Such glazing can be produced by printing human-visible, first-surface coatings on glass, in specific patterns. Another option is to print a UV-reflective coating on the glass to make use of the unique vision characteristics of birds. Such coatings have a lower visual impact on the human viewer.
Candidate coatings have been tested at the Powdermill Avian Research Center in Rector, Pennsylvania, USA. Avoidance scores of 70 to 92% have been observed for the candidate coatings. The testing conditions and a description of the avoidance score will be discussed.
Introduction
The transparency, strength and formability of glass makes it a material of choice for the exterior surfaces of buildings. The ability to make vacuum insulated glass (VIG) units, to decorate with enamels and functionalize the surfaces of the glass with reflective and electrochromic coatings further cements glass as a material for the future. While glass can be used to create awe-inspiring exterior surfaces for buildings, its use comes at a price. It is estimated that by the American Bird Conservancy that 100 million to 1 billion birds a year are killed by collisions with glass. Here, permanent glass coatings useful for the prevention of bird strikes will be discussed.
Materials
Annealed soda-lime glass sheets with a thickness of 3.5 to 4 mm were cut to 1 meter by 0.5 meters and the edges of the panes were seamed. The glass was then washed in an industrial washer, dried and stacked for use. First surface enamels in four colors were obtained from Ferro Corporation of Washington, PA, USA.
The colors of Blue, Green, Sweatshirt Gray and Etch were chosen due to the demand for these colors in architecture. TC1557-31B Paste and TC1557- 31N Paste were obtained from the Ferro Corporation Technical Center of Independence, OH, USA. Nylon screens with a mesh sizes 110.80 and 305.40 (each denoting mesh/inch and thread size in microns, respectively) were obtained from Schilling Graphics of Galion, OH, USA.
Tempering line time was obtained from Paragon Tempered Glass of Antwerp, OH, USA and Laurier Glass of Quebec City, QC, Canada. Digital printing and tempering of a 1 meter x 0.5 meter pane was arranged by DipTech, A Ferro Company of Smithfield, RI, USA. Wild song birds were netted at the Powdermill Avian Research Center in Rector, PA, USA.
UV-VisNIR spectra were obtained on a Perkin-Elmer Lambda 950 UV-Vis-NIR Spectrophotometer and a Perkin-Elmer Lambda 1050 UV-VisNIR Spectrophotometer. UV Photography was accomplished using a UV-SYS-01, available from Oculus Photonics of Santa Barbara, CA, USA.
Experimental
First Surface Enamels. The first surface enamels obtained from Ferro Corporation in Washington, PA were printed onto the sodalime glass panes with 110.80 Mesh nylon screens. One screen possessed vertical stripes with a width of 1” (2.5 cm), which were spaced apart by 2” (5 cm). This screen was used to print the Etch enamel only. Another screen possessed a diagonal array of ½” (12.5 mm) dots, with their centers spaced 2” (5 cm) apart. This second screen was used to print all four colors. After printing, the panes were passed through a drying oven to remove the screen print solvent from the prints. The glass was then tempered, using a furnace temperature of 710°C and push rates and quenching parameters usual for the 4 mm glass upon which the prints were made. After cooling, the panes were packaged for shipping.
Digital-Ceramic-Printed Pane. A pattern of random triangles of different colors was designed by Dr. C. Shepperd of the American Bird Conservancy and was submitted to DipTech, A Ferro Company for digital ceramic printing. A 1 meter x 0.5 meter pane of glass was printed with the pattern and tempered in a similar manner to what was described above.
Multi-Layer Coatings. An automatic screen printer was set up with a 305.40 Mesh screen in the stripe pattern. TC1557-31B Paste was then applied to the screen for printing. Prints were made and the glass was passed through a drying oven and fired with a tempering fire. This print deposits a relatively high indexof-refraction oxide coating on the glass after firing.
The excess paste was removed from the screen and it was washed with de-natured alcohol. After the screen was dry, it was set up with TC1557-31N Paste. The previously fired panes were then printed a second time. The paste was applied to the glass over the previously fired layer. The glass was again placed in a drying oven to remove the solvent from the print. The pane was then sent through a tempering fire a second time.
The TC1557- 31N Paste fires to provide an oxide layer with a relatively low index of refraction. To complete the three-layer coating, the screen was set up with the TC1557-31B Paste again and panes with two fired layers already applied were printed a third time. In a similar manner, the five-layer coating was completed by adding print/dry/fire cycles for the TC1557-31N Paste and the TC1557-31B Paste to panes already printed with three layers. The glass was packaged to ship.
Flight Tunnel Testing. The flight tunnel test has been described in detail elsewhere.3-4 In summary, wild song birds are netted at the Powdermill Avian Research Center. The birds are examined for species, sex and health before being banded. If the bird appears to be “bright,” meaning that it was not too stressed from the capture and banding process, it is placed in a dark cloth bag. Meanwhile, the flight tunnel is set up.
The apparatus consists of rectangular structure with approximate inside dimensions of 1 meter by 1.5 meter by 10 meter. The interior of the structure is lined with black felt. On one side, mirrors are used to cast light on a blue and white, cloud and sky scene, which is spaced away from the end of the tunnel. Two panes of glass are mounted at the end of the tunnel. One pane is a blank of untreated glass. The other pane is the treated pane. Inside the tunnel, near the glass, a thin safety net is located.
This net prevents birds from actually contacting the glass during testing. The tunnel can be rotated to catch the sun in the best manner. At the opposite end of the tunnel from the installed glass, a small port allows for the bird, contained in the felt bag, to be inserted into the tunnel and released. The bird choses a pane of glass at which to fly, bounces off the safety net and is then free to go through as small opening to the side of the safety net.
The flights are videotaped so that investigators can determine at which pane the bird flies. The goal is for the bird to see the coated glass and to choose to fly at the blank glass every time. The statistics generated result in the formulation of an avoidance index or AI. An AI near 50% indicates random behavior, where the coating does not give the bird any queue. The American Bird Conservancy gives a rating of “Preferred” to any coating that gives an AI of 70% and a rating of Most Preferred to any coating that achieves an AI of 80% or more.
Optical Characterization. UV-Vis-NIR spectra were obtained on a Perkin-Elmer Lambda 950 and a Perkin-Elmer Lambda 1050. Both instruments were equipped with a Spectralonlined integrating sphere, which allows data collection from 250 nm to 2500 nm. Both % Transmission and % Reflectance spectra were obtained. % Reflectance are of more importance to this discussion. The substrate glass usually reflects about 5% of the UV light. Since it is known that birds need a contrast of 20% or to see and avoid the glass, engineering coatings with good reflectance values allows for the best chance to create a useful coating.
UV Images. UV images were obtained with a camera obtained from Oculus Photonics. The camera was equipped with a band-pass filter with a transmission band from 335 nm to 510 nm. This range was chosen in an attempt mimic the wavelengths visible to bird through two of their four cones. The detector of the camera therefore measures the amount of reflected or emitted light in the range of 335 to 510 nm from the object, theoretically giving humans an idea of what a bird would be capable of seeing. Illuminators at wavelengths of 365 nm and 395 nm were used to light the panes. The panes were set up against a black background for UV photographs.
Results
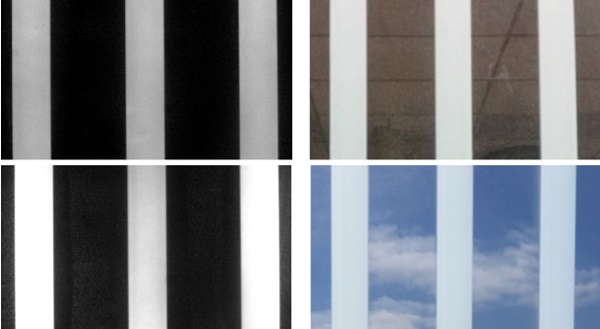
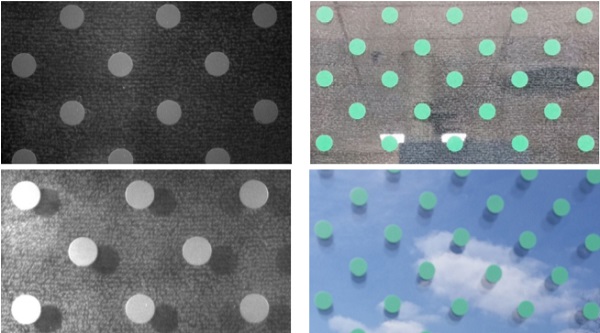
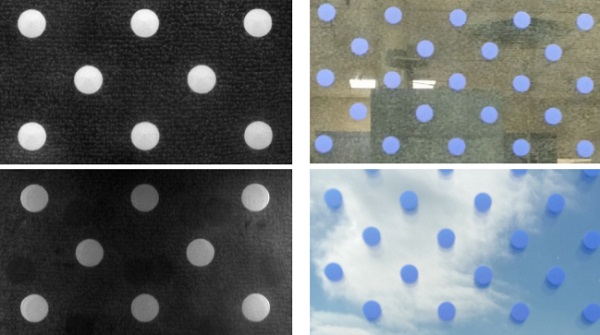
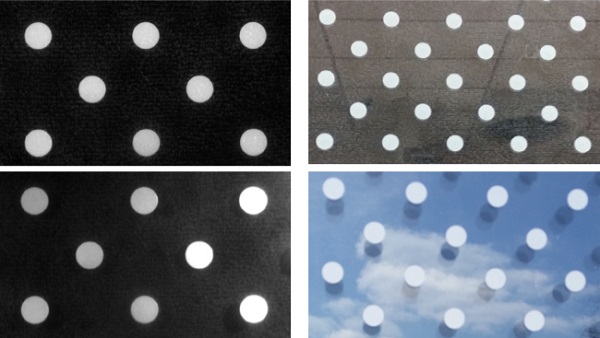
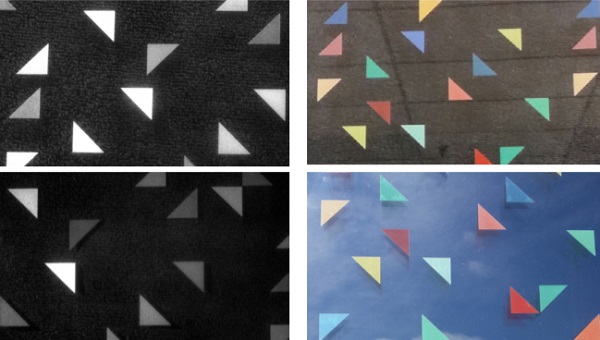
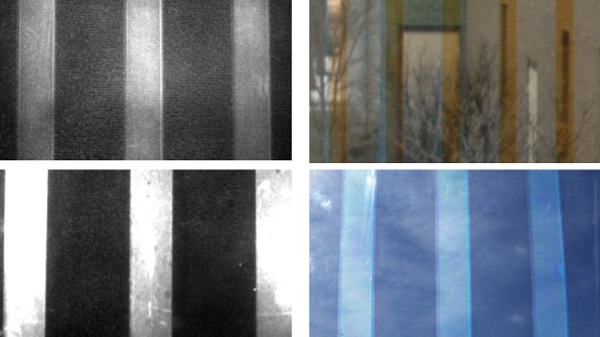
Discussion
Several strategies exist for reducing bird collisions with glass, according to “BirdFriendly Building Design,” published by the American Bird Conservancy. A major initiative is to request that the lights be turned off in high-rise buildings at night. Other, semipermanent strategies are also possible. Parachute cord can be hung in front of windows to make Acopian Blinds. Stickers or tape can also be applied to glass to help the birds to see and avoid it.
These strategies suffer because they are not permanent, weather-durable solutions. Permanent, weather-durable options exist. The glass can be acid-etched in bird-friendly patterns to give glass with some utility for reducing strikes. A detriment to this technique is that the color is basically restricted to variants of the etch appearance.
Another option is to laminate a plastic sheet containing UV-absorbing material printed in a bird-friendly pattern between two panes of glass. This strategy was examined in reference 1. The goal of the present work is to supply permanent, bird-friendly coatings for glass that can possess vivid colors or be nearly transparent to humans.
Based on discussions with ornithologists Dr. Christine Sheppard of the American Bird Conservancy and Prof. Daniel Klem, Jr. of Muhlenberg College, Dept. of Biology, bold patterns of stripes and dots were designed for the testing of the first surface enamels and multi-layer coatings. The goal of the research was to prove that the materials printed on the glass are suitable for the prevention of bird strikes and not what patterns are useful.
The dimensions of the features of these coatings were chosen based on the results described references 5-11. Basically, this is the 2” x 4” (5 cm x 10 cm) rule. Horizontal lines or rows of dots should be placed 2 inches (5 cm) apart and vertical lines or rows of dots should be spaced 4 inches (10 cm) apart. Such dimensions give the bird the impression that it cannot fit between the markings and thus it should divert from the approaching barrier. If the goal is to prevent hummingbird strikes, it has been found useful to reduce the spacing of the vertical features to 2 inches (5 cm) as well.
The first aim in this work was the design of the transparent, multi-layer coatings seen in Figure 6 and the last two entries of Table 1. The goal was to make use of the fourth type of cone that birds possess in their eyes compared to humans, please see Figure 7. It should theoretically be possible to manufacture coatings that are UV reflective, with a peak at 370 nm, that are also nearly invisible to human beings.
So called ¼ Wave Stacks were chosen as a strategy for producing these coatings. Two pastes were designed, one with a relatively high index of refraction and the second with a relatively low index of refraction. When the pastes are printed with the correct film depth and fired, they give oxide layers with thicknesses on the scale of ¼ of the wavelength of the light that is desired to be reflected, here meaning 50 to 80 nm thick. When the coatings were submitted for tunnel testing, it was found that birds can in fact see the coatings and divert from them, as noted by the avoidance indices of 80% and 71%, respectively, for the three-layer and five-layer coatings.
In order to visualize the coating as a bird could, a camera optimized to collect UV light was procured. Filters for the camera were chosen so that light with wavelengths of 350 to 510 nm were allowed to strike the detector. This is the closest mimic possible the UV and violetcentered cones that birds possess, as seen in Figure 7. The UV images in fact show good reflection of the UV light, especially for the image taken with 395 nm illumination, please see Figure 6, Upper Left and Lower Left.
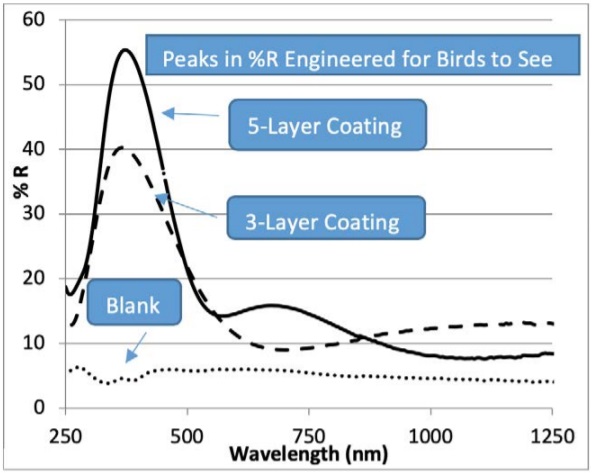
Due to the physics of the oxide layers applied during the manufacture of the coatings, there is some human-visible component to the multi-layer coatings. In the interior view of Figure 6 Upper Right, an orange color exists when the coating is viewed from the inside. Upon viewing the coating from the outside, a mirror-like appearance is seen, please see Figure 6 Lower Right.
It is possible that the visual impact of this coating could be minimized by reducing the size of the printed features. Another problem with these multilayer coatings is the intensive processing needed to manufacture them. Three to five cycles of printing, drying and firing are needed to apply the coatings. Glass fabricators are also loath to firing the glass multiple times, fearing that there could be breakage issues during the second and higher firing cycles.
With these concerns in mind, the strategy next turned to submitting first surface coatings to tunnel testing. These coatings are designed to be applied to the exposed surface of the glass. The coatings therefore need to be weather durable and should not cause undue stress related weakness to the substrate glass. The imitation Etch coating was printed in two different patterns, a broad stripe pattern and in a dot pattern.
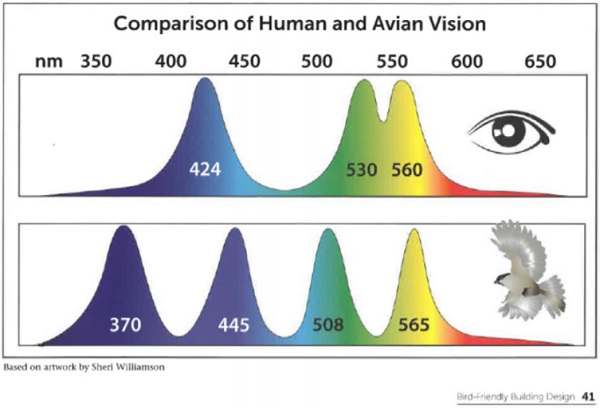
The Etch enamel is shown printed in the stripe pattern in Figure 1. In addition, three other colors of architectural interest were chosen for the study: Green, Blue and Sweatshirt Gray, as seen in Figures 2-4. As can be seen in Table 1, all of the coatings show significant activity toward diverting birds from strikes, due to the avoidance indices in the range of 76 to 87%. The Etch print in the stripe pattern attained a rating of “Preferred” by the American Bird Conservancy, since it possesses an AI≥70%. The four trials printed in the dot pattern attained the “Most Preferred” rating from the American Bird Conservancy due to AI’s≥80%. The highest score for the first surface coatings was attained by the Green coating. Possibly, the good contrast it has from blue sky and clouds is responsible for this behavior.
A digitally printed sample was also submitted for testing at the flight tunnel, please see Figure 5 and Table 1. This print gave the best performance of all of the trials, with an AI of 92%. It is interesting to consider the reasons why this coating performs so well. The outdoor image of the coating shows that there is good color contrast between the coating and the blue sky and clouds reflected from the glass, even to humans. The coating also shows various shades of gray in the UV images, so it is possible that all four types of cones in the birds’ eyes are seeing contrast. The pattern shapes are also “unnatural.” The triangles do not resemble trees, animals, rocks or even buildings. This could be a powerful queue to the birds to divert form the glass.
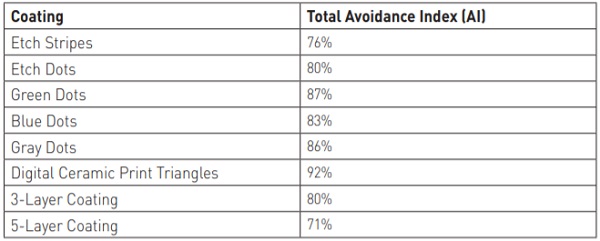
Conclusions
It is possible to provide permanent coatings for glass that can help birds to see the glass and avoid it. This conclusion is based on the results of flight tunnel testing of various coatings at the Powdermill Avian Research Center in Rector, PA, USA, which is under the direction of the Carnegie Museum of Natural History in Pittsburgh, PA, USA. The Avoidance Indices (AI’s) of 71 to 92% indicate that 71 to 92% of birds chose to fly at the blank glass set up beside the test pane because they can see the pattern on test pane. These behaviors allow the American Bird Conservancy to give ratings of “Preferred” for coatings with AI≥70% and “Most Preferred” for coatings with AI≥80%.
The optical reasons such coatings work well were examined with the use of a UV Camera, a conventional camera and a UV-Visible-NIR spectrometer. Coatings such as the 3-Layer and 5-Layer Coatings with relatively low visible impact to humans can be quite visible to birds. This can be seen by examining the large peaks in the % Reflectance (%R) spectra of Figure 7 and comparing them to the UV Camera images and the human-visible images seen in Figure 6. Human-visible colors also work to deter bird strikes. The variable colors of the digitally printed triangles gave the best results with an AI of 92%.
Future Work
The work of preventing bird strikes has just barely begun. It is necessary to begin building an approved list of patterns and colors that prevent bird strikes. The use of digital printing will be of great assistance in this endeavor, since both the patterns and the colors can be infinitely varied. At a certain point, it should be theoretically possible to certify a material for bird safe glazing if it is printed in a “bird friendly pattern,” so that the testing costs will be reduced. Work should be undertaken to expand the color palate for first surface coatings, giving architects and clients a wider array of colors and appearances from which to choose.
The flight tunnel test is an interesting and reproducible method for obtaining data on what birds can and cannot see during flight and currently is the method by which coatings are certified. However, a second method exists that may be more realistic. Klem and coworkers at Muhlenberg College in Allentown, PA, USA have developed a competing method.
A bird feeder is set up in the middle of a meadow surrounded by forest. At the edges of the clearing, frames are set up for the 3’ x 4’ (approximately 1 meter x 1.3 meter) test panes. The frames are set so that the birds can fly above, below or to the sides of the pane. Two panes of each pattern are needed for the test. One pane is placed in a frame with no backing, to mimic a window in a greenhouse or breezeway.
One pane is set in a frame and is backed by a black curtain to mimic a window in a dark house. Each day, the panes are monitored early in the morning and in the evening to determine the number of strikes and specimens that occur for each pane. This test goes on for six months and so is quite labor intensive and expensive. But a coating that could pass both types of testing should be considered as state-of-the-art.
Acknowledgements
This work would not have been possible without a lot of assistance and previous research. Groups such as Chicago Bird Collision Monitors, FLAP Canada and BirdSafe Pittsburgh, to name just a few, monitor buildings for dead and injured birds. It is the statistics that these groups generate that have brought this issue to light.
Dr. Christine Sheppard is thanked for her support, training and her design of the randomly colored, triangle pattern that scored so well in flight tunnel testing. Prof. Daniel Klem, Jr. is thanked for interesting discussions during a pleasant dinner in Allentown, PA. The glass cutting, press room, drying line and tempering line crews at Paragon Tempered Glass of Antwerp, OH, USA and Laurier Glass of Quebec City, QC, Canada are thanked for the glass fabrication of the first surface and multi-layer trials used in this work, respectively.
Dip-Tech, A Ferro Company, is thanked for arranging for the digital printing and tempering of the multi-colored triangle pattern designed by Dr. Sheppard. The technicians and scientists at the Powdermill Avian Research Center in Rector, PA, USA are thanked for the testing that they conducted on the glass trials.
References
1. “Evaluating the Effectiveness of Select Visual Signals to Prevent Bird-Window Collisions.” D. Klem, Jr. and P. G. Saenger. The Wilson Journal of Ornithology, 125(2): 406-411, 2013.
2. “Bird-Building Collisions in the United States: Estimates of Annual Mortality and Species Vulnerability.” S. R. Loss, T. Will, S. S. Loss, and P. P. Marra. The Condor, Vol. 116, 8-23, 2014.
3. “Farben-Glasdekorfolie-Getöntes Plexiglas 12 Weitere Experimente im Flugtunnel II.” M. Rössler and W. Laube. Vermeidung von Vogelanprall am Glasflächen, 1-36, 2008.
4. “Glass Pane Markings to Prevent Bird-Window Collisions: Less Can Be More.” M. Rössler, E. Nemeth and A. Bruckner. Biologia, Vol. 70/4, 535-541, 2015.
5. US Patent 8,114,488 B2. “Window for Preventing Bird Collisions.” J. Alvarez. Feb. 14, 2012.
6. US Patent 8,114,503 B2. “Method and Apparatus for Preventing Birds from Colliding with or Striking Flat Clear and Tinted Glass and Plastic Surfaces.” D. Klem, Jr. Feb. 14, 2012.
7. US Patent 8,389,077 B2. “Window for Preventing Bird Collisions.” J. Alvarez. Mar. 5, 2013.
8. US Patent 8,506,089 B2. “Avian Deterrent for Glass Using Projected UV Light.” K. W. Kayser. Aug. 13, 2013.
9. US Patent 8,869,480 B2. “Method and Apparatus for Preventing Birds from Colliding with or Striking Flat Clear and Tinted Glass and Plastic Surfaces.” D. Klem, Jr. Oct. 28, 2014.
10. US Patent 9,650,290 B2. “IG Window Unit for Preventing Bird Collisions.” G. Vikor and B. Disteldorf. May 16, 2017.
11. US Patent 9,862,835 B2. “Window Coating.” P. Thottathill, P. Kesavan, J. Ryan and S. Mukherjee. Jan. 9, 2018.