Article Information:
- Digital Object Identifier (DOI): 10.47982/cgc.9.652
- Published by Challenging Glass, on behalf of the author(s), at Stichting OpenAccess.
- Published as part of the peer-reviewed Challenging Glass Conference Proceedings, Volume 9, June 2024, 10.47982/cgc.9
- Editors: Christian Louter, Freek Bos & Jan Belis
- This work is licensed under a Creative Commons Attribution 4.0 International ( CC BY 4.0) license.
- Copyright © 2024 with the author(s)
Authors:
- Rianne Teeuwen - Delft University of Technology, Faculty of Civil Engineering & Geosciences
- Roel Schipper - Delft University of Technology, Faculty of Civil Engineering & Geosciences
- Jagoda Cupać - Technische Universität Dresden, Institute of Building Construction
- Hans Jansen - Permasteelisa group, Scheldebouw
- Christian Louter - Delft University of Technology, Faculty of Civil Engineering & Geosciences
Abstract
This article presents the metric avoided carbon for the reuse of aluminium unitised curtain wall façades, that are to be taken from a donor building and applied onto a receiving building. The metric is used to compare seven proposed circular reuse strategies, each showing a different level of reuse. Based on literature and reference studies, we identify those parts of the façade where reuse has the most impact and is technically feasible. The seven reuse strategies and the avoided carbon method are applied on a real case study building as donor project and a fictitious building as receiving project. We conclude that reuse is technically feasible, saves carbon, and that the proposed metric can help to incentivize building owners and project developers to adopt circular reuse.
1.Introduction
1.1. Circularity of façades: relevance, challenges, and scope
Material scarcity and climate change urge us to consider the potential environmental gain of the reuse of façades of buildings (CWCT, 2023; Lapido, 2022, Hartwell and Overend, 2019 and Fink, 2011). This article summarises a master’s thesis research (Teeuwen, 2023), focusing specifically on circular reuse of unitised aluminium curtain wall façades. Curtain walls are a façade typology often used for large commercial office buildings in urban areas around the world. In this article, we want to focus on two aspects from the thesis: firstly the technical challenges of reusing materials and components of existing façades, and secondly, the introduction of a useful metric to correctly account for and compare between reuse scenarios.
Technical challenges are, among others, the limited detachability of components and materials, the often outdated functional performance of existing façades (e.g. with respect to insulation values, airtightness) and the potential (mis)match between donor and receiving building. Finding a correct metric to measure the effectivity of reuse is equally challenging, as the present LCA-based methods are ambiguous due to the possible double-counting of environmental gains and unclarity how to account future reuse scenarios as a result of its linear rather than circular accounting method. Calculating the avoided carbonappears to be a fair and practical metric, as we will see later.
Due to scope limitations, other relevant aspects covered by the thesis are not discussed here, such as warranty, business case, logistics, connections, and quality and condition of the existing façade. The main research question we tried to answer is: “What strategies can be developed to increase the circularity of unitised aluminium curtain wall façades?”
1.2. Research methodology
The thesis research was conducted using a mixed-method approach: first a state-of-art study was conducted (section 2), by literature survey of scientific and professional publications, but also by interviews with professionals in façade industry. Four recent reference projects in which circularity principles had been applied were studied in detail, partially by a site visit, partially by studying the available project documents, and by interviewing people closely involved in the projects. As a next step and based on the knowledge gained by this reference project study, a set of eight generic reusescenarios were developed (section 3) for use in future projects, each with increasingly positive potential impact. To objectively measure this impact, traditional LCA was used plus a self-developed metric avoided carbon, introduced to better account for circular principles than LCA can. Finally, a test case was selected to verify the developed eight-scenario approach and to assess the “avoided carbon” method (section 4). The test case also served to identify possible unclarities and required future improvements (section 5).
2. State of art in aluminium curtain wall façades and their reuse
2.1. Literature on impact of façades and reuse strategies
The building sector contributes approximately 40% of the global energy demand and up to 50% of the raw material use (Fink, 2011 and Kubbinga, 2018). When looking at the overall embodied carbon impact of a building, the façade has a share of approx. 19% (Caroll, 2021 and Achterberg, 2016). These numbers justify close attention to the environmental impact of façades. Governments have expressed the objective to achieve a fully circular economy by 2050, which should reduce virgin material use, carbon emissions and waste. However, reuse of façades or façade components until now is exceptional. In structural engineering, already more examples can be found of reuse: concrete and steel structures from donor buildings have been reused in new buildings and bridges. Lessons from these projects are useful for façade engineering.
The concept of the Value Hill (Achterberg, 2016) illustrates the circular utilisation of materials and emphasises their value preservation. The Value Hill distinguishes five levels, with decreasing degree of material value: 1) reuse, 2) repair/maintain, 3) refurbish, 4) re -manufacture and 5) recycle.
In their framework for circular building strategies, Metabolic (Kubbinga, 2018) describes four pillars:
- Reduce: avoid or reduce the use of virgin materials and always certify possibilities for future reuse
- Synergise: combine and coordinate activities, preserve what is already made, do not aim for single-solution choices.
- Supply: keep resources as clean, renewable, recycled or beneficial as possible
- Manage: knowledge about when and how resources have been used is crucial; keep track of material flows, certify data transparency. The five Value Hill levels and the four pillars have been helpful in the further development of the strategies presented in this research.
Various studies have been conducted on the life span of façades and of façade components. Brand (1994) already recognised that different layers of a building may have very different service lives, ranging from 1-5 year (for “stuff”), 50 years (for “skin”) to 100 years (for “structure”). 50 years for the skin seems over-optimistic, as often the functional service life appears shorter than the technical service-life. This is illustrated by multiple cases where Scheldebouw, the industrial partner involved in this research, was asked to replace a façade they themselves manufactured and installed only 20 or 30 years ago, while technically it still was in good condition.
Hartwell & Overend (2019) distinguish quite different technical lifespans for various components within the façade, ranging from 10-15 years (mechanisms, motors, ironmongery), 20 years (external gaskets, sealing), 25 years (thermal insulation, anodised finish of aluminium), 30 years (insulating glazing units (IGUs), panels, structural glazing sealants) up to 60 years (cladding system structural framing, steel, bracketry and fixings). These estimated lifespans imply that full façade replacement after 20 to 30 years will leave much latent value unused of components that are still in good shape.
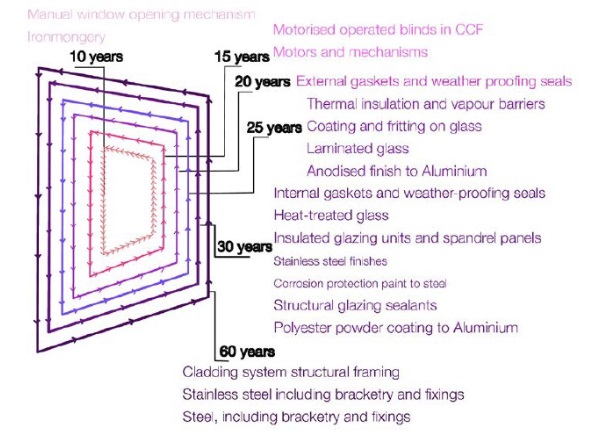
We will see in section 2.3 that especially the aluminium frames, steel parts and IGUs embody much carbon footprint, and that circular reuse opens a potential of significant carbon savings. In section 2.2 we will first address existing ways to measure circularity.
2.2. Existing metrics to measure and appreciate circular reuse
To enforce operational energy efficiency, many countries already have legal instruments in place for some decades. Various methods have been developed to stimulate and reward a broader take on sustainability performance of construction projects: for example, BREEAM and LEED are certification systems that, apart from energy use, also cover aspects as location in relation to car use, water and material use, waste management, indoor air quality and various ecological aspects of a building and of the building site. The required quality level, however, is not enforced legally, but driven mostly by the market incentives, for example the added property value that a certificate brings.
Aware of material scarcity, and to reduce strategic dependability on other countries and to diminish environmental impact, governments are gradually introducing legal instruments to restrict virgin material use. For example, in the Netherlands, calculation of the Environmental Cost Indicator (in Dutch: MKI) as described in the code NEN-EN 15643 (2021) is already compulsory for 12 years, although the maximum target values of the calculation have been enforced only recently. MKI is an LCA-based monetising method that expresses the environmental impact in 19 categories as one single financial value (€ per m² gross internal floor area), also named the “shadow costs”. Dutch government intends to legally restrict and gradually lower the target MKI-values over the coming years.
The abovementioned methods, however, are all quite open to variable interpretations on how to exactly weigh a second or third life of reclaimed (façade or other) materials, as the life stages A on the one hand and stage C and D on the other hand, in a circular process become intertwined.
Finally, it is also challenging how to exactly reward or penalise the (in)suitability of a present façade solution for future circular reuse. For example, glued or welded components will be harder to reuse or separate than bolted or screwed components. To this end, and inspired by regulations for consumer goods, detachability or design for disassembly and adaptability (DfD/A) metrics have been proposed (Circular Buildings - Meetmethodiek Losmaakbaarheid, 2019 and NEN-ISO 20887, 2020), that express the degree of ease to adapt, repair or take apart components. For façades, the development of this metric is still in a very early stage. Let us first look at which components of the façade are most effective to reuse in terms of carbon footprint.
2.3. Aluminium curtain wall façades: components and carbon footprint
From a sample of three mainstream commercial office projects consisting of in total six unitised curtain wall façades, the following components and materials were found to be commonly used: framing (aluminium extrusion profiles, thermal breaks), infills (structurally bonded IGUs, dry placed IGUs, insulation materials, panel constructions), elements connecting to structure (steel brackets, fire-stoppers) and additional elements (shading, decorative elements). From the sample the normalised average weight (kg/m²) and carbon impact (kgCO₂eq per 1 m²) of the contributing materials were determined. Extruded aluminium, glass, steel and aluminium sheet and brackets together formed the majority of the weight of the envelope systems (85%) and also of the embodied “upfront” carbon impact (75%, LCA stages A1 to A5). While in weight-percentage glass is contributing more than twice as much as the aluminium (on average 38 kg/m² = 45% glass vs. 18 kg/m² = 21% aluminium of the total weight 84 kg/m²), in terms of carbon impact the opposite is the case (152 kgCO₂eq/m² = 43% for aluminium and 76 kgCO2eq/m2 = 22% for glass of the total average 350 kgCO2eq/m²). Steel sheets and brackets together take the third place, both in weight (13 kg/m²) and in carbon impact (32 kgCO₂eq/m²). Although the sample size was limited and variation between the different projects relatively large, the proportional dominance compared to the other materials used justifies close attention to the reuse of aluminium, glass and steel when upfront carbon is used as environmental criterion. Fig. 2 below illustrates the relatively large impact of these three materials in all six façades in the sample:
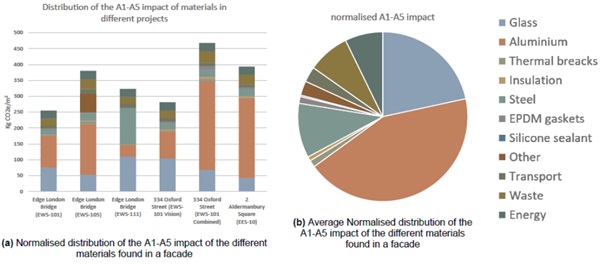
2.3. Reasons for replacing façades
In order to understand the reuse potential of façade components, it is necessary to understand why complete façades become outdated. Hartwell and Overend (2019) mention:
- Volatility in office demand: change of occupant or of function can lead to changes in requirements;
- Aesthetic requirements: a new appearance or character of the building is desired by the owner;
- Increased energy efficiency requirements for glazing, panels, and frames: if operational costs become too high or legislation is tightened, replacement can be beneficial to improve performance;
- Issues with parts or components: breaches of air- or watertightness, building physics performance, structural issues, glass breakage.
It is expected that many of the (remaining) elements within the façade could still meet requirements and can be reused with or even without refurbishment.
2.5. Literature example projects of reuse and reference case studies
Seven examples of whole or partial façade reuse were analysed. From literature, Lloyd’s London, Empire State Building NY, Commerzbank Tower Düsseldorf were studied. Information about 1 Triton Square London, Koningskade The Hague, Citibank London, and De Satelliet Amsterdam was made available by façade consultants or contractors. All examples from practice show the reuse potential of various façade parts. Components like IGUs have been seen to exceed their original expected life span. Upgrades were applied such as the IGU remanufacturing in the Empire State Building or cleaning of steel façades in the Commerzbank Tower.
In spite of the potential, also challenges appeared present in the example buildings. When materials and components are not reapplied in the original façade, determining or finding a donor building is crucial for successful reuse. Examples like Koningskade and 1 Triton Square, where a suitable donor building was found, showed a challenging yet successful outcome. However, in the projects Citibank and De Satelliet difficulties arose when having to design with existing façade elements and ensuring safety and warranty for the reused or refurbished façade. Lessons from the literature and reference studies are:
- Components exceed their expected lifespan
- On- and off-site testing was used to estimate the remaining value
- Original stakeholders and access to original drawings proved beneficial
- Projects without a receiving building are difficult to complete
In the next section we will look at which parts of the façade have the greatest reuse potential and impact, and how to fairly quantify that impact.
3. Development of circular strategy and fair accounting method
3.1. Technical challenges and opportunities regarding reuse
Based on the lifespans mentioned in Hartwell and Overend (2019), on the calculations from subsection 2.3 and on interviews with façade specialists, the information in table 1 below was collected.
Table 1: CO₂ potential, demountability and usefulness.
Table 1 helps to identify those parts of the façade where potential and practical possibilities for reuse coincide. The parts in italics can be considered to have either a low potential, or limited practical demountability or both, and will be neglected here. Aluminium and steel parts have high potential and are practically demountable and reusable. For glass and IGUs the potential is high, but the practical challenges are bigger than for steel and aluminium.
3.2. Life-cycle Analysis and possible ambiguities
Fig. 3 shows the LCA-stages from NEN-EN 15643:
Accounting with LCA has ambiguities and allows for potential (unintentional) greenwashing in a situation of circular reuse for the following reasons:
- “Foretelling the future”: for the donor building, stages C and D can be accounted for based on plans rather than on reality. This would result in a free discount, as there is no guarantee of real environmental gains.
- “Double-accounting”: In the receiving building, the reuse of components from a donor building can be accounted for again in stage A, while they may have already been accounted for in stage D of the donor building at the time of design of that donor building.
- Halfway interventions are hard to implement (e.g. replacement of glass)
LCA therefore is more suitable for a linear scenario, and is not deemed fully “watertight” for use in a circular economy scenario.
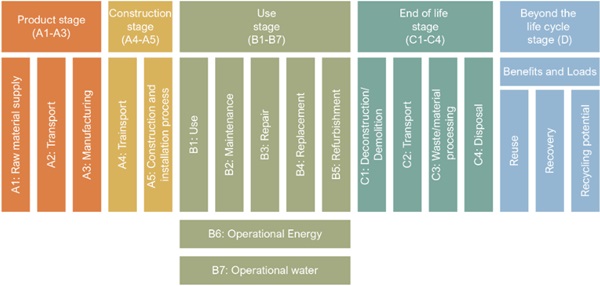
3.3. Avoided carbon method as addition to LCA for accounting circularity
In order to account for the circular use of products in a fair manner, a new method called the avoided carbon methodwas developed in this research project. The method does not use LCA stage D, it rather accounts for the avoided carbon emissions by not wasting materials or not having to extract raw materials. The avoided carbon method includes the circular use of materials in a fair and transparent manner. The method was developed by looking at existing circular projects and the route of the materials that were circularly used in those cases (Fig. 4 on the following page), as well as regarding the original methods of the LCA and finding their shortcomings. The standard LCA is used as a base layer of these calculations, and the definitions of the stages and impacts are still used. In standard new built (linear) projects, the LCA shows its ultimate potential. However, when circular strategies come into the picture, the standard LCA does not allocate the benefits and loads in a fair manner.
The avoided carbon method in essence encompasses a comparison between a traditional linear scenario and a circular scenario, and estimates all carbon emissions that will be avoided by a more circular reuse or recycling scenario. When looking at circularity, always two projects are involved: the Donor building and the Receiving building. At the moment of the intervention, the donor building or its components are at the end of their service life, so the avoided carbon method starts at the End-of-Life stage (C) of the donor building, where the demolition or dismantling, transportation and waste processing impact are attributed. Benefits are achieved by avoiding these impacts, due to the materials being used instead of raw materials for the receiving building, which avoids the landfill and transportation of these materials. Next, the LCA starts over in the product stage (A), where the benefits made by avoiding raw material extraction, transportation and manufacturing are allocated. This is graphically represented in Fig. 4, where an ideal (100%) reuse situation is simulated. In this case, the combined impacts in the End-of-Life phase of the donor building and the Product stage of the receiving building are fully avoided.
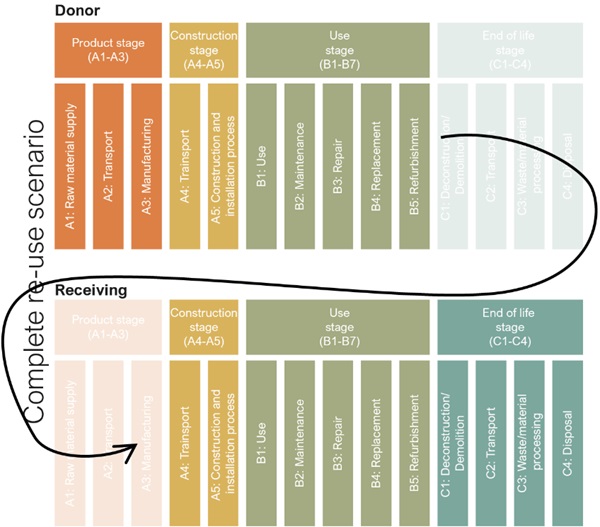
3.4. Seven reuse strategies
Next, seven strategies are identified, see Fig. 5. The impact of each of the seven strategies has been calculated using the “avoided carbon” method for a real donor building and a fictitious receiving building. In Strategy 0: Refuse, the objects are upgraded in their original location, so no dismantling takes place and the materials stay in their original locations where they have the best fit. The carbon impact which is made in this strategy is attributed to stage B, and remains outside of the scope of this calculation. Next, in the ‘Panel Strategies’ – Strategy 1: Direct Reuse, Strategy 2: Panel Refurbishment and Strategy 3: Panel Remanufacturing – it is assumed that the panels can be adjusted to their new function in a new building with no or minor interventions. The waste of the materials that are reused, are avoided as well as a large part of the raw material demand of the receiving building. The impact varies with the level of intervention and the level of replacements. Next are the ‘Component Based Strategies’ – Strategy 4: Component reuse and Strategy 5: Component refurbishment – where the panel is dismantled into components, which can be reused individually, like the framing or the glazing component. An arbitrary assumption behind the calculation below was done that half of the materials (50%) can be reused in these strategies. More waste is generated, however still a significant amount of raw material impact can be saved. Lastly, the ‘End-Of-Life Strategies’ include Strategy 6: Recycling and Strategy 7: Waste. Significant differences can be seen for impact of the donor building between a waste or a recycling scenario. kg CO₂eq/m² is used as unit, while all values are harmonised to 1 m² of façade and distributed over the LCA stages A to C. The more positive the value of the avoided carbon is, the better the reuse strategy from the perspective of carbon emission.
The difference in total length between the coloured bars in Fig. 5 yields the avoided carbonof the receiving and donor building combined when comparing two scenarios. For example, if the worst case scenario is Strategy 7 (putting all materials to waste, impact > 400 kgCO₂eq/m²) and a better scenario is Strategy 4 (50% component reuse, impact ≈ 200 kgCO₂eq/m²), the avoided carbon of both projects combined when selecting Strategy 4 rather than Strategy 7 is 400 – 200 = 200 kgCO₂eq/m².
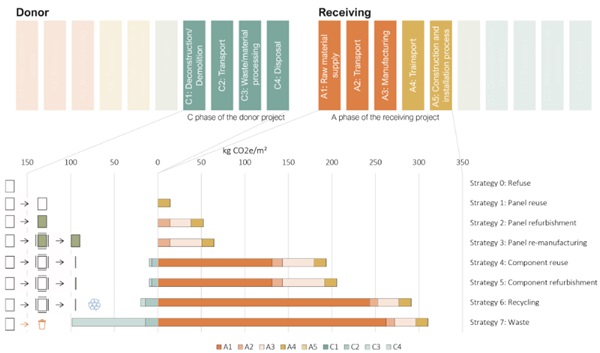
4. Application of the developed strategies on a test case
To be able to show the application of the avoided carbon method, a case study was performed. The project in which the method was applied is the case of Citibank, where various floor levels will be upgraded, because of the desire for a new character for the building. This means that the façade panels will be replaced. The façade’s age at the time of dismantling is 22 years and still holds a significant amount of remaining values visible in Table 1. Some components would need replacing; however, the main components could still act as a façade in a new project. Together with the professionals at the façade manufacturer involved, upgrade options with varying interventions have been developed. Comparing these with a more traditional recycling or waste strategy, the benefits regarding reuse become evident. Four of the eight presented scenarios from Fig. 5 have been used. For each of these options, a short description is given in Table 2.
Table 2: Overview of the options generated for the Citibank case and their strategy.
The results from the avoided carbon method calculations are shown in Fig. 6 below. For this figure, the impact of the C phase for the donor building and the A phase of the receiving building were calculated using the method described above. It can be concluded that by avoiding the impact by not wasting, or by not having to produce new materials significant CO₂ savings can be achieved compared to a waste scenario.
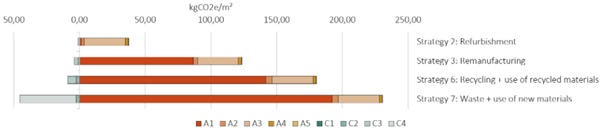
5. Conclusions and recommendations
5.1. Conclusions
In this paper the challenges and opportunities associated with the circular reuse of unitised aluminium curtain wall façades were investigated, addressing both the technical challenges as well as the development of a fair metric for accounting the loads and benefits of reuse in terms of CO₂ emissions.
Through a mixed method approach composed out of a literature review, reference studies, the strategy development and a case study application, the key potentials and challenges were identified. The existing LCA-methods, while valuable, were found to be insufficient in accounting for circularity.
The avoided carbon method was developed as a complementary metric to the LCA, with the main goal of transparently accounting benefits to each of the phases involved. It is a fair method, which improves its usability as incentive for building owners and project developers to start implementing reuse strategies.
The study outlined seven reuse strategies ranging from simple refurbishments to remanufacturing. The application of these strategies to the case study, the Citibank, showcased the potential of reuse in reducing both raw material use and material waste.
In conclusion, this research provided insight to improve the circularity of the façade industry, particularly the circularity of existing unitised aluminium curtain wall façades, to the end of reducing landfill and resource depletion, while also retaining the value of the components involved. Strategies were developed that provide a framework for achieving a more sustainable and environmentally aware façade sector as well as to encourage building owners and project developers to start implementing circularity in their projects. These strategies were proven to be more beneficial in terms of carbon than a traditional waste scenario.
5.2. Recommendations
Development of testing methods for refurbishment and remanufacturing are required to locate and quantify potential and risks. Recent developments on upgrading used IGUs (Empire state Building, Booosting) show high potential of Strategy 0. Testing of the remaining quality of components, such as glazing, thermal breaks and coatings may open up further potential and reuse possibilities.
Incentives - Creating a fair and transparent method of monetising circularity will help to avoid green washing while it also provides project owners or advisors with a tool to showcase the benefits of reuse. Since reuse is still paired with risks, unknowns, and often more costly than a new product, the carbon reduction has to show the benefit.
In addition to the financial and technical feasibility of circularity it appeared that transportation, storage, and labour-intensive applications still are very costly and threaten the business-case of circular reuse of façades.
References
CWCT. A brief introduction to ‘How to calculate the embodied carbon of façades: A methodology’ https://www.cwct.co.uk/products/a-brief-introduction-to-how-to-calculate-the-embodied-carbon-of-façades-a-methodology, last visited April 2024 (2022)
Ladipo, T., Facing up to embodied carbon in façades, CIBSE Journal, https://www.cibsejournal.com/technical/facing-up-to-embodied-carbon-in -façades last visited April 2024, (2022)
Hartwell, R. & Overend, M. Unlocking the Re-use Potential of Glass Façade Systems. in All Eyes on Smarter Glass – Glass Performance Days 2019, 273-280 (2019)
Fink, H. S. Promoting behavioral change towards lower energy consumption in the building sector. Innovation: The European Journal of Social Science Research 24, 7–26 (2011)
Teeuwen, R. Circularity of existing aluminium unitised curtain wall facades, MSc Civil Engineering Thesis, TU Delft, http://resolver.tudelft.nl/uuid:70fbb8c7-e41d-4259-952e-c06ca5655c38 (2023)
Kubbinga, B. et al. A (Metabolic) Framework for Circular Buildings - Indicators for possible inclusion in BREEAM. Preprint at https://www.metabolic.nl/publications/a-framework-for-circular-buildings-breeam (2018)
Thelen, D. et al. (WBCSD) Scaling the Circular Built Environment - pathways for business and government. Preprint at https://www.wbcsd.org/contentwbc/download/6173/85923/1 (2018)
Caroll, C. et al. (WBCSD) Net-zero buildings: Where do we stand? Preprint at https://www.wbcsd.org/contentwbc/download/12446/185553/1 (2021)
Achterberg, E., Hinfelaar, J.& Bocken, N. Master Circular Business with the Value Hill. Preprint at https://hetgroenebrein.nl/wp-content/uploads/2017/08/finance-white-paper-20160923.pdf (2016)
Brand, S. How buildings learn: What happens after they’re built, Viking Press, NY (1994)
Comments
Seven suggested circular reuse strategies—each demonstrating a varying degree of reuse—are compared using the measure. We determine the areas of the façade where reuse has the most impact and is technically possible based on reference studies and literature.