Im Vogelsang 18
Waidhofen/Ybbs 3340
Austria
Softsolution GmbH
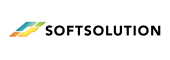
Find us on:
WHERE ULTIMATE INSPECTION TECHNOLOGY IS BORN
Softsolution - LiteSentry, are pleased to announce a new partnership to support both companies’ long-term growth and success. Softsolution - LiteSentry enhance their ability to respond to customer needs with more localized resources, improve end users’ access to new technology, and accelerate new product development.
At the locations in Austria and in the USA, the two partners score in the installation, service and support segments with higher availability, fast response times and short distances to the customer.
Both Softsolution and LiteSentry have products with a wide range of applications in quality fields of application in quality assurance.
Today, more than 3080 systems combined are in use worldwide. A large network of partners makes our products available on all continents.
Learn more at: https://www.glassquality.com
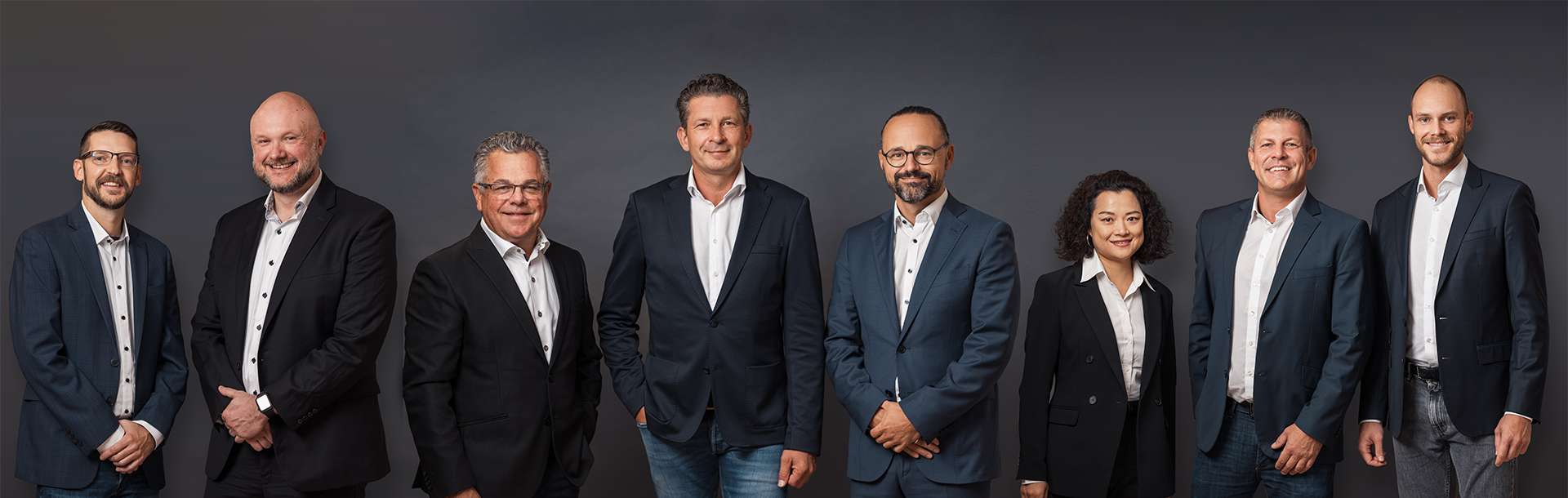
SALES AND SERVICE OFFICE Softsolution GmbH tel.: +43 7442 53988 ----- |
|
|
SALES AND SERVICE OFFICE LiteSentry™ LLC |
||
Products
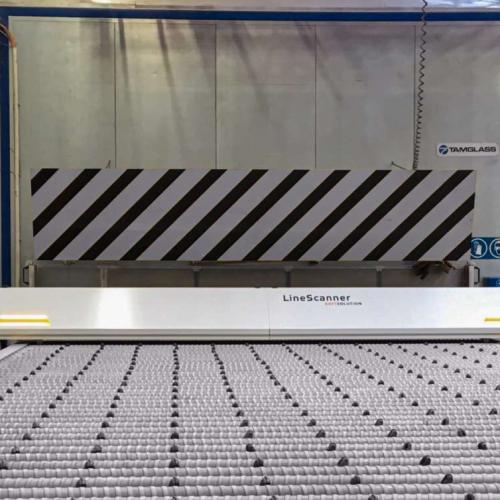
The LineScanner is the solution for all quality inspections of transparent flat glass products such as single sheets, insulating glass, automotive glass, processed glass, polycarbonate or film. LineScanner inspects your products with extreme precision for all defects in quality and dimension. Its flexibility as well as its simple operation and installation allow it to be put into operation quickly and easily with minimum space requirements.
- 90° telecentric light technology
- engineered for vertical and horizontal installation to fit any production line
- quality, dimension, anisotropy
- all kinds — float, heat-treated, laminated, IG unit
- AI technology included
- easy and transparent monitor display
- archive database, certificates
- smallest footprint ever
The LineScanner can handle any challenge, no matter how unique.
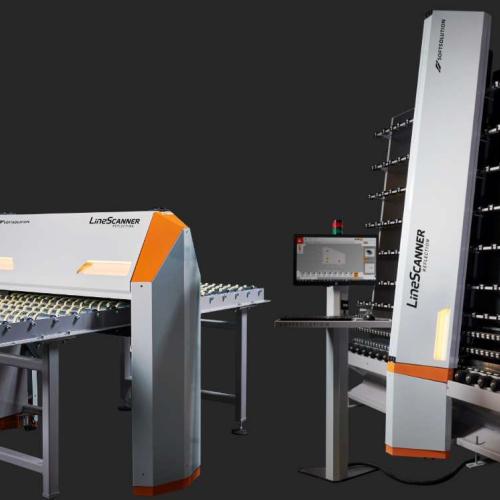
Making white haze visible is the key to reliable and stable detection.
There is one method where this defect becomes so visible and that method is reflection. Softsolution developed a unique hardware configuration using reflection-based scanning technology. Every image is interpreted by an AI-based algorithm. The system and software were developed in cooperation with highly experienced people from the tempering industry.
A critical defect that is difficult to see with the human eye can now be easily made visible.
- white haze detection in different levels
- unique reflection-based scanning
- AI-based software algorithm
- invented and developed in cooperation with Glaston
- smallest footprint ever
The CulletScanner from Softsolution with new tilt function scans with the highest resolution every tempered glass, such as architectural-, automotive-, window glasses and shower doors and eg. Each fragment is viewed from a 90° angle and the entire fragmentation image of a test lite is precisely and completely evaluated within seconds.
The position, size, length, area and weight are determined and each scan of a fragmentation image is digitally stored with the highest precision and sharpness.
- automatic break pattern analysis
- only system which checks the entire part
- automatically finds worst areas
- prevents operator errors
- 3 sizes available
- several norms available
- certificates and digital images
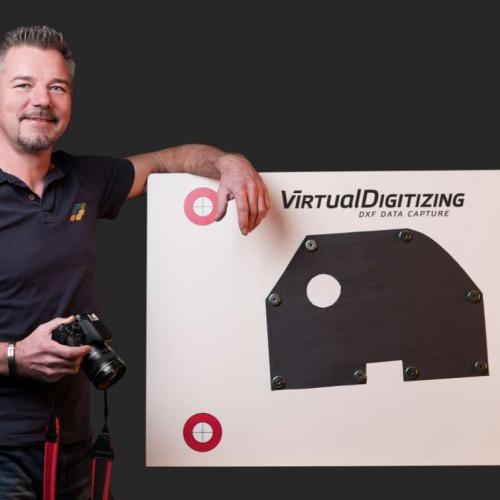
VirtualDigitizing – a software application for flexible digitization solutions for templates that can be used easily and quickly in any industry. This results in an unprecedented reduction in workload and increased flexibility.
- digitization solution for templates
- automatic conversion to DXF format
- spline optimization
- auto corner tool
- safe time and money by getting the template
- right the first time – everytime
VirtualDigitizing – will change the way you work.
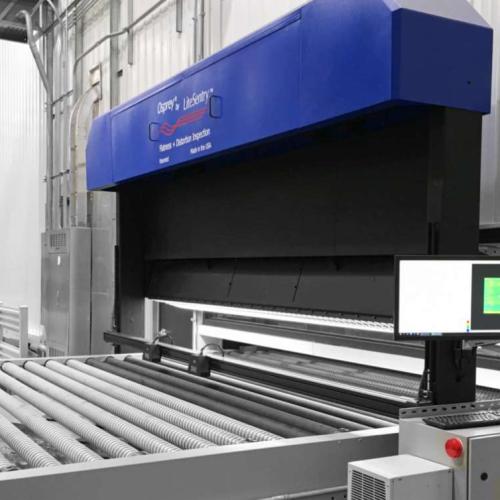
anisotropy and overall bending.
LiteSentry’s revolutionary Osprey® 10 advance inspection systems include the only high-performing systems that meet and exceed the growing requirements of leading architects and glass suppliers, including mandated distortion and anisotropy measurements.
- because quality matters
- imperative for lamination products
- not running furnace “blind”
- less dependency on human inspection
- 100 % of the glass aera is checked
Osprey® is designed to improve your bottom line and advance your opportunities with its complete, precise, and accurate inspections.
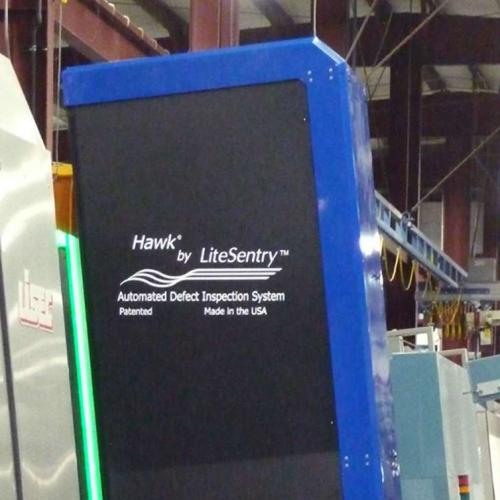
The Hawk® Scratch + Defect Inspection system for IG/Double Glaze fabrication, tempering, and coating lines detects a wide range of scratches, digs, and other defects.
- true brightfield and darkfield inspection
- engineered for vertical and horizontal installation to fit any production line
- modular design of sensors, lights and cameras for ease of maintenance
- detects pinholes, arc marks, edge grind skips and misses, skip scratches and cluster defects
- patented technology differentiates low-E coated glass from non-coated glass and sets unique inspection criteria for each type of glass
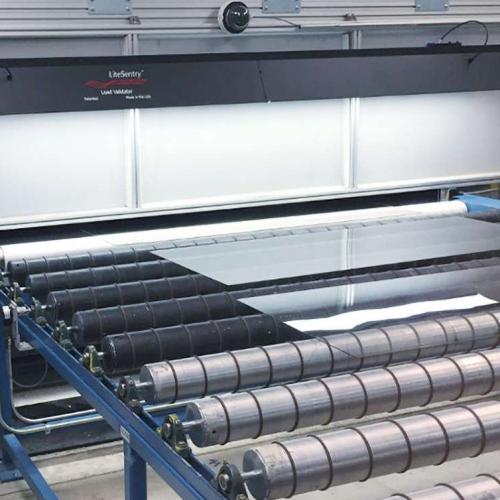
The Load Validator™ provides an accurate, repeatable, consistent measurement of glass size, load size, and critical fault conditions likely to cause glass breakage and line interruptions.
Load Validator technology is available as a stand-alone system or included with the Owl 5.
- ensures correct load geometry
- detects long load, overlapping, broken corner,
- wide load, minimum distance
- non-conforming loads or defective
- glass triggers
- alarms that stop the conveyor system
The Owl 5 transmits data to the furnace control system allowing the furnace to automatically select a recipe and optimize the heat profile, improving cycle time, minimizing distortion, and optimize flatness
Load Validator technology is included in Owl 5 OR as a stand-alone system.
With the Owl 5 Furance Optimization System, you will have your best furnace operator on every shift.
- automatic furnace control
- optimize heat time and other furnace parameters by coating, thickness, glass color, bed utilization and location of parts
- ensures correct load geometry
- glass thickness, color and coating automatically measured
- detects long load, overlapping, broken corner, wide load, minimum distance
- eliminates operator errors
- communicates with an Osprey to confirm all parts in a load are present