First presented at GPD 2017
Contemporary architectural designs of transparent building skins with curved geometries challenge the industry. Approaches using geometry rationalization in combination with planar glazing, cold bent glazing or tempered hot bent curved glass are coupled with geometry constraints and are not always architecturally desired. Hot bent annealed glass opens up additional freedom in design, especially biaxial and more curvature in the building skin’s glazing.
The paper will provide an overview of the currently applied engineering approach in the industry for curved hot bent glass in the absence of standards and codes. Design specifics of hot bent annealed glass applications will be highlighted and test results shown. It is an experience report of how innovative annealed curved glass applications can be realized with the currently available knowledge of research projects, engineering tools and project specific testing.
2. The need of hot bent annealed glass
Within the last years the façade industry is faced with the trend of curved building envelopes. Especially geometrically complex feature elements of buildings are predestined applications of curved glass with the intention to create unique and transparent enclosures (Figure 1 & 2).
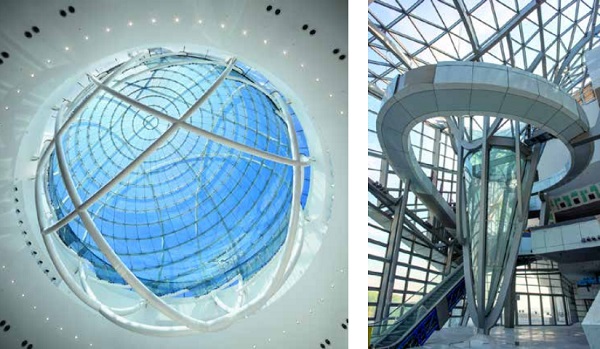
Figure 2 (right) Free-formed hot bent annealed glass, Museé des Confluences, Lyon (France) ©Karin Jobst
Even if recent technologies provide a broad range of opportunities to resolve curved envelopes, the use of hot bent annealed glass is essential to create extreme curvature as shown by the following limitations and approach-specifics:
1) Tempered curved glass: The overall glass sizes and producible radii are generally limited by the production process. Cylindrical curved glass is producible as heat strengthened glass and fully tempered glass if the radii are not too small (typically R>1000mm) and if the bending angle does not exceed certain limits [1].
Meanwhile double curved glass can also be produced as thermally tempered glass for large scale radii by few suppliers. The tempering process of curved glass products can be realized by adjustable rollers. Nevertheless, quenching and temperature control poses an increased difficulty to the production process compared to flat glass products.
Therefore, geometry and size limitations should always be verified in close collaboration with the glass supplier. Local distorsions through processing reduce the visual glass quality which is mostly lower compared to annealed curved glass. Soft coatings and frits are typically solely feasible on the concave surface of curved tempered glass products (hard coatings also on the convex surface).
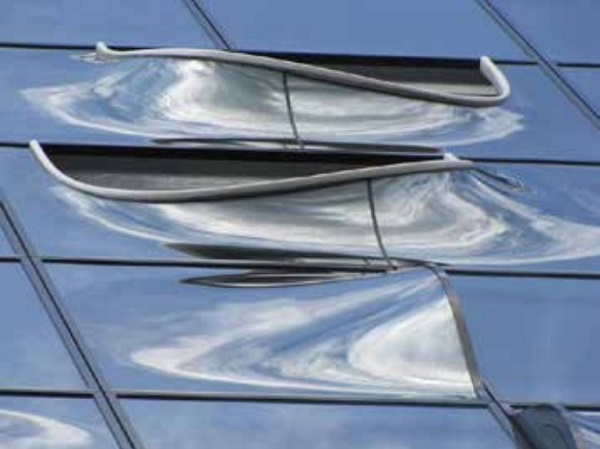
2) Cold Bending (including cold warping): Typically planar tempered glass panes will be forced in the required shape on site. The bending process causes additional constraints in the glass built-up; consequently only low curvatures can be achieved (Figure 4).
The degree of bending is either limited by additional long term stresses introduced in the glass, the mechanical and tightness properties of the deformed edge seal in case of insulated glass units or by the mechanical properties of interlayer connections in the case of glass laminates. Additionally, geometry and stability effects need consideration using the cold bending approach.
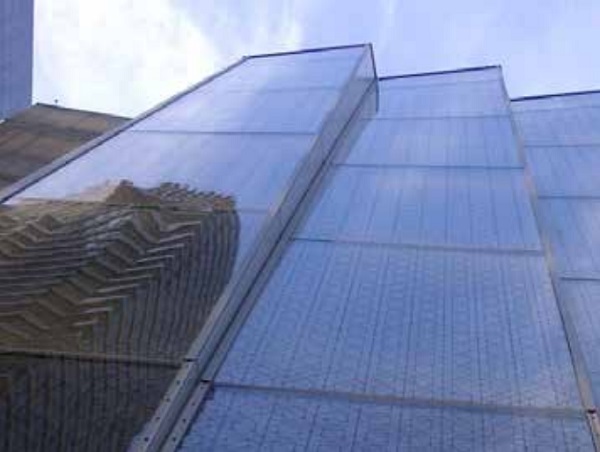
Manufacturing of cold bending during lamination is a technology which also allows only for low-curvature glass [2] and is a factory-made product compared to cold bending on site. Due to the technological complexity (e.g. spring back effect after cold bending and lamination) the amount of suppliers is limited.
The feasible degree of curvatures of both cold bending technologies, on site or factory-made, is within the same range. The major benefits of cold bending approaches are the high optical quality and the freedom of feasible glass configurations (frit, coating, etc.). General producibilty limitations are similar compared to flat glass products.
3) Geometry Rationalization and Methods of Form Finding: Typically the approaches are applied to approximate and simplify the given curved geometry, to transform double-curved glazing elements into single curved or planar glazing elements. In the context of big scale projects those method are essential due to their economic impact. However, the methods imply geometry and mesh modifications which are occasionally in conflict with the envisioned design intent and not desired for feature façade elements.
Chemically strengthened glass should also be mentioned at this point, although it is currently still a niche product within the building industry. The penetration of chemical tempering process affects only a very thin layer; consequently chemically strengthened glass is very sensitive to scratches and should be protected by adequate measures.
All the before mentioned boundary conditions require consideration while finding reasonable project-specific approaches for curved geometries. The nearly limitless freedom in shape (spherical, paraboloid, hyperboloid, etc.), especially bending along several axes are the driver to apply hot bent annealed glass products (Figure 3 & 5).
However, a high visual quality is also achieved by omitting quench marks and distorsions known as drawbacks from the tempering process. Additionally, the gravity bending production process of annealed glass in moulds allows bending in couples. The result is that several curved glass panels fit perfectly together (also different glass thicknesses).
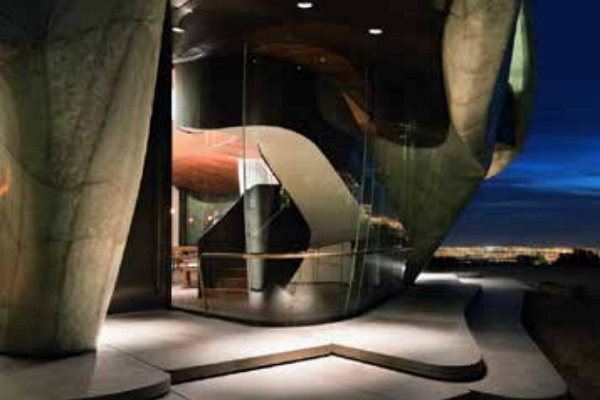
Given the brittle failure behavior of hot bent annealed glass, the whole design, fabrication and installation process requires special attention and a holistic approach. The complexity is increased by the absence of product standards respectively application standards. Fundamental aspects and findings experienced in the last Josef Gartner projects with the product are explored in the present paper.
![Figure 6 Edge Stresses spherical curved laminated glass (hot bent annealed) under thermal loading ∆T [6]](/sites/default/files/inline-images/Fig6_46.jpg)
![Figure 7 Microscopic view of failure origin [6]](/sites/default/files/inline-images/Fig7_39.jpg)
3. Approach to hot bent annealed glass
3.1 Design & Engineering
The structural behavior of curved glass elements differs tremendously from flat glass elements. Arching and membrane effects are triggered without previous deflections under loads [3]; creating very stiff and deformation resistant elements.
However, the edges of curved glass elements are mostly prone to the main tensile stresses. The load paths are very similar to non-membrane elements respectively structural glass elements, for instance, in the case of a spherical curved annealed glass panel. Figure 6 shows the main tensile stresses at the free glass edges, an area with limited strength caused by edge flaws and the lack of residual compressive stress. Edge flaws are caused by edge processing and other mechanical damages during the life time of such glazing elements.
Depending on the stress distribution, the edges of curved annealed glass are often the origin of fracture [4] as shown in Figure 7. The critical flaw initiates failure by propagation of an initial crack under tensile stresses [8]. The context of dealing with structural glass elements combined with the low strength of annealed glass products indicates already the evidence for special attention. Matters are complicated by the fact that currently most frequently used design methods (DELR and GFPM) do not provide verification formats for edge strength under in-plane loads [9].
Additionally, the actually existing edge flaw population is not considered in those methods. Even if using current standards, there is a lack of information on the material resistance side. The face surface strength and the edge strength of curved annealed glass are insufficiently documented in recently applied standards.
However, the “Guidelines for Thermally Curved Glass” (Bundesverband Flachglas) [10] provide recommendations for reduced characteristic strength values underneath other fundamental orientation in the use of curved glass throughout all project stages. Herein the characteristic surface strength is given with fk=40N/mm² and the characteristic edge strength with fk=32N/mm², verified by test series [10].
Nevertheless, if curved glass products without National Technical Approvals are used, it is recommended to verify the characteristic bending tensile strengths beforehand by testing [10].
But also the load side requires specific consideration. It could be observed that specific design loads like temperature loads or constraint forces induced by building movements or support conditions play a decisive role designing curved annealed glass elements (apart from impact loads and concentrated loads). It comes along that those loads need to be combined with general building design loads (dead load, wind load, snow loads, etc.) leading to further accumulation of tensile stresses mostly close to the curved glass elements edges.
Due to those reasons it is crucial that temperature data of the glass surfaces are available. Dynamic building simulation using representative weather data including spectral data of solar radiation can provide the necessary information. Metallic coatings and fritted glass surfaces have particular significance in this context as they induce long-wave radiation exchange between glass surfaces. The more diverse the thermal outflow of a heated up glass element is, the higher are the temperature differences on the glass surfaces [7]. Consequently the thermal stress within the curved annealed glass element is higher. Figure 8 shows the surface temperature results of a dynamic building simulation.
In any case substructures serving as support for the curved annealed glass elements must be engineered under the perspective of possibly occurring constraints. Glass tolerances (increased for curved glass [10]), substructure tolerances, building movements and deflections of adjacent structural elements must be analyzed precisely as they might cause cold bending or in-plane forces in the curved annealed glass elements.
Such additional forces should be avoided respectively minimized as far as possible by using appropriate support configurations of the glazing, as shown exemplary in Figure 9. Even constraint forces induced by climatic loads, typically occurring in curved double glazed units, can be reduced considerably by using flexible spacer systems [12].
Load conditions impacting the curved annealed glass infill elements require consideration within the structural glass analysis, including appropriate material idealization. Spring stiffnesses or material models should consider the real support situation and load paths precisely [3].
![Figure 8 Glass surface temperatures determined by dynamic building simulation [7]](/sites/default/files/inline-images/Fig8_34.jpg)
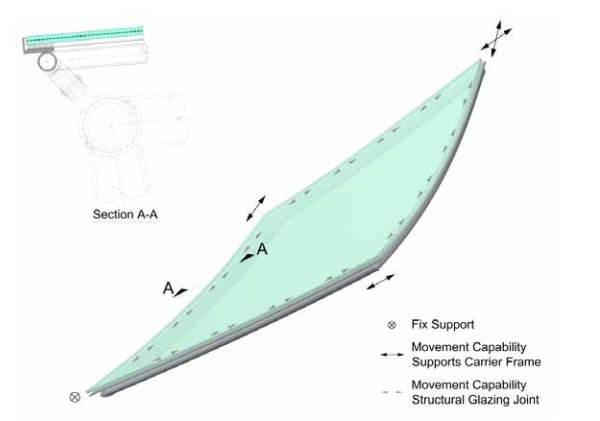
3.2 Testing
The general approach to determine the edge strength is a four-point-bending test setup. However, the EN ISO 1288-3 standard is solely valid for flat glass products. For this reason the research project PRÜFgbGLAS currently develops a testing method for cylindrically curved glass [13]. Geometries other than cylindrical can be tested by a simplified approach.
The glass strength is determined either by the four-point-bending test set-up or the ring-on-ring-test with flat test specimens passed through the thermal cycles of the bending process of curved glass. Using the ring-on-ring tests allows separating the surface strength from the edge strength to determine impacts of the gravity bending process itself [4]. To examine residual surface stresses induced by insufficient or inhomogeneous heating after bending of hot bent annealed glass, photo elastic residual stress measurements [5] or cutting tests can be applied.
Nevertheless, for some cases it is beneficial to perform real size tests of hot bent annealed glass elements including the envisioned support situation, especially for a better understanding of the post-breakage behavior. Accompanied by the tests described above, microscopic and fractographic analysis provide further in-sights of the material quality and strength (e.g. fracture mirrors, failure origin, edge chipping, etc.) [6].
3.3 After Manufacturing
Once the hot bent annealed glass panels leave the production, still extreme caution is required. Already packaging and transportation need to consider the brittle behavior of the material. Load cases exceeding the planned conditions, from production up to the final boundary conditions on-site, must be omitted. Especially the edges of hot bent annealed glass should be protected sufficiently. Eventually occurring edge chipping might reduce the edge strength tremendously (refer to Chapter 3.1). However, also surface scratches should be avoided during the complete lifetime of annealed glazing elements.
4. Findings from various testing
To quantify some of the major influencing, project-specific parameters on hot bent annealed glass different testing series were executed as described below. Furthermore the aim was to establish a reliable planning basis in the partly non-regulated normative situation.
4.1 Glass surface strength depending on individual processing
Specimens of different glass suppliers and different base glasses (GS-1, GS-2 and GS-3) were tested to ensure the appropriate product quality of the hot bent annealed glazing used in a project. Concentric ring-on-ring tests were carried out to investigate the bending surface strength. “To quantify the influence of the individual processing steps both acid-etched glasses, non-etched glasses and glasses which passed the hot bending process (heatup/cool-down process) were investigated” [7].
Test values were adjusted to the log-normal distribution (providing typically the best fit to evaluate material strength), the prognosis and confidence intervals for the regression were calculated (characteristic strength calculated based on 5%-quantile with a confidence level of 95%) [7].
![Figure 10 (left) Comparison of mean values of surface strength [17] Figure 11 (right) Comparison of characteristic surface strength between series GS-1, GS-2 and GS-3 [17]](/sites/default/files/inline-images/Fig10-11.jpg)
Figure 11 (right) Comparison of characteristic surface strength between series GS-1, GS-2 and GS-3 [17]
The following findings could be observed in [17]: Depending on the source the results spread in a certain range. Both the mean values (Figure 10) and the characteristic strength values (Figure 11) obtained by testing vary. The most promising results could be determined for the GS-2 series as shown in Figure 11.
Both the GS-2 series as well as the GS-1 series are in accordance with the requirements of the relevant product standard EN 572-1 [14]. The herein postulated float glass bending strength is defined with 45MPa. Substantial influences on the glass strength caused by acid-etching or by thermal cycles of the hot bending process could not be indicated.
Photo elastic residual stress measurements and tests of the fracture pattern were performed in other test series on full size hot bent annealed glass elements to gain further knowledge of residual surface stresses caused by the annealing process. Measured residual surface stresses are in the range of conventional flat annealed soda-lime silicate glass and did not show irregular crack patterns [5].
4.2 Edge Strength and Frit
Ceramic frit colors applied occasionally to glass surfaces pose additional challenges to hot bent annealed glass products. Beside the reduced characteristic bending strength of fritted annealed glass, which is not even regulated in product standards for planar glazing [15], dark frit colors may trigger thermal stresses by solar radiation.
Some test series including subsequent evaluation were executed to compare the edge strength of polished edges with frit to the edge (series 1), polished edges without frit (series 2 & 3), grinded edges with surface frit in a distance to the edge (series 4) and the surface strength (series 5) [6]. All test specimens (dimension. L= 180mm, h= 32mm, t=7,8- 8mm) went through the identical production process usually applied for hot bent annealed glass.
Series 1 to 4 were examined in 4-pointbending-test and series 5 in a concentric ring-on-ring-test. In the statistical analysis the measured values of the testing were adapted to the Weibull distribution [6] which considers next to the material strength also other parameters (e.g. size effects). The design strength was calculated corresponding to a failure probability of 1/1000 according to the ASTM E 1300 standard [16].
Based on the results of Figure 12, the following conclusion could be drawn by [6]: The characteristic edge strength of specimens with frit was 50% less, compared to the characteristic edge strength of specimens without frit. The allowable edge stresses determined by tests are about 40% of the allowable edge stresses after ASTM 1300 (glass without frit) [16].
The characteristic edge strength of test specimens without frit is in the same range as test specimens with surface frit in a distance to the edge. The mean value of the edge strength (Figure 13) is significantly higher compared to the mean value of the surface strength. Nevertheless, considering the big variation of test values, the characteristic edge strength is lower.
The test series above clearly indicate the required necessity of precise investigation and caution designing the edges of hot bent annealed glass elements. The following influences on the final edge strength are known: Edge finishing (cutting, grinding, polishing, etc.)[19], length of the edge (flaw population), load duration [20] and residual stress distribution. Frit seems to disturb the cooling process during glass production which reduces the final glass strength [15] [21].
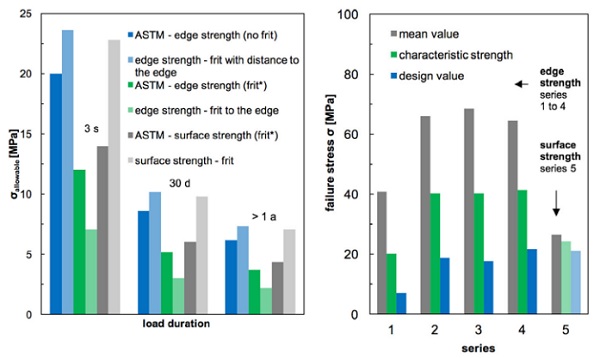
Figure 13 (right) Comparison of the mean strength, the characteristic strength and the design strength of the different test series
4.3 Thermal loading ∆T
In many cases different surface temperatures on the inside surface and the outside surface of the glazing, expressed as thermal loading ∆T, are the decisive criteria for the design of hot bent annealed glass elements.
To predict influences of the above shown low edge strength of fritted glass, in combination with uneven thermal loading ∆T, some element tests with different glass configurations were performed with the following test set up [11]: The interior glass surface (installed on the top) was heated by custom made silicone rubber heaters attached to the glass surface. The outer glass surface (bottom side) was cooled by a fan and sprinklers.
The thermal stresses were measured by strain gauges (Figure 15). Different glass configurations comparing fully fritted glass, edge delete frit glasses and clear glasses (glass built up 3x8mm annealed double-curved hot bent glass with 1,52mm SGP Interlayer, frit #2, low-e coating #6) were investigated under various uneven thermal loading conditions ∆T.
The following findings could be observed by [17] [18]: Nearly all glass breakages in the element tests started from the edge of the fully fritted glass. The measured stresses principally agree to the calculated stresses (by FEM Analysis). Breakages occurred solely for glasses with full frit to the edge on position #2.
The test results were fitted to the Weibull distribution to predict the failure probability as shown in Figure 14. A temperature difference of ∆T=10[K] between exterior glass and interior glass showed a failure probability of 0,8 percent (∆T=21[K] showed a failure probability of 3,4 percent). Based on the temperature results of previous dynamic building simulation failure probabilities of the glazing can be determined in dependence on its orientation.
In consequence, the failure probability obtained by evaluation of the tests described above, partly exceed the typically applied failure probabilities according to ASTM 1300 [16]. Such findings require modified glass configurations, or a mutually agreed shared risk policy for projects dealing with the material hot bent annealed glass.
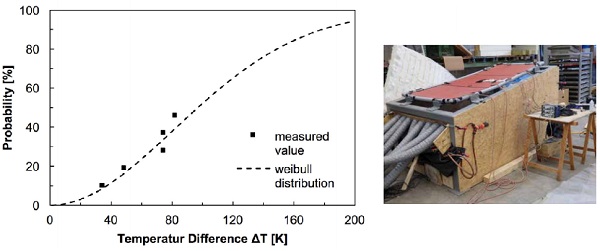
Figure 15 (right) Test setup of the component tests [18]
5. Conclusion
As long as there are no product codes and standardized test codes in place, projectspecific testing will be crucial to establish a reliable basis for the design of projects using the highly sensitive material hot bent annealed glass. In several testing series for hot bent annealed glass, results show a huge variation in stress resistance, mainly depending on the glass configuration and the quality of the annealed curved glass product itself.
A continuous control of the material quality and the production process is absolutely necessary, especially regarding edge strength with its fundamental role in the context of the glass fracture mechanics. Furthermore, hot bent annealed glazing requires very careful design and engineering.
Given its brittle material behavior and the absence of engineering standards, a holistic approach considering any boundary condition is essential to realize geometrically complex building envelopes. In general, a user friendly design method considering the material quality based on previous flaw detection as well as specific load conditions should be implemented.
6. References
[1] Haldimann M., Luible A., Overend M.: Structural Use of Glass, International Association for Bridge and Structural Engineering, Zürich, Switzerland, 2008.
[2] Fildhuth T., Knippers, J.: Interior stress monitoring of laminated cold bent glass with fibre bragg sensors, Challenging Glass 4 & COST Action TU0905 Final Conference EPFL–Louter, Bos, Belis & Lebet (Eds), Lausanne, Switzerland, 2014
[3] Schuler C., Elstner M., Illguth M., Stief S., Lorenz A.: Application of curved glass in architecture; Stahlbau Volume 81; Issue 3, March 2012
[4] Hof P., Oechsner M.: General technical approval for curved annealed and curved tempered glass in Germany, Proceedings of Cost Action TU0905 Mid Term Conference on Structural Glass, Porec, Croatia, April 2013
[5] Schneider J.; Hilcken J.: Test report 1163/2017.07.01 30th January 2017, Heusenstamm, Germany
[6] Schütz Goldschmidt Schneider – Ingenieurdienstleistungen im Bauwesen GmbH
[7] Post H.: Report Dynamic Building Simulation, b+e Consulting Engineers for Building Climate and Energy Schemes, January 2016, Munich, Germany
[8] Lindqvist M.: Structural Glass Strength Prediction Based on Edge Flaw Characterization; These No 5627 EPFL Ėcole Polytechnique Federale de Lausanne, 22. February 2013, Lausanne, Switzerland
[9] Haldimann M.: Fracture Strength of Structural Glass Elements – Analytical and Numerical Modelling, Testing and Design, These No 3671, EPFL, Lausanne, Switzerland, 2006.
[10] Bundesverband Flachglas, BF Merkblatt 009/2001, Guidelines for Thermally Curved Glass
[11] Schneider J; Hilcken J. Hagen B.: Test Report 1163/2016.44.02, 16th March 2017; Heusenstamm, Germany
[12] Wellershoff F., Förch M., Minasyan, M.: Impact of Foam Spacer Systems on curved double glazed units under climatic loads; Engineered Transparency – International Conference at Glasstec, Düsseldorf, Germany, 2014
[13] Bukieda P, Engelmann M., Elstner M., Weller B.: Research and Standardisation of Four-Point Bending Test for Thermally Curved Glass, Glasbau 2017, Dresden, Germany
[14] EN 5721:2004 German version, Glass in building Basic soda lime silicate glass products Part 1: Definitions and general physical and mechanical properties
[15] Weller B., Nicklisch F., Thieme S., Weimar T.: Glasbau-Praxis Konstruktion und Bemessung, 2010
[16] ASTM E 1300 -04, Standard Practice for Determining Load Resistance of Glass in Buildings, July 2004
[17] Schneider J.; Hilcken J.: Test Report 1119/2015.14.02, 28th April 2016, Heusenstamm, Germany
[18] Schneider J.; Hilcken J., Müller Braun, S.: Test Report Nr. 102.01.16 TU Darmstadt - Institute for Structural Mechanics and Design (ISM+D), 15th April 2016; Darmstadt, Germany
[19] Kleuderlein J., Ensslen, F., Schneider J.: Investigation of edge strength dependent on different types of edge processing, Proceedings engineered transparency, International Conference at glasstec, 21 and 22 October, Düsseldorf, Germany, 2014.
[20] Vandebroek M., Lindqvist M., Belis J., Louter C.: Edge Strength of cut and polished glass beams, Glass Performance Days, 17 -20 June, Tampere, Finnland, 2011
[21] BergersM., NatividadK.; MorseS. M.,Scott NorvilleH.: Full scale tests of heat strengthenedglass with ceramicfrit, Glass Structures &Engineering, Volume 1, Issue 1, June 2016"