First presented at GPD 2019
Engineers and designers are using glass in increasingly demanding applications such as stairs, floors, bridges, large minimally supported facades and overhead glazing. The use of laminated glass in structural applications has become more recognized and preferred as a safer choice to monolithic tempered or heat strengthen glass. Structural interlayers are stiff interlayers that increase the safety of the laminated glass by increasing the strength.
There are two options when choosing a structural interlayer, Stiff PVB or ionoplast interlayer. Both interlayers provide improved post breakage strength and structural benefits; however, some significant differences in properties that affect the final laminate performance exist. Applications that require high temperatures above 30°C or long load duration’s, ionoplast interlayers perform the best.
Ionoplast interlayers require some special processing to ensure optimum quality of the final laminate such as lamination to tin side of glass and fast cooling rate in the autoclave to prevent haze formation. In the case of multi-ply laminations, a primer is needed for proper adhesion to the air side of the glass. Recent developments in Ionoplast have greatly improved the lamination processability with improved adhesion to the air side of glass and haze less dependent on autoclave cooling rate.
Introduction
The use of laminated glass greatly increases the safety of monolithic glass because of its glass retention properties. When laminated glass breaks, the glass will remain in place providing protection from glass shards. While the glass retention provides some level of protection once the glass is broken, the post breakage strength can be compromised reducing its ability to withstand loads. Laminated annealed glass provides some residual post breakage strength due to the breakage pattern; however, laminated tempered glass is very poor. Laminated tempered glass when broken breaks in very small pieces and will quickly lose its ability to bear any load.
Structural interlayers are stiff interlayers that provide a coupling effect with the glass, which increases the effective thickness of the laminate. This creates stronger laminates allowing the use of thinner glass or higher or longer load durations. Laminated glass with structural interlayer has much higher strength and can be used in more demanding glass applications such as minimally supported, floors, stairs, railings and very large glass panels. Structural interlayers have much improved post breakage performance when compared to standard interlayers. This greatly improves human safety.
Types of structural interlayers
Today there are two types of structural interlayers, Stiff PVB and Ionoplast interlayer. Stiff PVBs are based on PVB chemistry with lower levels of plasticizer, which increases the modulus. Ionoplast interlayers contain no plasticizer and are based on unique ionoplast chemistry.
Stiff PVB provides structural performance at moderate temperatures while Ionoplast interlayers provide structural performance over a broader range of temperatures because of the unique chemistry.
Ionoplast processing
Ionoplast interlayers have a very different chemistry than that of PVB. Ionoplast is a semi crystalline polymer while PVB is more amorphous. This unique chemistry gives the high strength, tear resistance and enhanced structural properties. This also results in Ionoplast requiring slightly modified processing when compared to PVB. Special lamination settings are required to achieve the optimum adhesion and optics.
The lamination must be done using the tin side of glass or when not possible using a primer to achieve good adhesion. To eliminate haze, which is caused by the polymers crystallinity, the cooling rate in the autoclave must be fast enough to prevent haze formation. If the laminate does show unacceptable levels of haze, it can easily be fixed by re-autoclaving the laminate.
When processed properly the final laminate has very high adhesion and superior optical quality.
Ionoplast for improved processing
The objective of the development of a next generation ionoplast was to design it to be able to process closer to PVB while maintaining the same structural properties as Ionoplast.
The development of the new Ionoplast was focused on improving the adhesion to the air side of glass which eliminates the need for primer. This will make lamination of multiply easier as well as removing the need to orient glass to laminate to the tin side in single ply laminates. The other focus was on improving the optics by reducing the haze formation with slower autoclave cooling rates. This will reduce the need to re-autoclave due to haze as well as the possibility to increase the autoclave loading density.
Adhesion
Improvements of the adhesion to the air side of the glass have been achieved for the next generation Ionoplast without compromising the adhesion to the tin side. The below chart shows the pummel adhesion of both the air side and tin side for Ionoplast and next generation Ionoplast. No primer was used during lamination of the air or tin side.
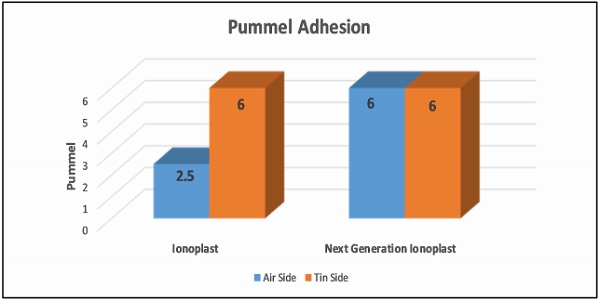
Freeze thaw cycling tests were conducted to understand the robustness of adhesion. Laminate samples were prepared both tin side and air side orientation with various interlayer moisture levels. The laminates were then pummeled and weighted. Laminates were immersed in water overnight and then placed fully wet into a freezer at -20°C. The laminates were weighed again. The cycle was repeated 4 times and total weight loss was recorded.
Next generation Ionoplast showed very little weight loss and a high pummel value with air side orientation indicting very high glass retention. The tin side orientation results were slightly lower with a increase in weight loss seen at a moisture of .6%.
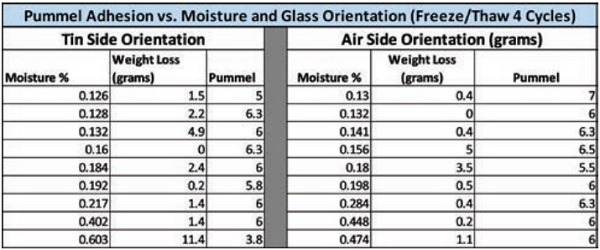
Ionoplast interlayer must be kept stored in sealed bags to protect from moisture. Moisture levels above .15% can affect the laminate adhesion. A study was conducted to understand the effects of storage conditions of the interlayer on the final laminate adhesion. The below figure 3 shows the effects of interlayer exposure to ambient air conditions and the effect of adhesion for the new Ionoplast interlayer. Pummel adhesion remains high even after 21 days of exposure and moisture level of .35%
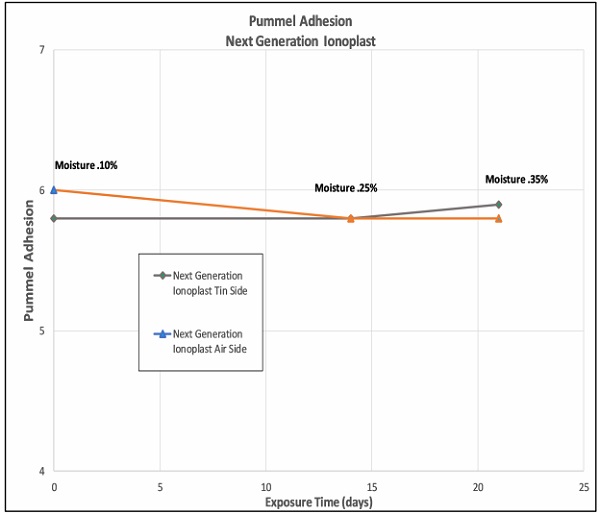
Haze
While PVB optics are not effected by autoclave cooling rate the optics of Ionoplast interlayers are influenced by cooling rate. Haze formation is dependent on the cooling rate and spacing of laminates in the autoclave. If cooling rate is not adequate laminates, particularly large or very thick, will show some haze. This is easily reversible by re- autoclaving the laminates. Next Generation Ionoplast shows much less haze sensitivity to autoclave cooling rate. Although not the same as PVB, it is much improved. Figure 4 shows the haze versus autoclave cooling rate for both Ionoplast and next generation Ionoplast.
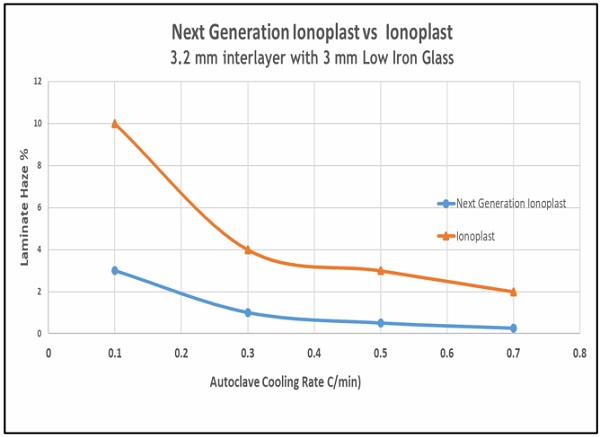
Structural performance
One of the objectives in the development was to improve the sensitivity of haze to autoclave cooling rate while maintaining structural properties. The haze formation is a result of the polymer morphology and changes to this to reduce haze have the potential to affect the structural properties.
Modulus data was developed over a range of temperatures and loads. This incorporated included bending studies, creep measurements and DMA. Preservation of structural performance was achieved with the exception of higher temperatures with longer load durations. The below table shows comparison versus stiff PVB, standard Ionoplast and next generation Ionoplast.
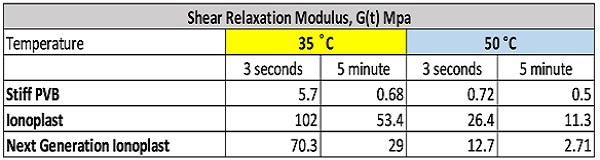
Physical and Impact properties
The basic physical properties of the next generation Ionoplast are similar to the current Ionoplast.
One concern with improving adhesion is the effect it will have on impact properties. Typically, when adhesion is increased the impact performance is compromised. Next Generation Ionoplast with 0.76 mm caliper was tested per EN12600 and EN356. Performance was the same as original Ionoplast passing P1A and 1B1 using 3 mm glass.
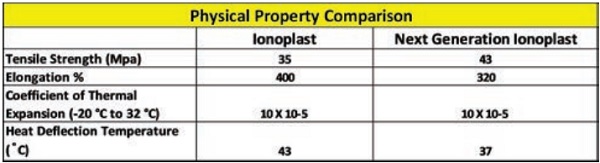
Conclusion
Next generation ionoplast improves adhesion to air side of glass, adhesion robustness and haze sensitivity to cooling rate. All of these improvements make the lamination process for Ionoplast closer to that of PVB while still preserving the structural and physical properties of Ionoplast. With the lower haze sensitivity, making very thick or large laminates becomes much less demanding with a lower risk of haze due to improper cooling.