Article Information
- Digital Object Identifier (DOI): 10.47982/cgc.9. 572
- Published by Challenging Glass, on behalf of the author(s), at Stichting OpenAccess.
- Published as part of the peer-reviewed Challenging Glass Conference Proceedings, Volume 9, June 2024, 10.47982/cgc.9
- Editors: Christian Louter, Freek Bos & Jan Belis
- This work is licensed under a Creative Commons Attribution 4.0 International (CC BY 4.0) license.
- Copyright © 2024 with the author(s)
Authors:
- Michael Elstner - AGC Glass Europe
- Antonella Contino - AGC Glass Europe
- Marco Zaccaria - Europe Technovation Center
Abstract
Increasing the circularity of flat glass does not only mean to collect glass cullet from internal and pre- consumer processes. It also means to use glass cullet from the post- consumer applications, such as residential or commercial buildings. The flat glass industry is currently in a transformation phase to reduce its CO2 emissions. To produce Low Carbon Glass with reduced carbon emissions generated during the production of float glass, a holistic approach is applied. Among these, one of the pillars is the increased use of cullet. Cullet comes from different sources: internal cullet, pre- and post- consumer cullet. In order to be able to use cullet in float glass production, it must be of high quality. Since there are a large number of architectural glass products and glass types, it is essential to collect and sort in the most adequate way.
1.Introduction
Flat Glass recycling plays a crucial role in achieving a circular economy, which aims to minimize waste and maximize resource efficiency. Glass is a unique material that can be recycled indefinitely without losing its quality or purity. By recycling flat glass, we can divert waste from landfills and transform it into new flat glass products, reducing the need for virgin raw materials and the environmental impact associated with glass production. This closed-loop system promotes resource conservation, waste reduction, and sustainable material management.
Flat-to-flat recycling is when post-consumer glass is collected, sorted and transformed back into float glass. With this method, glass can be recycled indefinitely. Recent studies (Hartwell, Coult, & Overend, 2022) have shown the importance of flat-to-flat recycling, with the potential of reducing the CO2emission by 18% if the full potential of post-consumer glass can be recycled (UK figures only). However, the actual flat-to-flat collection rate is not widespread for a series of challenges requiring a variety of stakeholders associated with technical and economic issues (Geboes, Galle, & De Temmerman, 2022). From a technical point of view, a study was made in order to assess whether post-consumer glass collected in containers and then treated by a recycler could provide a cullet quality satisfactory to a float plant (2017). Successful case studies (DeBrincat & Babic, 2019) have shown the actual possibility to recycle post-consumer glass, but the relatively scares repetition of this study highlight the difficulty of this practice. Recently, glass manufacturing companies are increasing their efforts in order to collect large quantities of post-consumer glass for flat-to-flat recycling.
2. Waste, glass and recycled content
The current situation in the building industry shows, that many buildings are demolished instead of being refurbished. From the perspective of the circular economy it is more than important that we use our resources more carefully than in the past. For that reason any construction material, including glass, should be reused or recycled as much as possible. Knowing that the glass industry is overall an energy intensive industry, glass is melted at about 1600° C mainly based on fossil fuels for the moment, we need to close the loop of flat glass recycling (cullet) as much as possible. To increase the quantity of cullet coming from installed glass units in demolishing as well as refurbishment projects, we need to organize the glass recycling in a better way. For a better understanding of the terms used in the context of glass recycling, we describe in the following chapter, the difference between the cullet types.
But using a high percentage of cullet has two major drawbacks: the limited availability of cullet itself and increased quality risk. In glass recycling, it is distinguished between internal cullet and pre- and post-consumer cullet. These terms refer to different sources of flat glass waste and play a significant role in the recycling process.
1.Internal cullet coming from float line rejects, such as glass rejected for quality issues, glass from edge removal operations and glass discarded as a result of changes in thickness and/or colour. The quality of this cullet is well known and there are generally no risks associated with the full and direct reuse of this cullet in flat glass production.
2.Pre-consumer cullet from glass processing (breakage during transport or production, geometrical losses or quality rejects) can be split into two groups: cullet which directly returns to a furnace without additional processing, mostly cullet from geometrical losses, which is considered as a by-product of glass processing; and cullet that must be processed by a recycler to allow its use in a glass melting furnace. Until it is processed by a recycler, this cullet is considered waste and it requires specific conditions for handling and storing. In both cases, handled and stored cullet must be considered a future raw material for float glass production, with the utmost care taken to prevent its contamination by other -products or waste. Indeed, the contamination of cullet streams is the main barrier to the full exploitation of available streams as a raw material for the production of flat glass. Such contamination can, in some cases, cause quality issues when recycled in a glass furnace despite the best processing efforts by recyclers. Recycling flat glass in a flat glass furnace is often jeopardised by the capture of cullet flows from container or the insulating wool sector.
3.Post-consumer cullet comes from the recovery of glass from the renovation or demolition of commercial or residential buildings. Cullet recycling in flat glass furnaces from post-consumer sources has been low or non-existent for years due to major concerns from flat glass manufacturers about the quality of this cullet and the limited economic benefits for all parties involved. Quality concerns are obvious with a much higher level of risk than for pre-consumer cullet, aggravated by the fact that the traceability of batches is difficult to maintain and that, consequently, the care taken in dismantling is often limited.
The limited economic benefit lies in the relatively low intrinsic value of glass compared to other materials, such as steel, aluminium and PVC from demolition/refurbishment which shifts focus towards these materials. For glass makers, limitations arise from the wide variety of sources for post-consumer cullet and the requirement for a massive and densely networked collection organisation in order to collect significant amounts of cullet.
Regulations, pressure for concrete actions to reduce companies’ environmental footprint and pressure on saving natural resources are changing this status. Extended producer responsibility schemes, such as the French REP (ÉCOLOGIQUE, 2020) regulation and circularity obligation, as well as consumer preferences for circular economy products, together with improving performance in processing recycling glass via more efficiently rejecting deleterious contamination have now created a more favourable context for post-consumer glass recycling in glass furnaces.
The dilemma then is to recycle this post-consumer glass in the flat glass furnace rather than forcontainer glass or for insulating wool. While at first glance, the choice of type of glass furnace is neutral in terms of carbon balance and impact on climate, the considerations listed below advocate for a ‘flat to flat’ obligation or preference, since it:
- increases the overall recycling rate, making it mandatory for other sectors to recycle all their recycling flows, with the best available value-add, even the lowest quality or more difficult to collect ones, instead of focusing on more accessible/better quality (e.g. lead content) flat glass flows : the recycling rate of container glass in Europe is 78% - FEVE data (Judson, 2021) and the glass wool recycling is in the early stages of its journey;
- stops the use of flat glass cullet in container glass to compensate for insufficient colour sorting, would pressure to improve this sorting at collect and at recycling stages with a positive effect on the requirement for the remaining needed sand in the flat glass batch, saving resources of low iron, mid iron sands used in flat glass production for higher iron content sands more widely available, used for coloured glass production;
- does not prevent some flows, i.e. those of lesser quality despite the best available assessment, from being directed towards sectors other than flat glass. (Lefèvre, Delmotte, & Chantrain, 2023)
In the context of “recycling”(Glass for Europe, 2023) it is important to have a closer look at the terms “recycled content” and “recycled material”. The declarations of the glass manufacturers could include on one hand the percentage of cullet used to manufacture glass with a reduced CO2 content and on the other hand the “recycled content”. The “recycled content” can be calculated according to ISO 14021. In this standard, the “recycled content” is defined as “Proportion, by mass, of recycled material in a product or packaging. Only pre-consumer and post-consumer materials shall be considered as recycled content, consistent with the following usage of terms (ISO/TC 207; ISO 14021:2016 + ISO 14021:2016/Amd 1:2021, 2016)”.
As described before pre-consumer cullet is defined as “waste glass resulting from the manufacture of products that contain glass as one of their components, and which leaves the specific facility where it was generated but not reaching the consumer market”. An example of pre-consumer cullet is the glass cullet constituted by cut offs of the production of insulating glass which leaves the facility and are re-melted in the flat glass manufacturing facility. And post-consumer cullet as “waste glass originated after the use of the glass products at the consumer market”. (CEN TC 129; EN 17074:2020-12 , 2020)
On the other hand “recycled material” is defined as “Material that has been reprocessed from recovered [reclaimed] material by means of a manufacturing process and made into a final product or into a component for incorporation into a product.”
3. Low Carbon Glass
To address environmental concerns, flat glass manufacturers have developed low-carbon products with a significant reduction of the Global Warming Potential (GWP).
To reach low CO2 values, a holistic approach is a useful and reliable approach. AGC for example is focusing on six key areas for scope 1, 2 and 3.
- Sustainable sourcing of materials
- Use of highly efficient melting furnaces
- Increased use of cullet
- Use of green electricity
- Optimisation of transport between production lines for finishing processes
- Optimisation of transport for end products
The scopes of carbon emissions were introduced by the Greenhouse Gas (GHG) Protocol, the internationally recognized standard for corporate carbon footprint calculations. They break down GHG emissions into 3 different categories, facilitating the work of assessing the carbon footprint.
- Scope 1 = direct emissions occurring at the production plants
- Scope 2 = indirect emissions from electricity and steam production
- Scope 3 = indirect emissions from upstream and downstream activities along the value chain
Amongst several measures to reduce the energy need and CO2 emissions, a very effective way to reduce the embodied carbon in glass is to increase the cullet content.
There are three main reasons for cullet increase: As mentioned before, the most important reason is lower energy consumption(EC JRC, 2013)with an estimated 2-3% savings for each 10% increase incullet usage. This reduction in energy consumption makes it possible, among other things, to decrease the consumption of natural gas and thereby the emissions related to the combustion of gas as fossilresources. The second benefit of making intensive use of cullet is that it replaces virgin raw materialsincluding carbonates (soda ash, dolomite and limestone). Using more cullet decreases the carbonemitted during batch decarbonisation:
The third positive impact is that the use of recycled glass limits the environmental impact linked to theproduction or extraction of the substituted raw materials.
By combining these 3 points, as a rough estimation, it is estimated that each tonne of cullet makes it possible to save around 0,7 tons of carbon. (Lefèvre, Delmotte, & Chantrain, 2023).
Increasing cullet percentage is one of the main thrusts in Low-Carbon Glass production, but it accounts for only about half of the total decrease in embodied carbon. The cullet percentage in Low-Carbon Glass has risen to above 50% of the glass melt and is used as a compensating tool when contributions from other sources are not enough to achieve the maximum embodied carbon target.
This increase in the use of cullet for Low-Carbon Glass production is possible thanks to an increase in total volumes of collected cullet in the plants in question, mostly from pre-consumer sources, but also from post-consumer origin at a lower level in this stage. (Lefèvre, Delmotte, & Chantrain, 2023)
Figure 1 is illustrating the different cullet types. As you can see the collection of post- consumer glass is quite new. To provide a collection service for post- consumer glass is the most demanding service for the glass industry as well as the waste and recycling companies. Post-consumer has the highest benefit related to Green Building certifications. For example, within the green building certification scheme LEED, pre-consumer external recycled content is accounted with 50 % and post-consumer external recycled content with 100 % for the rating.
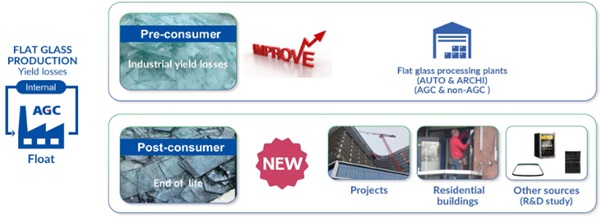
4. Proposal to increase the cullet quantity for the float glass industry
Flat glass used in buildings for interior and exterior applications, represents a significant use of glass in the construction industry. Recycling architectural glazing offers unique opportunities for waste reduction, resource conservation, and sustainable practices. These multiple applications are offering good opportunity to collect glass cullet.
A sorting as it is shown in figure 2 should be avoided for the production of flat glass. The reason is the high costs for recycling the glass to gain usable cullet and on the other hand in increases the risk for pollution which could have an effect for the yield and the technical quality of the float glass.
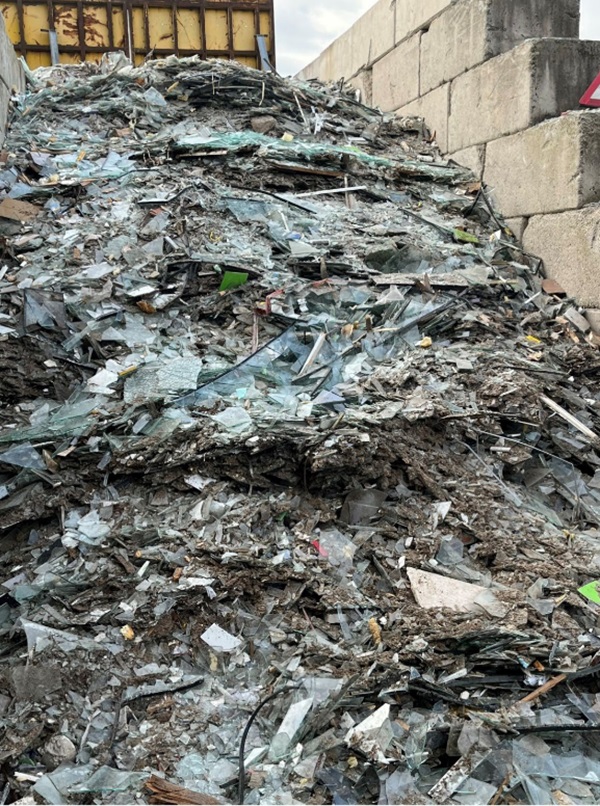
Increasing the cullet quantity for the float glass industry is a sustainable and economically viable approach. By collaborating with glass recycling facilities, raising awareness, implementing quality control measures, embracing technological advancements, and receiving government support, the industry can achieve higher cullet utilization. This proposal outlines strategies to promote cullet usage, leading to resource conservation, energy efficiency, waste reduction, and cost savings for the float glass industry. At AGC Glass Europe we have set- up a recycling service called “Recycle Glass”.
Recovering “old glass” from residential and commercial buildings we offer a service as shown in Figure 3.
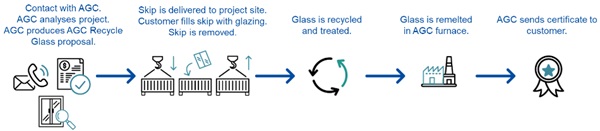
In detail this service includes:
- Skip Delivery: Once your project is underway, AGC arranges with its partner for the delivery of a skip to your project site. The skip provides a convenient and designated space for you to fill with glazing waste.
- Customer-Filled Skip: As the customer, you have the responsibility to fill the skip with the glazing waste generated during your project. This waste may include glazings, glass panels, or other glass components. They have to follow our specification for glass collection.
- Skip Removal: Once the skip is filled, AGC’s partner promptly removes it from your project site. Our dedicated logistics partners ensure that the skip is safely transported to the recycling facility.
- Glass Recycling and Treatment: At the recycling facility, the glass is carefully sorted, cleaned, and treated. We employ advanced recycling technologies to ensure that the glass waste is processed efficiently and effectively.
- Glass Remelting in AGC Furnace: The treated glass waste is then remelted in our state-of-the-art furnace. This remelting process allows us to transform the glass waste into high-quality recycled glass, ready to be used in new glass products.
- Certificate of Recycling: As a testament to our commitment to transparency, AGC provides a certificate of recycling to our customers. This certificate serves as proof that the glass waste generated from your project has been responsibly recycled and remelted in our furnace (for a “flat to flat” approach).
This service could be revised or adjusted project by project and location (region, country and city) as the conditions and regulations can vary.
The flat glass used in construction has a very specific composition. Other glass products (container, wool, tableware) than flat glass are not recyclable as a raw material in the flat glass process. To ensure perfect circularity, flat glass must be reserved for recycling in the production of flat glass. In case of deconstruction/demolition, if other glazing types (enamelled, mirror, etc.) are to be considered, a specific analysis will be carried out case by case by our services.
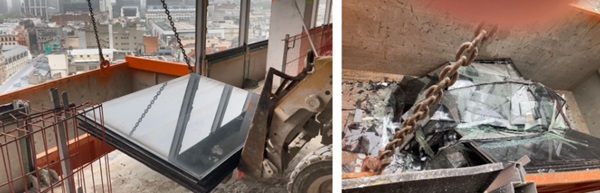
Figure 4 is showing the collection of the old glass pane of the project Oxy in Brussels, Belgium. For that project 300 tons were dismantled and brought back to a full closed loop recycling in the float glass production. Thanks to that approach 210 tons of CO2 have been saved as well.
However, the manufacturing process of flat glass requires strict quality and cleanness conditions in order to guarantee every chance of recycling. That's why it's essential that strict specifications and conditions of use are respected and guaranteed.
For the perfect circularity of the glass product it is important to sort and collect old glass panes. Allowed in the float glass production, are clear flat glass, coated or not coated, laminated glass, patterned glass, acid- etched glass, and other similar glass products.
On the other hand there are glass types which are not allowed to be used for the float glass production, such as wired glass, enamelled glass, glass bricks, mirrors, and others.
During the dismantling process the glazing will be removed from the frames either on site or in a specific workshop. All joinery, hardware, gaskets and sealants must be removed properly to limit the breakage of the glass. Broken glass lying on the floor can’t be recovered for recycling as this leads to huge risk of additional pollution (bricks, concrete, etc.).
Also the storage and transport conditions are very important to follow. More details about specific glass types and/ or storage and transport conditions can be found in our detailed specification.
5. Summary
Recycling glass is a crucial practice that contributes to a circular economy, waste reduction, and sustainable material management. By embracing glass recycling and the flat-to-flat approach, we can minimize waste, conserve resources, and reduce the environmental impact of glass production. Incorporating recycled glass into green building projects further enhances their sustainability profile, promoting energy efficiency, resource conservation, waste reduction, and improved indoor environmental quality. By prioritizing glass recycling, we can foster a more sustainable and environmentally conscious future. Another solution to give glass a “second life” could be to reuse it as a flat glass. Kowing that there are some constraints and questions behind that, it is currently addressed in R & D at AGC Glass Europe and also at the Fachverband konstruktiver Glasbau e. V. in Germany. There are questions related to the technical performance of a glass product (for example, is thestrength affected after the glass was installed several years in the building) and building law related ones (CE Marking etc.).
Our recycling initiatives significantly reduce CO2 emissions and preserve natural resources, contributing to a greener future. Customers benefit by fulfilling sustainability goals and reducing their carbon footprint. Embracing sustainable practices strengthens our position as a responsible and forward-thinking company, aligning with our corporate values and long-term business strategy.
References
CEN TC 129; EN 17074:2020-12. (2020). EN 17074:2020-12 Glass in building - Environmental product declaration - Product category rules for flat glass products.
DeBrincat, G., & Babic, E. (2019). Rethinking the Life-cycle of Architectural Glass. Glass Performance Days, (pp. 267-272). Tampere.
EC JRC. (2013). Best Available Techniques (BAT) Reference Document:for:Manufacture of Glass:Industrial Emissions Directive 2010/75/EU:(Integrated Pollution Prevention and Control).(P. O. Union, Ed.) Retrieved from http://eippcb.jrc.es/reference/BREF/GLS_Adopted_03_2012.pdf
ÉCOLOGIQUE, M. D. (2020, November 29). Décret no 2020-1455 du 27 novembre 2020 portant réforme de la responsabilité élargie des producteurs. JOURNAL OFFICIEL DE LA RÉPUBLIQUE FRANÇAISE Décret no 2020-1455 du 27 novembre 2020 portant réforme de la responsabilité élargie des producteurs.
Geboes, E., Galle, W., & De Temmerman, N. (2022). Make or break the loop: a cross-practitioners review of glass circularity. Retrieved from https://doi.org/10.1007/s40940-022-00211-y
Glass for Europe. (2023). Position paper on Reuse, remanufacturing, recycling: the case of glass for buildings.
Hartwell, R., Coult, G., & Overend, M. (2022, September 26). Mapping the flat glass value-chain: a material flow analysis. Springer. Retrieved from https://doi.org/10.1007/s40940-022-00195-9
ISO/TC 207; ISO 14021:2016 + ISO 14021:2016/Amd 1:2021. (2016). ISO 14021:2016 + ISO 14021:2016/Amd 1:2021. Environmental labels and declarations - Self-declared environmental claims (Type II environmental labelling).
Judson, J.-P. (2021, November 25). Close the Loop. Retrieved from https://closetheglassloop.eu/record-collection-of-glass-containers-for-recycling-hits-78-in-the-eu/
Lefèvre, H., Delmotte, L., & Chantrain, G. (2023). GPD 2023 Conference Proceedings, ow a holistic approach enables the production of Low-Carbon float glass with 40% less embodied carbon.
(2017). Life project: Flat to flat (Life12ENV/BE/000214) - Demonstration of an innovative fine crushing method for glass and alternative cullet in flat glass production.
Comments
This article presents an intriguing perspective on sustainability in the flat glass industry, focusing on increasing circularity through the integration of post-consumer glass cullet. By extending the scope beyond internal and pre-consumer processes to include glass cullet from residential and commercial applications, the authors highlight the importance of a holistic approach to recycling and reuse in the construction and glazing sectors. Chevrolet dealership Indianapolis