Source: glasstec
In its study “Glass 2045 – Decarbonisation of the Glass Industry”[1] the Federal Association of the Glass Industry (“Bundesverband Glasindustrie e.V.” - BV Glas) in cooperation with Stuttgart University’s Institute of Energy Economics and Rational Energy Use (“Institut für Energiewirtschaft und Rationelle Energieanwendung – IER”) charted and compared three transformation pathways which can lead the energy-intensive glass industry with its direct emissions towards climate neutrality by 2045. In the long term, the key lies in replacing natural gas in melting – currently accounting for 77% of the final energy mix – with electrical power and green gases. The Association and the Institute identify the highest probability of success in a gradual changeover to hybrid melting technologies. Focusing on decarbonisation as a focal theme in October, glasstec has examined the study highlighting how the path towards to CO2 neutrality in the glass sector – and in the container glass industry in particular – might be achieved.
[1] Leisin, Matthias; Radgen, Peter: Glas 2045 – Decarbonisation of the Glass Industry. IER, University Stuttgart, Study commissioned by Bundesverband Glasindustrie e.V., Stuttgart, 2022
In German glass production about four million tons of CO2 are emitted annually especially by firing the melting tanks with natural gas but also through process-related, chemical reactions of the raw materials used. There are few alternatives for the latter and carbon capture and storage (CCS/CCU) is hard to implement in view of the comparatively low CO2-concentrations in glass industry waste gas. There is a need for further research and the development of a CO2-infrastructure here. The biggest lever for decarbonisation therefore is replacing the fuel used for the process heat – moving away from natural gas to electrical power and green gases (hydrogen, biogas, synthetic methane). Technologically refitting the glass melting units originally designed for gaseous fuels poses a major challenge especially since other processes, such as the use of waste heat, have been interconnected in most production lines for a long time now. This task can only be accomplished by 2045 if the competitiveness of the industry is maintained and policymakers continue to see transformation as an existential challenge for society at large and drive it forward – indeed much depends on the successful, EU-wide transition from fossil fuels to regenerative energy and green gases.
With a view to obtaining a precise assessment of the status quo, the study analysed the factories producing container glass, flat glass and special glass in Germany – considering all the variables such as the numbers and types of melting tanks, production output and energy consumption; it examined three possible transformation pathways for the use of zero-emission energy sources – depending on the suitability and availability of the technology for the glass product to be manufactured, the availability of infrastructure as well as manufacturers’ already communicated or planned decarbonisation measures. In the “BAU” scenario no material changes versus the current state of the art in the individual glass works are assumed until 2045 – and this served as a benchmark for the following analysis of the alternative transformation pathways “Electrification”, “Hydrogen” and “Hybrid Scenario”, which were simulated in terms of energy consumption, CO2 emissions and foreseeable costs.
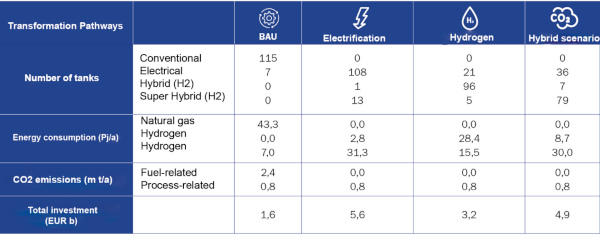
Chart: “Bundesverband Glasindustrie e.V.”
In the three transformation pathways the technologies used today are completely replaced by hybrid tanks, super hybrid tanks or all-electric melting units by 2045 – depending on their potential suitability. In the renewable concepts natural gas is gradually replaced by green hydrogen by 2045 so that fuel-related emissions go down to zero. As a function of the scenario electricity demand rises to 15.5 – 31.3 PJ and hydrogen demand to 2.8 – 28.4 PJ per year. The complete refitting to hybrid and all-electric melting tanks and the adaptation of the energy infrastructures require investment amounting to EUR 3.2 – 5.6 billion by 2045. The lower limit of EUR 3.2 billion represents the investment needs in a hydrogen scenario since the outlay involved in switching to this new fuel is comparatively low. However, whether green hydrogen will be widely available seems hard to tell. And, finally, process-related CO2 emissions amounting to 780,000 tons per year will remain in 2045 because no alternatives to the raw materials used for glass production have been found so far. To avoid these emissions, infrastructure for carbon transport and storage would be required by 2045.
Transformation of the container glass industry:
Energy, emissions, costs
Considering the study results, it is the hybrid transformation pathway that looks to be the most promising avenue for the glass industry as a whole since it is more flexible in view of the technology solutions to be deployed. With an output of 4.1 million the container glass industry manufactures the majority of the 7.4 million tons of glass produced across Germany. Here, in line with the hybrid transformation pathway the first hybrid tanks operated with electrical power and natural gas will be used from the middle of this decade; towards the end of this decade the first all-electric melting units for producing glass containers for beverages and food will go into operation. From 2030 the first hydrogen-only tanks, super hybrid tanks and all-electric tanks will follow. From 2040 the super hybrid tanks will start being changed over from natural gas to hydrogen – provided a complete green hydrogen grid has been built in Germany. By 2045 even the last conventional melting units will make way for hybrid tanks fuelled by hydrogen and all-electric tanks. Energy consumption: the changeover results in a marked increase in electricity needs, which will rise to 17.3 PJ (4,805 GWh) by 2045, according to the study. In addition, hydrogen will be needed in the order of 2.3 PJ per year. The fossil fuel natural gas will be completely substituted by 2045.
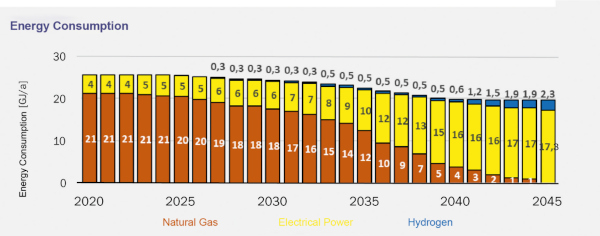
Chart: “Bundesverband Glasindustrie e.V.”
CO2 emissions: The use of all-electric and hydrogen-powered hybrid tanks will reduce direct CO2 emissions to zero by 2045. Furthermore, decarbonisation across the entire electricity sector will lead to a reduction in direct CO2 emissions. In addition to the already high proportion of recycled cullet, carbonates will also be used in future to manufacture container glass. By 2045, process-related emissions will have fallen to 328,000 tonnes of CO2 per year, a total reduction of 83%.
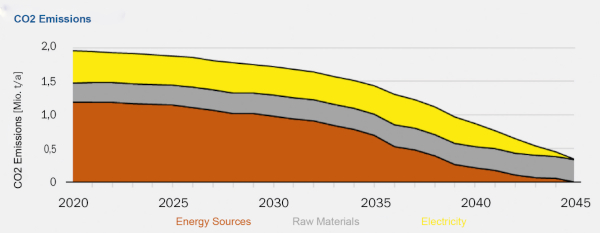
Chart: “Bundesverband Glasindustrie e.V.”
Production costs: the operating costs for producing container glass will increase with the use of the new energy sources. The share of energy costs will increase by around 110%, the specific CO2 costs will grow by 19%. Overall, production costs will increase by around 16% to an estimated EUR 526 per tonne of container glass.
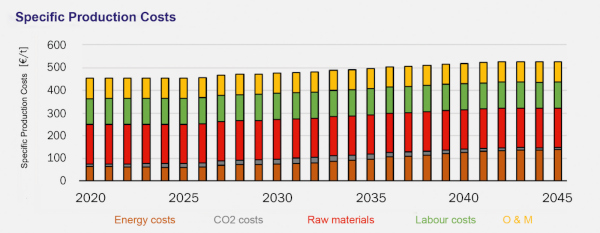
Chart: “Bundesverband Glasindustrie e.V.”
In the outlined hybrid transformation pathway investment amounting to EUR 3.2 million will be needed in the container glass industry by 2045.
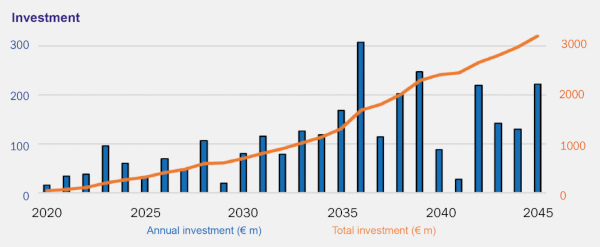
Chart: “Bundesverband Glasindustrie e.V.”
Decarbonisation is one of the hottest topics of glasstec and will also be addressed at the trade fair’s architecture forum in October.
For tickets and more information on glasstec 2024, the exhibitor and product databases as well as the high-calibre supporting programme go to: www.glasstec.de
glasstec Programme Overview:
https://www.glasstec.de/de/Programm/%C3%9Cbersicht_1
Marc Everling studied media education at the Technical University Brunswick, worked as a consultant in PR and marketing agencies for 14 years, and as Head of Marketing at one of the global flat glass players for six years. In February 2021 he founded his networking agency specialised in communications consulting and press liaison for construction material producers, initiatives, associations, trade fairs and architects which work and produce sustainably in the interests of the ecological transformation of the construction sector. Photo: Marc Everling Nachhaltige Kommunikation