Article Information
- Digital Object Identifier (DOI): 10.47982/cgc.9.590
- Published by Challenging Glass, on behalf of the author(s), at Stichting OpenAccess.
- Published as part of the peer-reviewed Challenging Glass Conference Proceedings, Volume 9, June 2024, 10.47982/cgc.9
- Editors: Christian Louter, Freek Bos & Jan Belis
- This work is licensed under a Creative Commons Attribution 4.0 International (CC BY 4.0) license.
- Copyright © 2024 with the author(s)
Authors:
- Marialena Toliopoulou - Delft University of Technology
- James O'Callaghan - Delft University of Technology
- Paul de Ruiter - Delft University of Technology
Abstract
The architectural prominence of glass structures, driven by ongoing innovations in manufacturing and post-processing techniques, reveals the material's remarkable structural potential. Aluminosilicate glass, distinguished by superior strength and flexibility, particularly in comparison to soda lime glass, facilitates the production of ultra-thin glass with thicknesses as low as 25 μm. This has led to the emergence of "thin glass," defined as any glass below 2 mm in thickness. Thin glass, celebrated for its unique attributes, has found diverse applications in industries like automotive and electronics. In architecture, thin glass holds potential for creating complex, lightweight, and transparent architectural structures. This paper addresses the constraints of thin glass in construction and explores optimal bending techniques to maximize its potential through a detailed study of its properties. The current study establishes design guidelines and a computational approach for utilizing cold bent thin glass in the design process. The findings showcase a successful computational method providing tools, design principles, and guidelines for working with single curved cold bent thin glass panels. The paper also examines suitable connection types for thin glass projects, proposing a hinge clamp connection. A case study illustrates the proposed workflow, resulting in a prototype using a 3D-printed approach for the suggested connection design.
1. Introduction
Typical flat glass is generally known, since it is a material widely used for the past centuries (Wurm, 2007), however thin glass is still to be exploited in the architectural world where it would open new horizons for expressions (Topcu & Marinov, 2020), due to its unique properties. Apart from thickness limitations, significant differences between thin and “regular” glass appear to their mechanical properties (Peters et al., 2019). This paper aims to address this gap by investigating thin glass through a proposed workflow that would assist the design process and is focused on the properties and potential applications of it within architecture. This research explores the mechanical properties of thin glass and examines cold bending to optimize its use.
The material’s composition apart from offering enhance flexibility and limiting its thickness, makes the glass more structurally challenging (Santos et al., 2018). Therefore, innovative testing methodologies and informed design workflows are required, to provide answers wherever traditional standards often fall short.
Drawing insights from industry experts and AGC Europe, while also employing testing methods such as the "clamp bender" (Zaccaria et al., 2022), this research establishes a framework for designing with thin glass. Through an exploration of cold bending techniques – as the safest way of pre and post verification to the proposed methods – and connection design principles, this paper aims to provide designers with tools to harness thin glass's potential.
The current research seeks to propel thin glass designs into the forefront of architectural innovation, offering a structured framework to guide designers in realizing its transformative possibilities.
2. Understanding thin glass
Zaccaria and Gillon (2019) define thin glass as aluminosilicate glass, whose composition varies depending on available products in the market. Aluminosilicate glasses, in general, can withstand higher temperatures, which according to SCHOOT (n.d.) can reach up to 600°C, leading to increased durability.
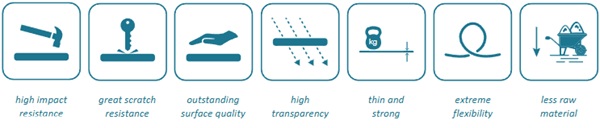
Alongside its different composition, thin glass products are chemically strengthened and consequently they fail, forming a breaking pattern with large fragments similar to a heat strengthened glass. As shown on the figure below, the breaking pattern depends on the inner energy due to pre-stressing. There, since extreme bending results in high loads, chemically strengthened glass elements with great surface quality can fail forming large amounts of smaller sharp fragments (powder like fracture) (Datsiou, 2017).
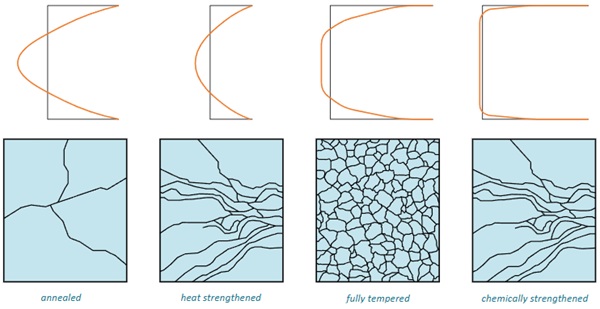
Generally, glass can withstand a lot under compression, however it does not yield and its failure is difficult to predict (O' Regan, 2014). As O' Regan (2014) states: “glass panes can deflect by more than their own thickness” and same applies to the extreme flexibility of thin glass panes. Thus, thin glass requires different handling to determine the strength and for the time being it does not apply to the European code EN16612 (Glass in building – Determination of the load resistance of glass panes by calculation and testing).
2.1. Thin glass design strength
Despite the absence of specific guidelines for glass design, EN 1288 (Glass in building – Determination of the bending strength of glass), which is a part of Eurocode 1 (Actions on structures), is often employed to establish a commonly approved testing method. Additionally, EN16612 (Glass in building – Determination of the load resistance of glass panes by calculation and testing), a component of Eurocode 8 (Geotechnical and seismic design), is recommended for calculating the design strength.
However, since thin glass presents extreme flexibility and the established methods do not correspond to the characteristics of that specific type of glass, large deformations will occur and the specimens will most probably not reach failure (Maniatis et al., 2016). On that manner, “the clamp bender” was developed according to EN 1288-3 (Zaccaria et al., 2022). Test data deducted from this process and that was received from AGC Europe, has been used for the presented research and contribute to the development of the proposed methodology.
According to EN 1288-5, such tests can result in an overestimated bending strength because of the size effect. In order to scale-up the data so as to match the real application the following formula is required:
where m is the Weibull modulus – this is calculated through the Weibull distribution that would be performed in order to define the characteristic strength (𝑓𝑏;𝑘1) – , 𝑉𝐸1 , 𝐴𝐸1 are the volume and area of the specimen accordingly and 𝑉𝐸2, 𝐴𝐸2 are the volume and area of the final glass pane accordingly.
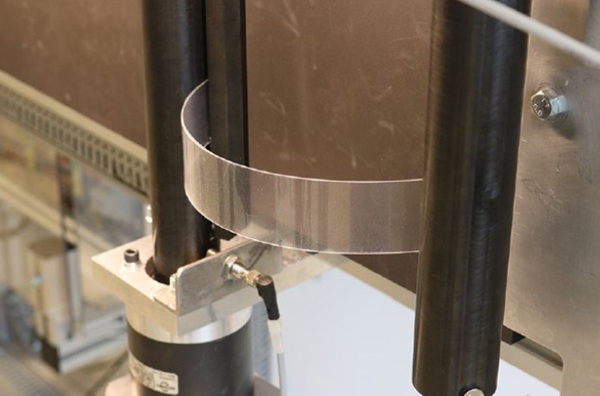
3. Understanding curved thin glass
The process of producing a curved glass panel involves accounting for its deviation from a flat surface (Datsiou, 2017). In order to understand the geometry and behaviour of a curved pane in two dimensions, it is necessary to apply the geometric rules of an arc. That could be understood and modelled computationally while the basis of it could be further developed into following the rules of a developable surface. Gavriil et al. (2020) and Rabinovich et al. (2018) have identified methods to attain double curvature in design by utilizing developable surfaces.
3.1. Cold bending
Cold bending process involves elastically inducing curvature through out-of-plane loads at ambient conditions (Belis et al., 2007). Even though the panel is then subjected to bending stresses throughout its lifetime, it still takes advantage of the additional geometric stiffness due to bending (Gregson et al., 2019).
Accordingly and based on the small thickness of it, thin glass is particularly adept for cold bending (Schneider et al., 2017). Considering the fact that it is substantially lighter compared to a regular float glass panel of the same size, it also makes it easier to be transported and assembled (Gregson, 2018). In addition, the required glass plates of various curvatures can be cold bent into shape without the need for costly moulds, thereby minimizing expenses and making cold bending a highly attractive method for creating curved glass surfaces.
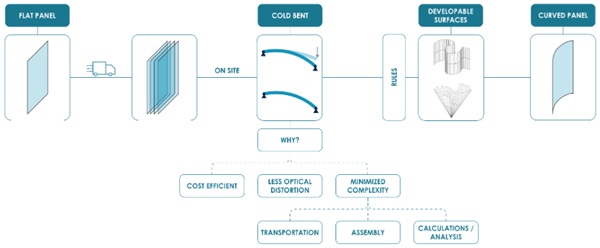
Not only does this method offer energy and cost savings, but it does not compromise the optical quality of the glass from its original flat state because it does not require viscous flow (Datsiou, 2017), unlike thermal bending. Cold bent glass can be used to produce single or double curved forms, with single curvature or developable glass surfaces being easier to form.
3.2. Connection design
Single cold bend glass panes can result in a limited amount of design combinations and require a single principle to allow for their curvature to be achieved.
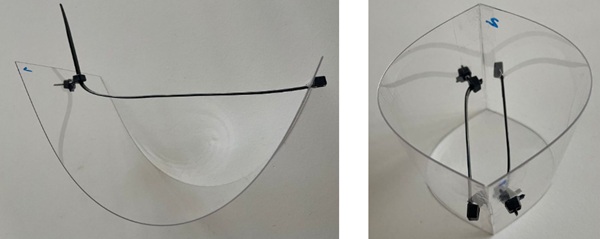
Case studies from previous research projects have led to the classification of appropriate thin glass connections, as depicted in Figure 5. Bolted connections are excluded as the panel’s thickness would not withstand the stress concentration. Additionally, purely adhesive connections are not recommended since the panel's spring back results in higher strength than what high strength adhesives can accommodate considered (Pennetier & Stoddard, 2019). Therefore, adhesives should be used in conjunction with another connection type, such as the one designed by EOC Engineers (EOC, 2019; Gregson et al., 2019). Continuous linear connections, as demonstrated by Stoddard (2019) in a pavilion design and other projects utilizing single and double curved thin glass or as in IGUs (Ottens, 2018; van Driel, 2021), are also considered viable options.
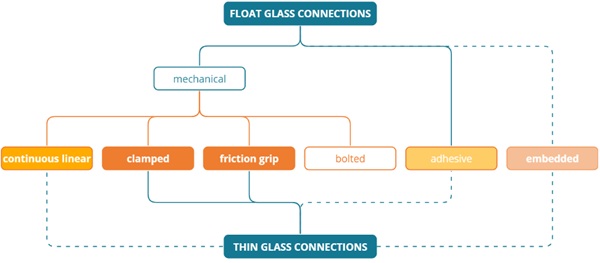
To accommodate the connection principles, a connection has been designed and practically tested-through a prototype. To minimize complexity, one single unit is designed and can be adjusted to connect from one (1) to two (2) cold bent panels simultaneously. This is needed so several panel combinations could be achieved within any design. The hinge principle offers a rather easy way to accommodate two tension cables and therefore two possible radii in a design. The difference is that the option for unequal needed tension would require two bolts for the cable’s pretension.
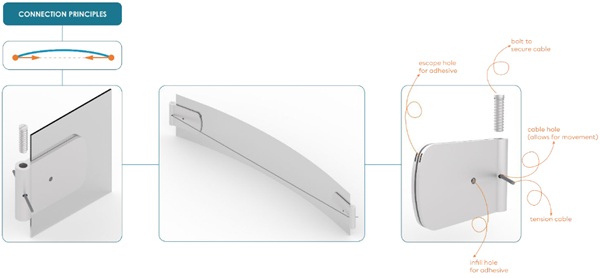
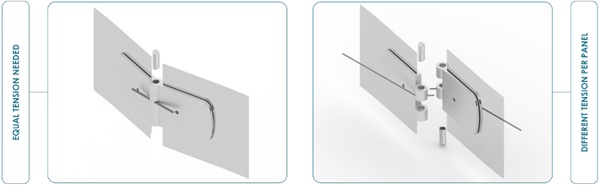
4. Prototype
To demonstrate the feasibility of cold bending thin glass and the suitability of the connection design for such applications, a prototype is constructed. Falcon glass panels were supplied by AGC Europe, with thicknesses of 1.1 mm and 0.7 mm. These chemically tempered panels measure 500 mm by 500 mm and serve as the basis for the prototype.
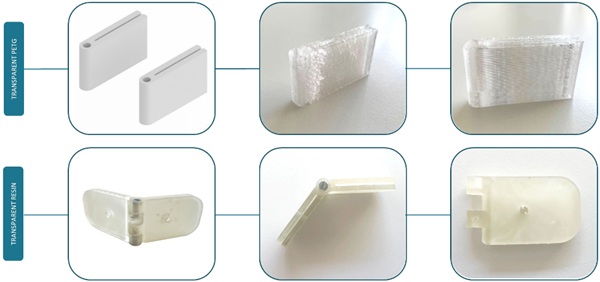
The prototypes were manually assembled on a wooden mould, like the one shown on Figure 12 below. Using clamps on the sides, it is possible to keep the pane bent while attaching the connections to the required spots. Following, tension is applied through the bolt that keeps the cable and panel in place.In the case of the 3D printed connection, no adhesive was needed since the connection would stay in place due to the friction caused by the object’s roughness.
5. Workflow design
The method’s purpose is to incorporate material data and by assigning the possible curved combinations and connection points – based on the aforementioned connection design - as well as by incorporating a structural analysis, a verified design can be achieved. By proposing a closed loop, each step can inform the next as well as the previous, contributing to more informed decision making.
5.1. Guidelines
The proposed workflow was based on the aforementioned, and results in seven (7) steps, that include both scientific data and design-based decisions. Namely, these steps are: a) product availability and data, b) project specific limitations, c) possible radii of curved panels, d) design combinations, e) connection points – represent the connection design utilized, f) finite element analysis, g) informed design. The following sections explain the process and reasoning of the steps that mostly define it, those being the curvature and structural analysis.
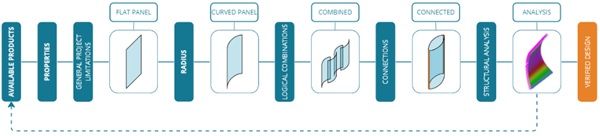
As mentioned, data from AGC Europe as well as glass samples were received and therefore the Falcon glass product was used as the basic input for this computational methodology.
5.2. Curvature
The glass’ curvature is the one that mostly defines the design process and outcome. Therefore, the definition considers the minimum and maximum (flat panel) radii that a single pane could achieve. As per the testing procedure, during the minimum radius of a panel, the maximum stress is reached. The data is then handled to calculate the design value of the product’s bending strength. For a more onerous approach, the worst-case scenario is chosen.
The accepted number of specimens that would provide sufficient data for good estimates is 30 (Lau, 2017) and therefore a number of specimens of 30 and above should be considered. The received and utilized data refers to two sets of 32 laser cut Falcon glass specimens, of a span of 120 mm and 0.50 mm of thickness and another two sets of 32 ground edge Falcon glass specimens, of a span of 120 mm and 0.50 mm of thickness. To describe the strength data obtained from thin glass specimens that have similar macroscopic properties, it is common to use a two-parameter Weibull distribution (Datsiou & Overend, 2018). Therefore, the Weibull distribution of those tests is estimated, and a characteristic strength value is calculated, by considering the European regulations.
For the mentioned data, the resulting characteristic value was calculated to 281,70 MPa. This value is then dependent on the different load case scenarios that will be project relevant and are calculated as shown in Figure 15 below.
5.3. Structural analysis
The mechanical properties of thin glass – or Falcon glass in specific – indicate that a non-linear approach should be considered (Galuppi & Riva, 2022) and a software that is able to perform non-linear analysis is chosen.
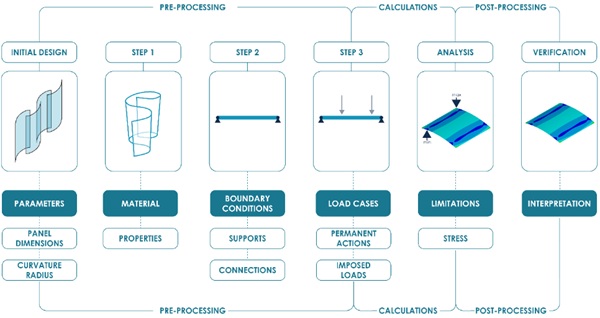
In a project specific occasion, the designer is able to assign load case scenarios that would feed the analysis and the whole loop, feeding back to the minimum radius of the pane.
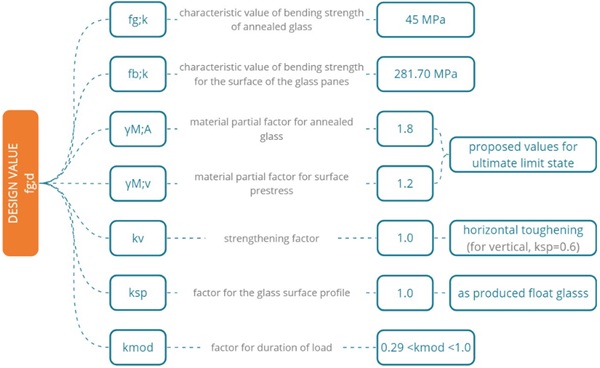
5.4. Closed loop
The first diagram presents the different steps of the suggested workflow as this would appear in a grasshopper definition. Tools like Karamba3D offer the ability of non-linear analysis and the ease of keeping a simplified workflow within the same environment.
However, more sophisticated tools, would be ideal to work with an API inside grasshopper, as this would offer more accurate results.
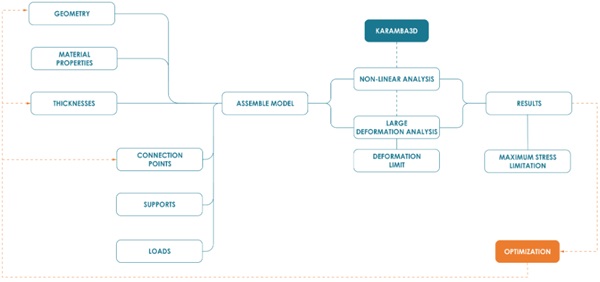
The diagram on Figure 18 below analyses the steps, offering the optional step of the glass panelisation and the optimization process of minimizing waste in production. From an analytical process like the one presented there is the possibility to acquire information for construction and cost process, for example the number of panels, specific dimension, amount of connections and connection cables.

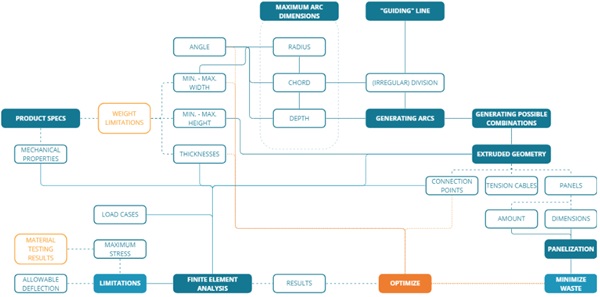
6. Case study
To showcase the use of the computational workflow – as this is shown on Figure 18 – within a design concept, the layout of an existing showroom has been utilized. The masonry partitions are redesigned with curved glass panes. Therefore, the trace of the existing wall is used as a guiding line where the new transparent partitions will be placed on. The figures 19 – 21 below show the steps of the process.
7. Potential and further applications
The investigation into the potential of thin glass in architecture has highlighted its significant promise, although the limited literature on its material capabilities remains a challenge. Thin glass presents an opportunity for a fresh architectural vocabulary, pushing the boundaries of glass design innovation. The proposed computational workflow holds promise for application in diverse projects, contingent upon tailored adjustments. However, successful integration into practice hinges on close collaboration within a design team.
The conducted research highlights several areas warranting further exploration. Firstly, there is a need to establish a comprehensive database of characteristic values for thin glass due to its limited exploration in architecture. Material testing methodologies require further scrutiny to precisely define thin glass properties for architectural and structural applications. Secondly, while cold bending presents cost-efficient and straightforward solutions, alternative bending processes such as lamination bending offer more stable but complex design outcomes with simpler connection designs. Exploring doubly curved surfaces could expand design possibilities further. Thirdly, connections play a crucial role in glass design, serving both structural and aesthetic purposes. Investigating different connection principles and designs is essential, with the potential development of detailed connections for various types of bent thin glass panels. Lastly, streamlining computational processes and enhancing communication between software tools could facilitate optimization across design parameters while ensuring structural integrity. Investigating automation along the workflow and integrating design iterations could further enhance efficiency, albeit requiring precise parameterization from the outset.
Acknowledgments
The authors gratefully acknowledge the contribution of Marco Zaccaria, for his assistance, valuable input and practical support. The authors thank AGC Europe that through Marco Zaccaria provided valuable data and Falcon glass samples, that were key drivers for the completion of this research.
References
Datsiou, K. C. (2017). Design and performance of cold bent glass University of Cambridge].
EOC, E. (2019). Prototype for thin flexible glass pavilion showcased. https://www.eocengineers.com/prototype-for-thin-flexible-glass-pavilion-showcased/
Galuppi, L., & Riva, E. (2022). Experimental and numerical characterization of twisting response of thin glass. Glass Structures & Engineering, 7(1), 45-69.
Gavriil, K., Guseinov, R., Pérez, J., Pellis, D., Henderson, P., Rist, F., Pottmann, H., & Bickel, B. (2020). Computational design of cold bent glass façades. ACM Transactions on Graphics (TOG), 39(6), 1-16.
GPD. (2020, 2019). Sophie Pennetier | Ultra-Thin Glass Projects.
Gregson, S. (2018, November 2018). Thin Glass applications for Yachts International HISWA Symposium on Yacht Design and Yacht Construction, Amsterdam, NL.
Gregson, S., Santelli, L., & Jouy, A. (2019, 7-10 October 2019). Design of the Thin Glass Pavilion. IASS Annual Symposium 2019 - Structural Membranes 2019, Barcelona, Spain.
Maniatis, I., Nehring, G., & Siebert, G. (2016). Studies on determining the bending strength of thin glass. Proceedings of the Institution of Civil Engineers-Structures and Buildings, 169(6), 393-402.
O' Regan, C. (2014). Structural use of glass in buildings (Vol. Second). The Institution of Structural Engineers.
Ottens, R. (2018). HIGH STRENGTH THIN GLASS AS STIFF STRUCTURAL FABRIC TU Delft]. Delft.
Pennetier, S., & Stoddard, J. (2019). Prototyping with Ultra-Thin Glass. Proceedings of IASS Annual Symposia,
Peters, T., Jaschke, S., & Schneider, J. (2019). Thin glass in membrane-like structures-applications, modelling and testing. Proceedings of IASS Annual Symposia,
Santos, F. O., Louter, C., & Correia, J. R. (2018). Exploring thin glass strength test methodologies. Challenging Glass Conference Proceedings,
Schneider, J., Neugebauer, J., Schuster, M., & Peters, T. (2017). Cold-bent thin glass laminates for architectural applications: Computational design and material modeling. Proceedings of IASS Annual Symposia,
SCHOTT. (n.d.). Aluminosilicate Glass.
SCHOTT. Retrieved April 18, 2024, from https://www.schott.com/en-hr/expertise/materials/aluminosilicate-glass,
Stoddard, J. (2019). Concepts for Working with Ultra-Thin Glass in Elastic Bending: Typological Development and Emergent Technology University of Southern California]. Southern California.
Topcu, Ö., & Marinov, V. (2020). Thin Glass in Architecture-Possible Applications and Challenges. Challenging Glass Conference Proceedings,
van Driel, T. (2021). Investigations on the Cold Bending Behaviour of a Cold-Bent Double Glazing Unit with a Rigid Edge-Spacer Frame TU Delft]. Delft, NL.
Wurm, J. (2007). Glass structures: design and construction of self-supporting skins. Walter de Gruyter.
Zaccaria, M., & Gillon, X. (2019). Scaling Thin Glass Use to the Architectural World. Świat Szkła, 24.
Zaccaria, M., Peters, T., Ebert, J., Lucca, N., Schneider, J., & Louter, C. (2022). The clamp bender: a new testing equipment for thin glass. Glass Structures & Engineering, 7(2), 173-186.