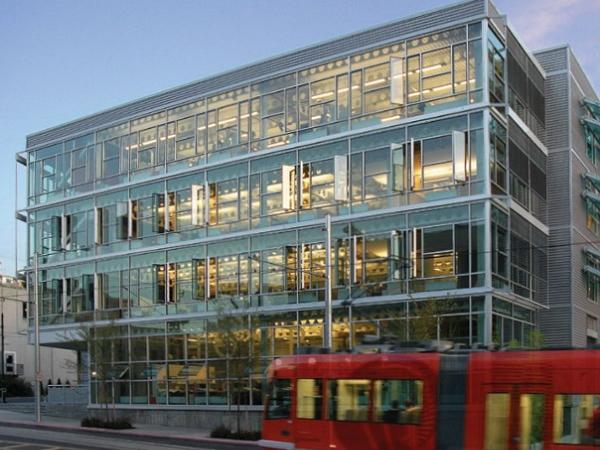
Date: 29 August 2019
The Terry Thomas is more than Seattle’s newest architectural jewel, it also is one of the country’s most impressive green buildings. That’s the judgment of the American Institute of Architects (AIA) Committee on the Environment (COTE), which honored The Terry Thomas as one of 2009’s 10 best green building projects.
Situated in Seattle’s thriving South Lake Union neighborhood, The Terry Thomas is home to Weber Thompson, the architectural firm that designed the building with the goal of making it a showcase for sustainability, an effort that was ultimately rewarded with LEED® Gold for Core and Shell certification and Platinum for Commercial Interior certification by the U.S. Green Building Council (USGBC).
As the owner of LEED’s two highest certification designations, The Terry Thomas features countless energy-saving mechanical, design and building material highlights. The most ambitious is a passive cooling system whose performance relies in part on windows fabricated from Solarban® 70XL glass by Vitro Architectural Glass (formerly PPG glass). The first passive cooling system for a major office building in Seattle in decades, it is designed to cut energy use by 30 percent compared to similarly sized office buildings.
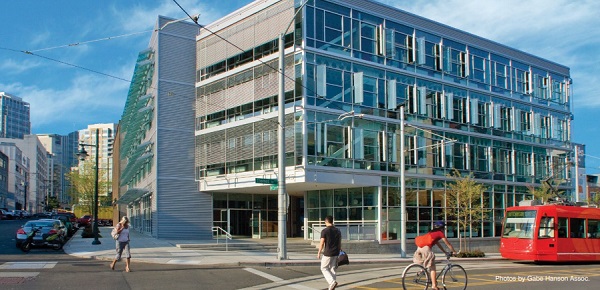
Photo by Gabe Hanson Assoc.
Gabe Hanson, an associate with Weber Thompson and the senior project designer of The Terry Thomas, said the passive cooling system orchestrates several design strategies to enhance ventilation and reduce solar heat gain. Because glass predominates the building envelope and makes its inviting, translucent appearance possible, Solarban® 70XL glass is critical to many of them.
According to Hanson, the primary engine of the passive cooling system is a central courtyard, which acts as a chimney, distributing fresh, cool air among the building’s narrow 38-foot floor plates. Workers overlooking the courtyard have operable windows fabricated with Solarban® 70XL glass, enabling them to control the temperature and environment around their workspaces.
Solarban® 70XL glass also is featured on the east and west facades, where custom-designed sunshades in front of punch windows provide abundant daylight and limit solar heat gain. Along the north façade, gull-winged windows, also made with Solarban® 70XL glass, allow summer breezes to permeate the entire structure.
Beyond its mechanical function, Hanson also identified the transparent Solarban® 70XL glass on the north façade as the “metaphorical soul” of the building, connecting it both literally and figuratively to the surrounding streetscape.
Although he had little familiarity with Solarban® 70XL glass before this project, Hanson said it quickly became apparent that it was the ideal choice for his company’s new home. “We considered a number of different glass types for this project,” he explained, “Solarban® 70 [XL glass] was the one with the best balance of clarity, hue and thermal performance.”
Introduced at the U.S. Green Building Conference in 2005, Solarban® 70XL glass offers visible light transmittance of 64 percent in a 1-inch insulating glass unit, along with a solar heat gain coefficient of 0.27. The resulting light to solar gain ratio of 2.37 remains unmatched in the industry, four years after the product’s debut.
Other energy-saving highlights include computer-automated blinds and louvers, light metallic exterior materials and a white high-albedo roof that provides fresh air, reduces heat island effect and cools the building.
Recycled materials, including steel, aluminum, and fly ash concrete figure heavily into the building’s construction, as do dual-purpose interior elements such as ceiling-mounted acoustical panels that act as light reflectors, hermosote panels that reduce noise and hold pin-up materials, and a metal cable tray system that corrals electrical and data cabling while providing mounts for lighting fixtures.
Hanson said the building materials, including Solarban® 70XL glass, were chosen for their ability to reduce costs, embody energy and express the building’s honest, simple form and function.
After the first year of occupancy, Hanson reports that The Terry Thomas actually outperformed its ambitious 30 percent energy-reduction goal. Preliminary studies showed it actually consumed about 46.38 kBtu per square-foot in its first year of operation, a reduction of nearly 42 percent compared to the U.S. national average of 79.8 kBtu per square-foot of office space. Even more impressive is the yearly workspace energy consumption of 40.63 KBtu per square-foot, which is 51 percent less than the average American workspace.
Most importantly, there is high satisfaction among the people who work in the building, which includes not just the architectural firm but several other tenants as well. An independent, postoccupancy survey showed that a full 100 percent of the respondents had experienced improvement in, or were very satisfied with, their sense of community, physical comfort, daylight, ventilation and ability to control systems.
PROJECT CREDITS
Owner
Thomas & Terry, LLC
Architect/Designers
Weber Thompson
Seattle, WA
Vitro Products
Solarban® 70XL glass
Glazing Fabricators
Oldcastle BuildingEnvelope®
Battleground, WA
Glazing Contractor
Issaquah Glass
Issaquah, WA
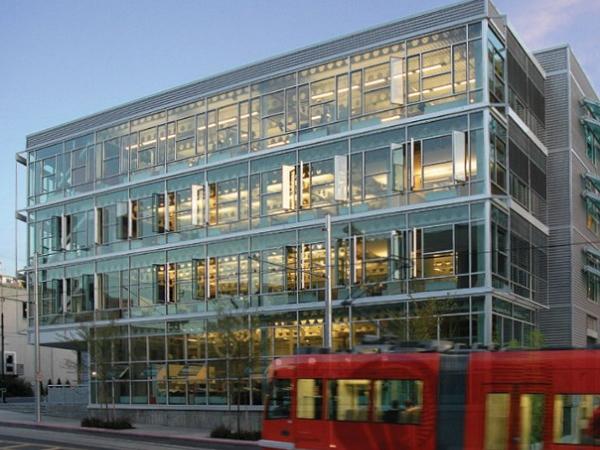

Add new comment