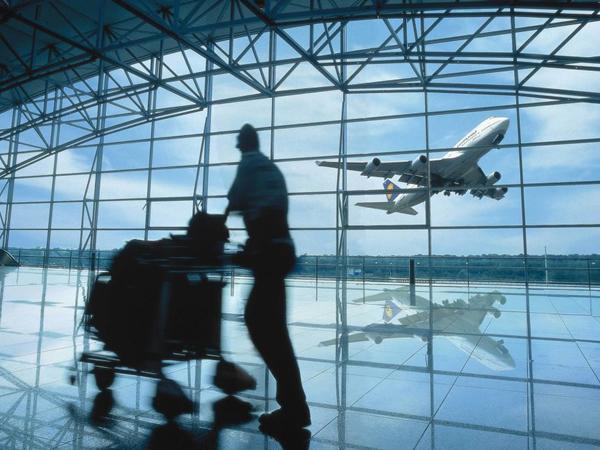
Date: 4 April 2020
The trend to buildings with large areas of glazing glazed with fewer supports is showing no signs of abating. Windshields in vehicles are getting bigger, too. For many years now, simple glazing has not been able to meet the challenges on its own. Modern plastic interlayers – made of polyvinyl butyral (PVB) or ionoplast –help give glass the necessary physical properties. And for some applications they are indispensable. With careful planning, glass interlayers can reduce the total weight of the finished insulating unit.
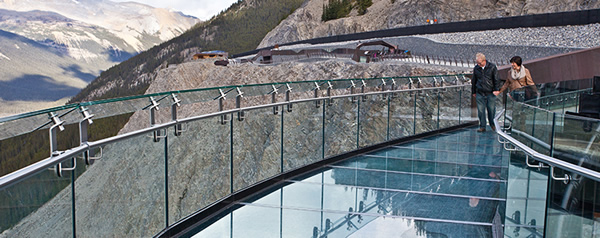
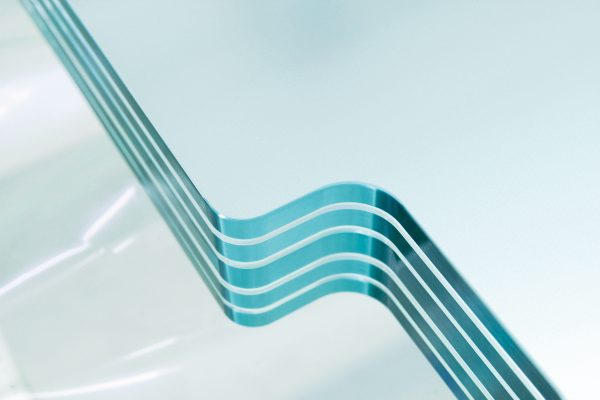
Laminated glass – a composite comprised of at least two layers of glass with a PVB or ionoplast film interlayer between them – makes glazing safer, tougher and more resistant. So if it breaks, the splinters of glass adhere to the adhesive film, preventing injury to people close by.
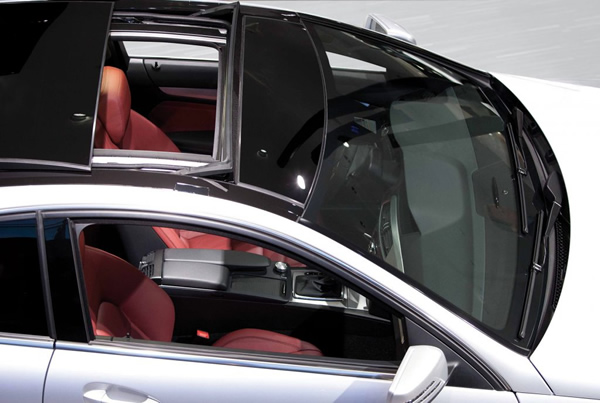
The effect is not visible to the naked eye: the finished product is as transparent as a single pane of glass. Only experts can tell the difference. Yet, the increase in safety is massive! For example, if a windshield is damaged while driving on the highway, it does not burst. It simply tears, leaving enough visibility to bring the vehicle to a halt safely. Everywhere in the world, windshields in vehicles have to be made of laminated glass. That is a legal requirement. Laminated glass is also mandatory for glazing in buildings that can injure people if it breaks.
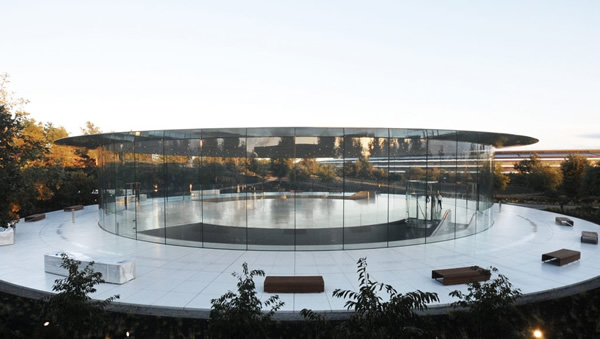
As laminated glass improves, it is opening up completely new architectural possibilities. Today’s glass façades and roofs look lighter and more airy. Wherever possible, modern architects try to hide or even do without visible supports and edge-framing. The cube built by computer manufacturer Apple on Fifth Avenue in New York is a good example: the original structure built in 2006 comprised 18 laminated glass panes on each side of the cube.
The building was redesigned in 2011 and now it has just three laminated glass panels on each side. That gives the building almost unmatched transparency – a design feature that architects around the globe seek to emulate. Trosifol® helps them achieve it. Tinted films and digitally printed films and other innovative products for interior are important to meet complex architectural requirements. Trosifol® is apply to meet such needs as well.
Glass is becoming a load-bearing structural element
The Trosifol brand has been part of the Kuraray Group since 2005. It is a world leader in PVB and ionoplast interlayers for laminated safety glass for applications in architecture and the automotive and photovoltaics sectors.
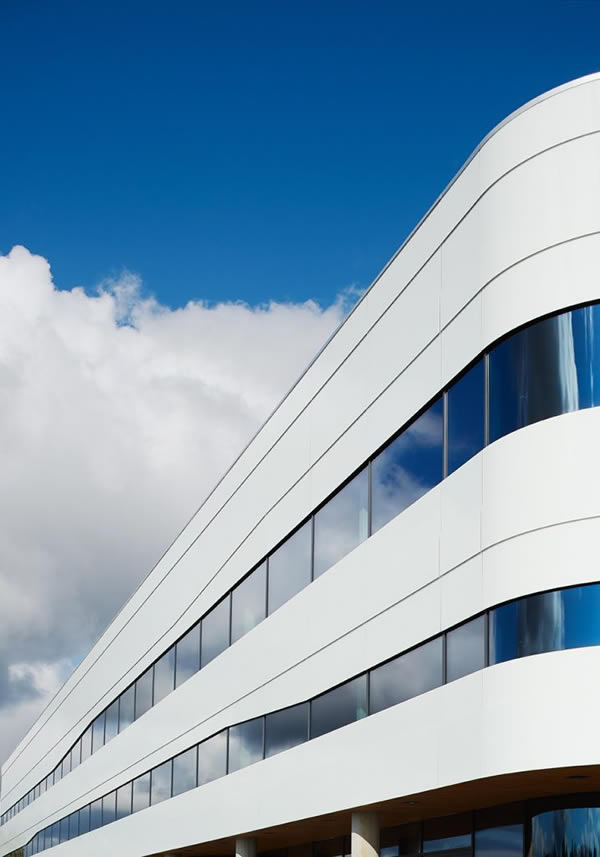
Photo: Lindman Photography
Structural interlayers with good stiffness improve the mechanical properties of laminated glass, open up far new more options for high-performance glass façades. Better deflection properties and enhanced stiffness permit longer, thinner and bigger glazing with better resistance to mechanical strain. The structural properties of modern glazing mean that it can be used as a load-bearing element.
Hurricane-proof glazing can withstand massive storms and provide protection against large and small pieces of wind-borne debris. This type of glazing is often used to protect people and buildings in regions at high risk from hurricanes and cyclones. If the glass is not laminated, storm-force winds can cause it to break and get into the buildings. The pressure that builds up inside can lift the roof off. That means the building loses a key structural element, causing it to collapse. Laminated glass prevents that because it does not burst.
Special Trosifol® films are also used in impact-resistant glazing for both low-level and high-level security requirements (embassies, government buildings, high-risk buildings, interior fixtures). Naturally, Trosifol® products also offer excellent defense against break-ins, vandalism and burglaries.
Plastic interlayers enhance design and convenience
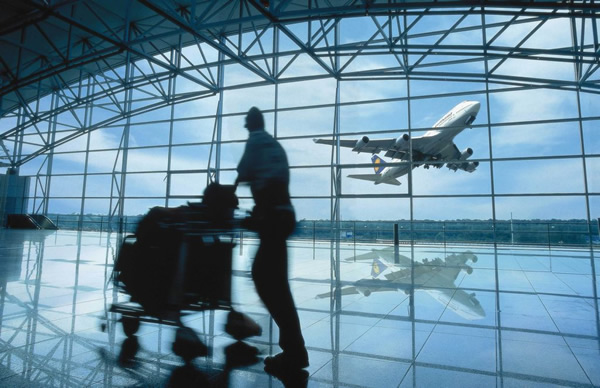
Acoustic insulation is becoming increasingly important in light of the awareness of the health-risks associated with noise. In addition to reducing aircraft, traffic and industrial noise in buildings, acoustic glass is also becoming more common in vehicles. Special films are needed to meet individual requirements. For example, Trosifol® films are an effective way to ensure glazing provides protection from UV radiation. Or the opposite: to make sure the glass transmits as much UV radiation as possible. That is important, for example, in greenhouses and in zoos, in order give the animals real sunlight.
Convenience and, above all, safety are features of today’s head-up displays in vehicles, which project key data such as speed, indicator settings and navigation data onto the windshield. That means drivers no longer have to take their eyes off the road to look at the instrument panel. So their eyes do not have to adjust from the brightness of road to the dark interior of the vehicle – seconds in which they are distracted from what is happening on the road and cannot react rapidly enough if something unexpected happens.
How does the film get into the glass?
To manufacture laminated glass, the interlayer film is pressed between two layers of glass by applying high pressure and heat. That makes sure it is transparent and gives the glass new properties: shatter-proofing, acoustic insulation, UV protection, etc. According to the experts, the end product is only optimum if the film is invisible. No-one except an expert can see whether glass is laminated or not simply by looking at it.
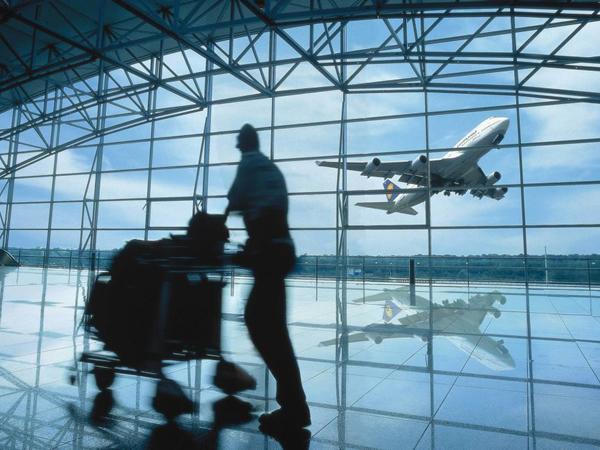

Add new comment