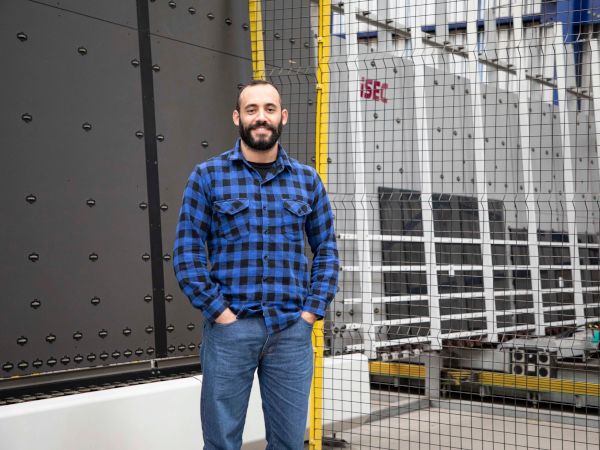
Date: 12 February 2025
Facing unique challenges in a country where climate and culture create a large market for tempered single glass, Clarity Glass is a household name known for high quality and incredibly fast batch size 1 production. They have partnered with LiSEC to realize their vision of becoming the first fully automated producer of tempered glass in Brazil.
B2B2B2C – A unique business model for a large market
With a production area of 18,000 sqm and around 200 employees, Clarity Glass’ production in São José dos Campos is unique in many respects. Their products, mainly customized tempered glass for interior and exterior application, are exclusively sold on the domestic market, within a range of approx. 600 km around Sao Paulo. About 92 % of their production consists of special dimension glass. Power is sourced primarily from solar and wind energy providers, while glass waste is sent directly to a nearby float glass manufacturer for recycling. Additionally, water is reused through a treatment system.
The sheer size of Brazil makes delivering the glass a challenge. While at one point, Clarity Glass operated 18 trucks, they have upgraded their distribution model to be able to focus on the glass production. “My business is B2B2B2C,” explains Andre Costa, owner of Clarity Glass. “We work with about 60 distributors, who are situated close to local glaziers. These distributors supply the glaziers not only with glass but also with all other materials they need.”
Mr. Costa know what his customers need: “We are last in the chain. When the customer orders the glass, the building is ready, and they are eager to have the panes as quickly as possible.” For faster turn-around times, Clarity Glass recently completed a project that linked all their distributors to their ERP system. The direct data connection had a huge impact on production speed, says Mr. Costa: “The glazier shows the customer the product in an app. When the customer approves, the order goes into straight into production. We need less time, and there’s less of a chance for mistakes.” This way, Clarity Glass can offer tailormade products fast: 24 hours from a jumbo pane to the rack, with next-day delivery to the distributor. The total delivery time for the customer is 48 hours, setting the benchmark on the market.
Partnering with the all.in.one:solutions provider: Clarity Glass & LiSEC
When Clarity Glass was founded in 1996, all work steps were done manually, while tempering was outsourced. Mr. Costa looks back, “We keep moving towards new solutions. When we bought our first, vertical furnace, we operated 3 shifts a day, 7 days a week, and produced 5.500 sqm per month. Year by year we bought new machines and increased our capacity, our experience and our know-how.” Laughing, he adds, “Until we found LiSEC to help us keep growing.”
Clarity Glass first visited LiSEC in Austria in 2017 and placed the first of a series of orders in 2018. What made LiSEC the perfect partner? Mr. Costa remembers, “We were looking for a company that had the whole solution. LiSEC is the only company I saw that had the complete solution for my case.” Many factors played into the choice; he says: “LiSEC is not a new company. They have a lot of experience, which is very important for us. We wanted to build a business relationship with a company that is good in experience, know-how, problem solving, and spare parts supply.”
It was very important for Mr. Costa to understand every aspect of the project: "Before initiating the first phase, we engaged in extensive discussions, covering the entire project and solution, including the back office and all machinery. The phases were designed to test the functionality and ensure immediate return on investment.” Due to this meticulous preparation, phases one and two were completed without significant issues or delays.
In the first phase a glass storage system with a feeding crane (PKL) was installed, along with an automatic cutting table (SprintCut) with X breakage and a custom label marker system. “We replaced three manual cutting tables with the automatic one,” says Mr. Costa.
The second phase added automatic Y and Z breaking and automated transport (SHL) to the existing processing lines. Phase three, realized in 2024 and 2025, includes an automatic sorting system (ASM), the first of its kind in Brazil. It splits the production stream after edge processing. One stream heads towards five topDRILL RX processing machines from Schraml, two of which include a waterjet cutting system. The second stream feeds the tempering furnace, where the panes arrive in furnace-bed optimized sequence and are loaded and unloaded by a robotic handling system (RHH). Clarity Glass is the first plant with automated furnace bed loading in Latin America.
In the background LiSEC’s production software solution (GPS.prod) with dynamic optimisation (Dynopt) ensures optimized cutting as well as automatic re-integration of remnant plates. LiSEC’s sorting system GPS.autofab with dynamic buffer organisation directs the panes down the different production streams. At the toughening furnace, the automatic furnace bed optimization ensures the most space and energy efficient load. In addition, three Viprotron ECO quality scanners confirm the continuous high quality at the end of the processing line.
Technologically mature solutions supplied with integrity
Talking about his experiences during the project, Mr. Costa highlights LiSEC’s reliability: “The cooperation is professional. While I was in Austria to discuss the project, specialists from different areas were asked to add their expertise. In my experience, there can be a point where too much customization becomes too complex for a supplier. With LiSEC, everything was put into writing. When I received the order, it had 110 pages – that gave me confidence. You can check that you get exactly what you paid for. I have been out on the production floor every day to follow the progress of the installation, and everything has been exactly as agreed, down to the number of brushes in the washing machine.”
As a tech-savvy owner who once processed glass on the shopfloor himself, Mr. Costa is very interested in the technology behind his machines. He has high praise for LiSEC’s ingenuity: “When we use a machine 1 year, 2 years, we can’t help but look for ways to improve it – move a sensor, solve some problem. When I see the LiSEC machines, I know they are doing the same thing. They always look for ways to improve, with their own engineer team, but also by listening to their users. I like to sit down with a machine and look at the details. On the LiSEC machines I see things I wouldn’t have thought of. I am certain LiSEC invests much in machine development and market research to make certain that LiSEC does it better.”
In summary, Mr. Costa states: “LiSEC offers the best automation solutions that meet our expectations and ensure stability every day, year after year. Their well-built and reliable construction is crucial for our 24-hour operation. Additionally, having LiSEC's support service in Austria is also very important to us."
A clear vision for the future
After the pandemic, the flow of information in Brazil's market has sped up, with new products and ideas being shared quickly. Businesses must keep up with this fast pace to succeed. On this highly competitive market, Clarity Glass has a bold vision, shares Mr. Costa: “We want the end consumer to recognize and request the Clarity brand directly, seeing the Clarity logo on the windows in their homes and offices.” Automation will play a big role in this, assuring the high quality and quick availability of their products.


Add new comment