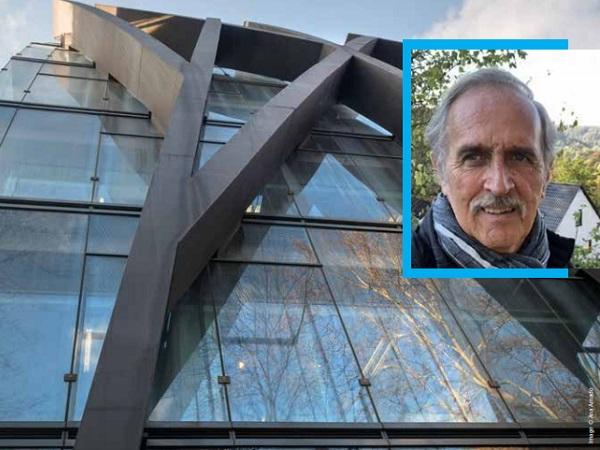
Date: 19 March 2020
Q. Tell me about you and your company.
After completing my studies in 1976, I got my first job working as a draftsman at an architectural aluminum company that covered the production of the whole value chain of curtain walls, from casting the alloy, up to field installation. Later in my career, I managed a consulting company that promoted the use of value-added glass products, such as laminated and tempered glass, in Argentina, Chile and Uruguay. This experience led me to form Estudio Marshall, a consulting firm specializing in facades. We don’t sell any products and we have no commercial relationships. Our focus is on design, quality control, forensics, and, very importantly, education.
Q. As a façade design & engineering company, how has the development of ever more capable interlayers changed your design capabilities/visions?
Large units certainly rank up there as does the growing use of structural glass. We can now do balustrades without any metal – this would have been crazy 30 to 40 years ago. Interlayers like SentryGlas® ionoplast interlayers from Trosifol have changed the way you can use glass. This opens new design opportunities.
While large glass is popular with architects around the world, it can be challenging to source it locally. In Argentina, for example, glass fabrication is limited to 5 meters. We had a project designed in the US for an Argentinian building, which required 6 m panels, but we knew that no local company could produce panels of this size. So we had to go abroad to get the sizes we needed. Architects may have a vision, but we have to ask, “who can bring this vision to life?” As façade consultants, we employ the best technology available, such as AutoCAD and 3D printing, but we still have to be realistic about limitations in fabrication and logistics.
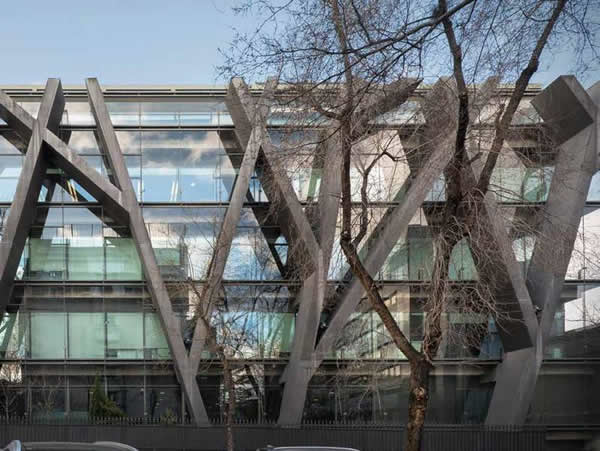
Image © Ana Amado
Q. Do you find that architects are now more aware of the capabilities of structural glass?
It depends on the market and the country. Sometimes you do find architects who are more up to date in terms of technology and commercial capabilities, but sometimes you don’t. This is why we find the education angle about façade design and technology is a good business.
Q. Are they using structural glass more in their designs?
There’s a famous phrase from a Spanish architect − he said − regarding innovation − it’s not good being the first one, it’s better to be the second one. Most architects are reluctant to design with innovative facades. They want to innovate, but they don’t want the responsibility (run the risk) of being the first. They are also restricted by budget, so often head back to more widely applied concepts. In answer to your question… “Yes, but slowly.”
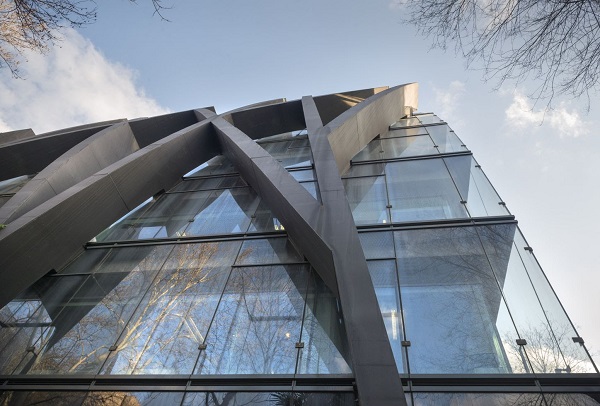
Image © Ana Amado
Q. Can you give us some examples of your glazing projects (using Kuraray interlayers)?
The View Building in Argentina was interesting. It is an apartment building and the owner wanted a curved façade on the balconies on all floors around the circumference of building. The initial design called for lots of aluminum posts, but I suggested a different approach to produce a cleaner, more unique appearance with structural laminated glass made with SentryGlas®. Thus, we designed an all-glass balustrade, with curved glass on the corners.
The Fortuny 32 structure in Madrid, was unique from an architectural standpoint. The original design was just a simple façade with sun screens. We proposed a double skin façade to provide a more controlled environment. The outer skin needed to be as invisible as possible, thus we specified a low-iron laminated glass with SentryGlas®, with the structural columns on the outside. The curved areas were cold bent units of the same configuration. You only see the façade from the inside. The façade supplier Bellapart did an amazing job with our design. The outcome is a very beautiful building that is almost sculptural.
Also in Madrid, the Campus Repsol was a real challenge. The architect wanted 4 x 4 m façade units, which lead us to a local façade company who could produce units of this size and special slim extrusions were developed. The typical glazing units were double laminated with two 10 mm low iron insulating glass panels each incorporating SentryGlas®, with a 20 mm air space. In specific areas exposed to the powerful sun of Madrid, we used a unique proprietary double dot printing pattern on surface #2. The exterior layer, with its unique supporting system was also constructed of low iron glass laminated with SentryGlas®.
Q. Why did you opt for Kuraray interlayers, such as SentryGlas® for these projects?
We are well aware of the capabilities and have broad experience using SentryGlas®, where, to date, we have not seen any failures or delamination. We also receive super technical support from Kuraray. This industry needs the support of reliable suppliers and toplevel quality control. We must know that the technical support is as good as the products. We feel more secure and comfortable working with a company that can answer questions from all stages of a project (design, fabrication, build, etc.) and we need fast answers − ideally within 24 hours. We value this so much.

Image © Ana Amado
Q. How/when do you get involved in a “typical” project?
Most of the time we come on board during the schematic design phase (Concept) but depending on the country we also get involved during the construction phase, mostly for quality control. One thing we do well is create product specifications for each project − we work very hard on this.
In some countries we do not have regulations for every item, so we need to refer to foreign standards and specifications. For this reason, we encourage our clients to include our specifications in their contract documents and, more importantly to make sure that contractors follow them. Our spec book is about 100 pages and it represents best practice.
Sometimes we undertake forensics when structure has been built. In these cases, I like to think of us as the CSI of façade design, with the normal conversation being: “If you’d called us earlier, we could have stopped this issue.” Imagine a shopping mall with 100 leaks… we need to catch them before the lawyers get involved.
Q. What sort of things are now possible that maybe weren’t 5-10 years ago?
As well as the frameless balustrades I mentioned earlier and large glass, I am very interested in glass connections, namely the inserts that allow you to connect one lite to another. These have opened up a lot of new opportunities for glass design. I am also fascinated by modern simulation methods. There is some wonderful software out there that can simulate the behavior of façades and materials.
Finally, a favorite of mine is drone inspection. When I was younger, I could climb 30 storeys, now I don’t need to. I can do it from my office. With my experience I know where to inspect and where to point the camera.
In many cases, the codes might only call for the adjustment of one thing, but there are still multiple other factors to consider. We get in a lot of battles with local authorities, especially regarding balustrades. As a result, we have to create a lot of proofs and undertake testing, just to show that the designs meet the code’s intent.
Q. If you had a wish list, what would the next generation of interlayers offer?
As an engineer, I would say stiffness… but as an architect I look holistically and think about transparency and translucent lites that can both create and store energy.
We are working with transparent photovoltaics, but they are not particularly efficient at the moment. It would be wonderful to have a normal window that gives you a view of the streets, but at the same time produces and stores energy.
Connectivity from a data sense is important too − it’s amazing what you can do with wires and wi-fi. Glass needs to be connected too. It must be a major player in the built environment, and these days you cannot be a major player if you cannot connect.
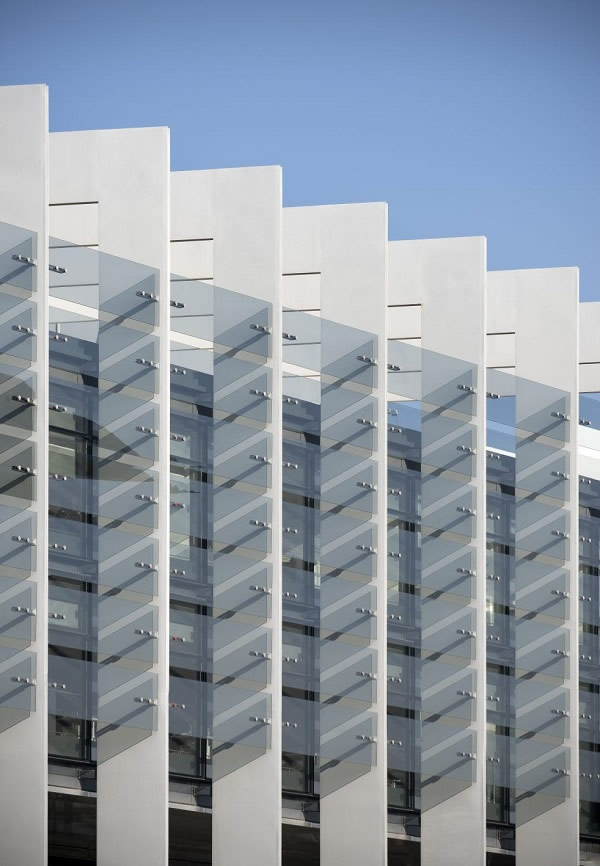
Image © Ana Amado
Trosifol is the global leader in PVB and ionoplast interlayers for laminated safety glass in the architectural segment. With the broadest product portfolio Trosifol offers outstanding solutions:
- Structural: Trosifol® Extra Stiff (ES) PVB and SentryGlas® ionoplast interlayer
- Acoustic: Trosifol® SC Monolayer and Multilayer for sound insulation
- UV Control: from full UV protection to natural UV transmission
- UltraClear: lowest Yellowness Index in industry
- Decorative & Design: black & white & colored interlayers
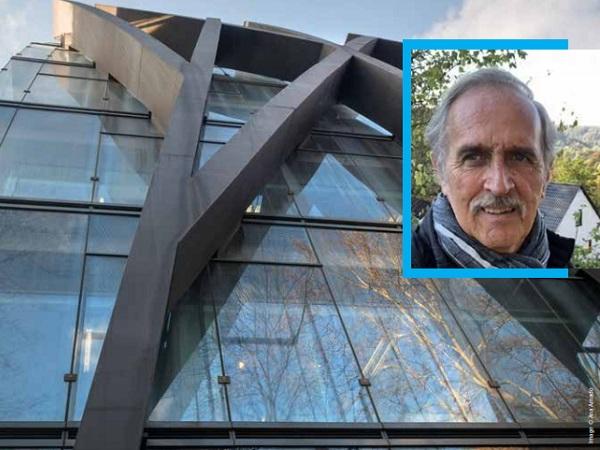

Add new comment