First presented at GPD 2017
Rising awareness about safety related to glass usage instigated by accidents due to human impact is the driving factor for evolution of safety regulations for usage of glass in a building. Singapore building authorities look for a solution that complies with the most stringent safety criteria, limiting the induced deflection in a free standing balustrade, in “all layers broken” condition to a limit that is deemed to be safe against “fall through”.
Live load testing of a balustrade, laminated with Ionomer interlayer, was done with a leading railing system supplier. The test concluded that the glass balustrade can be designed for sustaining the design loads, not only in “ pre-breakage” but also for “post breakage” condition, thus providing a very high redundancy in balustrade design.
Introduction
A balustrade can be defined as a system designed to keep people from (in most cases unintentionally) straying into dangerous or ‘off-limit’ areas. Most public places are fitted with guard rails as protection against accidental falls. Any abrupt change in elevation (where the higher portion is accessible) makes a fall possible. Due to this responsibility and liability, rails are placed to protect people using the premises.
According to most of the building standards, railings are generally required where there is a drop of 30" or more. There are many types of guard railings in a building, and are mandatory per the building codes in many circumstances. Railings along stairways are common, and balconies are also lined with them. The most common residential balustrade is usually a wood railing around the deck. However, nowadays glass is becoming more and more integral component of any modern day building.
As a result, glass balustrades open the view while still providing safety, as at the Grand Canyon Skywalk in USA. Depending on the support conditions, glass may act only as an infill material or as a structural component. Whenever glass acts as a structural component, it becomes necessary for the engineer to ensure a reasonably high degree of redundancy in the design. Fig 1(a),(b) & (c) illustrate common types of balustrades where glass is acting as a structural component for sustaining the imposed lateral loads [1].
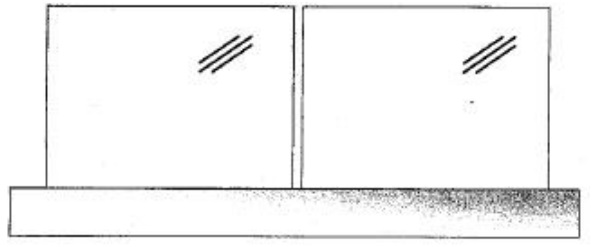
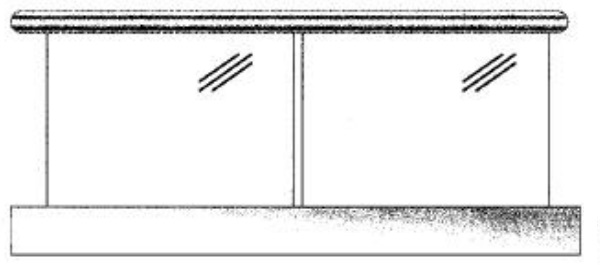
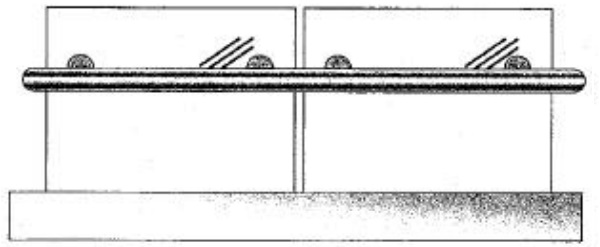
Global Standards on Balustrades
Major countries like USA, UK, Australia, Germany and EU have their relevant standards for design of balustrades. Others follow the criteria laid down by these countries or have their standards derived from them. All of these standards specify a minimum lateral imposed load that should be sustained by a balustrade and the desired performance when it is subjected to impact loads.
ASTM - E2353 – 06
The standard requires shot bag test, pendulum test, horizontal and vertical static load tests for the balustrades. The performance of the panel under impact is classified as follows:
(i) Unbroken
(ii) Broken & retained
(iii) Broken & not retained
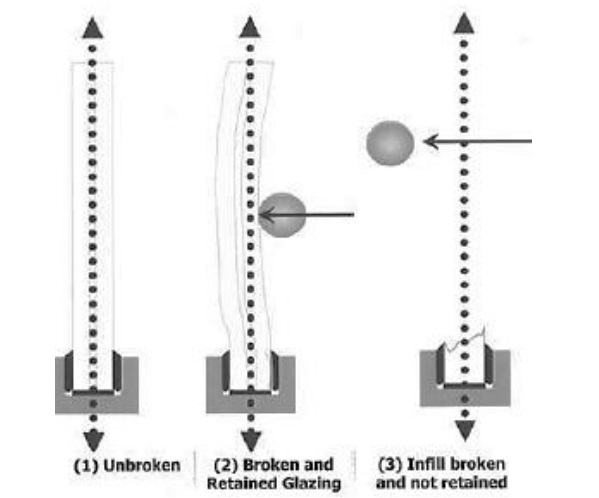
The standard requires broken glass to be strong enough not to allow a spherical steel ball of diameter 75 mm when pushed with a force of 18 N.
AS 1288 – 2006
The Australian standard permits cantilevered balustrades that have an interlinking hand rail. The handrail is non-load-supporting, unless a panel breakage occurs, and is connected to adjacent panels of glass, or the building, where the adjacent panels are at least 1000 mm wide and three or more panels of glass form the balustrade. If any one panel fails, then the remaining panels and handrail are required to be capable of resisting the design load [2].
Building authorities in Australia permit “free standing” balustrades (without interlinking hand rails) only on a project by project basis, through an “Alternate Solution” per Building Code of Australia(BCA)-2015. As per BCA 2016, the same is known as “Performance Solutions” that involves rigorous assessment methods[3]. Singapore too, has a similar regulation that bars “free standing” balustrades.
German TRAV Guideline – 2003
Germany has its TRAV Guideline for Balustrades.So far it does not allow cantilevered balustrades, or only with a structural top-railing cap.For balustrades without top-cap a project specific approval and test scenario is required. Similar to Australia, the approval criteria depends on the project and local authority involved (could differ from one state to another).
BS 6180 – 2011
Depending on the type of occupancy of the building, the British Standard has requirements of sustaining below design loads for barriers
1. Uniform distributed loads of 0.5KN/m2, 1.0 KN/m2 & 1.5 KN/m2
2. Linear live loads of 0.36 KN/m, 0.74 KN/m, 1.5 KN/m & 3.0 KN/m
3. Concentrated Live Loads of 0.25KN, 0.5 KN & 1.5 KN
Additionally, the standard requires the glass to be Class A safety glass. However, there are no criteria for post breakage strength [4].
The review of the above important standards & building regulations conclude that Australia & Singapore in particular have a critical approach towards free standing balustrades without any interlinking hand rail. The approach highlights the concern of the authorities for human safety. Clearly, the intent of authorities is to ensure the highest safety level in post glass breakage scenario.
Post Breakage Strength Test for Laminated glass
Does glass has a strength after it has broken? It all depends on what type of glass and interlayer has been chosen for laminate construction and its boundary conditions. A tempered glass laminate construction with PVB interlayers in a balustrade application may have the desired structural strength but has poor post breakage strength depicted by “blanket effect”.
This justifies the safety concerns of Building authorities in Australia & Singapore. Ionomer interlayers, rightly address this problem by not only enhancing the stiffness of the glass laminate construction but bring in additional benefits of a very high edge stability compared to standard PVB.
Singapore building authorities look forward to elevating the balustrade safety standards by requiring the broken laminate construction, to resist the design live loads within a safe deflection limit of maximum 150 mm when a design load of 1.5 KN/m is applied with all glass layers broken. Clearly, no parallel can be drawn to such a high performance standard of glass balustrade.
In 2015, Kuraray attempted a post breakage strength test on a balustrade having a 2 x 12mm Tempered Glass laminated with 2.28 mm Ionomer Interlayer. The test was conducted at an ambient temperature of 33°C, at TUV Singapore. In the test, the broken tempered laminate construction provided sufficient post breakage strength against a “collapse”. However, the broken glass construction was not strong enough to meet the Building Construction Authority (BCA) of Singapore’s requirements as the top edge deflections far exceeded 150 mm when 1.5 KN/m linear load was applied at the top edge.
Although, this test was a failure, it provided two key learnings – 1. Tempered glass laminate does not have the required post breakage strength. 2. The base of the balustrade need to be made perfectly rigid to mitigate the base mobility issues observed in the built up U Channel base holding the glass panel In 2016, Kuraray & Q Railings together, ventured out to develop a solution that meets the intents of not only the architects but the building authorities (BCA) as well in Singapore. The same test was repeated at an in house testing lab of Q Railings at Mumbai in India, which concluded that Ionomer interlayers with heat strengthened laminated glass constructions can achieve a very high structural strength capable of safely resisting the design loads in post breakage condition too.
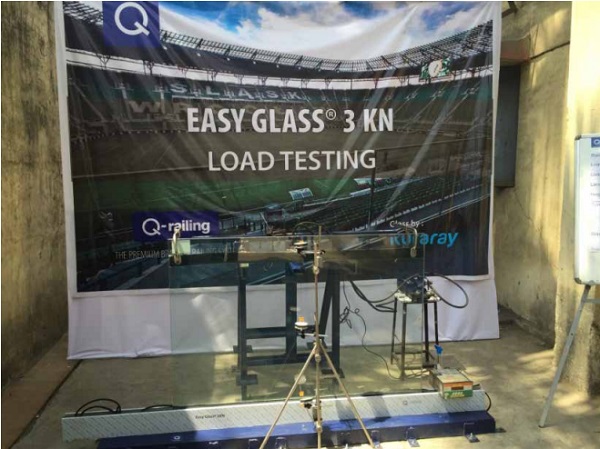
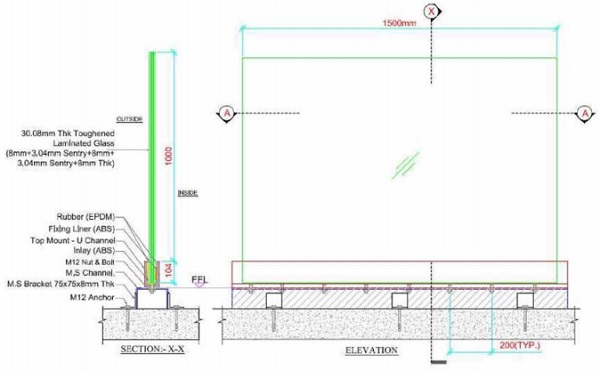
The U Channel base with Acrylonitrile Butadiene Styrene (ABS) Fixing Liner ensured a perfectly rigid base to the balustrade. The glass construction was also changed to a triple laminate construction made with heat strengthened glass instead of tempered glass, with a hope that the middle glass layer “interlocked” between outer glass layers would improve the post breakage strength.
Laminated Glass Construction Details –
8mm Heat Strengthened + 3.04 mm Ionomer Interlayer + 8mm Heat Strengthened + 3.04 mm Ionomer Interlayer + 8mm Heat Strengthened
Test Methodology
The glass panel was applied horizontal linear loads with hydraulic jack and load cell arrangements as shown in Fig 5. The entire test was conducted in an uncontrolled temperature (33-35°C) environment.
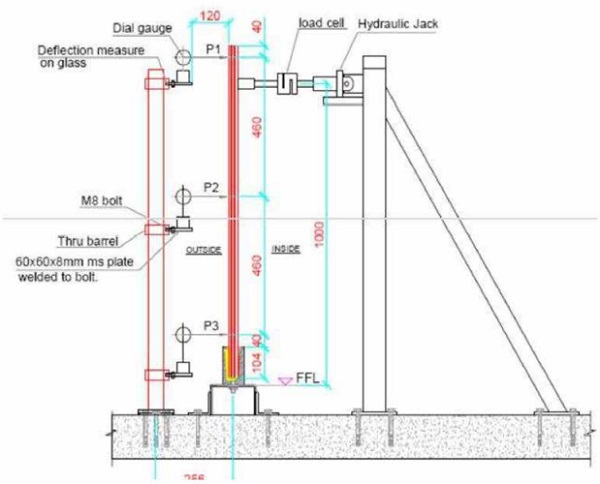
To ensure a linear load distribution, the load was applied at two locations at the top edge. The dial gauges for measuring the panel deflection at the top, centre and at the top of the rigid support were used. The load was gradually ramped up from zero to 1.5 KN/m. One specimen (Number 2) out of three had an unexpected breakage at 1.5 KN/m. Deflections were recorded for 1.5 KN/m and 3.0 KN/m load. The load was gradually ramped up to ultimate load capacity of the panel. Post to the breakage of glass, a linear of 1.5 KN/m was applied and deflections recorded after one minute. The test results are tabulated below.
Specimen #2 had an unexpected breakage, probably due to less surface compression stress. The deflections in the Specimens # 1 & 2 in pre breakage conditions for 1.5 KN/m were bit on the higher side because a full rigidity of the bottom edge could not be achieved for the non-standard glass thickness with combination of two different standard ABS wedges. For Specimen # 3, the base stiffness was enhanced by Q Railings, using slightly thicker ABS wedges which resulted in significant reduction in top edge deflections of the panel in pre and post breakage condition [5].
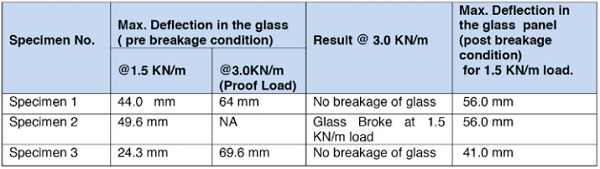
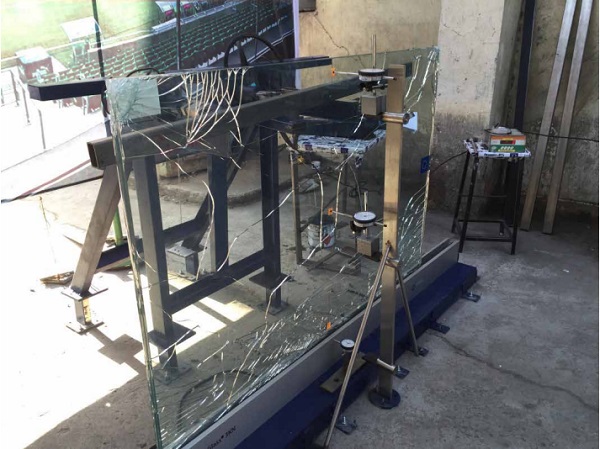
Conclusions
1. Advanced Structural Interlayers like Ionomers, when used in a triple layer heat strengthened glass laminate construction, significantly enhance the structural integrity of the glass balustrades to resist the design loads in post breakage condition as well, thus meeting the most stringent safety norms laid down by countries like Singapore & Australia.
2. The test was done only for laminates made with Ionomer Interlayer. PVB Laminates although not tested but have little or no chance to pass the post breakage performance requirement achieved in the test because shear modulus value for PVB is almost one hundredth of the value for Ionomer.
Future Testing
Stiff PVB has a shear modulus comparable to Ionomer interlayers up to a temperature of 30°C. Future tests can be aimed at exploring how Stiff PVB laminates perform in comparison to Ionomer interlayers.
Acknowledgements
The authors would like to extend a special thanks to Mr. Vijay Sawant, Head (Technical) of Q Railings India Pvt. Ltd. and his team for their support in conducting the post breakage strength test at their facility.
References
[1] ASTM E 2353 - Performance of Glass in Permanent Glass Railing Systems, Guards, and Balustrades
[2] AS 1288 – 2006 – Glass in Buildings – Selection & installation
[3] Building Code of Australia – 2015, 2016
[4] BS 6180 – 2011 – Barriers in and about Buildings – Code of Practice
[5] Testing of Glass Balustrade System, free standing without cap rail / handrail by Q Railing India for Kuraray India Pvt. Ltd.