Article Information
- Digital Object Identifier (DOI): 10.47982/cgc.8.441
- This article is part of the Challenging Glass Conference Proceedings, Volume 8, 2022, Belis, Bos & Louter (Eds.)
- Published by Challenging Glass, on behalf of the author(s), at Stichting OpenAccess Platforms
- This article is licensed under a Creative Commons Attribution 4.0 International License (CC BY 4.0)
- Copyright © 2022 with the author(s)
Authors:
- Valérie Hayez - Dow Silicones Belgium srl
- Georg Scheutz - Dow Silicones Belgium srl
Abstract
Since the early 2000s, an increasing number of globally reported fires in tall buildings, which have spread quickly, have been attributed to the façade. These dramatic events have raised concerns regarding the fire risk posed by materials used in façades and inside the building. Improved performance in both reaction to fire and fire resistance is a necessary requirement for construction materials. Silicone is used in many locations of the façade and buildings, such as sealing of linear joints or firestopping of penetrants in fire-rated walls and floors.
Standardized testing enables the evaluation of the fire resistance of such linear and penetration seals in terms of integrity (avoiding the passage of hot smoke and flames) and insulation (limiting the rise of temperature on the non-exposed side).Silicone can also be used to assemble glass-to-metal frames in bonding applications such as smoke barriers. In these applications, retention of bonding and the mechanical properties of the silicone are a cause for concern when exposed to smoke and high temperature. This paper reviews the high-temperature behavior of a selected range of silicones used for sealing and bonding in construction.
1. Background
Since the early 2000s, there has been a steady succession of incidents associated with the outbreak of fire in high rise buildings, whereby the exterior walls have been identified as a specific concern for spread of fire. Fire performance levels demanded by construction regulations (UAE 2018, UK 2019)have been increased, placing specific requirements upon engineers and architects with regard to the fire related performance of their structures. Specifically, minimizing the likelihood of a fire and reducing damage and personal injury in an inevitable fire event must take utmost priority.
Some of the building regulations can only be met if new fire resisting materials and improved design concepts are used. Sealants and adhesives are an essential element to fulfil both compliance with building code requirements (e.g., thermal performance) and respect the architectural design intent. Thanks to their unique chemical composition, silicones combine interesting mechanical properties and durability of performance which makes them the material of choice for bonding assemblies (Wolf 2017) in façades and buildings. Importantly, silicones also show promising behavior upon fire exposure.
The fire performance of sealants can be assessed through different testing standards. In the reaction to fire tests, suitable materials do not propagate fire when they burn and do not continue burning for any significant period following removal of the source of ignition. Important test methods are, for example, the single burning item test (EC 2010) and the surface spread of flame of building materials (EC 2002). Results of reaction to fire testing of silicones indicate that this material tends to burn locally, without flame propagation laterally or vertically and without production of flaming droplets.
In other words, silicones do not contribute significantly to the development of fire in the early stages. Standards such as EN1366 part 3 and part 4 (EC 2009, EC 2010) allow the evaluation of fire resistance of sealants used as linear joints and penetration seals in fire-rated walls and floors. Results of fire resistance tests show that fire-rated silicones maintain adhesion upon fire exposure and can reach more than 4 h integrity (E) and insulation (I) resistance, making them an effective means to block passage of hot smoke, gases and flames and prevent heat increase on the non-exposed side of a fire-rated compartment (EOTA 2017).
Designers seeking to fulfil fire requirements and using silicone bonding need to know how strong the silicone is, how long it will last and how the assembly will perform in a fire. In the event of a fire, bonding sealants should therefore not only maintain adhesion like the weatherproofing sealants, but also keep appropriate levels of residual strength. Figure 1 shows bonded glass units after exposure to a real external fire.

During the fire, the heat was sufficient to distort metalwork. However, the silicone still showed some level of adhesion, retaining the shards of the broken glass on the frame. Furthermore, a char can beseen on the silicone surface, resulting from the oxidative degradation of silicone to silicate-like (SiO2) structures (Tomer 2012, Camino 2002). Although considerable confidence in bonding silicones can be drawn from this type of result, it is important to quantify fire resistance. Unlike weatherproofing sealants, the standardization route to determine the fire resistance of bonding sealants is not well defined. Typical testing standards available to assess the performance of a curtain wall, such as the EN1364 series (EC 2014a, EC 2014b), do not allow an evaluation of the performance of bonded and unitized façades as their scope is currently limited to mechanically fixed façades. Efforts are in place to revise these standards to include this type of façade as well (Anderson 2021).
As well as resistance upon direct fire (flame) exposure, designers also seek answers regarding the flammability of the bonding silicones when exposed to high temperatures. Silicone sealants that bond to a fire-resistant surface, which shields the bonding sealant from the flames and oxygen, will not tend to burn, but it is important to ensure that the heat conducted to the bonding sealant does not impair its adhesion or mechanical performance. Bonding silicone sealants can also be used to fix protection systems such as smoke curtains. In this type of application, the sealant will not see direct flames but will be exposed to hot smoke.
The smoke temperature depends on many factors, such as the heat release rate of the fire, gas velocity, geometric constraints (e.g., longitudinal versus transversal gas flow), and the distance from the smoke source (Li 2011, Shi 2014, Yi 2019). Experiments suggested that smoke temperatures typically vary between temperatures around 400 °C when the exposure to smoke is close to the origin of the fire and less than 100 °C at larger distances (Hu 2005, Shi 2014, Starr 2014,Li 2017, Yao 2017, Yi 2019). Similarly, the European norm EN12101 (EC 2005) specifies a temperature of 200 °C for the testing of material permeability to smoke.
Even though silicone sealants do not melt, softening and potential degradation can occur upon exposure to high temperatures. Although the sealant might not show signs of visible deterioration especially when not exposed directly to flames but only to heat, it is critical to maintain mechanical integrity of the bonding seal upon high temperature exposure. For this purpose, it is key to determine the maximum time-temperature exposure of the material that would lead to mandatory sealant replacement. Very little is known about the loss of mechanical performance of silicone elastomers exposed to high temperatures. The study in this article is presenting the mechanical performance of state-of-the-art silicones used for bonding (structural glazing) and secondary sealing of insulating glass units (IGU) after exposure to high temperatures. The conclusions can be used to infer the behavior of these materials when exposed to smoke or reached by the bonded surface in the event of a fire, without direct flame exposure.
2. Experimental
There is no standard procedure available for the classification of sealants according to their thermal and mechanical stability. The data provided by manufacturers are based on various processes and assessment criteria. The test methods can differ in terms of duration of heat ageing, while the assessment can be based on different material characteristics, such as change in hardness, modulus, elongation and tensile strength at break, or ability of an adhesive to retain its adhesion on a hot surface. Depending on their use in the façade, different properties should be maintained upon exposure to high temperature. Bonding silicones used in façade or insulating glass should not only retain adhesion to the assembled substrates (e.g., glass and metal) but their ultimate tensile strength and modulus should not deteriorate significantly to maintain the bonding capacity. If movements of a particular scale are to be absorbed, a certain minimum elongation at break must also be ensured.
In terms of temperature and duration of the exposure, the target was to prove that bonding sealants maintain mechanical properties with minimum 75% of the original values after 2 hours at 180 °C. The temperature of 180 °C is the limit above which spontaneous ignition of materials may occur even in the absence of direct fire and flame exposure. It is one of the parameters defining insulation (I) criteria (EC 2007). The duration of 2 hours was chosen as it corresponds with an often required fire resistance performance level in the industry for insulation and integrity of linear joints. However, additional temperatures were also evaluated to better understand material behavior.
In the event of a real fire, it is possible that sealants will be exposed to the combined effect of temperature (up to 180 °C) and different mechanical loads, for instance the self-weight of glass or thermal movements. It is known that combining loads can reinforce their individual effect, however, this imposes more complex testing procedure and equipment. To compensate for single load testing, an additional safety procedure consists in requiring a relatively high retention of the initial mechanical properties to compensate for unforeseen effects. A threshold value of 75% of the initial properties after thermal ageing was chosen, aligned with the ETAG002 (EOTA 2012) approach. This threshold approach has been successfully and safely used for more than 20 years in silicone structural glazing to compensate for the use of single load tests.
Heating was performed in a Carbolite CWF1100 oven (5 L chamber volume). After an equilibration time of 15 min, the samples were introduced into the oven at the desired temperature. Oven temperature and temperature uniformity were controlled with an IR camera (FLIR E6).
The sealants used in this study were representative commercially available materials as described in Table 1. Bonding silicones used in façade and insulating glass were evaluated, both mono-component and two-component. As a comparison, a PU bonding sealant, used typically for bonding of windows in railway and transportation, was evaluated in similar conditions. Relevant initial properties are provided in Table 1.
Table 1: Mechanical properties of the materials tested in this study. a) Determined by dynamic mechanical analysis (DMA) at a frequency at 10 Hz and 30 °C. b) ISO 8339 (ISO 2005). c)Technical datasheet
Different types of samples were prepared to allow quantitative assessment of the change in mechanical performance with heat and duration of exposure. A first series consisted of small aluminium cups filled flush with the surface and left to cure for at least 28 days at 23 °C and 50% humidity in a controlled climate chamber. These cups were used to assess the behavior at different temperatures and duration of exposure using a thermogravimetric analysis (TGA) and dynamic mechanical analysis (DMA).
TGA was conducted on a TGA/DSC 3+ (Mettler-Toledo) using an aluminium oxide pan (70 μL) under air or nitrogen flow (50 mL/min) either in isothermal mode (200 °C, 3 h) or dynamic mode with a fixed heating rate (10 °C/min) from 30 to 900 °C. The coupling of TGA to a differential scanning calorimetry (DSC) sensor allowed concurrent recording of mass loss and heat flow during combustion. To compare the mass loss after the 3 h isotherm between sealants containing different filler levels, equation 1 was used to account for the undegradable filler, providing a mass loss only based on the polymer matrix.
The filler content can be determined from dynamic TGA experiments under nitrogen using the residue between 450 and 600 °C. Additionally, carbon black formation during TGA under nitrogen was accounted for by a final heating ramp under air.
DMA (Figure 2) is a versatile technique that can rapidly assess the viscoelastic mechanical properties of materials. For this report we focused on E’, representing the elastic properties of the material. Conceptually, E’ is related to the Young modulus and is a measure for material stiffness. However, E’ is determined from an oscillating deformation, whereas the Young modulus in tensile testing is derived from a continuous deformation, making a direct comparison difficult. In practice, E’ values are often higher than the Young modulus (Narducci 2016, Gioia 2020), which was also observed in the present studies. The absolute value of the modulus from DMA is dependent on instrumentation (Deng 2007)and following the recommendation of ASTM D4065 (ASTM 2017), E’ was used to identify trends in decreased mechanical performance and stiffness after heat treatment compared to the pristine material before heat treatment. Ultimately, the observed trends of E’ will also apply to measurements of the Young modulus in tensile testing.
DMA was performed on a Metravib 0.1dB Viscoanalyzer DMA50 in tensile mode with a fixed gap between clamps of 6 mm. The samples were cut into rectangles of approximately 20 mm length, 17 mm width, and 2 mm thickness. Storage (E’) and loss (E’’) modulus of samples without heat treatment and after heat treatment were determined in frequency sweep measurements from 0.1 to 100 Hz, at 30 °C and a fixed static force between 0.3 to 1 N, resulting in a strain of 0.5% (i.e., a deformation of 30 μm).

Conventional tension-adhesion (TA) joints (12×12×50 mm3), prepared according to ISO 8339 (ISO 2005)both on glass and on aluminium substrates were used to evaluate quantitatively the mechanical properties of the heated sealants. Samples were tested at 5 mm/min. Testing itself was performed at RT. At least 3 TA joints were tested to failure after each temperature ageing. From the stress-strain curve, the stress at 12.5%, the tensile strength and total elongation at maximum force were defined.
Indications of how the permanent load or creep resistance would behave after heat ageing was first evaluated for DOWSIL™ 993 Structural Glazing Sealant with lap shear samples of dimension 20 mm by 25 mm. Heat aged samples (2 h at 180 °C) were exposed to permanent weights at room temperature as well as in an oven at 60 °C, 85% RH, for 3months to accelerate the ageing condition. The weights applied on the bonded surface results in a permanent loading of 7000 and 11000 Pa respectively. These values were chosen as they are the permanent load resistance of a pristine DOWSIL™ 993 Structural Glazing Sealant and of a pristine DOWSIL™ 895 Structural Glazing Sealant.
Compared to 11000 Pa, the value of 7000 Pa represents only 63% instead of the previously used threshold value of 75%. Similar to the evaluation of the creep test defined in the guideline for silicone structural glazing ETAG002 (EOTA 2012), the movement during the loading and residual after unloading was monitored. In a second step, an adapted double H-piece was built and loaded as sketched in Figure 3. Again, different weights representing dead loads of 11000 Pa and 7000 Pa were hung from the central aluminum substrate to induce the permanent shear deformation. Permanent shear loading along the longitudinal direction or along the transverse direction were evaluated.

3. Results
In a first step, cup samples were exposed for various times (30 to 180 min) to increasing temperatures up to 300 °C to identify critical values for both parameters as a function of the sealant. After heat exposure, cross sections of the cups were prepared and TGA and DMA performed at various locations of the bulk and the surface (Figure 4).

The storage modulus E’ of the bonding and secondary sealing sealants decreases as temperature increases above 150 °C. As an illustration, Figure 5 shows the decrease in E’ for 30 min exposure up to 300 °C for DOWSIL™ 993 Structural Glazing Sealant and DOWSIL™ 3363 Insulating Glass Sealant. Although the surface and bulk have similar DMA moduli at RT, a slight difference occurs after heat exposure, with the surface showing higher E’ values than the bulk. DMA measurements of dogbone sheets with 2 mm thickness showed a decrease of E’ that matched the E’ decrease for the surface samples, suggesting that such sheets do not capture bulk degradation.
Therefore, being prepared out of thin sheets, the resulting modulus of dogbones after heat treatment will be higher than for a TA joint and less representative of real ageing conditions involving joints with a minimum sealant depth of 6 mm. This difference motivated the choice in the remainder of this paper to use TA joints (ISO 2005)to evaluate the materials’ performance rather than working with dogbones (ISO 2019). At 300 °C a significant softening of the material occurred which does not allow reliable measurement of the bulk modulus. The loss of strength compared to the reference is larger than 25% at 250 °C and therefore further evaluation will be focused on 180 °C, maximum 200 °C.

As the exposure time was increased at a fixed 200 °C heating temperature, the E’ (Figure 6) decreased following a first-order rate law according to equations 2 and 3, with E’₀ as the initial modulus before heat exposure, the rate constant k, and time t.

Using equation 2, the 12.5% Modulus of the DOWSIL™ 993 Structural Glazing Sealant after 2 h at 200 °C was calculated based on the average rate constant ((ksurf+kbulk)/2). The predicted value (0.26 MPa) and measured value (0.26±0.02 MPa) were very close. The determined rate constant is an absolute measure for heat stability of the evaluated material. It should be used with caution and not extrapolated beyond the assessed exposure time range. Notably the first-order rate dependence also applied for the modulus of the DOWSIL™ 3363 Insulating Glass Secondary Sealant. However, the mono-component bonding sealant DOWSIL™ 895 Structural Glazing Sealant followed a second order decay according to Equation 4. Based on chemical kinetics, second-order decay proceeds slower than first-order decays and DOWSIL™ 895 Structural Glazing Sealant should show better property retention upon high temperature exposure.

Importantly, the non-silicone, polyurethane (PU)-based bonding sealant exposed to similar conditions showed a quite different behavior. The material has a reference E’ modulus of 5.6 MPa (before heat exposure). After 2 h exposure at 200 °C, the material has softened too much to allow measurement of the modulus (Figure 8).

The mass loss according to isothermal TGA measurements at 200 °C for 3 h is considerable for the PU (20% of the total polymer mass) and neglectable at less than 2% for all the evaluated silicone sealants independent of their type (Figure 9A). The overlay of the mass loss curves for bonding and PU sealant demonstrates the fast and continued degradation of the PU sealant at 200 °C (Figure 9B). This was further verified by a temperature ramp from 30 to 900 °C, showing a steep weight loss starting at 200 °C for the PU sealant. The mass loss of the bonding silicone occurs later and at a lower slope (Figure 9C).
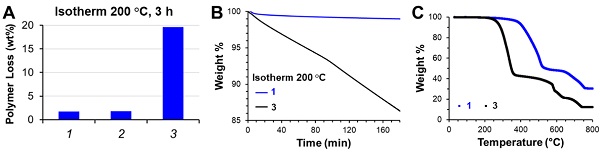
Furthermore, the PU releases about 480% more heat (7800 J/g) than a comparable silicone sealant (1600 J/g; Figure 10) and will contribute more to the fire development.

In a second step, the change in mechanical properties was evaluated through TA joints testing. Figure 11 shows the tensile stress-strain behavior of the DOWSIL™ 993 Structural Glazing Sealant TA joints after 120 min at different temperatures on glass and aluminium substrates. The tensile strength and stiffness decrease, whilst the elongation capacity is retained. When heated for 2 h at 180 °C the material retains adhesion and cohesive failure is observed. Some partial adhesive failure starts to occur after 2 h at 200 °C on glass which is not observed on aluminium substrates until 250 °C.
As the samples undergo 2 h exposure at 250 °C, adhesive failure is observed on both glass and aluminium (Figure 12). The better adhesion on aluminium substrates versus glass is well-known (Descamps 1994) as besides covalent Si-O-Si bonds, a physical interlocking in the pores of the aluminium surface occurs. Despite the observed adhesive failure, the values of tensile strength and elongation are still acceptable.


Interesting to note is that preliminary testing on a limited number of samples at significantly longer exposure times (up to 6 h) at 200°C does not indicate much further degradation of the mechanical properties of the DOWSIL™ 993 Structural Glazing Sealant (Figure 13). This observation correlates with an exponential decay for the first few hours of exposure that slows down at a longer time scale. The dominating degradation mechanism consequently changes as exposure times reach several days, resulting in harder and brittle sealants with higher modulus, that the exponential decay law will no longer predict. Further testing is ongoing to confirm these observations.

The secondary sealant DOWSIL™ 3363 Insulating Glass Sealant, behaves in a similar way, as illustrated in Figure 14 (left). The partial adhesion loss on glass is only observed when temperatures exceed 200 °C, which explains the better retention of properties. DOWSIL™ 895 Structural Glazing Sealant shows (Figure 14 right) a more stable behavior with little degradation between 180 and 200 °C in TA joints, which is similar to the previous DMA results.

As glass proved to be the worst case, this substrate was mainly used for further quantitative evaluation of performance change for both the bonding and secondary sealing silicones. The loss in mechanical properties at 180 °C and 2 h remains below or close to the chosen 25% performance criterium. At 200 °C, the loss in tensile strength and stiffness is just larger than 25%. However, they still providemechanical strength and did not disintegrate. Figure 15 summarizes the results obtained in tension.

Figure 16 compares the retention of DMA modulus and 12.5% moduli for the different types of silicone sealant after 2 hours heat exposure at 200°C. These results confirm that the DMA modulus can indeed be used as a quick alternative to TA joints analysis to study trends in property changes in the material.

Similarly, TA joints were tested in shear at various temperatures. Results are provided in Figure 17 and Figure 18. Compared to the original shear at RT, the bonding and secondary sealants are able to retain 75% of the original value of tensile strength, stiffness and elongation after heat treatment. No difference in tensile strength behavior is observed between the 180 °C and 200 °C exposure conditions. The shear stiffness does not decrease as much as in tension. This better performance in shear could be explained by the absence of high stress regions in the joint when loaded in shear, especially in the area close to the plane of adhesion with the substrate. On the other hand, TA joints tested in tensile have a heterogenous stress distribution with a high stress in the area close to the plane of adhesion.

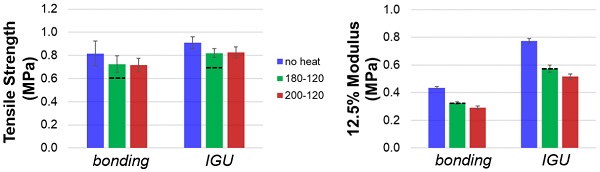
Finally, the evolution of the dead load resistance of the DOWSIL™ 993 Structural Glazing Sealant was evaluated after heat ageing the samples for 2 hours at 180 °C. The lap shear samples— typically used for this type of testing—did not show any loss in permanent load resistance, which is probably due to the smaller surface exposed to oxygen which limited thermal degradation in the oven at 180 °C. Therefore, we specifically designed double H-bar samples (Figure 3) to use TA joint dimensions during the dead load experiments.
After heat aging at 180 °C for 2 h, the double H-bar samples do not show any deformation when loaded at RT with 7000 or 11000 Pa dead load for 6 months. After 3 months in the oven at 60 °C and 85% RH, fresh samples (not heat aged) in the longitudinal direction resist both loads. Heat aged samples (2hours at 180°C) do show deformation at 11000Pa, whilst they are able to resist the lower permanent load of 7000Pa without resulting deformation. Results in the transverse direction were not useful due to the rotation of the samples which was not compensated for during the testing.
These preliminary tests seem to indicate that bonding silicones, exposed to a permanent load and high temperature, may need a replacement in the longer term as the observed changes in properties is larger than 25%. Further testing, including establishing a link between the new double H-bar test and the creep test referenced in ETAG002, should be performed to complete the evaluation of the permanent load resistance after heat exposure.

4. Conclusion
The ability of a bonding sealant to accommodate a useful dynamic load after heat exposure such as smoke or conduction heat (2 h at 180 °C) remains important. Both the bonding and secondary sealants retain 75% of their original mechanical properties (tensile strength, elongation, stiffness). A loss of 25% versus the original mechanical properties observed for this heat exposure is likely acceptable according to the state-of-the-art bonding guidelines. These results suggest that there is no need for direct replacement of bonding sealants after this type of exposure, which could occur in rooms isolated from, but adjacent to a fire. Further evaluation is needed to confirm the permanent load resistance of heat-aged silicones and the need for replacement. As a good level of adhesion is kept until 200 °C, a heat exposed bonding sealant can still provide a major barrier preventing the egress of hot gases.
The study described in this paper has focused on a worst-case scenario whereby small samples were evaluated quickly and fully exposed to the full heat ageing. In building applications, joints exposed to high temperatures of smoke or conduction heat may benefit from the scale effect of the larger structure they belong to. Depending on the system, they may undergo slower heating and lower effective maximum temperature, especially if sprinkler systems are active nearby or if materials in contact act as heat sink, leading the heat away from the silicone bonds.
Additionally, silicone-based materials exhibit sluggish heat transfer. Fire modeling studies (Mazzucchelli 2020; Zhang 2021) of curtain walls exposed to fire, smoke, and high temperature suggest that temperatures at different locations of the curtain wall vary and may be substantially lower in some places, leading to a residual mechanical strength of the sealant, which does not show failure in real fire conditions similar to real fire observations reported in Figure 1. Thermal breaks can further contribute to joint strength retention and control of temperature in the bondline area. Heat barriers created by insulating materials or intumescent coatings can be introduced to minimize the temperature in at least some parts of the bonded area.
In contrast to the promising behavior of silicone, the behavior pattern is quite different if sealants from other chemistry types, e.g., polyurethanes, are considered. The PU sealant evaluated in this study originates from the railway industry, where it is used for the bonding of windows. This material was found to lose not only its mechanical performance but also completely disintegrated upon heat exposure for 2 h at 200 °C. While using this type of chemistry for interior bonding applications without UV exposure may be considered in the future, the presented results evidence the high sensitivity of the PU material to temperature.
This material’s sensitivity challenges the use of this type of chemistry when any risk linked to high temperature exposure needs to be avoided and highlights the importanceof technology choice in façade applications. Indeed, the long-term durability could be affected when exposed to even moderate temperatures, such as 80 °C, which are commonly reached in non-glass façades and thorough experimental evaluation is strongly recommended to validate the application.
Future work includes building a time-temperature plot at 75% tensile strength loss for the various materials to allow easy selection of sealants for their high temperature resistance by the industry and continuing the evaluation of the dead load resistance. Finally, additional research is needed to understand the impact of test variability relative to a statistical relevance, which should include sample replicates, evaluating lot-to-lot variation or influence of mixing ratio. It is important to note that the provided results are only applicable to the evaluated sealants.
Acknowledgements
The authors wish to thank François De Buyl, Pierre Descamps and Frederic Gubbels for the fruitful discussions; the construction lab in Seneffe for the sample preparation and Aurore Arnould for support in performing TGA analysis.
Disclaimers
This information is offered in good faith for your consideration, but without guarantee or warranty (express or implied), as analytical conditions and methods of use of the information and materials described herein may vary and are out of Dow’s control. Although this information is based on data Dow believes to be reliable and accurate we do not intend for you to use, and you therefore should not construe, the contents of this documents as business, technical or any other form of advice. We recommend you determine the suitability of the information and materials described herein before adopting or using them on a commercial scale. Dow assumes no liability in connection with the use of this information.
References
Anderson J. et al, European approach to assess the fire performance of façades, Fire and Materials ;45: 598–608 (2021). https://doi.org/10.1002/fam.2878
Camino, G.; Lomakin, S. M.; Lageard, M., Thermal polydimethylsiloxane degradation. Part 2. The degradation mechanisms. Polymer, 43 (7), 2011-2015 (2002) https://doi.org/10.1016/S0032-3861(01)00785-6
Deng, S.; Hou, M.; Ye, L., Temperature-dependent elastic moduli of epoxies measured by DMA and their correlations to mechanical testing data. Polymer Testing, 26 (6), 803-813. (2007)https://doi.org/10.1016/j.polymertesting.2007.05.003
Descamps, P. et al. in Science and Technology of Building Seals, Sealants, Glazing, and Waterproofing: 3rd Volume, 95-106 (1994)
EOTA, ETA 13/0281, DOWSIL™ Firestop 700 (2017)
ASTM D4065-1 Standard Practice for Plastics: Dynamic Mechanical Properties: Determination and Report of Procedures(2017)
EC, EN ISO 11925-2:2020, Reaction to fire tests - Ignitability of building products subjected to direct impingement of flame -Part 2: Single-flame source test (2020)
EC, EN 12101- 1: 2005 - Smoke and heat control systems. Specification for smoke barriers (2005) fire resistance tests, excluding ventilation services (2007)
EC, EN 1364-3:2014 Fire resistance tests for non-loadbearing elements. Curtain walling - full configuration (complete assembly) (2014a)
EC, EN 1364-4:2014, Fire resistance tests for non-loadbearing elements. Curtain walling. Part configuration (2014b)
EC, EN 1366-3: 2009. Fire resistance tests for service installations. Part 3. Penetration seals (2009)
EC, EN 1366-4 :2006+A1:2010, Fire resistance tests for service installations. Linear joint seals (2010)
EC, EN 13823:2010, Reaction to fire tests for building products - Building products excluding floorings exposed to the thermal attack by a single burning item (2010)
EOTA, ETAG002 Guideline for European technical approval for structural sealant glazing kits (2012)
Gioia, C.; Colonna, M.; Tagami, A.; Medina, L.; Sevastyanova, O.; Berglund, L. A.; Lawoko, M., Lignin-Based Epoxy Resins: Unravelling the Relationship between Structure and Material Properties. Biomacromolecules, 21 (5), 1920-1928 (2020) https://doi.org/10.1021/acs.biomac.0c00057
Hu, L. H.; Huo, R.; Li, Y. Z.; Wang, H. B.; Chow, W. K., Full-scale burning tests on studying smoke temperature and velocity along a corridor. Tunnelling and Underground Space Technology, 20 (3), 223-229 (2005)https://doi.org/10.1016/j.tust.2004.08.007
ISO 527-1:2019, Plastics — Determination of tensile properties — Part 1: General principles (2019)
ISO 8339: 2005, Building construction — Sealants — Determination of tensile properties (Extension to break) (2005)
Li, D.; Zhu, G.; Zhu, H.; Yu, Z.; Gao, Y.; Jiang, X., Flame spread and smoke temperature of full-scale fire test of car fire. Case Studies in Thermal Engineering, 10, 315-324. (2017)
Li, Y. Z.; Lei, B.; Ingason, H., The maximum temperature of buoyancy-driven smoke flow beneath the ceiling in tunnel fires. Fire Safety Journal, 46 (4), 204-210 (2011)
Mazzucchelli E.S., P. Rigone, B. J. de la Fuente Ceja, P. Giussani, Fire Safety Façade Design and Modelling, Journal of Facade Design and Engineering 8(1):21-42 (2020) DOI: 10.7480/jfde.2020.1.4703
Narducci, R.; Chailan, J. F.; Fahs, A.; Pasquini, L.; Di Vona, M. L.; Knauth, P., Mechanical properties of anion exchangemembranes by combination of tensile stress–strain tests and dynamic mechanical analysis. Journal of Polymer Science Part B: Polymer Physics, 54 (12), 1180-1187 (2016)
Shi, W. X.; Ji, J.; Sun, J. H.; Lo, S. M.; Li, L. J.; Yuan, X. Y., Influence of fire power and window position on smoke movement mechanisms and temperature distribution in an emergency staircase. Energy and Buildings, 79, 132-142 (2014)
Starr, J. W.; Lattimer, B. Y., Evaluation of Navigation Sensors in Fire Smoke Environments. Fire Technology, 50 (6), 1459-1481 (2014)
Tomer, N. S.; Delor-Jestin, F.; Frezet, L.; Lacoste, J., Oxidation, Chain Scission and Cross-Linking Studies of Polysiloxanes upon Ageings. Open Journal of Organic Polymer Materials, 02 (02), 13-22 (2012)
Approved Document B (fire safety) volume 2: Buildings other than dwellings, 2019 edition, ISBN 978-1- 85946-916-3 (2019)
UAE Fire and Life Safety Code of Practice, (2018), https://www.dcd.gov.ae/portal/en/preventive-safety/rules-regulations/uae-fire-and-life-safety-code-of-practice.jsp accessed December 2021
Wolf A.T., Recknagel C., Sitte S., Structural Silicone glazins: life expectancy of more than 50 years?, Conference Proceedings - Glass Performance Days 25th anniversary, pp 338-345 (2017)
Yao, Y.; Cheng, X.; Zhang, S.; Zhu, K.; Zhang, H.; Shi, L., Maximum smoke temperature beneath the ceiling in an enclosed channel with different fire locations. Applied Thermal Engineering, 111, 30-38 (2017).
Yi, X.; Lei, C.; Deng, J.; Ma, L.; Fan, J.; Liu, Y.; Bai, L.; Shu, C.-M., Numerical Simulation of Fire Smoke Spread in a Super High-Rise Building for Different Fire Scenarios. Advances in Civil Engineering 2019, 1659325 (2019)
Zhang T., Di Cao, "Simulation Study on the Influence of Fire Partition on Curtain Wall Temperature in Super High-Rise Buildings in China", Complexity, vol. 2021, Article ID 4124049, 16 pages (2021). https://doi.org/10.1155/2021/4124049