Gavin Way, Nexus Point, Off Holford Drive,
Birmingham B6 7AF
United Kingdom
Thermoseal Group Ltd.
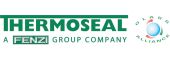
Find us on:
Thermoseal Group is dedicated to insulated glass. We have our own technical centre where we develop new insulated glass components with a focus on energy efficiency. We manufacture warm edge spacers in the UK, as well as many other insulated glass components.
We supply over 2,500 insulated glass components, including: sustainable warm edge spacers, aluminium spacer bars and steel spacer bars and accessories; integrated blinds; Victorian grille; Georgian style window components; molecular sieve desiccant; sealants; lead; decorative glass bevels and accessories; adhesive tapes; tools for glazing manufacturing, and most other items required for sealed unit manufacture.
In recognition of our excellent products, quality and service, as well as our dedication to staff and customers, we we've been awarded multiple awards including some from one of the glass and glazing industry’s coveted G-Awards and the Queen's Award for Enterprise: International Trade 2017.
We export world-wide, so whether you're a sealed unit manufacturer, a window fabricator or a double glazing installer in any location, we are the one-stop-shop for insulated glass components and machinery for all levels of glass sealed unit manufacture.
Thermoseal Group was founded in 1979 and quickly developed into an industry leader. Our original business was the sale of a limited amount of machinery from our small factory in Birmingham. Thermoseal Group now operates from four rapidly expanding branches in Birmingham, Wigan, Kent and Northern Ireland. We now stock and manufacture a wide range of insulated glass sealed unit components and machinery for sealed unit manufacturing.
Aside from our Kent-based lead plant where we produce our exclusive range of decorative DecraLed, most of our manufacturing processes have always taken place from our Birmingham factory.
However, as the business has expanded, we now have a large manufacturing base in Wigan dedicated to the production of our own energy efficient products including – Thermobar warm edge spacer tube made with engineering plastic and Thermoflex warm edge spacers made from a flexible foam material.
Alongside production on this site, we also have our own Technical Centre focussed on designing, developing and testing our range of products to meet the changing regulations. Research, development and manufacturing of future-proof products is now the focus of the Group.
In addition to this manufacturing base, we also have an expanding injection moulding division based in Birmingham where we are developing our own range of components compatible with key industry products including Thermobar and Thermoflex.
We are also active members of the Glass and Glazing Federation (GGF) and Bundesverband Flachglas (BF) and the IGMA working for the IG industry. Our warm edge spacers are also certified by the Passive House Institute (PHI). Thermobar is certified with a phA rating (phA+ with Hot Melt).
With innovation and a willingness to develop our industry as a priority, we offer a guaranteed quality of product and a reliable and timely delivery of goods, which in the UK are by our dedicated team of drivers.
We know that our customers have their own customers' needs to meet, so we make it our business to ensure that we provide a tailored supplier support system.
Products
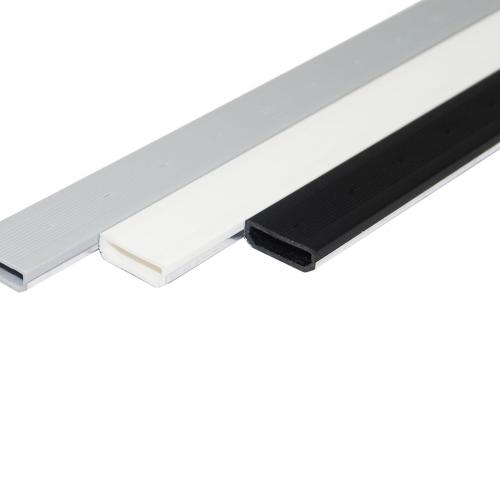
As it is a Passive House approved component, Thermobar achieves a phA and phA+ (with Hot Melt) rating for Arctic Climate Zones and all other climate regions with lower requirements. It also has the highest rating in Passive House Hygiene requirements and best thermal values as certified by Bundesverband Flachglas Association Data Sheets.
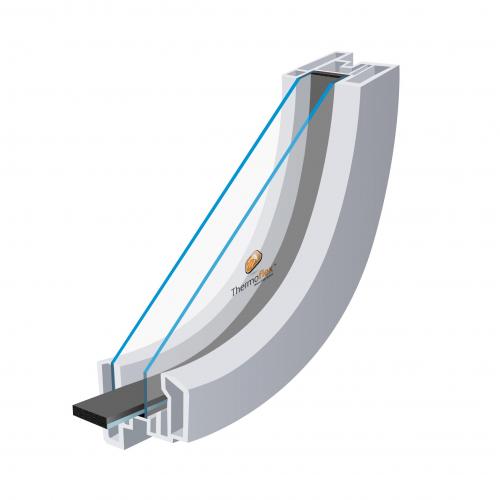
By creating our own warm edge spacer systems, we have complete control of the content and quality of the product from the initial mixture to the mixture to product processing, packaging and final distribution. Ensuring you always get the very best quality and service from us.
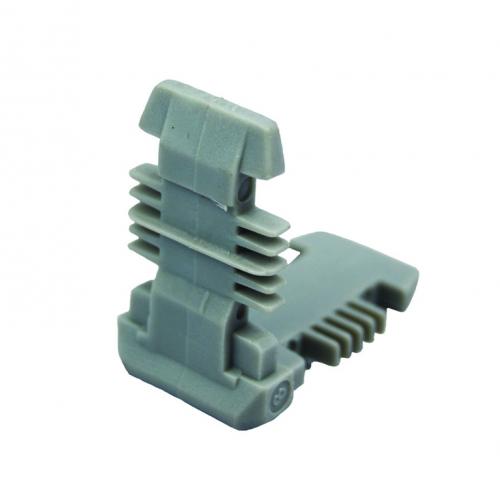
Suppling the largest volume and range of spacer bar accessories to the international market means you’ll find over 2,500 components detailed on our website, but if you can’t find what you’re looking for, please give us a call.
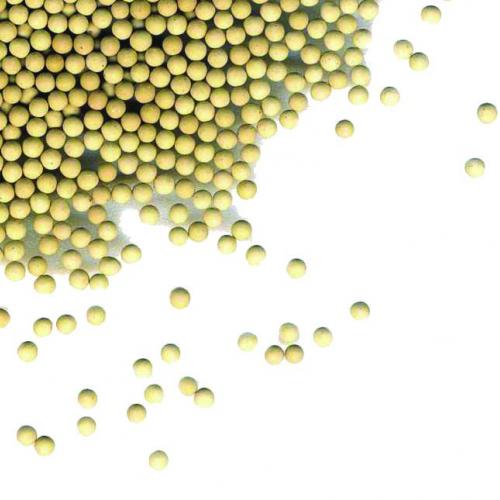
All desiccant is continually batch-tested and benchmarked against other market-leading molecular sieve desiccants. Every single shipment is comprehensively tested and delivered with a Certificate of Analysis, not only this but all deliveries we receive are examined on arrival. Any shipments found not to meet our exacting standards are immediately returned for replacement. This ensures only the highest quality reaches our customers.
Our desiccant’s thorough testing include checks for Gas Desorption (a premium desiccant will only adsorb moisture vapour and not inert gases in the sealed unit); Delta-T Results (generally, but not conclusively, an active desiccant will generate heat upon contact with moisture); Initial Moisture Content (should be less than 2.5%); Moisture Adsorption Capacity (tested to proposed revisions to EN1279 standards); Dust Content (to check consistent bead size); Bulk Density (to check volume).
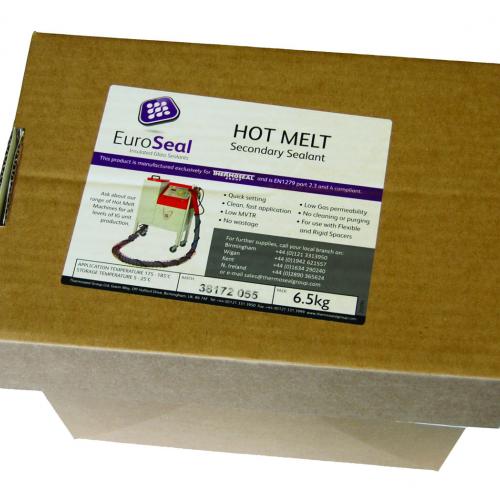
Our range of Polyisobutylene (PIB) sealants are used as a primary seal, they serve several purposes including: as a handling aid, as a barrier to prevent moisture gaining access and to help minimise the loss of energy saving inert gases from the unit.
Secondary sealants bond to the spacer bar and seal the edge of the IG unit from moisture ingress and protect the unit from gases passing out of and into the internal construction they include Hot Melt, Polysulfide, Silicone and Polyurethane.
All sealants are independently tested to EN1279 part 2 and 3 standards. Our sealants are all continually tested and benchmarked to EN1279 standards in our own in-house test facilities to ensure good adhesion to glass and spacer; optimum tensile properties; low density, as well as very low moisture vapour and gas transfer rates.
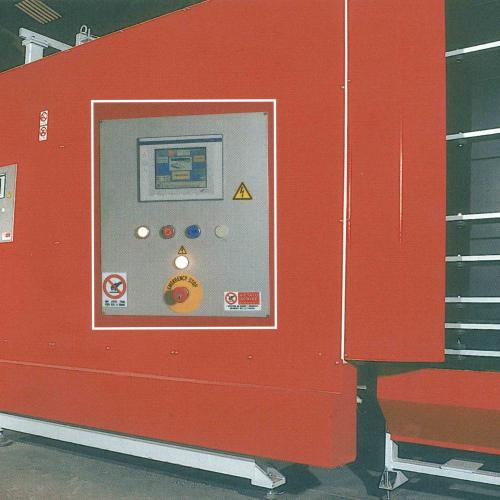
TGE (Thermoseal Glass Equipment), part of the Thermoseal Group, manufacture a superior range of glass machinery built specifically for the production of insulated glass units.
Our machines cater for all levels of sealed unit production and are built with a range of features to ease the job of the operator and help smoothen the production process.
We take our responsibility towards the environment seriously, so building energy efficient machines is a big priority. Of course, helping our customers to save money is also a bonus!
All new machines come with a 12-month parts and labour contract within the UK mainland.
We also supply a range of used machinery, so if you're looking for a second-hand machine for any level of sealed unit production, you'll find some details on our site. All used machines are refurbished and come with support from our TGE service team.
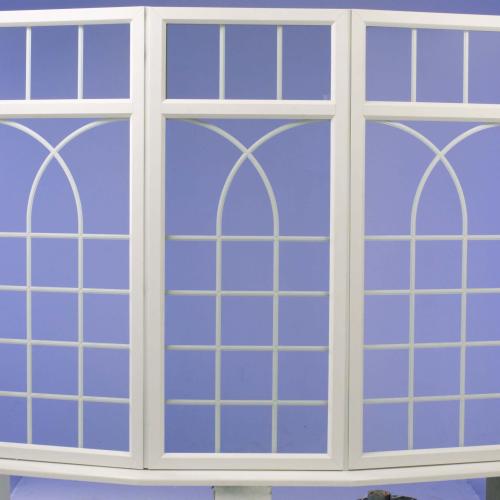
You can purchase components to create your own Georgian Design or Victorian Grille Pattern, we supply one of the UK’s largest ranges of high-quality bar and fittings suitable for any design. We also supply Surface Mount Bar to fit over internal muntin bar or duplex systems (we manufacture and supply energy efficient Interbar and Duplex Fittings).
If you don’t want to manufacture your own patterns, our Georgian fabrication department is dedicated to offering one of the largest ranges of Georgian bar and grille patterns available. They come in a multitude of sizes and differing colours - we can match any colour through powder coating or foiling bar and fittings. We make internal grid systems that can be tailor-made to your own design and to fit a specific shape and size of the window. A range of stock patterns is also available to order. The only limit is your imagination!
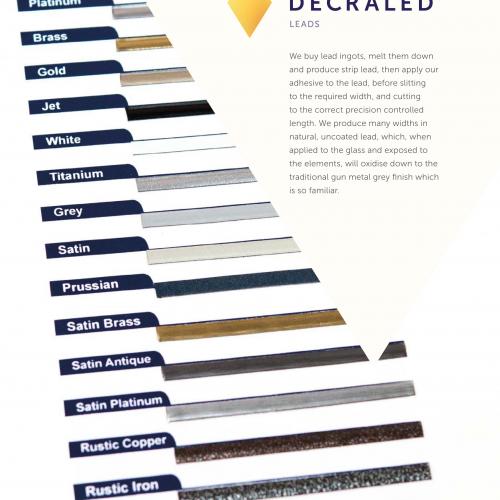
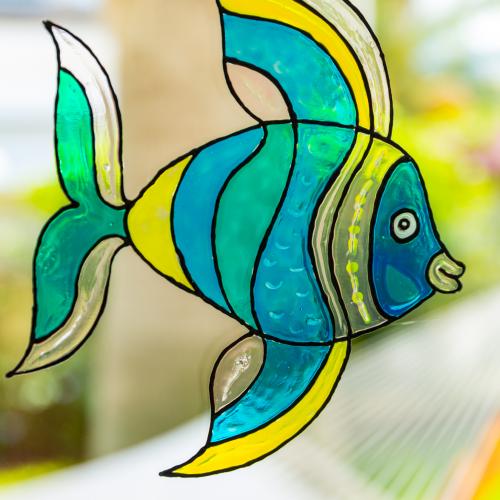
We have invested in a modern state-of-the-art design studio in Wigan to produce bespoke designs for our customers so they can use them in their own insulated glass units. Our Films are also extremely popular in the crafts market as they can be used on any glass surface to give a stained-glass look.