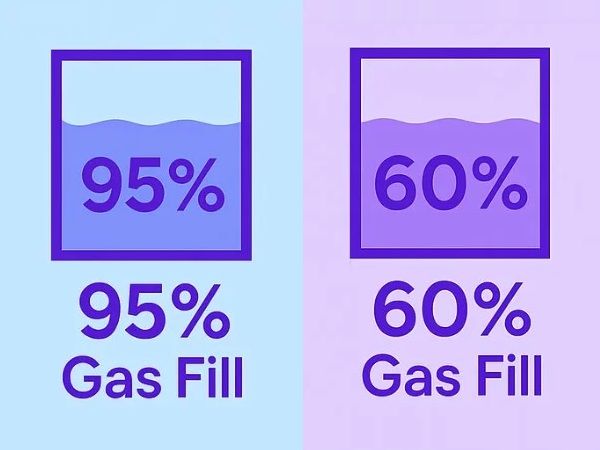
Date: 9 April 2025
Accurate measurement with argon tester and strict quality control are essential components in the production of high-quality insulating glass units (IGUs). As industry standards become increasingly stringent, manufacturers and suppliers must employ reliable methods to ensure product quality and performance. This case study involving two UK-based companies demonstrates the critical importance of precise gas measurement and proper calibration in maintaining consistent product quality.
The Story
A small glass manufacturing company reached out to our distributor for a demonstration to find out if there are inconsistencies in the insulating gas content of their IGUs. Producing around 20-30 IGUs per day, the company also sources an additional 200 units weekly from a larger supplier. As part of the demonstration, the company conducted gas content testing on both their own products and those sourced from their supplier.
The self-produced IGUs had consistent gas content levels of 88-95%, confirming adherence to their internal quality standards. However, the gas content levels of the purchased units showed significant deviations, measuring only 60-65%. This discrepancy raised concerns and prompted the company to address the issue with their supplier.
Taking Action
Using data gathered from Sparklike Handheld gas measurement device, the smaller manufacturer brought the issue to the attention of their supplier. As a result, the supplier has returned both of their own Handheld devices for calibration—one of which had not been calibrated since 2012 and the other since 2014. This incident highlights the necessity of quality control routine and calibration and maintenance to ensure the continued accuracy of gas measurement devices. Read Why Calibrate and Service Your IGU Quality Control Equipment Annually.
The Impact
Following this discovery, the smaller company is now looking to invest in its own argon tester, Sparklike Handheld, to maintain full control over the quality of its production.
Lessons Learned
Accurate Measurement is Critical: This case underscores the importance of precise gas measurement in maintaining consistent product quality. Even small deviations in gas content can indicate potential quality issues.
Regular Calibration is Necessary: Gas measurement devices require regular calibration to ensure they provide accurate readings. Neglecting calibration can lead to incorrect measurements and ultimately compromise product quality.
Proactive Quality Control: By implementing robust quality control measures and using reliable equipment, manufacturers can build trust and accountability across the supply chain. This approach not only benefits the manufacturer but also their suppliers and customers.
Reputation Risk Cannot Be Ignored: Poor quality control has broader consequences beyond defective products. In this case, the supplier’s reputation suffered when their customer identified inconsistent gas fill rates. Once a customer finds a quality issue, trust is damaged, and this can result in lost business opportunities or strained partnerships. Maintaining a strong reputation requires ongoing commitment to quality control and transparency throughout the production process.
Conclusion
This case study serves as a reminder that ensuring the quality of insulating glass units requires the right tools and processes. Regular gas content measurement and device calibration are key factors in achieving consistent quality and maintaining compliance with industry standards. Whether a small manufacturer or a large supplier, accurate measurement practices are fundamental to delivering products that meet customer expectations and regulatory requirements.
Contact us to learn how Sparklike devices can streamline your quality assurance.


Add new comment