020; Oikonomopoulou 2019; Bristogianni 2022; Damen et al. 2022; Giesecke and Dillenburger 2022) display the attempt to escape from the 2D design space and explore the potential of 3D glass components for architectural applications. Casting of glass shows great potential in 3D structural applications in realised projects such as the optical house (JP), the crystal houses (NL), Mirage (USA), Qaammat Pavillion (GL), the light vault (UK), the Atocha memorial (SP) and the Qwalala Sculpture (IT). All these projects consist of repetitive cast glass elements that mimic the shape and size of standard masonry brick, with a mass limited to less than 10 kg (Oikonomopoulou et al. 2020) (see Fig. 1). Examples of complex, customised monolithic shapes at large scale are currently limited to telescope blanks (up to ⌀ 8.4 m) (Zirker 2005; Oikonomopoulou et al. 2018b) (Fig. 2a) and art objects, e.g. Roni Horn, 2024; Karen LaMonte (Hauser and Wirth; Smithsonian American Art Museum).
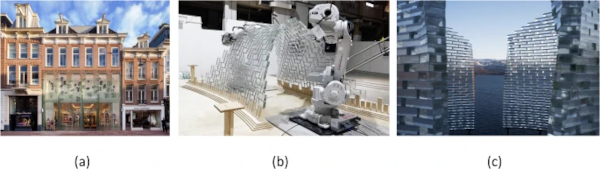
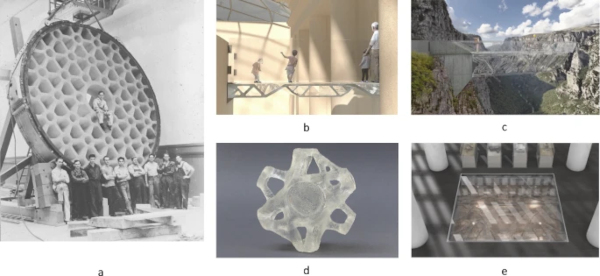
For the realisation of customised and complex monolithic 3D structural glass components of considerable dimensions, design, material and fabrication particularities need to be addressed. Glass requires a lengthy annealing process, as displayed in the work of (Klein et al. 2015; Oikonomopoulou 2019; Damen et al. 2022; Oikonomopoulou et al. 2022; Koniari et al. 2023). In cast glass, the mass and thickness of the designed object increase the annealing time exponentially, skyrocketing the cost and the feasibility of such voluminous glass components (Oikonomopoulou et al. 2018b). Through the implementation of mass optimization, such as by utilising topology optimization (TO), the mass and volume distribution of the glass objects can be greatly reduced, allowing for large monolithic structural components of minimised annealing time, leading to a more feasible and cost-efficient production (Damen et al. 2022; Oikonomopoulou et al. 2022; Koniari et al. 2023); (Fig. 2b, c, d, e).
TO designs, even though they contribute greatly to an optimised shape of minimum mass and thus of a feasible annealing time, they also result in complex, customised forms (Fig. 2) that are challenging to produce with the currently available fabrication methods for moulds. On one hand, high-precision permanent metal (steel or graphite) moulds can yield a glossy, smooth surface quality and high accuracy, their high cost can render them economically unsustainable for the casting of massive, one-off glass units. Moreover, even though multi-part metal moulds can be engineered to accommodate perplex forms, they are still unable to accommodate undercuts (due to demoulding), limiting shaping freedom. On the other hand, disposable moulds are preferred for small batch castings and customised components, as they are significantly cheaper (Niehe 2017) than the permanent metal moulds. Other advantages of disposable mould technology, especially 3D-printed sand moulds (3DPSM) produced via binder jetting, are that they allow for great shape and size freedom.Footnote1 On the downside, glass objects cast on such moulds result in a rough and opaque glass surface, that necessitates post-processing, a time-and labour-intensive process (Oikonomopoulou et al. 2020).
The successful implementation of 3DPSM for casting a TO steel node (Fig. 3) realised by Arup and 3Dealise (Galjaard et al. 2015), as well as the fabrication of two TO slabs in concrete by DBT group at ETH Zurich (Jipa et al. 2016), highlight the potential of this mould fabrication method for glass casting. This claim is further supported by previous experimental work conducted at TU Delft (Oikonomopoulou et al. 2020; Damen et al. 2022), where a TO column segment was prototyped in glass (Fig. 4).

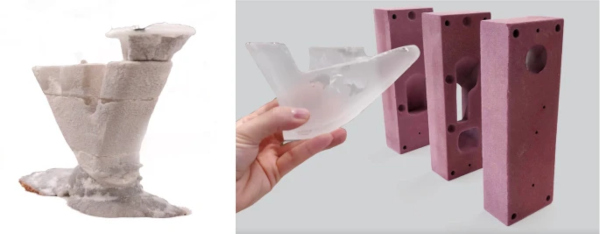
1.1 State of the art
Typically, 3DPSM are used for foundry casting (hot-pouring) of aluminium or iron objects. During the hot-pouring of metals, 3DPSM are exposed to high temperatures for a short period of time. On the contrary for kiln casting of glass, moulds need to be exposed to high temperatures for a prolonged time which has an unknown effect on the integrity of their structure. Extensive research in kiln-casting using disposable moulds has been conducted at TU Delft (Bristogianni 2022; Oikonomopoulou 2019). Follow-up research work of (Oikonomopoulou et al. 2020) where different 3DPSM are tested under kiln-casting suggests that inorganic binder is the most promising option and demonstrates that the introduction of a protective layer between the mould and the glass can significantly improve the surface quality. In fact, the inorganic binder is as stated by (ExOne 2023) the preferred binder for 3DPSM in terms of environmental impact and finishing quality. The results while encouraging, still mandated a lot of manual post-processing (polishing) to account for the surface roughness (Fig. 4).
Recent application of refractory coatings on glass casting by (Giesecke and Dillenburger 2022) displayed improved results in the contact (mould to glass interface) surface quality of foundry- and kiln-casted glass specimens at 1200 °C and 900 °C respectively. The experiments were conducted using 3DPSM fabricated by binder jetting additive manufacturing of silica sand and the use of organic and inorganic binders. The moulds were then coated with a combination of Zirkofluid® (isopropanol-based) and graphite-water dispersion coatings achieving good surface quality directly after demoulding. The most promising coatings were tested for foundry casting (hot-pouring) (Fig. 5f–h) of small cylindrical samples with the best combination suggested by the authors to be Zirkofluid® 1219 + Zirkofluid® 6672 + Bonderite® L-GP (Fig. 5h). Larger scale and more complex shaped samples were tested only under hot-pouring which is associated with a considerably reduced exposure of the mould to the maximum temperature (max. temperature) compared to kiln-casting. Up to today, there is no extensive testing of the most promising binder (inorganic) and refractory coatings on kiln casting of glass at various annealing schedules and at the associated prolonged exposure to heat, testing different types of sands and more complex geometries that can provide some first insights on the effect of the scale factor.
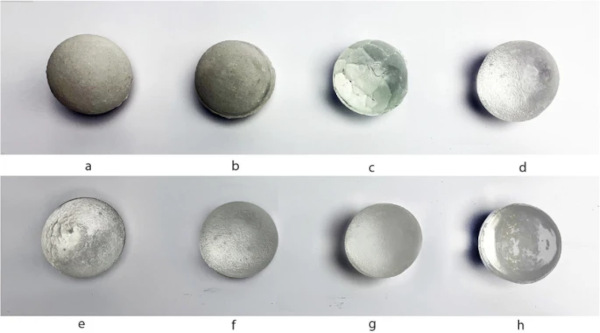
1.2 Approach
Using as a basis the prior knowledge and research by TU Delft and ETH Zurich, this experimental work aims to shed more light on the potential of fabricating voluminous and customised glass elements for architectural and structural applications using 3DPSM and refractory coatings for kiln-casting that can yield transparent and smooth glass surfaces in contact with the mould, therefore minimising post-processing.
The objectives of this research are:
- To understand the behaviour of 3DPSM produced using different sand types at different firing temperatures and different annealing programs;
- To explore the potential of the use of refractory coatings applied on disposable moulds and especially 3DPSM, on casting customised and complex glass forms;
- To access the effect of scale (scalability on the results), since the more massive the cast object, the longer the time that the mould is exposed to the max. temperature (Oikonomopoulou et al. 2018b).
2 Methodology and materials
The research uses as a starting point the previous findings on 3DPSM and associated coatings for glass casting by the research groups of TU Delft and ETH Zurich. All 3DSPM presented in this research have been produced via binder jetting additive manufacturing technique and inorganic binder and are sponsored by ExOne. The relevant refractory coatings are sponsored by Hüttenes Albertus Chemische Werke GmbH (HA). Personal communication with ExOne and HA has further shed light on the properties of the moulds and refractory coatings. The experiments involve the use of five different mould geometries as shown in Table 1.
Table 1 Geometries of moulds used for the experiment series A-D followed by glass mass and dimensions in cm - Full size table
The moulds for geometries 1, 2 are printed in two different types of sand: (a) quartz (white colour) and (b) ceramic/ synthetic (terracotta colour). Geometries 3 and 4 are fabricated from ceramic sand. Geometry 5 is fabricated in silica plaster (Crystalcast®) through the lost-wax technique investment casting method.
The coatings used are: a. Zirkofluid® 1219, b. Zirkofluid® 6672, c. Arkopal B5® (ΗΑ). The protective layers applied between the mould and the coating are (a) shelf-primer ® (Bullseye glass co.) and (b) Crystalcast® (Proverto Gruppo).
Two types of glass are used for the kiln casting experiments. For casting at higher than 900 °C recovered and cleaned fully tempered soda lime float glass is used. For casting under 900 °C Bullseye® Tekta AK 90 is the preferred type of glass. For series D (hot-pouring) glass recipes are indicated per sample.
All kiln casting experiments are done on a Rodhe® ELS 1000S electric kiln and samples are analysed under a Keyence® VHX-7000 digital microscope (20–200 × zoom). For the hot-pouring experiments glass is heated up inside a Carbolite® Gero HTF 1700 and is then annealed inside a Rodhe® ELS 200S electric kiln.
Samples of all test series are named following the principle as indicated in Fig. 6 below:
- Indicates the test series: A, B, C or D
- Defines the type of mould material: C = Ceramic sand moulds, Q = Quartz sand mould or S = silica plaster moulds (Crystalcast®)
- Shows the type of protective layer: S = silica plaster (Crystalcast®), P = Shelf-primer®, 0 = no protective layer
- Indicates the coating applied: A = Arkopal B5®, Z = Zirkofluid® 1219, X = Zirkofluid® 6672 or 0 = no coating
- Defines the number of coating layers: 0 = no coating, 1 = one time or 2 = two times, followed by application method: B = Brush, F = Flow or I = Immersion
- Sample number: 0 = 1120 °C normal, 1 = 1120 °C slow, 2 = 970 °C normal, 3 = 870 °C normal, 4 = 870 °C normal + 2 h, 5 = 870 °C normal + 4 h, 6 = hot-pouring.
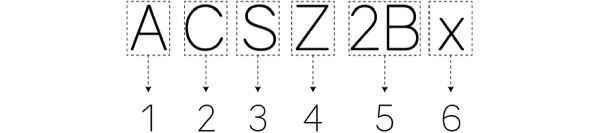
If two coatings are applied 4 and 5 are repeated for the second layer of coating before 6. If the same set-up is fired under the same temperature, then a letter is appended at the end after 6.
2.1 Experimental series
Surface quality and transparency of the cast glass surface in contact with the mould are investigated by a series of experiments conducted at the glass lab of TU Delft (Stevin II Lab). The following set of experiments are conducted (Table 2):
Table 2 Experiment series overview - Full size table
Series A: The aim of this series is to test the effect of various annealing schedules on two different types of 3DPSM. Coatings are introduced for an overview of the final set-up and for getting some first insights for the next series of experiments. The coatings are applied in small dents scraped off the surface of geometry 1 (Table 1) moulds using a small spoon, or in the cavity of geometry 2 (Table 1). Sand mould pieces are placed in the oven following different annealing cycles to determine if and how the prolonged exposure to heat affects the structural integrity of the moulds.
Series B: Kiln-casting experiments are carried out to investigate the resulting finishing quality of the glass surface in contact with the mould, using different types of coatings and protective layers applied on 3DPSM (ExOne). Small cylindrical-shaped specimens (geometry 2 negative) are the outcome of this set of tests. The contact surface of the glass is examined optically to determine the best combination in terms of optical transparency and surface quality.
Series C: Slightly larger scale prototypes (up to 40 cm) (geometry 3, 4 and 5) (Table 1) are realised using the most promising set-up as indicated in experiments series A and B. The larger and more complex shaped glass geometries help evaluate the scaling effect and prolonged exposure at high temperature on the effectivity of the coatings and overall casting feasibility.
Series D: Finally, a set of hot-pouring experiments is conducted using geometry 2, on a limited selection of mould types and coatings/coatings combinations. The goal of this series of experiments is to explore alternative fabrication methods better suited for industrial application.
2.1.1 Annealing schedules
For series A and B, four annealing schedules (1120 °C normal, 1120 °C slow, 970 °C normal, 870 °C normal) with three distinct max. temperatures are used, as shown in Fig. 7. For the schedule of 1120 °C two heating-up rates are tested: 50 °C/h and 30 °C/h, to address initial concerns of the heating-up curve affecting the integrity of quartz sand moulds.

For series C a slightly modified 870 °C normal schedule is used. For geometry 3 and 4, two (2) additional hours at max. temperature (870 °C) and for geometry 5, four (4) additional hours at max. temperature (870 °C) are added.
2.1.2 Assessment of samples
Assessment of the visual quality of samples in terms of smoothness and transparency is purely qualitatively based on visual inspection of the cast glass specimens.
2.2 Moulds preparation
2.2.1 Protective layer application
The protective layer is applied directly on the 3DPSM and before the coating. Two materials are used: Crystalcast® and Shelf-primer® (kiln wash). The former is based on silica plaster and is used for investment casting, through the lost-wax technique and has been successfully tested on temperatures of up to 1000 °C (Oikonomopoulou, Singh Bhatia, et al., 2020). The latter is used as a separator between mould and glass with an unknown maximum service temperature.
The protective layer is applied with the use of a soft natural brush (brush application) on 3 layers with a minimum drying time between each layer of 1.5 h at room conditions and dilution ratio as indicated in Table 3. The set-up is then left to fully dry for 24–72 h before any coating application.
Table 3 Protective layers used during the experiments - Full size table
2.2.2 Coating Application
Two types of coatings have been used: isopropanol-based (Zirkofluid® 1219 and 6672) and water-based (Arkopal B5®). The coatings are applied in one of the following ways: (i) Brush application, (ii) Flow application, (iii) Immersion application.
In specific, in the flow application, coatings are diluted according to the ratios in Table 4 and are poured into the cavity of the mould. After approx. 6 s the mould is flipped upside down to remove any excess liquid. The immersion (dipping) application is performed in the same way as the flow application, with the only difference being the dwell time, in this case approx. 13 s. The process is repeated up to two times as indicated by the name of each sample. In case of a second layer, this is applied after the first layer is completely dry. For samples up to the size of geometry 5, the drying time is approximately 1.5 h at ambient conditions (for the isopropanol-based coatings) or until the previous coating layer obtains a complete mat look (for the water-based coatings). For the application of Arkopal B5® directly on the 3DPSM, fast drying using a hot air blower is used, to reduce the detrimental effect of the water-based coating on the bearing capacity of the inorganic binder of the 3DPSM. For the brush application method, a soft brush from natural fibres is used. For the application of Zirkofluid® 6672 ventilation or specialised respiratory protection is necessary according to the safety instructions, so the process in this case is performed inside a fume box.
Table 4 Coatings used for the experiments - Full size table
3 Results
3.1 Series A
The provided 3DPSM, are typically used for foundry casting (hot-pouring) of metals such as aluminium or iron, which require lower max. temperature and considerably lower contact time with the mould (and thus, exposure of the mould to a high temperature) compared to glass. According to (Anna Gowsalya and E. Afshan 2021) the temperature of molten aluminium does not exceed ~ 850 °C and the max. temperature of the mould remains below 200 °C. Prior tests of glass casting on 3DPSM have been conducted up to 810 °C for approx. 120 h total dwell time (Oikonomopoulou et al. 2020) and up to 900 °C for approx. 27 h of total dwell time (Giesecke and Dillenburger 2022). A comprehensive, detailed study of the behaviour of 3DPSM under kiln-casting has not been conducted for the combination of high temperature and prolonged exposure to high heat.
The mould geometries 1 and 2 are tested in the kiln following different annealing cycles, with different max. temperature and heating-up rates. Depending on the maximum firing temperature, a different type of glass is used as specified in Chapter 2. Before firing moulds are placed inside a heat-resistant container (either in direct contact or on top of sand Fig. 8), or are embedded in sand, as indicated in Table 5. Some first insights from this first set of experiments are summarised in Table 5 and discussed in depth per type of sand.
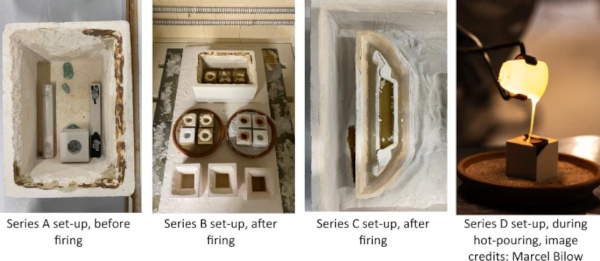
Table 5 Overview of test series A. Naming system as described in the methodology - Full size table
3.1.1 General observations on Quartz sand printed moulds
Samples AQ0A1B0, AQ0A1F0, AQ0Z1B0, AQ0Z1F0 and AQ00000 (Table 5), fired at 1120 °C normal annealing schedule display cracking at multiple points. Specifically, moulds become porous, and the glass attaches to both the sand of the mould and the coating, regardless of the type and application method. After the firing, all samples lose any bearing capacity and collapse under contact.
Similar results can be observed at 1120 °C slow annealing schedule for samples AQ0Z1F1, AQ0Z1B1, AQ0X1F1, AQ0A1F1, AQ0A1B1 and AQ0X1B1 (Table 5). The difference this time is that the bars (geometry 1) are embedded in sand, thus, cracking is less severe, but casting cannot be considered successful. Samples have no bearing capacity and glass, coatings and sand become one.
Tests at 970 °C normal reveal some possible compatibility issues between this type of sand (quartz) and coatings. Sample AQ0X1B2, AQ0X1F2, AQ0Z1B2 and AQ0Z1F2, which are coated with isopropanol-based coatings (Zirkofluid® 1219 or 6672) and regardless of the application method, display cracking and sand-to-glass adhesion. Sample AQ0A1B2 and AQ0A1F2 coated with water-based coating (Arkopal B5®) display no mould cracking but still, the glass adheres to the coating and mould materials. Sample AQ00002 (placed on top of sand and without coating) indicates no cracking. Overall, the integrity loss at this temperature is lesser than at 1120 °C.
Finally, samples AQ0X1F3, AQ0Z1B3, AQ0Z1F3, AQ0X1B3, AQ0A1B3 and AQ0A1F3 fired at 870 °C normal maintain their integrity, with the cast glass adhering minimally to the mould and primarily to the coating. Sample AQ0A1B3 coated with Arkopal B5® (brush application) displays areas of smooth and transparent glass.
3.1.2 General observations on Ceramic sand printed moulds
Ceramic sand moulds (terracotta colour) perform differently than quartz sand moulds. For this type of sand, only geometry 2 is tested at annealing schedule (a) 1120 °C normal, (b) 970 °C normal and (c) 870 °C normal. On all samples (AC0Z2I0, AC0X2B2 and AC0A2F3) glass tends to adhere to the sand, rendering it impossible to achieve directly a clear and transparent surface after demoulding. At all temperatures/ annealing schedules, this type of sand hardens after firing. Demoulding is challenging, requiring immersion of the mould in water and the use of a hammer to free the glass object.
3.1.3 Series A interim conclusions
Extensive tests using moulds printed with quartz and ceramic sand indicate that their behaviour is different. Quartz sand moulds lose a percentage of their integrity after firing at all annealing schedules, while ceramic sand moulds harden. This can be attributed to the different expansion coefficients of the two types of sands and the different amounts of inorganic binder used during their production.
According to (Roller et al. 2016) quartz sand has a higher expansion coefficient and a higher amount of inorganic binder is used to produce moulds of this sand (ExOne 2023), compared to the fully synthetic (ceramic) sand. When quartz sand moulds are exposed to high temperature their grain size increases and so does the porosity of the mould (Roller et al. 2016), increasing therefore the risk of glass penetrating the mould material and reducing the mould integrity.
On the contrary ceramic sand moulds grain expands minimally, while a lesser amount of binder is needed to obtain the same level of adhesion between sand grains. The hardening of ceramic sand moulds is in line with the observations of (Szymański and Borowiak 2019) stating that inorganic binder gains higher final strength after firing making demoulding more difficult.
Regarding coatings some possible mould–coating material compatibility is evident. In specific: Arkopal B5® displays less cracking when applied on quartz sand moulds, whereas the same applies for Zirkofluid® 1219 and 6672 coatings on ceramic sand moulds. Further testing of all annealing schedules and various thicknesses of coatings and protective layers is necessary to validate this preliminary result further.
3.2 Series B
The second set of experiments explores the application of different coatings and their combination on 3DPSM manufactured with both sands and moulds of silica plaster (Crystalcast®) as described in chapter 2.2. The results are compared with samples produced without any coating application. An overview of the test sets of this series can be found in Table 6.
Table 6 Overview of series B experiments per annealing schedule indicating the parameters and aims - Full size table
3.2.1 General observations regarding annealing schedule: 1120 °C normal
At 1120 °C normal annealing schedule, all sand mould samples display adhesion of the sand, coating and protective layers to the glass. The level of adhesion depends on the set-up but always results in an opaque and rough surface.
Glass samples cast on silica plaster moulds (Crystalcast®) exhibit less consistent results depending on the type of coating: they either display surface chipping and breaking (BS0Z2I0 and BS0X2I0) or have a rough and opaque finishing quality (BS0A2I0).
3.2.2 General observations regarding annealing schedule: 970 °C normal
Initial tests at 970 °C normal and application of coatings directly on the 3DPSM via brush and flow (single and double) display similar results to the ones at 1120 °C normal. Sand and coating adhere to the glass surface of the specimens (see Tables 7 and 8).
Table 7 Results of samples tested at 970 °C normal firing schedule using quartz sand moulds. Naming system as described in the methodology - Full size table
Table 8 Results of samples tested at 970 °C normal firing schedule using ceramic sand mould. Naming system as described in the methodology - Full size table
i. Quartz sand moulds (Table 7).
The combination of quartz sand mould and Zirkofluid® coatings (see Table 7) results in cracking of the coating layer (samples BQ0Z2F2, BQ0Z2B2, BQ0X2F2 and BQ0X2B2). The cracking of the coatings allows glass to penetrate the mould and attach to the sand. Samples examined from the contact side have intricate veining patterns matching the shape of the cracks on the coating. The top side of the glass shows a similar cracking pattern.
Samples without coating (BQ00002) and coated with Arkopal B5® (BQ0A2F2 and BQ0A2B2) show no cracking but yield an opaque and rough surface of the glass.
(ii). Ceramic sand moulds (Table 8).
For ceramic sand moulds cracking of the glass is present on specimens treated with Arkopal B5® (BC0A2F2 and BC0A2B2). All samples of Table 8 display similar contact surfaces. Noteworthy is the fact that the glass samples BC0X2F2 and BC0X2B2 released from moulds coated with Zirkofluid® 6672 (both flow and brush application) failed spontaneously long after the release. For this type of sand, separation of the mould and the cast glass element is hard and can lead to damage to the glass sample (e.g. sample BC00002 where no coating was applied).
(iii). Introduction of protective layer at 970 °C normal (Table 9).
Table 9 Results of samples tested at 970 °C normal firing schedule after the introduction of a protective layer of Crystalcast® (3X brush) between the mould and the coating. Quartz sand (top row) and ceramic sand (bottom row). Samples are cleaned only with a soft sponge and water. Naming system as described in the methodology - Full size table
Further experimentation at 970 °C normal using two different protective layers (Self-primer® or Crystalcast®) between the mould and the coating was introduced and applied as specified in Chapter 2 and Table 3.
The application of a Self-primer® (P) intermediate layer on quartz sand moulds with a single flow application of Zirkofluid® 1219 or Arkopal B5® coatings resulted in mould cracking and rough and opaque surface of the glass specimens (BQPZ1F2 and BQPA1F2).
The application of a Crystalcast® (S) intermediate protective layer displays promising results at this temperature in terms of transparency and surface quality of the contact side. Initial tests using a single layer of Zirkofluid® 1219 (BQSZ1F2) and of Akropal B5® (BQSA1F2) yield a translucent glass surface with minimal coating adhesion. Samples BQSX2F2, BCSZ2B2, BCSX2B2 and BCSA2B2, where two layers of coating are applied (brush and flow application), do not exhibit an improved surface quality. In fact, the application of multiple layers of coating (thicker coating overall) seems to result in their adhesion on the glass surface (Table 9). The brush application of the coating results in the imprint of the brush strokes’ texture on the glass surface (e.g. samples BCSZ2B2 and BCSX2B2).
3.2.3 General observations regarding annealing schedule: 870 °C normal
Taking into consideration the results from test series B thus far, Crystalcast® is applied as a protective layer in specimens cast under this annealing schedule. Initially, coatings are applied according to previous indications of mould–coating material compatibility: Arkopal B5® on quartz sand moulds and Zirkofluid® (1219 and 6672) on ceramic sand moulds. Later, Arkopal B5® is also applied on ceramic sand moulds with and without the use of a protective layer.
i. Quartz sand moulds (Table 10).
Table 10 Results of samples tested at 870 °C normal firing schedule using quartz sand moulds. Samples are cleaned only with a soft sponge and water. Naming system as described in the methodology - Full size table
Best results in terms of transparency and optical quality are observed when a dual layer of Arkopal B5® is applied directly on the mould via brush (quick drying) (BQ0A2B3). The addition of Crystalcast® protective layer does not improve the surface quality to the extent of justifying the additional time and effort involved in the dual protective layer/ coating process (BQSA2F3). Flow application of Arkopal B5® directly on the mould results in coating adhering to glass (BQ0A2F3). The use of the mould without coating outputs a rough and opaque surface (BQ00003).
ii. Ceramic sand moulds (Table 11).
Table 11 Results of samples tested at 870 °C normal firing schedule using ceramic sand moulds. Samples are cleaned only with a soft sponge and water. Naming system as described in the methodology - Full size table
Application of Zirkofluid® 1219 or 6672 directly on the mould, regardless of the application method, yields an opaque contact surface (BC0Z2F3, BC0Z2B3, BC0X2F3 and BC0X2B3). The use of Crystalcast® as an intermediate, protective layer shows promising results, especially when combined with Zirkofluid® 6672 (BCSX2F3), delivering the best overall surface quality and transparency. Similar surface quality can be achieved with the use of Crystalcast® and Zirkofluid® 1219 (BCSZ2F3). Application of Arkopal B5® either directly on the mould (BC0A2F3) or using a protective layer of Crystalcast® (BCSA2F3) outputs a rough and translucent surface.
(iii). Crystalcast® mould
The idea of applying the coatings directly on Crystalcast® moulds emerged while demoulding a 3DPSM which had a protective layer of Crystalcast® on. The Crystalcast® protective layer, even after firing, maintained its integrity by forming a thin-shell, distinct mould (Fig. 9).
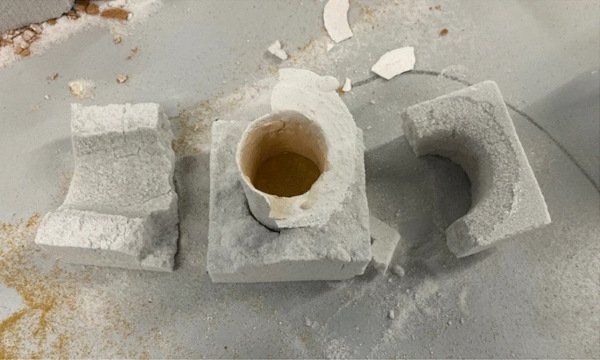
All three coatings are applied two times via brush on cube-shaped mouldsFootnote2 with 10 cm edge (Table 12). The results are promising, especially for Zirkofluid® 1219 (BS0Z2B2) and 6672 (BS0X2B2). Noteworthy is the fact that while the attained glass surface is clear and translucent, it is not totally smooth. The imprint of the brush strokes for applying the coatings is visible. This suggests that the flow or immersion coating application method might be more suitable towards attaining the best surface quality (Table 12).
Table 12 Results of samples tested at 870 °C normal firing schedule using silica plaster moulds (Crystalcast®). Samples are cleaned only with a soft sponge and water. Naming system as described in the methodology - Full size table
Interim conclusions test series B (Table 13).
Table 13 Results of best set-ups tested at 870 °C normal firing schedule. Samples are cleaned only with a soft sponge and water. Naming system as described in the methodology - Full size table
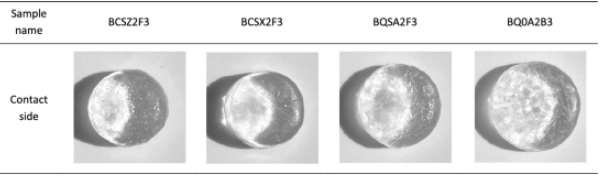
As indicated by test series A the best annealing schedule that results in successful casting (no cracking or glass to mould adhesion) and the best finishing quality of glass is that of 870 °C normal. The best combinations at this temperature are:
a. quartz sand moulds coated with Arkopal B5® (BQ0A2B3) or Crystalcast® and Arkopal B5® (BQSA2F3)
b. ceramic (synthetic) sand moulds coated with crystal cast and Zirkofluid® (BCSZ2F3, BCSX2F3).
Especially, the combination of Crystalcast® and Zirkofluid® 6672 applied on ceramic sand moulds gives the best results in terms of surface quality (BCSX2F3). Nevertheless, the application process is complex. Crystalcast® is diluted on water and Zirkofluid® is based on isopropanol, meaning the protective layer must be completely dry before the coating is applied. Zirkofluid® 6672 further requires special respiratory protection. The result is a thick coating layerFootnote3 that can compromise the dimensional accuracy if it is not considered during the mould-making phase, resulting in increased production time and cost.
Personal communication with (ExOne) states that water-based coatings (e.g., Arkopal B5®) are detrimental to inorganic binder (water–glass type) used on all 3DPSM as part of this research. Nevertheless, the application of Arkopal B5® directly on quartz sand mould via brush (quick drying) offers the third-best surface quality (BQ0A2B3) for geometry 2 sized samples. The results are inferior when the same coating is applied via flow directly on quartz sand mould. This effect is more evident on ceramic sand moulds; where most probably the lesser amount of binder is more severely affected by the water-based coating, leading to inferior surface quality (Table 11, first row).
Regarding the application method of protective layer/ coatings, flow application of the coating is to be preferred over brush, since it allows for a smoother mould surface which translates into a smoother cast glass surface.
3.3 Series C
To further validate the results of the coatings and protective layer effectivity, moulds with complex geometry and larger scale are tested (geometries 3, 4 and 5). Geometries 3 (CCSX2F4a) and 4 (CCSX2F4b) are realised in 3DPSM while geometry 5 is made of Crystalcast®. For the 3DPSM the findings of series A and B are taken into consideration, hence ceramic sand is selected as the preferred type of sand for the printed moulds, i. for its ability to maintain the mould integrity after firing and ii. for offering the best surface quality. An overview of this series of experiments can be seen in Table 14.
Table 14 Overview of prototypes of test series C - Full size table
3.3.1 Ceramic sand moulds (geometry 3 and 4)
The samples are fired on a slightly modified 870 °C normal annealing schedule with an additional 2 h at max. temperature to allow for proper melting of the increased amount of glass compared to the previously cast geometries 1 and 2. Samples CCSX2F4a and CCSX2F4b are coated with Crystalcast® and Zirkofluid® 6672 following the suggestions of series B experiments. The dimensional discrepancyFootnote4 that the protective layer of Crystalcast® results in is taken into consideration before printing, allowing dimensional accuracy of the glass element. The fabrication steps from mould to glass for geometry 3 (CCSX2F4a) and geometry 4 (CCSX2F4b) can be seen in Figs. 10 and 11 respectively.
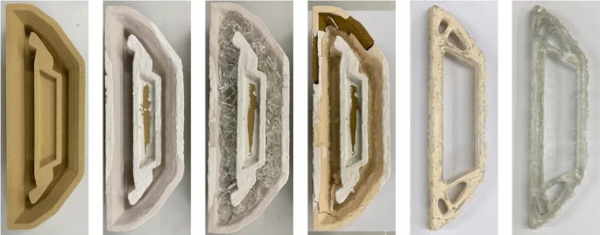
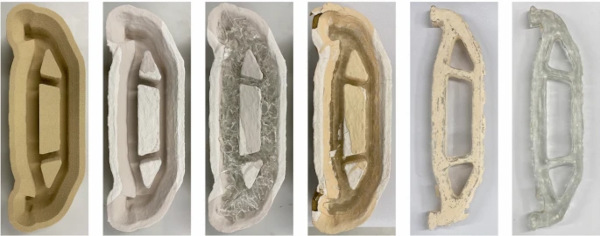
After firing, the mould maintains its integrity. The surface quality of the cast glass elements is similar to the one received from the same set-up on smaller samples (e.g. BCSX2F3) but the adhesion of the Crystalcast® protective layer and coating to the glass object is more severe. The glass object can be cleaned relatively easily, without using any water, using a soft metal brush attached to Dremel® (see, Figs. 10 and 11, steps 5 and 6). The final resulting beams of geometry 3 and 4 can be seen in Fig. 12.
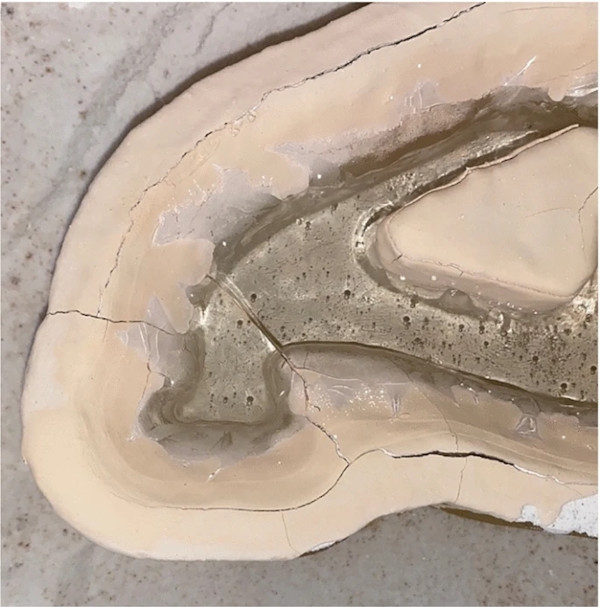
Geometry 4 (CCSX2F4b) faced a serious issue while annealing. Two of the total four beams cast in this geometry broke almost at the same point, at the sharpest edge of the mould as seen in Fig. 13.
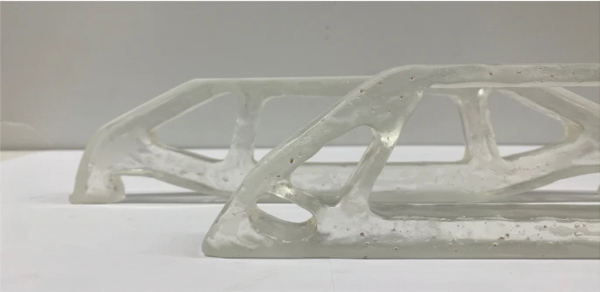
The cracking of this sample during annealing can be attributed to a variety of factors, such as the hardness of the mould, the different expansion coefficients between the different materials or the sharpness of the geometry at locations when casting on ceramic sand moulds.
3.3.2 Crystalcast® mould (geometry 5)
Further experimentation is done with geometry 5 (CS0X2F5) made of a Crystalcast® mould (lost-wax technique). The mould after steaming displayed cracking at its thinnest cross-sections and was locally repaired with some Crystalcast® mixture (using the typical mixing ratio: 1 part water and 2.8 parts Crystalcast®) before glass casting. After drying the mould was coated with Zirkofluid® 6672. Finally, the set-up was placed in the oven and two terracotta flowerpots were placed on top containing the required amount of glass. The set-up was fired following the 870 °C normal with an additional 4 h at max. temperature to allow for proper casting of the even larger volume prototype. Complete mould-making and preparation for casting can be seen in Fig. 14.
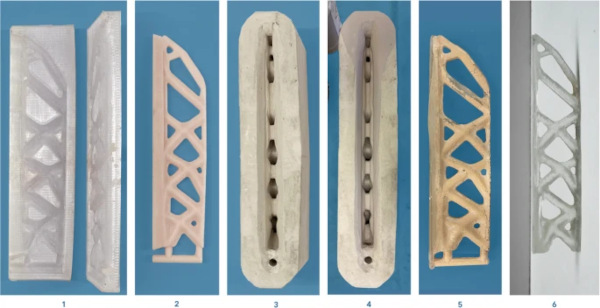
After firing, the release of glass from the mould was somewhat challenging. Immersion of the mould in water was necessary. After soaking and careful removal of mould material using small metal tools glass is obtained. The resulting cast glass component displays coating adhesion that is in a similar manner to geometry 3 and 4. The before and after the cleaning process can be seen in Fig. 14 (step 5) and Fig. 15. Most of the coating residue is removed in this way, leaving the glass surface relatively smooth and translucent. Noteworthy is the fact that the glass covered most of the volume without any significant defects, except for the thinnest part (10 mm) (Fig. 15, bottom right part) where glass fails to cover 100% of the narrowest part.
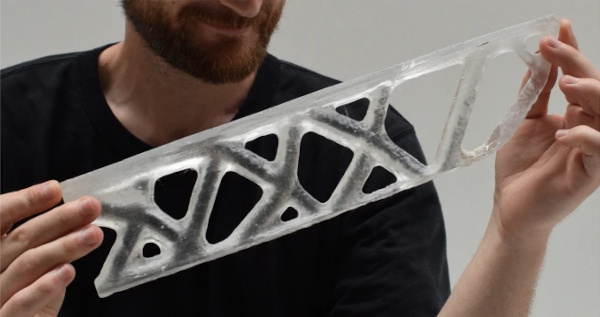
3.3.3 Interim conclusions test series C
Experimentation on more complex and slightly larger scale geometry supports the assumption of heat-time relation to the effectiveness of the coating. Larger samples require longer exposure at the max. temperature to allow for proper melting of the glass. The additional hours at max. temperature greatly affects the optical quality and results in the adhesion of the coating to the glass. In the comparative Table 15 where microscope images of × 30 magnification are presented, the impact of long exposure to max. temperature on the surface quality becomes more evident. For example, sample BCSX2F3 displays no coating adhesion zones compared to larger-size samples CCSX2F4a (ceramic sand) and CS0X2F5 (silica plaster).
Table 15 Glass surface under the microscope (× 30 zoom). Left cast glass on steel mould (benchmark surface quality) - Full size table
The results are improved with the current set-up (CCSX2F4a) (Fig. 16b and Table 15) when compared to previous kiln-cast glass experiments by the research group at TU Delft (Fig. 16a). Yet, the surface quality of the resulting glass objects remains far from the benchmark optical quality and transparency of glass cast on steel moulds (Fig. 16c and Table 15).
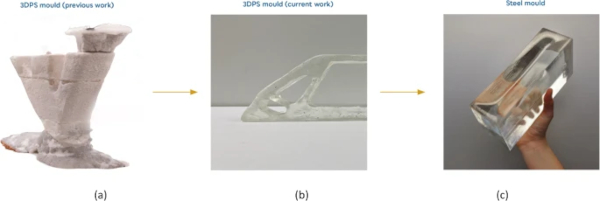
The improved surface quality translates into reduced post-processing, which in turn, can decrease both the time and cost of production. In that sense, the series of experiments are promising, with further testing needed to fine-tune the set-up. However, total elimination of the need for post-processing on larger elements kiln-cast on 3DPSM seems difficult with the current acquired data.
The casting of geometry 5 (CS0X2F5) indicated that it is not advisable to cast cross-sections thinner than 10 mm in diameter on a silica-plaster mould for this volume and size of the mould.
3.4 Series D
Although the focus of this research is towards kiln-casting, an additional foundry casting (hot-pouring) test is conducted using mould specimens of geometry 2, to provide insights into the factors that affect the surface quality, such as the max. temperature and the total exposure time on high temperature of the mould, and the combination of the above. After hot-pouring the specimens are placed directly in the annealing oven at 480 °C following the part of the annealing schedule of 870 °C normal from 26 h till 55 h (end) (Fig. 7).
For this experiment two types of glass are used: a. Bullseye® (DQ0A2F1, DQ0X2FA2F1, DCSX2F1) and b. a modified soda-lime glass recipe for casting (DQ0A2F2). The overview of samples and aim can be seen in Table 16. The glass is heated up to 1380 °C (dwell for approx. 1 h.) and then poured into the prepared 3DPSM as shown in Fig. 17.
Table 16 Overview of the hot-pouring experiment of test series D - Full size table
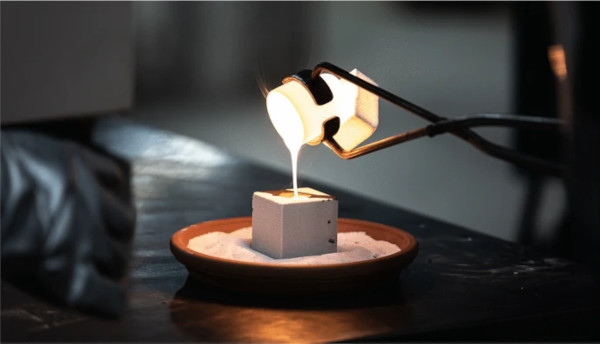
After demoulding, all specimens present a contact surface with no sand or coating adhesion. Samples DQ0A2F6a (Bullseye®) and DQ0A2F6b (modified soda lime glass) coated with Arkopal B5® (flow) display significantly improved surface quality than the kiln cast sample at 870 °C normal BQ0A2F3 (Table 17). The type of glass seems to play a role in surface quality as sample DQ0A2F6bFootnote5 seems to be smoother than DQ0A2F6a. The dual protective layer/ coating system applied on DQ0X2FA2F6 seems to yield a transparent but rough surface. Lastly, the application of the best protective layer and coating combination, as concluded at test series B, delivers the smoothest surface between the samples cast with Bullseye® glass but has a less transparent crystalline zone in the middle of the contact surface (DCSX2F6).
Table 17 Contact surface of hot-pouring test series D samples - Full size table
3.4.1 Interim conclusions series D
During the hot-pouring experiment coatings and moulds were exposed to a max. temperature ≈1380 °C for a short period of time (minutes) and annealed for 30 h at T < 480 °C. The kiln cast samples at 870 °C normal are exposed to T > 480 °C for 13.5 h and anneal for the same time as the hot-pouring samples (Fig. 18). Compared to kiln-cast samples at 870 °C, the hot-pouring samples display a smoother surface giving a preliminary indication that the prolonged exposure to high heat greatly affects the performance and integrity of the moulds and coatings.
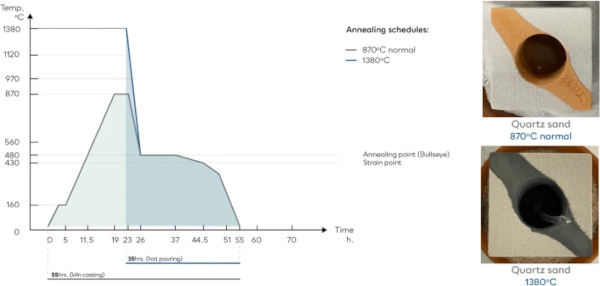
Discolouration of Arkopal B5® coating is evident after firing at 870 °C normal while after hot-pouring the coating remains unaltered (Fig. 18, right).
Overall, hot-pouring seems to be a better-suited method for casting glass on sand moulds. Hot pouring heating and cooling cycle is more similar to the cycle used in aluminum and iron castings already performed in such moulds, although the max temperature in this case is higher. Samples produced this way minimise the need for cleaning and manual post-processing to the glass surface and result in a good surface quality but not the best overall which is obtained via kiln casting at (BCSX2F2).
4 Conclusions
The described experimental work focuses on improving the glass surface quality in contact with the mould directly upon demoulding, aiming to arrive at an optically transparent and smooth surface via pre-processing the mould, sparing the need for time- and labour- intensive post-processing. In specific, the experimental research focuses on investigating the effect of (i) max. firing temperature and annealing schedule, (ii) mould materials and (iii) different coating combinations, to the resulting glass surface in contact with the mould/coatings.
Overall, the experiments conducted using 3DPSM and Crystalcast® moulds indicate that there is a significant relation between the resulting glass surface, and the max. temperature and the corresponding exposure time of the mould to the latter. In principle, the longer the exposure to high heat, the poorer the performance of the mould and coatings, and thus the resulting glass surface quality, is. Further experimentation is needed to assess the extent of the scalability factor on these results.
Series A and B indicate that moulds made of Crystalcast® and Ceramic sand seem to be the best options for the mould material for larger-scale geometries as they maintain their carrying capacity after firing.
Overall, the best surface quality is attained (after demoulding and cleaning) for kiln-cast glass samples, tested at the annealing schedule of the lowest max. temperature = 870 °C. Casting at higher max. temperature is not advised for the tested types of moulds.
For Ceramic sand moulds the most promising coatings combination, is that of Crystalcast® and Zirkofluid® 6672. Depending on the size of the sample and the total dwell time the results vary from a smooth surface with some minor inclusions and a translucent look for small cylindrical samples BCSX2F3 (Table 15), to a smooth surface with inclusions and minor coating adhesion to the glass and a translucent look for samples up to 30 cm (CCSX2F4a) (Fig. 19b).
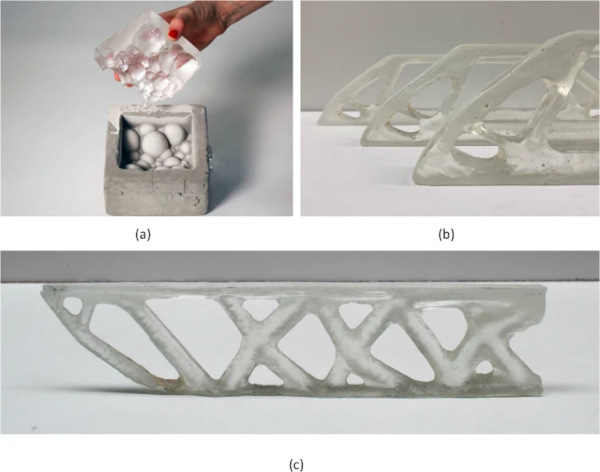
For Crystalcast® moulds the best tested coatings combination is that of Zirkofluid® 6672, which yields similar results with the latter (CCSX2F4a) in terms of transparency and surface smoothness, for samples up to 40 cm (CS0X2F5) (Fig. 19c). The results suggest that post-processing cannot be entirely avoided but it can be significantly reduced, as the surface quality in contact with the mould requires much less polishing, compared to non-coated kiln-cast specimens using the same type of moulds, to achieve a fully glossy surface.
Finally, series D experiments further suggest that hot-pouring (foundry casting) exhibits high potential in combination with coated 3DPSM compared to kiln-casting, due to the significantly reduced exposure time on high temperatures and reduced max. temperature that the moulds reach using this casting method. This assumption is supported by prior experiments using quartz sand moulds and Zirkofluid® coatings (Giesecke and Dillenburger 2022) where a smooth and relatively transparent glass surface is noticed (Fig. 19a).
5 Discussion and future research/ Next steps
Shifting from post-processing to pre-processing in glass casting has significant time and cost benefits, as already illustrated at relevant approaches in the making of the giant telescope cast glass mirrors. In specific, for the production of the Giant Magellan Telescope blank, a method of spin casting was devised to significantly reduce the post-casting polishing time (Zirker 2005). While trying to provide exact numbers is difficult, it is common knowledge that polishing (post-processing) of glass requires disproportionally longer time than that of the mould preparation (pre-processing). Apart from the time gain, on complex geometries such as the ones presented in this work, it is impossible to reach at all the creases and folds, hence pre-processing can be considered as the only viable option.
Overall glass casting on disposable mould displays potential for new architectural and artistic expressions on glass. This research focused on concluding to the best possible set-up to achieve a high surface quality (of the glass surface in contact to the mould) for kiln-cast glass components, shifting from post-processing to pre-processing. The best set-up as concluded at test series B and C opens possibilities for casting complex and customised glass components, shedding at the same time light on some of the practical implications of its application on larger scale samples. Limitations are primarily linked with the i. mould material, ii. the application method of the protective layer, iii. the effectivity of the coatings and the application process and iv. The time-heat effect on the set-up.
Regarding the mould material, ceramic sand moulds with inorganic binder allow for successful casting of glass at max. temperature 870 °C but harden after firing, making the release of the cast component challenging. Geometries 3 and 4, which are practically extruded 2D geometries can easily be removed from the open top surface. The release process will not be as easy for larger and more complex geometries featuring closed and narrow parts (e.g. geometry 5). Furthermore, more extensive testing is required to define the parameters that can lead to the breaking of glass samples of geometry 4 at specific areas. Testing using moulds with different bending strengths or less sharp edges is necessary to conclude whether the set-up is suitable for even larger glass prototypes.
Concerning the protective layer application, on small samples the application via brush is straightforward and all areas can be easily accessed. When the geometry is scaled up the brush application of Crystalcast® becomes more challenging especially when accessing narrow parts of the geometry, even if the 3D printed sand mould is made of multiple layers assembled together (segmented). This suggests that a different application method than brushing should be explored for the protective layer of Crystalcast®. Since Crystalcast® dries quickly after being mixed with water, the authors suggest exploring a spraying system that mixes the two components at the outlet as an effective solution. As of the coating application, spraying application should also be tested under kiln casting.
In terms of surface quality Crystalcast® mould used for prototyping (geometry 5) yielded similar results when compared to 3DPSM while eliminating the need for the use of a protective layer (Table 15). Currently, the limitation of Crystalcast® moulds lies in the production through the laborious lost-wax technique (Fig. 20). The mould production process is simplified with the introduction of 3DPSM, but the fact that the mould materials and binder systems are not tailored for glass casting opens the discussion for 3D printing of different materials. A promising new direction could be the direct 3D printing of moulds from Crystalcast®. Such hypothetical moulds could in theory greatly reduce the mould-making time and enable the casting of large-scale glass objects in a cost- and time- efficient way with a significantly reduced need for post-processing when combined with refractory coatings.
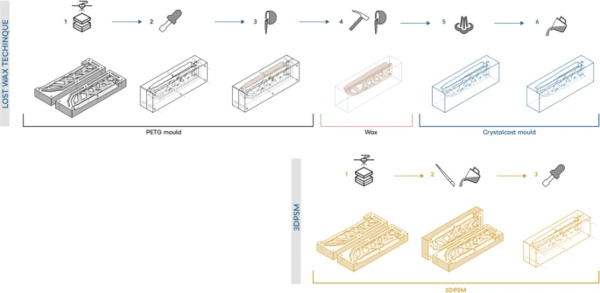
As for, the time-heat influence on coating effectiveness, this is expected to be even more profound for larger glass objects due to the prolonged annealing required. For larger samples more layers of coatings might be necessary or alternative coatings and coatings combinations. Thus, it remains unclear if the findings of this research are directly applicable to considerably larger in scale castings. Switching towards hot-pouring might be the best option for larger scale samples.
Notes
- Undercuts are possible since the mould material can be easily removed.
- This type of geometry is used since it was easier to be produced via investment casting at the lab.
- The difference in diameter of the cylindrical samples with and without the use of Crystalcast® as measured on one sample at the lab is 5mm. This translates to an approx. 2.5 mm difference in radius of offset when designing an object. This accuracy is proportional to the size of the object but can be crucial for smaller components or details.
- Approx. 2.5 mm offset outwards.
- For the modified soda-lime glass used for casting of the sample DQ0A2F6b a different process of foundry glass has been used resulting in a reduced volume and weight compared to the rest of the samples of test series D. Direct comparison is thus less consistent.