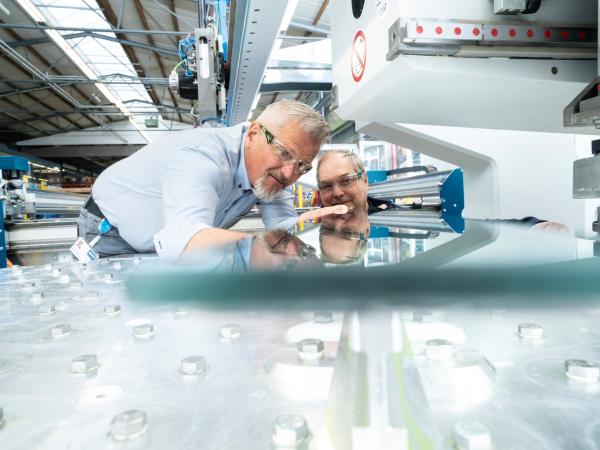
Date: 25 May 2023
Each time you save energy, you cut your electricity bill. This significantly contributes to mitigating climate change and increasing your profitability. Glaston continues to push the development of modern glass processing technology to meet production needs with significantly lower electricity consumption. With our upgrades, you can also take advantage of new developments and start saving energy. Join us on our mission toward building a better tomorrow through safer, smarter, more energy efficient glass solutions.
Advancing energy savings in glass tempering technology
“Glaston is developing advanced heating and cooling technologies for the best glass quality, outstanding energy efficiency and reliable automation. Our tempering lines with advanced heating control make it possible to increase loading efficiency and decrease energy without sacrificing quality. With recent technology solutions, quenching energy can even be optimized,” says Riku Färm, Director at Heat Treatment Technologies.
Minimize energy losses in glass lamination
The easiest way to save energy when laminating glass is to upgrade from a traditional infrared heater furnace to full convection technology. Energy losses are minimized, as the same air is recirculated inside the furnace. The right amount of energy stabilizes the furnace temperature. Processors often report energy savings of at least 50% after a heating technology upgrade.
Convection cuts energy use in automotive glass processing
Heating technology is also key in bending and tempering automotive glass. With its targeted and efficient heat transfer, convection heating minimizes energy loss during the process. Convection provides uniform heating for bending both clear and printed glass surfaces. For windshield and sunroof processing, convection minimizes the number of old-fashioned reflection plates, saving more energy per unit produced.
“In automotive glass pre-processing, energy can even be recovered. Energy is fed back into the grid by decelerating the tools with electric motors. In addition to that, our lightweight equipment saves up to one-third of the energy required by conventional machines,” says Robert Prange, SVP of Automotive & Display Technologies.
Save energy by simplifying insulating glass production
The Glaston Thermo Plastic Spacer (TPS®) system produces IG units with only one machine instead of several components. This reduces cycle times and saves energy by completing daily production faster.
“Glaston’s latest washing and drying machine automatically switches the drying zone off when the glass plate is dry. This reduces washing machine energy use by 25%, while the closed water circuit further reduces water consumption,” says Uwe Risle, Director at Insulating Glass Technologies.
Boost energy with upgrades
“A secure way to ensure energy efficiency is to maintain the equipment together with the Glaston experts and original spare parts. Then, upgrading an existing glass processing line with the latest technology leads to significant energy improvements without investing in an entirely new line. Most of our latest technology is available as an upgrade, making it quick and efficient to increase capacity, reach better output quality and yield, reduce maintenance and improve uptime,” comments Artturi Mäki, SVP Services.
For more about energy efficiency in glass processing visit https://www.glastory.net/
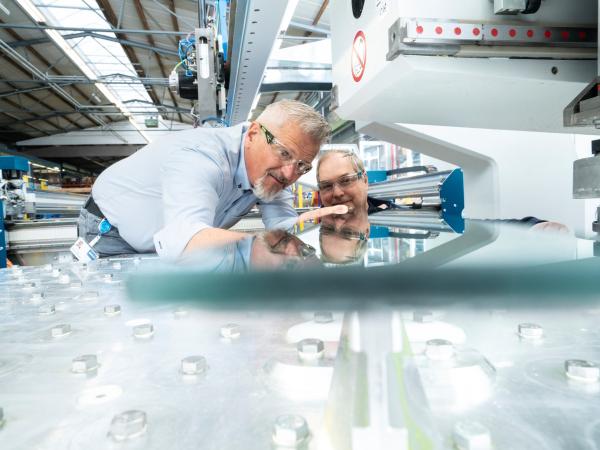

Add new comment