This paper was first presented at GPD 2019 by Thomas Rainer from iHEGLA boraident GmbH & Co. KG.
In the last years the demand on new functions in building glass products growths dramatically to realize smart window applications. The realization of these new functions leads to the development of new glass processing technologies using laser radiation. By means of laser radiation it is possible to change a broad range of properties of the glass product. Those laser structures are able to be seen by the naked eye as well as to be invisible. For this laser induced processes examples of laser applications will be presented as well as the process tool laserbird.
The laserbird is a universal tool, making it the perfect choice for a broad portfolio of customers, applications and glass products. Extra applications can be added at any time to expand the production range and create new glass building products. Laser finishing can be used to produce custom, functional and decorative glass products. The trend towards new applications in this segment has not been driven exclusively by technological progress. In fact, the development has far more to do with changes in customer demand and the more general feasibility of options for generating greater added value.
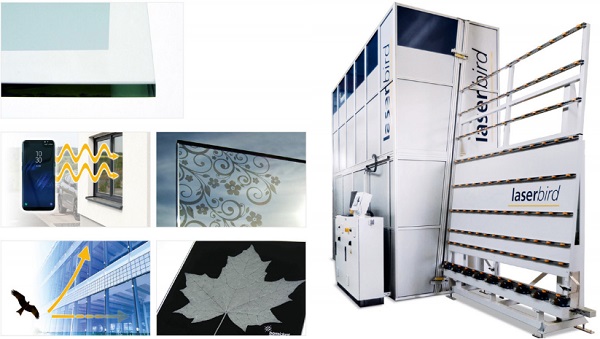
Laser processing of custom glass products
Until recently, laser-assisted finishing in the glass processing industry was seen primarily as an aesthetic tool for fulfilling custom glass designs. The laser printing process is used to apply a wafer-thin, scratch-resistant pattern to the glass that matches the specified template. When working with coated glass, the physical properties of the coating can also be used to turn it into a sample or another motif through careful application of the laser.
What makes these two processes special is that they don’t require any tooling or set-up time – and that applies to the production of both one-off pieces and larger-volume series. Among the company’s many proprietary development is the laserbird, a system that can be used for finishing on single-glazed panes, laminated glass and insulated glass units (IGUs).
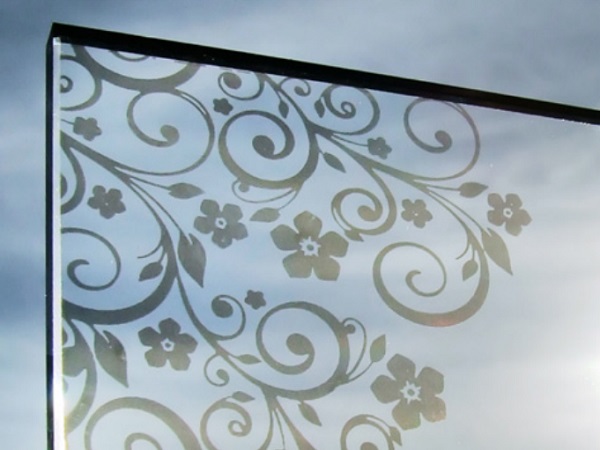
Laser decoating for a crystal-clear surface with no scratches
The increasingly strict demands with regard to the quality of structural glazing and edge decoating in general are making the laser a more popular tool for these types of applications, too. Decoating using laser technology is gentle, highly precise and causes zero damage to the surface. Customers uses laser decoating for controls on their machines or to create lighting effects behind mirrors.
High-functionality smart glass
In addition to finishes of high aesthetic quality, the added functionality of smart glass is another area with potential for the future. Glass products that can now be produced using laser techniques include glass with increased permeability to mobile communication radio waves – perfect for use in areas such as conference rooms and offices. The technology can also be used to finish bird protection glass, apply site-specific sun protection or increase radar dampening in areas close to airports. There is also the option of using laser prints or coating conversion to turn glass panes into conductors, which can then be used for technical applications.
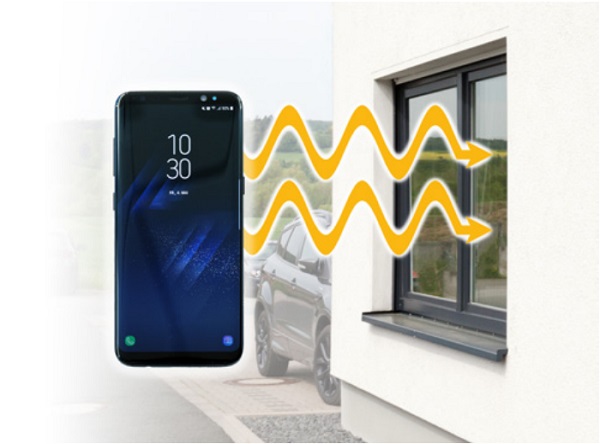
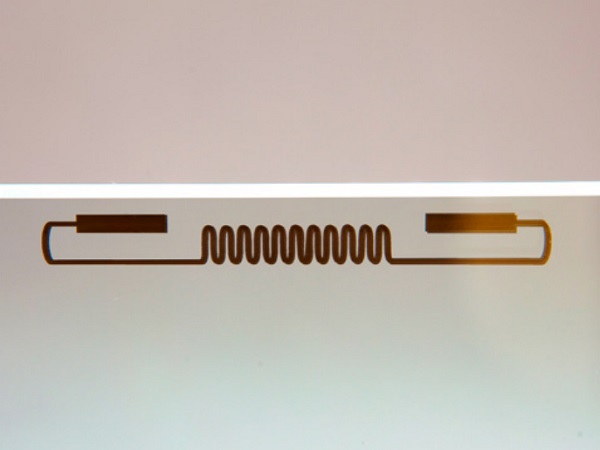
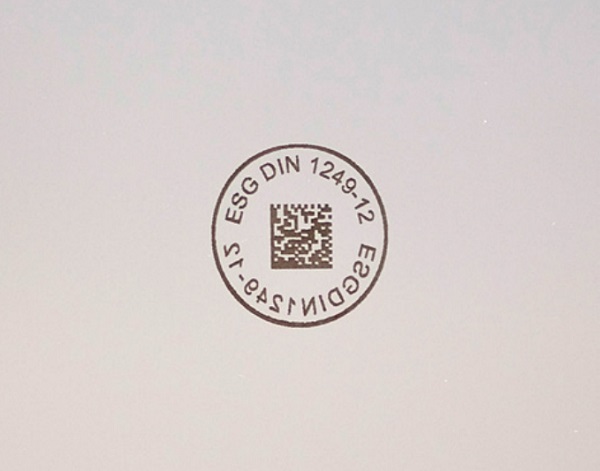
Clear markings for traceable glass and product identification
The laser-assisted design and functionalisation of glass panes is used primarily for finished products that are designed to provide added value. However, as the Internet of Things grows and production processes become increasingly automated and digitalised, laser technology is becoming more important for use in identification processes.
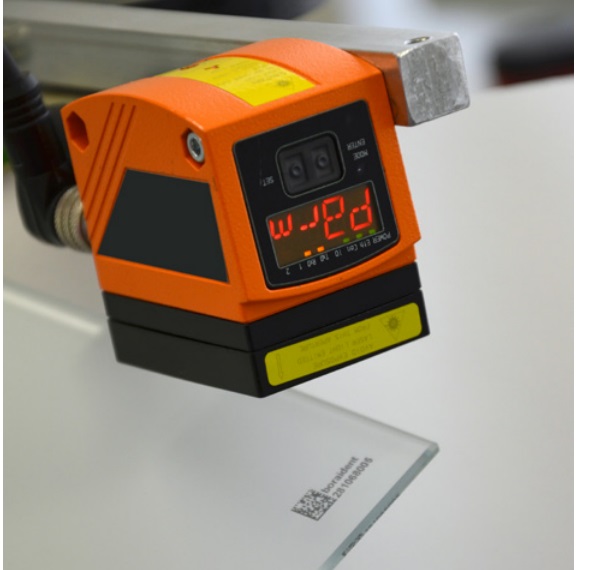
In order to facilitate production management and product traceability, the panes are marked with a unique, machine-readable QR or data matrix code (and often a logo) before being cut to size. Marking the glass using the UniColor laser printing process, for example, leaves the surface undamaged and permanently bonds the marking to the pane without scratching it.
This individual marking allows the entire production process to be monitored in real time and optimised using special software. Depending on backup procedures and the data available, it is possible to track down the production company that made the IGU and the company that installed it for the end customer years later, as well as the stations and machines used in the production process. Data collection and storage also provides everyone involved with a wealth of experience to draw on.
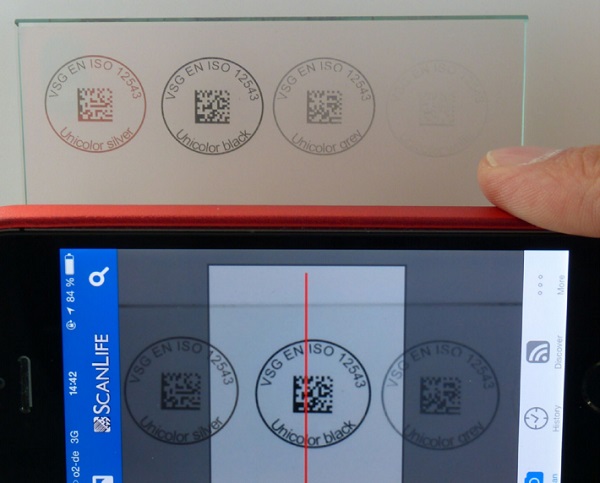
Contact:
HEGLA boraident GmbH & Co. KG
06118 Halle, Koethener Strasse 33a, Germany
Dr.Thomas Rainer
Tel.: +49 (0) 345 / 47 82 35 0
E-mail: rainer@boraident.de