Article Information
- Digital Object Identifier (DOI): 10.47982/cgc.9. 514
- Published by Challenging Glass, on behalf of the author(s), at Stichting OpenAccess.
- Published as part of the peer-reviewed Challenging Glass Conference Proceedings, Volume 9, June 2024, 10.47982/cgc.9
- Editors: Christian Louter, Freek Bos & Jan Belis
- This work is licensed under a Creative Commons Attribution 4.0 International (CC BY 4.0) license.
- Copyright © 2024 with the author(s)
Authors:
- Matthew Tee - Eckersley O'Callaghan
- Carmelo Guido Galante - Eckersley O'Callaghan
- Romaric Massard - eLstar Dynamics
Abstract
Mechanical heating and cooling are often required to balance the energy flows in and out of space to maintain comfortable temperatures. There is significant pressure in many countries to reduce the energy consumption of buildings and one way to achieve this is to reduce the area of glazing. However, this conflicts with providing natural daylight which is critical to the visual comfort, health, and well-being of occupants. The typical approach currently used to improve glass performance is to use coatings applied to the build-up; the major limitation with glass coatings affecting most buildings globally relates to the solar and light transmission properties being fixed. This implies that a static glazing solution is often not working optimally for most of the year. Dynamic glass solutions can be pre-programmed, operated according to sensors that respond to the environment, or switched manually by occupants of the building to balance energy and visual comfort demands. This paper aims to present the findings of a study on a specific dynamic glass technology, Electrophoretic Light Modulator (ELM) produced by eLstar Dynamics, showing how this compares from an energy and daylight perspective against a ‘static’ typical glass with high-performance coating in the climate of Amsterdam, the Netherlands. Using the software package IDA ICE, simulations were performed showing the benefits of adopting the eLstar technology in reducing energy demand while also improving internal daylight conditions.
1.Introduction
Dynamic glass technologies enable the solar and light transmission properties of glazing to be varied to meet the changing demands of the building and user according to the climate conditions throughout the year. Such technologies may improve occupant comfort through better internal daylighting conditions and control of glare, while also offering potential reductions in operational energy consumption of buildings when compared to glass coatings with static performance.
This paper presents the findings of a study of the potential benefits of one particular technology, Electrophoretic Light Modulator (ELM), on the energy and daylight performance for an office building in Amsterdam by means of dynamic simulation of a ‘shoebox’ perimeter zone model.
2. Electrophoretic Light Modulator (ELM) Technology
Electrophoretic Light modulator is a dynamic glass technology based on electrophoretic principle which relies on the electrically driven motion of charged particles within a fluid. The ELM concept is based on two parallel transparent substrates that can be either glass, plastic or any other transparent material. For the convenience of production, it is currently mainly developed on glass. On each glass substrate, metal electrodes are micropatterned on their surface. The substrates are aligned with each other to ensure alignment of their electrode patterns. Substrates are kept apart by the introduction of spacer materials, usually ball spacers as used in liquid crystal displays or so called photospacers, spacers generated by microphotolithography. Finally, an electrophoretic ink is introduced between the substrates and limited by a seal on the perimeter of the window.
The electrophoretic ink is usually designed to absorb a specific range of the light spectrum from UV to visible to near infrared (IR). Here the current focus is on a black ink that absorbs both visible and near IR wavelengths. Without power, the pigments used in the electrophoretic ink are evenly and fully dispersed within the whole volume between the substrates. The window appears black and absorbs both the visible and nearIR wavelengths. By applying an electric field between the electrodes, the charged pigments accumulate in the volume between the electrodes. The colouring material of the ink is then hidden from the view by the opaque electrode material. The window becomes transparent and colour neutral as no coloured material is now present in the field of view. By applying specific electrical fields between electrodes on opposite substrates and from the same substrate, the pigments are redistributed in the entire volume and the window is restored to the default black position.

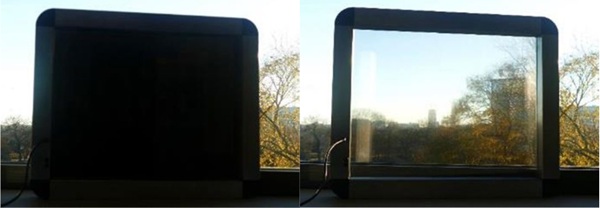
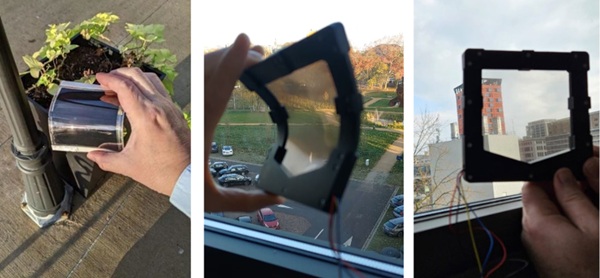
Dynamic glass technology requires a wide spectral transmission range to optimise the energy transferred to the building but also to remain visually appealing compared to standard windows and reach an appropriate consumer acceptance level. Whilst visible light transmission is critical to comfort and wellbeing, it is equally important to modulate infrared (IR) light, which represents roughly half of the total solar energy if energy efficiency is to be achieved. Furthermore, being able to independently control the modulation of visible light and IR would enable glazing to optimise for both energy and daylight conditions separately at the same time. Existing glass solar control coating technology allows only a constant relationship between light and solar energy transmission, if one is reduced then the other is also reduced or vice versa.
Existing dynamic glass technologies use various technologies such as Liquid Crystal, Electrochromic, Electrochemistry, Suspended Particle motion or Electrophoresis. Specifically, Electrophoretic Light Modulators achieve a dynamic range of transmission and colour neutrality using pigment motion under the control of electric fields. This enables the development of dynamic glass of any colours or light band by exchanging the pigment type; independent control of visible and IR light is also possible in principle.
The use of dynamic glazing is currently limited, due to high cost and size limitations for example. However, wide scale adoption could enable more meaningful impacts on operational energy reductions of the built environment generally. However, massive adoption of dynamic glass raises significant challenges on availability, sustainability, and cost of the technology. Availability is dictated by the type of natural resources required to produce the technology. As recently flagged by the World Economy Forum¹ development of materials competing for resources may create tensions on specific raw materials with currently constrained supply, such as¹ lithium, cobalt, copper, nickel, and other rare earth materials. Dynamic glass technologies based on such raw materials may therefore have a limited ability to be broadly deployed. Contrary to some other technologies like electrochromic dynamic glass which use lithium, in the case of Electrophoretic Light Modulators all materials used are non-critical in terms of availability of resources. The technology consists of glass, standard metals like aluminium, copper or any other conductive metals for the electrodes. The spacers are usually polymer resins and in very limited quantity. Finally, all components of the electrophoretic ink are under European REACH regulation and exclude the usage of rare earth metals or any exotic elements.
Availability also means the ability to produce the technology in large quantities, form factor and with global distribution. As the ELM technology is based on very well developed, high quality and high-yield LCD production lines, the ELM production could quickly scale to the required volumes without requiring additional manufacturing capacities. Capable of being shaped in any form and compatible with flexible light substrates, the ELM fits the purpose.
3. Methodology
The objective of this study was to assess the potential heating and cooling energy benefits of the ELM dynamic glass product compared to a typical static glass configuration while maintaining suitable internal daylight levels. The study was intended to be representative of a commercial building using the climate in Amsterdam, the Netherlands. The baseline glass was chosen to use a high-performance glass coating to provide solar control, as is currently common practice. This technology provides constant performance throughout the year, not adapting to changing environmental conditions.
Geometry
The simulation was undertaken for a ‘shoebox’, consisting of a cuboid volume representing the perimeter floor zone of a typical commercial building. This approach was used rather than modelling a larger volume, such as a whole floor or building, to reduce the computational time when running many versions of the model while developing the control strategy or testing different orientations. The shoebox geometry was based on the BESTEST Case 600 Low Mass Building (ANSI/ASHRAE Standard 140-2001), which considers a rectangular single zone (8m wide x 6m long x 2.7m high) with no interior partitions and 12m² of windows on the external elevation.
This corresponds to a glazing ratio of 55%, considered to be representative of modern office buildings in Amsterdam. The simulation was run for four key facade orientations of North, East, South and West.
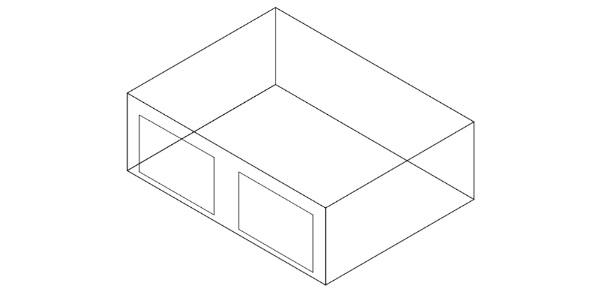
Fabric performance
The fabric performance assumptions defined in the BESTEST Case 600, published in 2004, are no longer considered relevant to modern construction, particularly in Europe. Therefore, alternative fabric performance was assumed, as defined in Table 1. The glazing performance assumes double glazing with a double silver high-performance solar control coating, while the wall U-value and air permeability are based on the typical performance of new construction.
Table 1: Fabric performance assumptions.
Loads, schedule and setpoints
The following assumptions were made in the energy model:
- Occupied hours were assumed to be 8am-6pm. No occupancy on weekends or holidays.
- Occupant density was 0.1/m2
- The ventilation rate was 12l/s/person. This is equivalent to 58l/s.
- The heating setpoint was 21⁰C
- The heating setback temperature when unoccupied was 12⁰C
- The cooling setpoint was 24⁰C
- The cooling setback temperature when unoccupied was 50⁰C
- Heating and cooling loads were scheduled to be on during occupied hours and off at other times.
- The energy loads are calculated as ideal air loads.
Glass configuration
LM technology can be integrated into a Double Glazing Unit. As ELM technology is currently produced using LCD manufacturing lines, the initial module consists of the assembly of 2 thin glass substrates (typically 0.5mm each). Such modules do not themselves demonstrate adequate mechanical robustness, or thermal or acoustic performance for architectural glazing. The ELM module is therefore laminated onto a thicker architectural glass using conventional processes based on PVB, EVA materials. The standard IGU construction for ELM dynamic glass production will be described below.
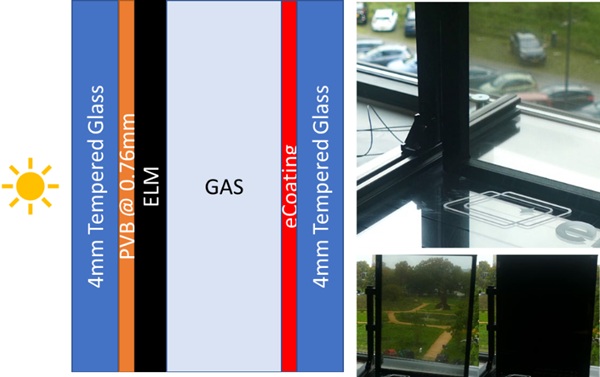
For this study, measured spectral transmission and reflection data was provided by eLstar dynamics for the ELM in isolation, but this was combined was other layers using LBNL Window & Optics into the DGU configuration shown in Figure 6(R).
The DGU consisted of laminated external glass with a monolithic toughened internal pane. The cavity was assumed to be 16mm wide and filled with 90% argon and 10% air. The solar control was assumed to be provided solely by the ELM, with no solar control coating being assumed. Instead, a low-emissivity coating was assumed on the internal side of the cavity to achieve a U-value of 1.0 W/m2K.
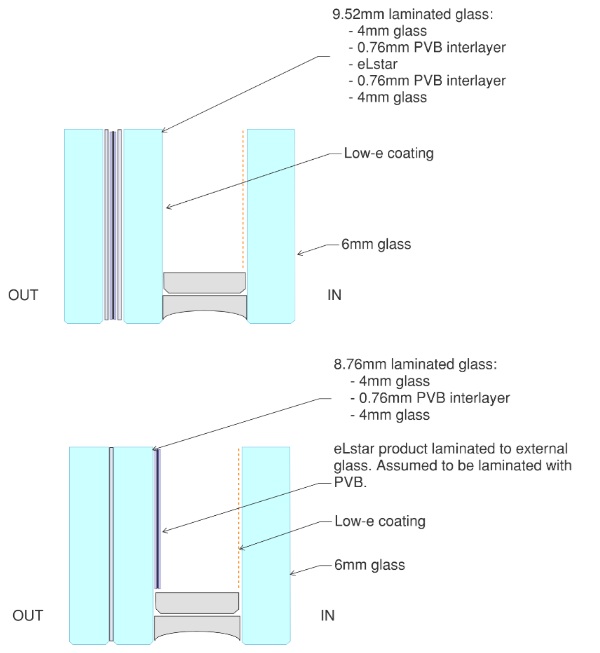
Two positions were considered for the ELM; either laminated in between the external glass panes (between face #2 and #3) or laminated to the inside of the external glass panel (behind face #4) within the cavity as shown in Figure 6. The g-value and light transmission properties of both options were found to be very similar and Option 2 was selected for this study. The performance of this configuration is shown in Table 2 for the darkest state and the lightest state. The analysis assumed also used 8 intermediate states which were linearly interpolated and evenly distributed between the light and dark state.
Table 2: ELM Glass Performance.
Software
A review of commercially available energy modelling software was undertaken and IDA ICE from EQUA was selected as the preferred software as it appeared to allow the most flexibility for controlling the state of the glass when modelling dynamic glazing products.
Dynamic Glazing Control Strategy
As the ELM glazing can vary the g-value and light transmittance properties to any intermediate state between the darkest and lightest state, a significant part of this study was developing and implementing a control strategy to determine which state was most suitable at each timestep of the simulation.
The objective of the control strategy was to reduce energy consumption while maintaining acceptable internal daylight levels. To achieve energy savings, a different strategy is required if there is heating or cooling demand. Therefore, one of the three states below was selected based on whether the zone temperature was within the setpoint range (no heating or cooling), above it (cooling demand) or below it (heating demand):
Cooling Demand: To reduce cooling energy demand by reducing solar heat gains, the glazing is placed in the darkest possible state while maintaining a minimum internal daylight level for occupant comfort and to limit energy use for artificial lighting.
No Heating Or Cooling: The glazing is placed in the lightest possible state while not exceeding a daylight threshold.
Heating Demand: To allow a higher proportion of solar heat gains, the glazing is placed in the lightest possible state while not exceeding a direct daylight threshold, which may create a risk of visual discomfort to occupants due to glare.
This control logic was implemented in IDA ICE using a visual scripting interface, shown in Figure 7.
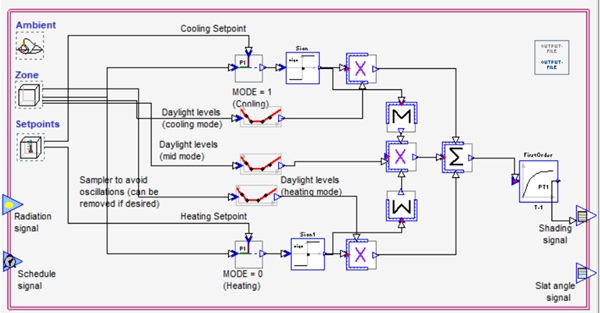
The acceptable range of daylight was assessed using the Annual Solar Exposure (ASE) and Spatial Daylight Autonomy (sDA) metrics. ASE was used as the upper limit of acceptable daylight levels and refers to the percentage of area in the room which receives 1000 Lux or more for at least 250 occupied hours per year at the work plane height. Exceeding this limit may indicate an increased risk of glare. The sDA describes the percentage of floor area that receives at least 300 lux for at least 50% of the annual occupied hours on the horizontal work plane. This represents the lower limit of acceptable daylight.
The possibility for implementation of this control logic in IDA ICE was limited and the chosen strategy to use pre-determined profiles to select the glazing state coefficient, which scales linearly between the dark and light states, depending on the measured daylight level on an internal grid of points. The grid was evenly distributed across the internal space at a working height of 850mm above floor level. These control profiles had to be specified before running each annual simulation and constant at each timestep, so it was necessary to set these profiles iteratively by a trial and error process of checking the annual daylight levels for compliance with the ASE and sDA thresholds then adjusting and rerunning if necessary. Different profiles were created for periods of cooling demand, heating demand or neither of these.
This calibration process was undertaken for the South orientation, to optimise the control strategy for the elevation which has the greatest solar exposure in Amsterdam and therefore largest potential for energy benefits.
As an example, one set of final coefficient profiles is shown in Figure 8. In the cooling state, the glazing transitions towards the dark state (1.0) to reduce solar gains more quickly than when in the heating state. The opposite is true for the heating state.
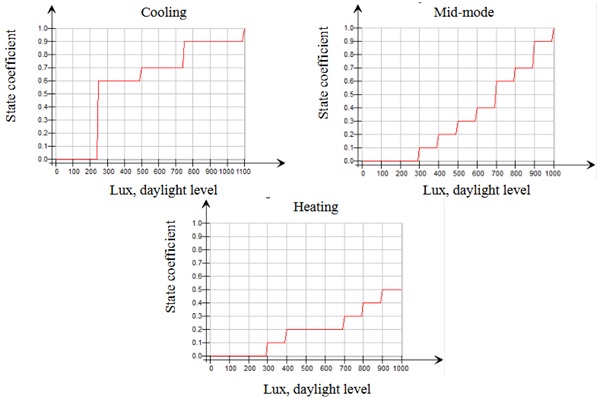
4. Results
The results of the daylight modelling are shown in Figure 9. These show that the Annual Solar Exposure (ASE) is significantly reduced for all elevations, suggesting that the ELM dynamic glazing product is reducing higher levels of direct sunlight which can contribute to a risk of visual discomfort (glare) to the occupants. The Spatial Daylight Autonomy (sDA) for the South elevation, for which the control strategy was optimised, indicates a relatively small reduction of 6%.
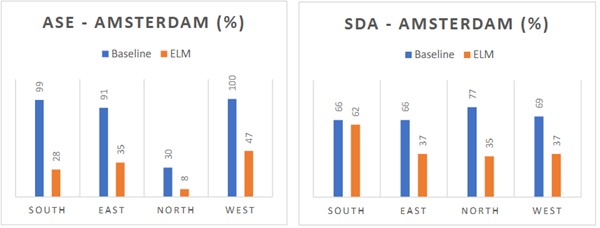
This shows that the minimum daylight levels are not significantly affected by the control strategy when optimised, hence a significant increase in artificial lighting demand would not be expected. In combination, these results indicate the ELM product can be beneficial to daylight performance and may reduce potentially uncomfortable high levels of daylight without compromising minimum daylight levels.
The energy results indicate that there are both heating and cooling demands for both the baseline and ELM glazing, as expected for the temperate climate in Amsterdam. The ELM product achieves both heating and cooling energy reductions for all elevations, except for the heating energy in the South elevation. The largest overall energy reductions are seen for the South elevation as this is the most exposed to the sun and has an optimised control strategy. This demonstrates the potential of dynamic glazing products, such as the ELM, to improve energy performance while suggesting that further improvements could be achieved if the control strategy is further refined.
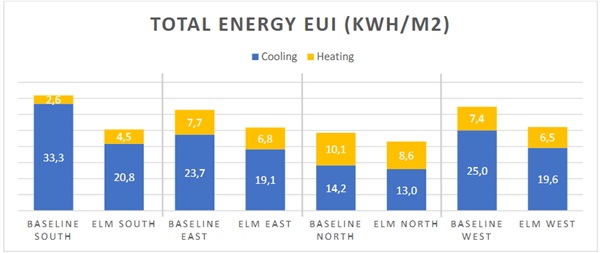
5. Discussion
These results indicate the potential energy and daylight benefits of ELM dynamic glazing technology when compared to existing glass coating solar control technology. This is due to the ability of the dynamic glazing to adjust the glass transmission characteristics to suit the varying climate conditions throughout the year. Existing solar control coatings are instead typically specified to reduce solar gain during summer months, which leads to darker glass with less light and solar transmission than optimal during other times of the year, like winter. This implies that a static glazing solution is often not working optimally for most of the year.
The study also indicated the limitations of implementing dynamic glazing control strategies in commercially available energy modelling software. IDA ICE was believed to be the most capable and flexible, yet the process of setting up the control profiles and calibrating these to achieve suitable daylight levels was a time-consuming process and specific to each orientation. This would also require calibrating for different climates. Further development is required to create alternative control strategies which are faster to implement, particularly when adapting to each orientation or climate.
6. Conclusions & Further Studies
It has been shown that in temperate climates such as Amsterdam, the eLstar ELM product when applied to a typical double-glazed unit with a low-e coating can achieve significant operational energy for both heating and cooling while also improving internal daylight conditions. Further simulations could consider comparisons to other dynamic glazing products and consider the impact on internal lighting energy.
While still in development, this is an exciting technology to improve the energy performance and daylighting conditions of buildings. ELM technology is currently under development to validate a first product qualification. The emphasis will then be on IGU integration and increasing scale of production. Future development of ELM products will rely on technology and system development. From a technology point of view, further improved optical performance is expected as well as development of new colours, typically white and IR pigment types to enable separate modulation of light and heat.
Major development steps will occur on a system level to make ELM technology more beneficial for end-users. Integration of photovoltaics to ELM design without impact on current optical performance is also being considered. This is seen as a major step for mass adoption. This will be further facilitated by the development of non-volatile inks to maintain transmission states without power. Antenna integration is another area that can contribute to the mass adoption of dynamic windows, as well as adding significant value. Developing free cutting ELM modules and non-rigid products will further enhance access to new markets and applications.
References
https://www.linkedin.com/feed/update/urn:li:activity:7156912526776045568/
https://www.equa.se/en/ida-ice
Casini, M: Active dynamic windows for buildings: A review. In: Renewable Energy Vol. 119, pp.923-934 (2018).
Lollini, R., Danza, L., Meroni, I.: Energy efficiency of a dynamic glazing system. In Solar Energy Vol. 84 Iss.4 pp.526-537 (2010).
Baetens, R., Jelle, B.P., Gustavsen, A.: Properties, requirements and possibilities of smart windows for dynamic daylight and solar energy control in buildings: A state-of-the-art review. In: Solar Energy Materials and Solar Cells Vol. 94 Iss.2 pp. 87-105 (2010).
Ruggiero, S., De Masi, R.F, Assimakopoulos, MN., Vanoli, G.P.: Energy saving through building automation systems: Experimental and numerical study of a smart glass with liquid crystal and its control logics in summertime. In: Energy and Buildings Vol. 273 (2022).