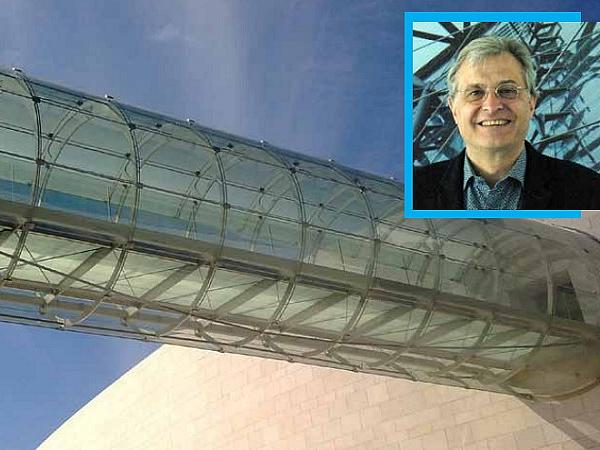
Date: 29 May 2019
‘Laminated Glass News’ speaks to Francesc Arbós, President of the Bellapart Group and discovers how technology and new design philosophies have moulded and defined the uptake of glazing in architectural construction.
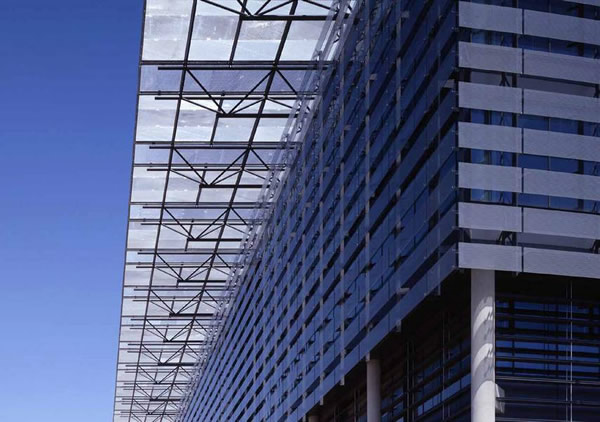
Image © Bellapart
Bellapart specialises in the design and construction of bespoke structures, façades and complex building envelopes made from glass, steel, aluminium and other high-tech materials. First established in 1939, and still family owned (3rd generation), the company is located in Catalunya, Spain, with subsidiaries in other countries, including the UK, the USA and France.
Its past and current project list reads like a ‘Who’s Who’ of landmark construction, with some of the most fascinating architectural projects benefiting from the company’s expertise. One particular project, the Endesa Headquarters in Madrid, set a milestone in the combined histories of Bellapart and Kuraray, as it was the first instance of SentryGlas® being used in Europe.
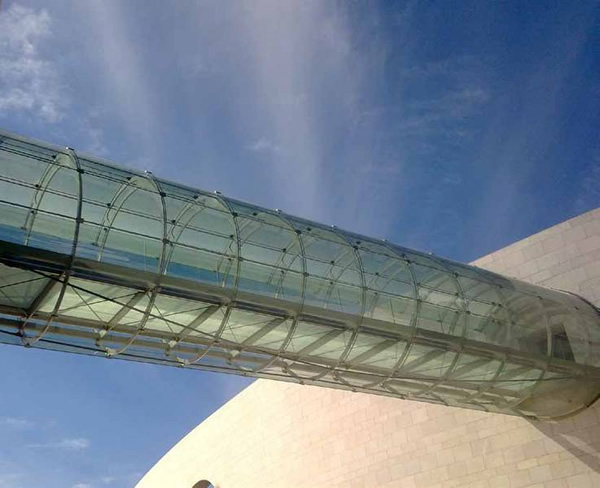
Q. As a façade/building-envelope design and engineering company, how has the development of ever more capable interlayers changed your design capabilities and visions?
“At the time of the Endesa project, we were undertaking studies into larger flat glazed roofs,” Arbós explains,” but we faced issues relating to the lack of stiffness and post-breakage performance of traditional PVB interlayers. I actually first read about SentryGlas® in this very publication, ‘Laminated Glass News’, where DuPont (the original developer of SentryGlas®) mentioned a new interlayer that it had created for hurricane applications. This really captured my attention. So, like any self-respecting and curious engineer, I contacted DuPont to ask if this new interlayer could be used for my application.
“It was fortuitous timing,” he adds, “because at that time there was a need for a much more structural interlayer and SentryGlas® was just what the market needed. I remember asking for the material’s properties, but it was so new and still under test, so DuPont could only send me some very basic figures for elastic modulus. However, I was able to mock up a design using these values and found that it was a perfect match for the demands of this project.”
Built between 2001 and 2003, the roof of the Endesa building was subject to an in-depth inspection in 2014 − 11 years after it had been installed − and Bellapart’s faith in the material was more than justified, with one of the testers commenting that the glazed panels delivered performance characteristics similar to ones that had been fabricated much more recently. The main concern was delamination, especially around the circular mounting holes installed during construction, but the inspectors found both the exposed edges and the hole perimeters to be delamination free. A real testament to the longevity and performance of the interlayer.
“The original design was done with PVB,” Arbós elaborates, “and I was able to get good postbreakage performance from the PVB using the circular mounts, but when I did the same test using SentryGlas® the results were incredible. When the panel was broken, the PVB construction offered us about an hour of weight bearing before failure, whereas the SentryGlas® equipped panel simply refused to fail. Endesa was the beginning and we have kept using SentryGlas® ever since.”
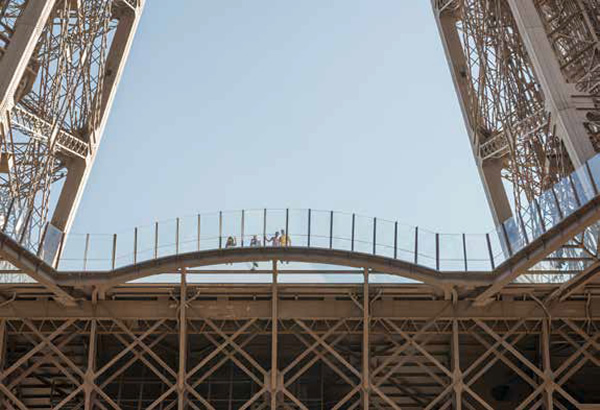
Image © Bellapart
Q. How has your frame & mounting technology developed based on the new levels of strength and stiffness available?
“The designs are developed by architects. We get the design engineering specification and then work from there,” Arbós explains. “In the early days, architects did not understand the capabilities of interlayers, so we often had to get them up to speed. This has now changed dramatically. Not everyone is completely informed about their performance characteristics, but the main players know the capabilities of interlayers and what they can do. We now regularly receive drawings in which the interlayer has already been specified.
“What we receive in terms of drawings and technical specifications then have to undergo significant engineering design and evaluation,” he adds, “so we know the glass can be manufactured and installed safely. This is one of the reasons why I feel we can achieve excellence at what we do, thanks to our engineering capabilities and our testing labs. We have seen projects fail due to a lack of knowledge.
“You have to have a deep understanding of physics, structural behaviour and engineering,” he elaborates. “That’s the only way you can discover and then define the best manufacturing and installation processes. For that reason, we call ourselves an engineering firm with a workshop rather than the reverse. We really design, analyse and test every single detail, in order to be able to manufacture every item, along with how it is installed, its tolerances and its relationship with other parts of the structure. Experience is important, but so is having a good and talented engineering team.
“We don’t like using the words ‘standard design’,” he explains, “we are very solution oriented; we love those challenges. In fact, the more difficult the better! We always try to find a solution to make the intent physical. We are proud to have worked with many design agencies, and there are some very talented and brave (in terms of design attitude) engineers out there − with a willingness to go much further than what is evident.”
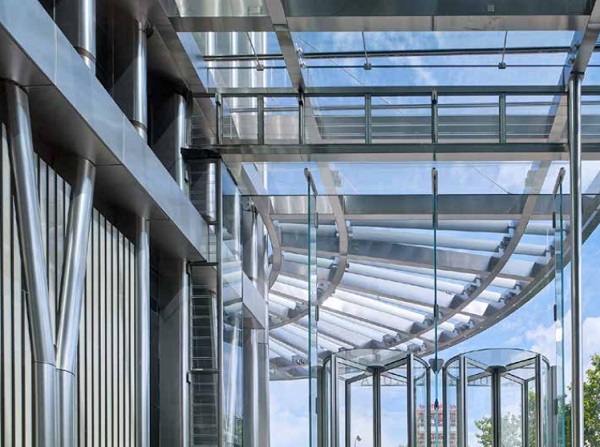
Image © Bellapart
Q. What sort questions do you need to ask architects when they present you with their glazing visions?
“Architects are good at communicating their visions,” Arbós tells us. “When we first meet, they have thought through these visions − sometimes from months or even years − and can communicate what they want. We need to be able to understand and follow these visions, often with the help of other engineering disciplines. Our strength lies in our ability to follow these ideas, even to the smallest detail, so that the initial intent can be safely built. This often forms the Keystone of the project. You have to ask the right questions to get the right answers in order to satisfy what the architect really wants… without sacrificing the safety or the performance of the structure.”
Q. Are you seeing any trends based around glazing?
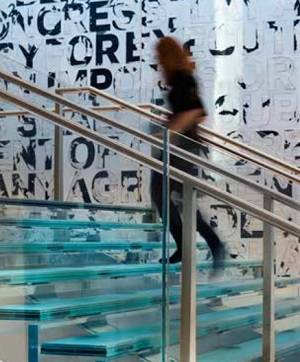
Image © Bellapart
“In Europe particularly – much more so than other regions – glass is used a lot in buildings and is very common in almost all designs,” he explains. “Structural glass jobs have certainly increased, but it is still a relatively small niche compared to general glass usage. Performance interlayers such as SentryGlas® are used where they are needed, and their take up is certainly growing, but only in applications where their performance characteristics are essential.”
Q. Can you give us an example of Bellapart glazing projects using Kuraray interlayers?
“The one that immediately springs to mind is the Bombay Sapphire project,” Arbós enthuses. “In this particular case I will admit that this was a job where all the skills we had were not enough. As a result, we had to develop new skills to solve the complex scenario; and I am delighted to say that we succeeded – and received an international prize for the design of the two curved glass greenhouses that really do look spectacular, delivering both functional and aesthetic characteristics to the distillery.”
Q. What sort of things are now possible that maybe weren’t 5-10 years ago?
“The most stunning evolution is the glass sizes, primarily thanks to SentryGlas®,” he explains. “Huge panels are now available in multi-laminate constructions. I could never imagine that the size could grow this big − 12 metres was already very big. It is a surprising trend and still in fashion right now and will continue for several years, thanks to the specific properties of SentryGlas®. All the interlayer’s properties have been exploited, but I think there are more to be discovered.
“Product evolution is also important,” he adds, “and developments such as SentryGlas® Xtra will certainly see use in demanding applications. In the US embassy in London, there is the main staircase and 36 m-long pedestrian bridge, which were made using thick glass laminates. In this instance haze can be an issue if the laminates have not been processed properly or precisely, so SentryGlas® Xtra will certainly help to get beams and stiffeners more transparent than ever before.”
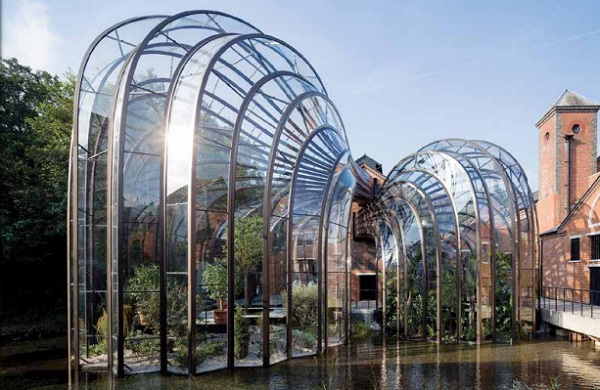
Image © Bellapart
Q. If you had a wish list, what would the next generation of interlayers offer?
“Communication is vital in this day and age,” Arbós says. “If interlayers could double up as some form of information delivery system too, that would be amazing. There are other projects trying to achieve this, but having it as a function of the interlayer would tick many boxes.
“From an engineering perspective,” he continues, “one of my first uses was in a roof at the science museum in Barcelona, specifically the Amazonian Space. Scientists from the museum asked for laminates that would let in UV for plants. We used SentryGlas® Natural UV for this application, but it would be great to be able to tune and adjust UV levels depending on the conditions required. Also, in terms of engineering, more stiffness would be desirable – any engineer will tell you this − and enhanced thermal properties are certainly starting to appear on whish lists, but without sacrificing clarity.”
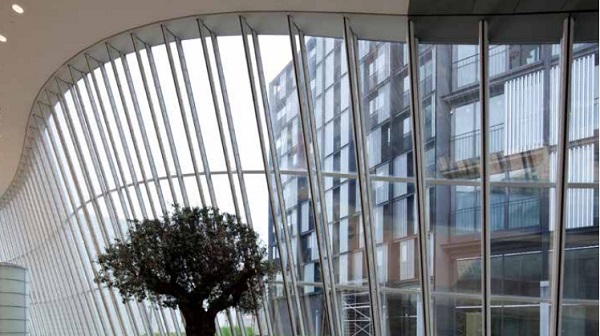
Image © Bellapart
Q. What do you think will be the next major breakthrough/trend in the world of structural glazing?
“We are working on a few different aspects in our research,” he explains. “We are reactive to architectural design; in that we build designs from others. Our research is centred around solving specific problems, such as how to increase strength or how to fix dissimilar materials using high-strength bonds for high-temperature applications. We invest a lot in knowledge. There are many materials available, but how do they behave in certain applications, scenarios and scales? We need to discover all of this.
“We always strive to look to the future and undertake research that will help us to understand physics, mounting, welding, parameters, installation, movement, etc.,” he concludes. “Our research is truly scientific in many ways, but we don’t really design new products, we design new ways that help manufacture the designs to come.”
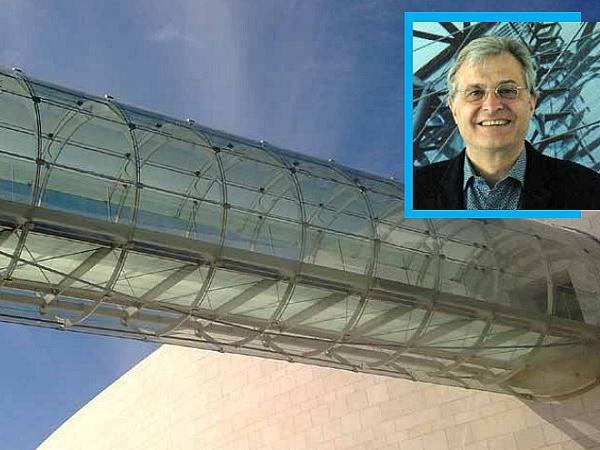

Add new comment