Authors: Hong Miao, Chong Li, Qiang He, Shanwen Zhang, Yanjun Zhang and Sixing Liu
Source: Advances in Materials Science and Engineering - Hindawi | https://doi.org/10.1155/2019/2657810
Abstract
To explore the effect of welding speed on the micromorphology and mechanical properties of the laser-welded vacuum plate glazing joints, this paper introduced the research status of the laser welding vacuum glazing and then carried out the preparation for experimental materials. This paper also analyzed the microstructure, the cause of the pores, and the mechanical properties of the sealing layer. The results show that the smaller the welding speed is, the more fully the solder melts.
When the welding speed is 80 mm/min, the sealing layer generates the large thermal stress due to excessive laser input energy, which results in many connected cracks in the sealing layer. The porosity of the sealing layer increases with the increase of the welding speed. The thickness of the interface reaction wetting layer decreases with the increase of the welding speed. The hardness, tensile strength, and shear strength of the sealing layer will increase first and then decrease with the increase of welding speed. These studies can provide the theoretical basis for laser sealing manufacturing of vacuum plate glazing.
1. Introduction
Laser welding has the characteristics of high energy density [1], small thermal deformation of welding, and high welding efficiency. So it has wide application prospects and is considered as one of the most advanced welding methods in the 21st century [2, 3]. As a new type of energy-saving transparent insulation material, vacuum plate glazing has the advantages of strong thermal insulation performance, excellent anticondensation, and sound insulation performance and has been applied in the fields of construction, vegetable greenhouse, solar energy application, refrigeration transportation, etc.
In the sealing process, the vacuum plate glazing will produce pores of different degrees inside the sealing layer. The presence of the pores cannot make the microstructure dense, and the sealing quality is good. The pores are less and evenly distributed, and the density and strength of the sealing layer are high. The more or unevenly distributed pores, which tend to cause stress concentration, can reduce the vacuum tightness, mechanical properties, and service life of the plate glazing. Zhao et al. [4] prepared porous metal-bonded cubic boron nitride (CBN) grinding wheel with ideal porosity and excellent mechanical properties and studied its performance.
The experimental results showed that the porous CBN grinding wheel can obtain higher material removal rate and lower surface hardness under the same conditions compared with the vitrified grinding wheel. Miao et al. [5] studied the effect of graphite content on the bonding properties of the abrasive layer and determined the optimum graphite content of 10 wt.%. The porosity of the abrasive layer reached 25% and the bending strength reached 125 MPa, which was beneficial to meet the requirements of high-speed grinding. Miao et al. [6] adopted the vacuum welding to seal the vacuum glazing from the side and executed the experiments using different sealing temperatures.
The impact of different sealing temperatures on the microstructure of the sealing layer was analyzed to evaluate the combination of material science features on the interface and to reveal the influence of the sealing temperature on the hardness and residual stress of the sealing layer. In 2018, Kim and Jeon [7] used the hydrogen-mixed gas torch in the cross-sectional shape satisfying the strength performance of the sealing parts. This is because the edges of vacuum glazing panels sealed using a hydrogen-mixed gas torch were various shapes, which affected the strength of vacuum glazing. In 2018, Zhang et al. [8] researched the influence laser power and welding rate on sealing edge porosity. The results showed that the interface layer is compact and smooth, and the pores decline in numbers with the increase of laser power. When the power exceeds a certain value, the interface becomes unsmooth with the increasing number of pores.
This paper will carry out in-depth analysis on the pore defects of vacuum plate glazing laser welding, study the influence of the welding speed on the micromorphology and mechanical properties, explain the cause of pores formation from the aspect of porosity, and improve the sealing reliability of the vacuum plate glazing. The aim is to provide a theoretical basis for vacuum plate glazing laser sealing manufacturing.
2. Experimental Materials and Methods
The solder preparation process is as follows: the mixture of ethyl cellulose and terpineol with a mass ratio of 1 : 9 is selected as the flux, then the solder and solvent with a mass ratio of 10 : 1 are mixed, stirred for 30 mins, and then placed for 30 mins to defoam, completing the preparation of the coated solder.
The size of the soda-lime glazing selected for the welding experiment is 50 mm × 50 mm × 4 mm. Before welding, the glazing surface to be welded is polished by the BD46N abrasive belt sanding machine, so that the glazing has a certain roughness.
Taking the HGL-LCY300 Nd : YAG laser welding system as the test platform and laser welding technology as the approach, the effects of welding speed on the melting layer, pore distribution, interface reaction wetting layer, and mechanical properties of vacuum flat glazing are studied. The welding process parameters are optimized to determine the optimal set of process parameters.
3. Effect of Welding Speed on the Joint Microstructure
When the pulse current I is 160 A, the pulse width τ is 2 ms, the pulse frequency f is 18 Hz, and the welding speed is changed, Table 1 shows the welding process parameters.
Table 1 Welding process parameters when changing welding speed. - Full size table
Figure 1 shows the microstructure of the molten layer at different welding speeds [9, 10]. The smaller the welding speed is, the more fully the solder melts. When the welding speed is 80 mm/min, the sealing layer generates the large thermal stress due to excessive laser input energy, which results in many connected cracks in the sealing layer. When the amplification factor is reduced, the internal part zone of the sealing layer is seriously burnt. Increasing the welding speeds to 90 mm/min and 100 mm/min can make the sealing layer smooth and compact. When the welding speed is 110 mm/min, the laser input energy is low, and the molten layer solder is not completely melted [11, 12].
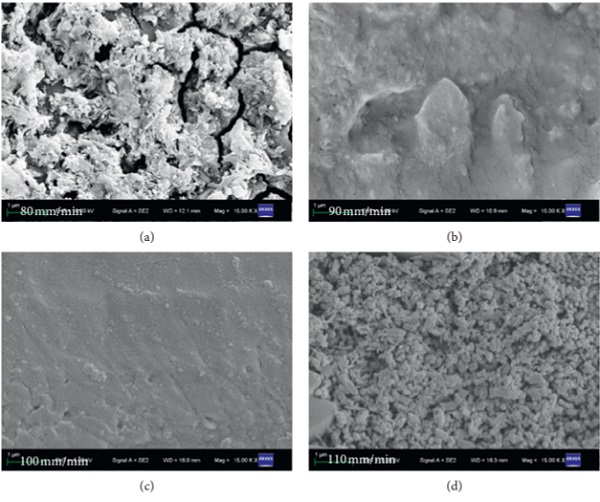
Figure 2 shows the pore distribution and the porosity variation curve of the sealing layer at different welding speeds [13]. Results show that the porosity of the sealing layer increases with the increase of the welding speed. On the one hand, the temperature gradient of the sealing layer increases with the increase of the welding speed, which makes the cooling rate of the molten solder quicken, and the bubbles in the sealing layer solidify before they escape. On the other hand, the increase of welding speed makes the melt viscosity increase, which will hinder the escape of the pores [14]. When the welding speed is 80 mm/min, the porosity is the least, only 0.02%. When the welding speed is 90 mm/min, the pores are less and small. When the welding speed is 100 mm/min and 110 mm/min, respectively, the number of pores is increasing, and the porosity is 0.63% and 0.89%, respectively.
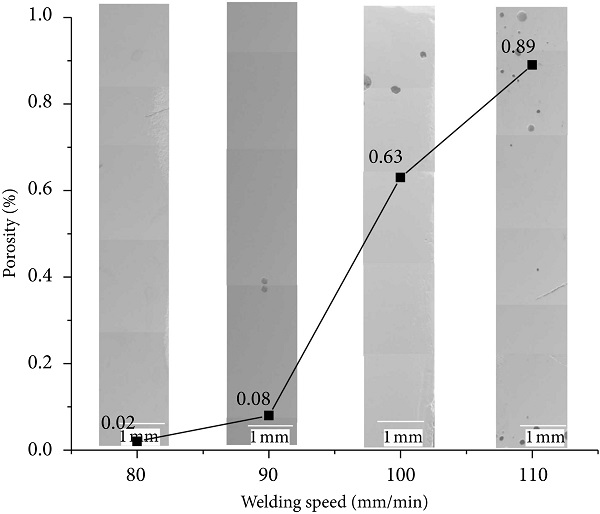
Figure 3 shows the location of the EDS line scanning test, the scanning location is a line composed of 100 fixed points from A to C. Among them, A, B, and C represent the glazing matrix, interface reaction wetting layer, and melting layer, respectively.
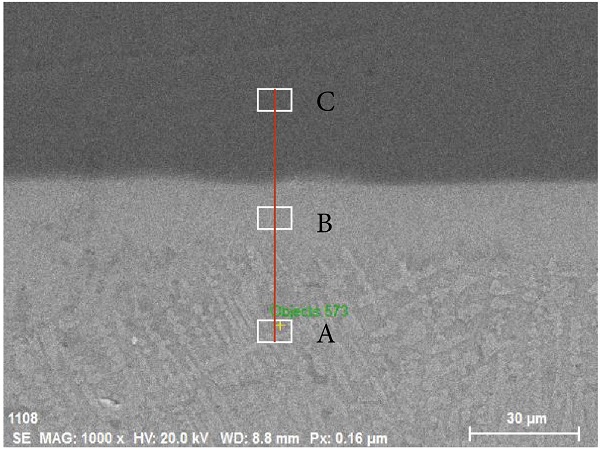
Figure 4 shows the results of the line scan of the joint interface at different welding speeds. Among them, the left side of the interface reaction wetting layer represents the glass matrix and the right side represents the melting layer. Results show that with the increase of the welding speed, the thickness of the interface reaction wetting layer decreases, but the migration rate of Si in the interface reactive wetting layer accelerates. This is because the action time of the heat source becomes shorter with the increase of welding speed, which makes the temperature reduce, and the solder starts to solidify without melting, resulting in poor wettability between the solder and the glazing, so the thickness of the interface reaction wetting layer decreases.
In addition, the migration rate of Si in the interface reactive wetting layer increases with the increase in welding speed. This is because the compounds between Pb-Ti-O, Pb-O, Si-O, and Al-Si-O are formed in the interface reaction wetting layer, mainly in the presence of the PbTiO3 phase. New chemical bonds formed by new substances can improve the bonding performance between glazing and the solder at the interface. At the same time, when the line scanning reaches the point of 70, the thermal reaction becomes weaker, the migration rate of all elements does not change obviously, and the signal intensity of elements tends to be constant.
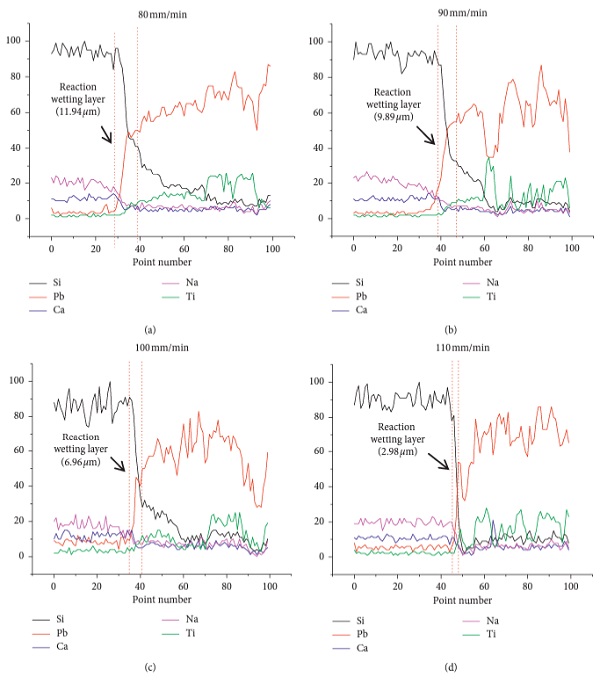
4. The Effect of Welding Speed on the Mechanical Properties of the Sealing Layer
Table 2 shows the hardness, tensile strength, and shear strength values of the sealing layer at different welding speeds [15]. Results show that the hardness, tensile strength, and shear strength of the sealing layer will increase first and then decrease with the increase of welding speed. When the welding speed is 90 mm/min, the mechanical properties reach the peak value. When the welding speed is 90∼100 mm/min, the sealing layer spreads better, and the molten layer is dense, so its mechanical properties are relatively high. When the welding speed is 80 mm/min, there are large cracks in the sealing layer, which will aggravate its fracture tendency, so the tensile strength and shear strength will be very low. When the welding speed is 110 mm/min, there is a lot of unmelted powder in the sealing layer, and the bonding effect between particles is poor, so the mechanical properties of the sealing layer decrease when the welding speed is increased.
Table 2. Hardness, tensile strength, and shear strength values of the sealing layer at different welding speeds. - Full size table
Through the analysis of the aforementioned test data, it is found that when the welding speed v is 90 mm/min, the morphology of the molten layer is better, the porosity of the sealing layer is lower, the thickness of the interface reaction wetting layer is larger, the mechanical properties are better, and the welding quality is better. Therefore, when the pulse current I is 160 A, the pulse width τ is 2 ms, the pulse frequency f is 18 Hz, and the welding speed is 90 mm/min, the quality of the sealing layer is the best, which can be selected as an optimal set of process parameters.
5. Conclusions
The paper first introduces the research status of the laser welding vacuum glazing, then introduces the experimental materials and methods of laser sealing vacuum plate glazing, and finally studies the effect of welding speed on micromorphology and mechanical properties of laser-sealed vacuum flat glazing joints. The experimental results are as follows:(1)There are three basic interactions between laser and glazing: reflection, absorption, and transmission. Most of the light through the upper layer of glazing is absorbed by the middle solder and converted into heat energy, melting the solder powder surface locally.(2)The smaller the welding speed is, the more fully the solder melts.
When the welding speed is 80 mm/min, the sealing layer generates a large thermal stress due to excessive laser input energy, which results in many connected cracks in the sealing layer.(3)The porosity of the sealing layer increases with the increase of the welding speed.(4)When the welding speed is 80 mm/min, the porosity is the least, only 0.02%. When the welding speed is 90 mm/min, the pores are less and small. When the welding speed is 100 mm/min and 110 mm/min, respectively, the number of pores is increasing, and the porosity is 0.63% and 0.89%, respectively.(5)The hardness, tensile strength, and shear strength of the sealing layer will increase first and then decrease with the increase of welding speed.
Conflicts of Interest
The authors declare that they have no conflicts of interest.
Acknowledgments
This study is supported by the National Natural Science Foundation of China (grant no. 51672241), the 14th Batch High-level Talents Project for “Six Talents Peak” (grant no. XCL-092), the Natural Science Foundation of Jiangsu Province (grant no. BK20170500), the Natural Science Foundation of the Jiangsu Higher Education Institutions of China (grant no. 18KJB460032), “Green Yang Jin Feng Program” leading talent support project in 2018, the Jiangsu Science and Technology Plan Project of China (grant no. BE2016134), the Province Postdoctoral Foundation of Jiangsu (grant no. 1501164B), the Technical Innovation Nurturing Foundation of Yangzhou University (grant nos. 2017CXJ024 and 2017CXJ021), and the China Postdoctoral Science Foundation (grant no. 2016M600447).