This paper was first presented at GPD 2017 by Olavi Uusitalo from Holmark.
Since the mid-1990 flat glass has had two separate products again: high quality float glass and lower quality float glass. The aim of the paper is first to explain how float glass could merge the subindustries and second to analyze the situation of lower quality float glass in the industry.
The modified design envelope model is applied to demonstrate the technological competence and especially strategic thinking concerning to understanding of the markets and positioning the product. The envelope model helps companies building scenarios for responses if new unexpected innovations are introduced. The analysis of lower quality float glass with modified design envelope rise the question: Should there be a lower quality float glass available?
1. Introduction
In the late 1970s the flat glass industry had two separate industries, sheet/window (later on sheet) glass and plate glass. The float glass innovation has its origins from both industries. It aimed to have optical quality of plate glass and “fire-finished” manufacturing method from sheet glass. The R&D process of float glass in Pilkington, that time a UK based family owned company, took seven years.
During it the company made a strategic decision to position float glass as a readymade product in the plate glass industry and not too quickly in between two industries. In the 1960s Pilkington developed the float glass technology, so that float glass could compete also with sheet glass (see Figure 1.).
The aim of the paper is to explain how Pilkington was able to revolutionize the flat glass industry. This involved both high technological competence and also strong strategic thinking concerning to understanding of the markets and positioning the product. I use a modified version the design envelope model (DEM) [2] for analyzing the emergence of float glass innovation and to demonstrate the reasons beyond the revolutionary change in the flat glass industry. The DEM is also applied in the analysis of lower quality float glass. The study applies a longitudinal and contextual approach with the use of a multiple case study method.
The rest of the paper has three parts. First, the DEM is presented. Second, the emergency of float glass as the dominant design is illustrated by applying the modified DEM. This includes also illustration to the Chinese lower quality float glass. Third, conclusion and managerial implications are given.
![Figure 1. Flat Glass Production in the U.S., 1964-1980 (Millions of Sq. Ft.) [1].](/sites/default/files/inline-images/Fig1_82.jpg)
2. The Design Envelope Model (DEM)
A technological innovation, which later may be thought of as the capture of design dominance (DD), depends heavily on the degree to which market structure and market needs are understood [2]. To link the market structure and technological deployment decisions, a DEM is proposed for analyzing the complex closed or open systems. Based on the analysis of float glass innovation I draw conclusions from positioning of it. [2] Positioning is a matter of corporate strategy not sales tactics [3].
The purpose of the authors is threefold: first, to develop a comprehensive business strategy according to which the top managers needs an intimate understanding of product class evolution (especially the emergency of DDs), i.e. technology as an outcome of community dynamics (variation, selection and retention), second, to offer a perspective suggesting that emergencies of DDs may be explained in terms of ‘lumpiness’ of markets which have finite and limited customer bases and, third, to identify the mechanisms through which executive teams shape technology strategy, and to identify the processes which affect the scope, direction and quality of technology strategy decisions. [2]
The focus is primarily on systemic technologies, because these more complex technologies are influenced much more heavily by social, organizational, and political processes. Since it is the rare technology, which clearly dominates across all possible dimensions of merit, a process of compromise and accommodation between suppliers, vendors, customers, and government becomes important in adjudicating among feasible options. The achievement of a DD can thus be seen to be driven by the strategic decisions made by organizations interacting with other organizations and with practioner communities. [2].
Technological merit is crucial. A difficulty with this concept of technological evolution is that the DD can only be identified ex post, and at an industry level. How a DD can be created in an industry for a firm? It might be useful to develop a framework for thinking about the drivers of DD in complex, interdependent systems. This requires a more specific definition of DD, which both captures the industry level ex post construct but also allows strategist ex ante, and through the linkage between the firm’s technology strategy and the way it wishes to attack its markets [2]
The two-dimensional model (bases on two product attributes) is in Figure 2. The edges of the ‘design envelope’ are defined by the current limits of technology. Designs are constrained by a multiplicity of technological barriers, in much the same way as linear program solution is held within a multidimensional envelope of constraints. The edges are defined as Barrier 1, Barrier 2 and Barrier 3. [2].
Customers make trade-offs between attributes depending on the price charged for it. In virtually all real markets, uneven concentrations of customers clustered around different attribute preferences create disparate sub-populations who each make their own trade-offs in product attribute space. These unevenly concentrated groups of customers are defined as lumps or ‘market knolls’. For instance, group A (or market knoll A) may require only attribute 1, while group C prefers attribute 2. For group B both attributes are equally stressed. At a given price level, each group would have its own isoprice line (Figure 2), which suggests that at the given price, the group A would buy any design to the north and east of line A and so on. [2].
The area north and east of lines A, B and C are the knolls. Standard marketing treatments divide the market into niches and each knoll is being handled separately. In the light of the potential for very rapid and substantial changes in technology, however, firms usually focus exclusively on developing niche products that serve only one of the knolls (a product at a price in points X for group A, Y for B and Z for C). However, companies could use technology to design products at points U, V and W in which case each of the niche players will find their products obsolete on their niche attributes, while at the same time the new entrants reaps the benefits of a larger market size than any of the niche players with now obsolete designs.
As new designs advances north and east in an attribute space, the number of sub-populations that are attributed by that design increases. This means that there might emerge a design that captures all the market knolls lying to the south and west of the design. This highlights the specific conditions that determine the viability of a niche, as well as its fragility. ‘It is only for as long as technological barriers confine designs within specific market knolls that these knolls can be thought of as niches. Since technology advances can create a design that lies to the north and east of whole groups of niches, niches are strictly tactical in the long run’. [2].
A revised definition of DD captures the strategic problem of attempting to develop such a design ex ante and at firm level. “A DD in any market knoll is that design that lies the most northeast in that knoll’s product attribute space.” Executive teams should shape technology strategy as follows: “Executive teams must put in place the processes that will drive technology development in the appropriate directions, so that the firm can navigate from its current design to a future design that gives the maximum increase in market access per unit development cost.” [2].
The challenge of executive teams is to help establish key dimensions of merit both by managing environmental relations and by managing intraorganizational dynamics to produce a system that dominates in the targeted product space. The more complex the product is, the more complex the intra- and extraorganizational strategic and managerial challenges are. Their definition of the concept of DD lets them to contribute in two ways: first, to develop a more precise understanding of the factors that lead one particular design to dominate another, and second, to begin to think through the strategic implications of managing technological investments to capture DD. [2].
![Figure 2. Combined Effects of Market ‘Lumps’ and Technology [2]](/sites/default/files/inline-images/Fig2_87.jpg)
4. The Flat Glass Industry and the Float Glass Innovation
In the 1940s (and as late as 1975) the flat glass industry had two separate industries: the sheet glass and plate glass industries. Sheet glass was subject to inhomogeneities and sheep while plate glass was free of optical distortions and expensive. Float glass was launched in 1959 and it changed the whole flat glass industry globally. [4] Later on China and its float glass technology took a large share in the world market [5].
4.1. Flat Glass Manufacturing in 1930-1960
To make plate, molten glass was rolled into a plate and then ground and polished both surfaces were smooth and parallel. The process was noisy and created a lot of dirty. Plate glass was used in more sophisticated applications such as mirrors and the large windows used for retail displays and architectural effects, where the inhomogeneities and optical distortion were not acceptable.
The plate glass industry was characterized by high quality and high price products. Sheet glass was drawn into a ribbon through a block floating on the surface of the molten glass. The ribbon passed vertically upward through an asbestos roller and then into a cutting room where the cooled, hardened glass was cut and stacked. It was suitable for ordinary windows used in construction. [4].
In Figure 3 the plate glass and sheet glass industries are illustrated in a modified DEM. The X-axis is the unit price (descending) and the Y-axis is the optical quality of glass. I call my model a modified version since the price is on the X-axis. Thus, I do not have isoprice lines as the original model has [2]. On the other hand, unit price could be seen as an attainable attribute due to the technology. These attributes are offered to the customers, i.e. the glass producers, with certain costs of acquisition (comparable to isopricelines) [4].
The plate glass line (solid) in Figure 3 tells that customers preferred high quality products and as cheap as possible, i.e. customers were above the plate line (this refers to a market knoll). The plate glass industry in the early 1930s was located on the left upper corner, Area 1, since a technology barrier, ‘Fire Finished’ Barrier (i.e. the need of grinding and polishing) was the constraint for the cost (price) reduction of plate glass. There was no technology barrier for quality of plate glass, since quality depended on the amount of grinding and polishing.
The drawing processes allowed producing 2-12 mm thick flat glass. The customers valued cheap products and as high quality as possible, i.e. customers were right and above the sheet line. Sheet glass was `fire-finished’ (i.e. no processing after cooling) and thus beyond the ‘Fire-Finished’ Barrier for plate glass.
The quality of sheet glass was, however, constraint by another technology barrier, Stretching Barrier (i.e. if a glass ribbon is drawn from molten glass without any continuous support the ribbon has optical distortion). Since sheet glass has partly manual control the Process Control / Scale Barrier limited for the cost reduction. The sheet glass industry by 1950 was in Area 2 in Figure 3. [4].
The industries targeted different customers and were quite different. The plate glass industry was much more concentrated because of high investment requirements and large production capacities. Large flat glass companies produced both sheet glass and plate glass. However, the companies although they developed technologies in both industries kept the products and their applications separate.
They also started safety glass production in the 1920s. Since then the car industry was the main customer for plate glass. In 1935 Pilkington introduced a `twin’ grinding to grind both sides of a plate glass ribbon at the same time. This lowered the cost of plate glass [6]. The company licensed twin grinding technology (referred to as the I licensing in Figure 4) to the plate glass producers [6]. The plate glass industry moved to Area 3. [4]
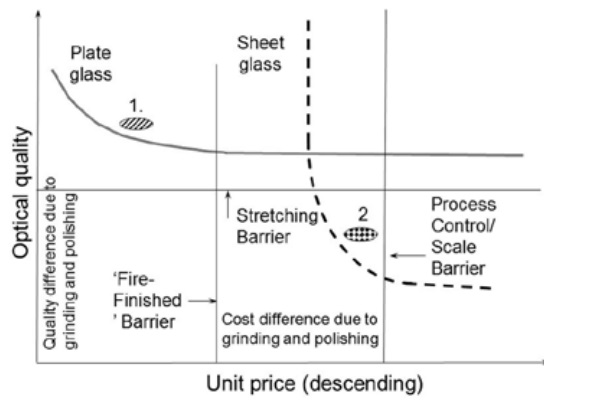
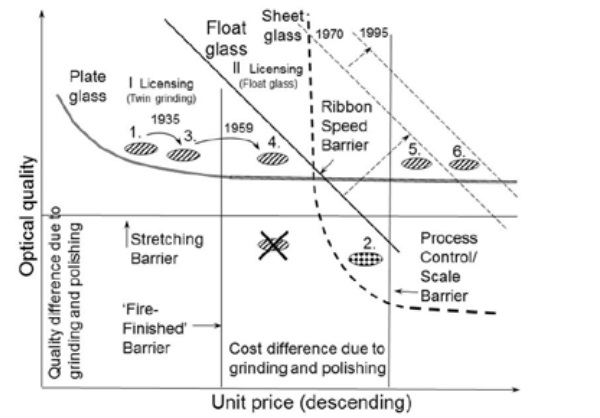
4.2. Float Glass Innovation
The float glass development started in 1952. Two years later Pilkington decided to launch float glass only if it could replace plate glass (not on Area crossed). The cost of float, if successful, estimated to be closer to those of sheet glass than those of plate glass. In 1959 the process was launched. Float glass is “fire finished” having no grinding and polishing phases.
Its quality is equal to that of plate, but the investment and production costs were much less than those of plate glass. First the only possible thickness was 6.5 mm, luckily suitable for side panes in cars. Pilkington moved over the ‘Fire Finished’ Barrier to Area 4. Float glass was above the Stretching Barrier since the molten tin gave continuous support to floating glass.
There was, however, a new barrier, the Ribbon Speed Barrier, which prevented manufacturing of thinner float glass and thus, prevented float glass entering the laminated windscreens and the sheet glass industry. Pilkington by licensing float glass technology (II licensing) inside the plate glass industry let the whole industry to move to Area 4. Pilkington worked also with the further development of float glass and it could move the Ribbon Speed Barrier further north east. [4]. In 1970 Pilkington produced 2 mm thick float glass.
Float glass started to compete with sheet glass. Ultimately float glass went beyond the Process Control / Scale Barrier (Area 5) of sheet glass. In the mid-1970s float glass took over sheet glass. As Pilkington positioned float glass clearly in the high cost plate industry, and not in between two subindustries, it was able concentrate on one ‘market knoll’ with prevailing technological competence. Sheet glass was not challenged before float glass was cost-effective enough to replace the existing technology. The US situation (Figure 1) illustrates well, how float glass made these two subindustries obsolete one by one. By 1995 large scale operation had decreased the manufacturing cost of float glass and it moved to Area 6. [4].
4.3. China’s float glass
In the 1960s the Chinese scientific and technical workers began to study float glass process. In 1971 the first industrialized test line for float glass production was built in Luoyang. In 1981 the process was named “China Luoyang Float Process”. Since then China float process has been third process among Pilkington and PPG processes. In the 1990s the development focused the capacity.
The progress from 90t/d to 700 t/d. By 2006 the capacity reached 900 t/d with glass ribbon width up to 5.2 meters. Since then China has been one of the few countries in the world capable to build super tonnage float glass lines. In 1980s China established float glass quality standard. The quality of float glass made by the China float glass technology has increased with better equipment and raw material.
This has narrowed the gap with the international advanced level greatly. The super grade product meets the needs of automotive glass, mirror glass and other fabricated glass. The national standard is the lowest quality target. More and more companies have taken as their objective to satisfy the market demands on high quality flat glass products. [5].
In 2002 the global flat glass market was about 35 million tons of which 22, and 7 million tons were high quality float glass and lower quality float glass produced mainly in China, respectively [7]. Two years later the numbers were 38 (flat glass), 23 and 10 million tons, respectively [8]. In 2009 the numbers were 52 (flat glass) 29 and 19 million tons, respectively [9].
Although the Chinese government tries to eliminate the lower quality float glass capacity and tighten the capacity expansion, these policies have execution risks [10]. The fluctuating oil price in was the main cause for the difficulties facing the Vietnamese flat glass industry in 2008-2009. Moreover, the increase in imports of flat glass, a decrease in domestic demand due to the global economic crisis and commercial fraud (low-quality float glass sold with labels of high-quality products) contributed to the injury to the domestic industry [11].
Basically, Chinese float glass was lower quality at global scale depending on the supplier. There were clear category difference with leading companies like CSG (China Southern Glass), Xinyi and Jinjiang. There were differences in the basic technologies and how did companies monitor the process. Costs were reduced by using low cost of materials, low cost labor, local incentives from local administration to employ more people. In quality sense for instance the nominal thickness could have 15-20 % difference. Lower quality float glass was/is used by customer segments with home appliances, furniture etc. products. Whether lower quality float glass will disappear is a question of the cost difference and investments. [12]
Based on the previous information I can place the lower quality float glass on the modified DEM (Area 7 in Figure 5). There are again two types of glass as in the 1950s, but for how long. It seems that every Chinese manufacturer also like to produce high quality float glass [5].
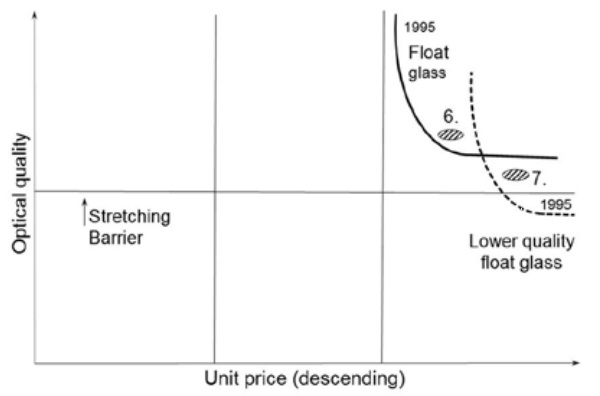
5. Conclusion
The ultimate goal of float glass was based on the combination of the attributes of products of two separate industries, the sheet glass and plate glass industries. Pilkington positioned float glass clearly in the high cost plate industry and not in between the sheet glass and plate glass industries. This left no chance for creative imitators [13].
Had Pilkington introduced float glass as a semi-finished product in between sheet glass and plate glass it would have been difficult for them to persuade plate glass users to buy lower quality and sheet glass users to pay higher price. More over there would have been a risk that another company, a creative imitator, would have taken (by further development) float glass to the plate glass industry. With careful licensing policy Pilkington managed the interorganisational dynamics world-wide. The great differences between plate glass and sheet glass justified the merge of the two industries.
In China there has been / is problems with the quality as we saw above. This situation has created confusion in the industry. On the one hand, large established manufacturers seem to devalue lower quality float glass, but on the other hand, the Vietnam case showed that some manufacturers try or have tried to cheat with lower quality float glass.
However, it seems that every firm in the industry aims to produce high quality glass. Flat glass will / has become a commodity without any room for differentiation, segmenting and thus different prices. Savaëte calls this a mistake the flat glass industry has done [14].
It seems that while flat glass being a commodity the service is the only way to differentiate in the flat glass market. Should it be so? There are several types of float glass: tinted, self-cleaning, extra clear etc. for special purposes. The float glass manufacturing process seems to be well understood and managed. It should not be difficult on purpose manufacture lower quality float glass on lower cost (and thus on lower selling price) for less demanding applications. Luoyang Glass is in a sense advocating this [15].
As we saw, before float glass there were two types, plate and sheet, of flat glass for different applications. All big manufacturers produced both types of glass and kept reasonable well the industries separate. Could it be possible in the float glass era? Last April I visited my friend’s elegant villa on the lake and built by 1960. It was both cool and nostalgic to see 2 * 2 meter2 windows made by Lahti Glassworks’ Fourcault machines. Naturally the optical quality difference between high quality and low quality float glass is much less than that of plate glass and sheet glass.
Generally speaking, if a technology to be used in manufacturing a simple product (the manufacturing process san be the most sophisticated one just as the case of float glass) occupies a position of dominant design there is a risk of the product becoming a commodity which means that there is only one universal product with the same price for a demanding and nondemanding applications. There is now room for differentiation of product and segmenting the market for charging different prices. In a sense the DEM should be worked in reverse way. This finding is a theoretical contribution for DEM.
References
[1] Edge, K. C. “Section 11, Flat Glass Manufacturing Processes (Update)” in Tooley, F. (ed.) Handbook of Glass Manufacture, 3rd Edition, Volumes I & II, Books for the Glass Industry Division, Ashlee Publishing Co., New York, pp. 714/1-21, 1984
[2] McGrath, R., MacMillan, I. C. and Tushman, L. M. “The Role of Executive Team Actions in Shaping Dominant Designs: Towards the Strategic Shaping of Technological Progress”, Strategic Management Journal, Vol. 13, pp. 137-161, 1992.
[3] Kalafatis, S. P., Tsogas, M.H., and Blankson, C. ”Positioning strategies in business markets”, Journal of Business & Industrial Marketing, Vol. 15 No. 6, pp. 416-437, 2000.
[4] Uusitalo, O. “A Revolutionary Dominant Design - The Float Glass Innovation in the Flat Glass Industry”, dissertation A-108, Helsinki School of Economics, Helsinki, 1995.
[5] Peng, S. “Present Status and Internationalization Prospect of China Float Glass Technology”, Boletin de la Sociedad Española de Cerámica y Vidrio Nota Técnica, 47(2), 117-121, 2008.
[6] Barker, T. C. “The Glassmakers. Pilkington: the Rise of an International Company 1826-1976,” Weidenfeld and Nicholson, London, 1977.
[7] Som, A. “Saint-Gobain: The Expansion Options”, International Journal of Case Method Research & Application, 17(4), 477-487, 2005.
[8] Industry Overview www.hkexnews.hk/listedco/listconews/SEHK/2006/.../EWP111.pdf, 2006 (read 25.4.2017).
[9] Pilkington “Pilkington and the Flat Glass Industry”, 2010.
[10] UOBKayHian, China “Update Glass Sector New Demand Emerging”, March, 2013, utrade.com.hk/en/blue-top/315201344036PM524953.pdf, (read 25.4.2017).
[11] Layton, D. W. and McConkey, M. “Vietnam issues final determination in country’s first trade remedy case”, March 10, Mayer Brown LLP, 2010 http://www.lexology.com/library/detail.aspx?g=36f0ad52-6253-409e-a5f2-48b45b6521e3, (read 25.4.2017).
[12] Nieminen, P. Answers to a questionnaire. April 2, 2017.
[13] Drucker, P. “Innovation and Entrepreneurship”, Pan Books, London, 1985.
[14] Savaëte, B. “25 Years (1992 – 2017) in the flat glass industry – What did we get during last 25 years in the flat glass industry (1992-2017) and what could we expect for tomorrow? in the chapter “Main mistakes we have made during last 25 years” @ BJS. Différences [Document in preparation for GPD 2017 at Tampere]
[15] Luoyang Glass Company Limited http://lygoverseas.en.hisupplier.com/about-us.html