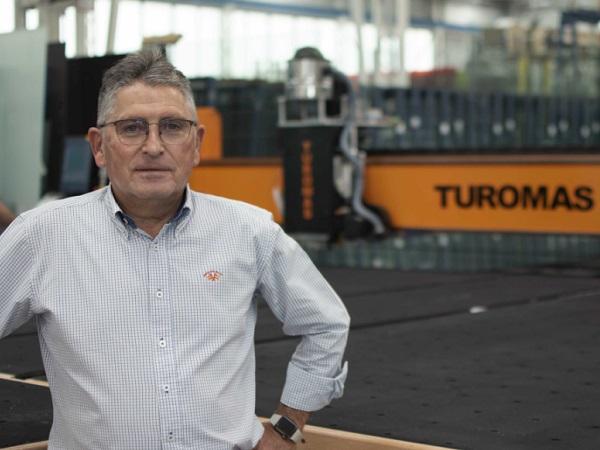
Date: 16 November 2021
ACRISTALAMIENTOS VINUESA, SA, is a family company, founded in 1967 in Soria, Spain by 5 brothers, who after many years of experience in the glass industry took the opportunity to found their own company. In 1977 they had the need to expand the facilities to the current 6,072 m2 of industrial factory, 720 m2 of offices and 30 employees.
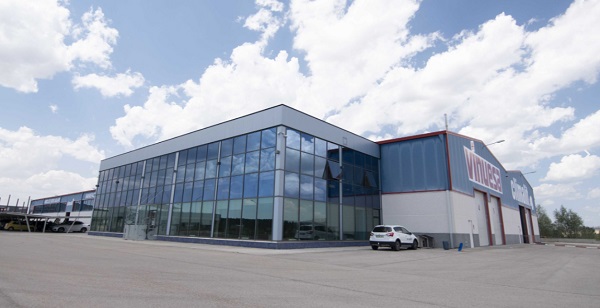
The main activity is the transformation of flat glass, printed glass, decorative glass, safety glass and manufactured glass for both professional and private customers. Since 1990 VINUESA has been a licensed manufacturer of the SGG CLIMALIT (Insulating Double Glazing) insulating glass brand, whose cutting process is managed entirely by TUROMAS machinery, VINUESA’s supplier since its origins.
We talked to Felipe Parra, director of ACRISTALAMIENTOS VINUESA, about his business, his objective and the development of the Spanish market.
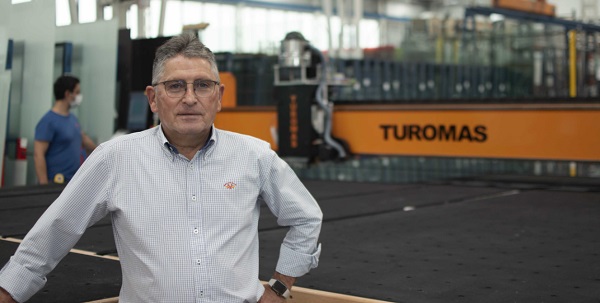
What is ACRISTALAMIENTOS VINUESA, S.A.?
Acristalamientos Vinuesa was founded as a family business in 1967, a time when glass did not have the presence it has today, nor of course did it have the technical characteristics it has today. It was my elder brother who started the business, having worked in a small glassworks, and this was the reason why he proposed to the family to start this project.
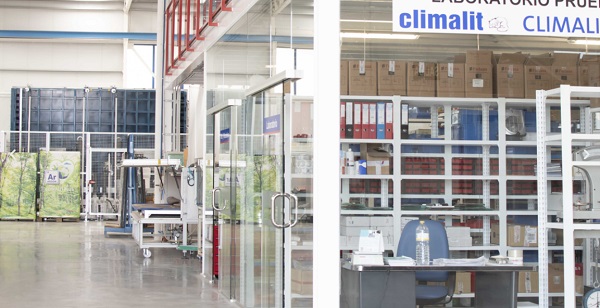
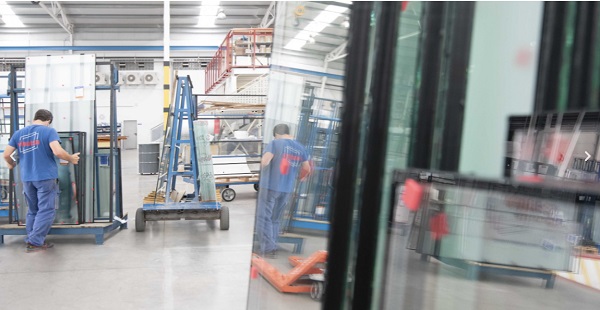
I joined the company 5 years later and from the beginning I liked the business very much. This enthusiasm for the product, together with my concerns, led me to seek new and more ambitious horizons. I started to visit international fairs, in Paris, Germany, and I saw that there was machinery that I didn’t know about.
At that time I made the decision to qualify the technology and media company. And well, in one of those forays through mutual colleagues, I got to know the TUROMAS company. We started to have contact and soon we had the first TUROMAS table.
What products and services does ACRISTALAMIENTOS VINUESA, S.A. offer? What production processes can be found in the factory?
Originally, we were installers of glass, three-millimetre float glass, two-millimetre float glass, glass with glass panes… and we have always sought to differentiate ourselves by offering products with higher technical performance to our customers.
Therefore, we immediately started manufacturing chamber glass and when we had sufficient capacity, we signed the contract with Saint Gobain. We went from more elementary machines to more modern machines equipped with better features that allowed us to produce more quantity and better quality.
Today, fifty years later, we have once again made our move by incorporating new technology in both cutting and manufacturing insulating glass. In the case of cutting with TUROMAS and in the case of double glazing with another reference company.
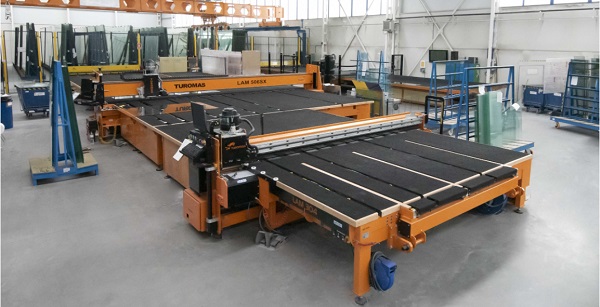
How did the need for the new cutting machines arise?
As I said before, we have always wanted to be at the forefront of our customers’ demands and for that it is necessary to listen to market demands. Nowadays, products with high performance, high dimensions, high thicknesses are required and all this has led us to realise that the machinery we had was obsolete.
In addition, the new machines are faster and produce with a higher quality and precision that is transferred to the rest of the edging, seaming and washing processes. We must not forget that everything starts from the zero point, which is the reception, cutting and handling of glass.
And that was the reason that motivated us to renew both cutting lines.
Why TUROMAS?
Just as in business, there has to be a chemistry between supplier and customer and with TUROMAS this has been there from day one. Although we had other options from manufacturers of machines we already had in other processes, the cutting tables from the beginning have been TUROMAS.
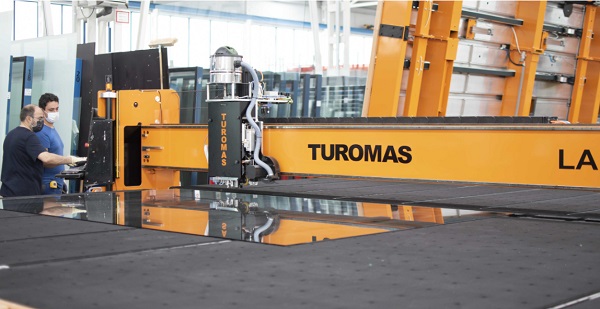
They have always been very responsive to our needs, providing us with full support and exceptional after-sales service and that is very important to us.
Since the first machine, the confidence in their products has been absolute, showing us that their equipment is a reference in the market, not only nationally, but also internationally.
Therefore, we had no doubt that the TUROMAS offer was the most attractive for us.
Which models of TUROMAS machines have been installed? Why are these machines the best for ACRISTALAMIENTOS VINUESA, S.A.? What would you highlight about them?
Two automatic cutting lines for 6-metre glass have been installed. One of them for float glass cutting – RUBI 516C and the other one for laminated glass cutting – LAM 506SX.
RUBI 516C
The float glass cutting table is equipped with linear motors guaranteeing unprecedented performance and quality in any cut.
It incorporates a cutting system with 4 individual cutting tools with automatic selection. Each has its own roller, lubrication system and pressure cylinder specifically dimensioned for its cutting range.
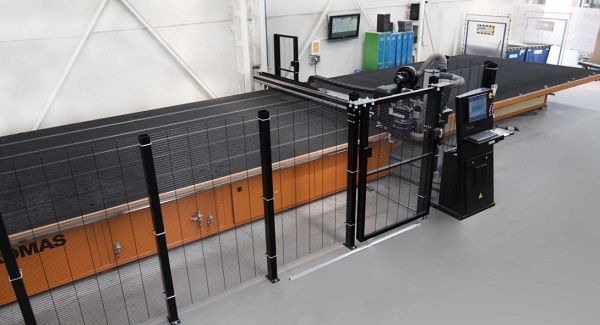
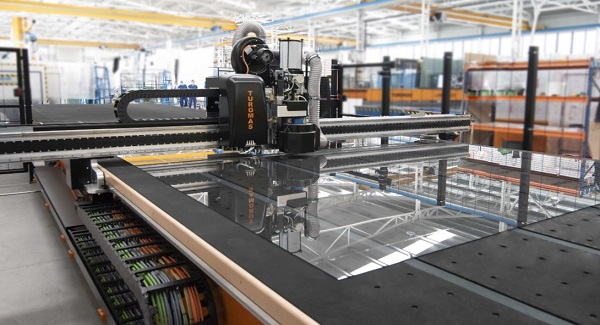
In addition, an extra software – Cutting TV – has been installed to assist in the process of opening cuts. It automatically displays the optimisations so that, at a glance, the operator has all the information needed for the cutting process. Once the cutting table has evacuated the workpiece, the display changes automatically without the need to operate any buttons or foot pedals.
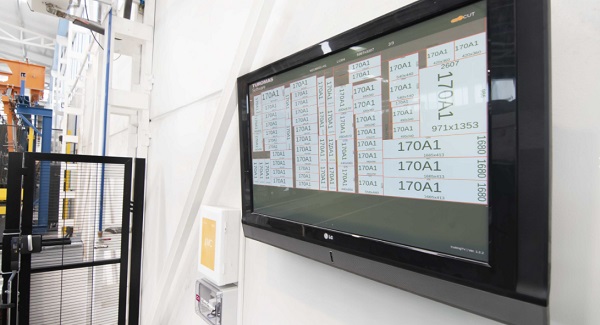
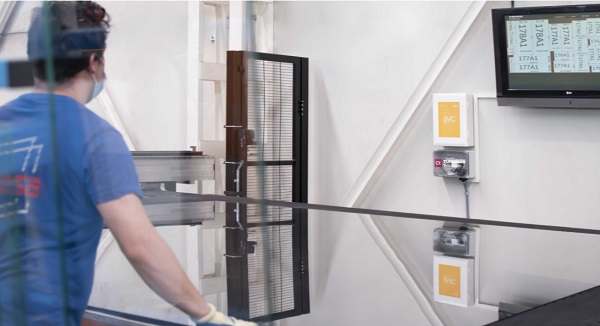
LAM 506SX
Regarding the LAM 506SX laminating line, it is a table that allows us to position, rotate, strip and cut and separate glass up to 12 + 12 mm fully automatically.
The most important feature of this line and what made us decide for it was the quality of the cut, even with thicker thicknesses the result is perfect.
It has been integrated with a second cutting bridge – LAM 304 to speed up the process, increase the cutting rate and productivity. For this purpose, a defragmenter for cross-cutting optimisations has been installed on this second line to distribute the cuts and keep the two tables productive at the same time.
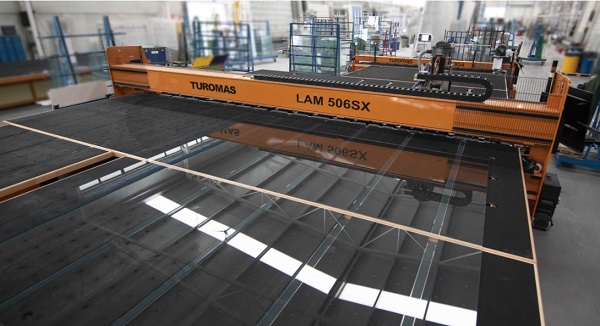
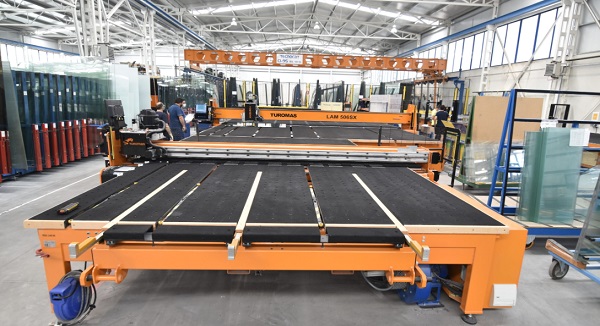
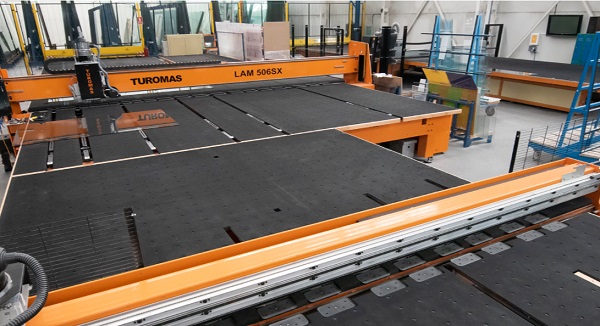
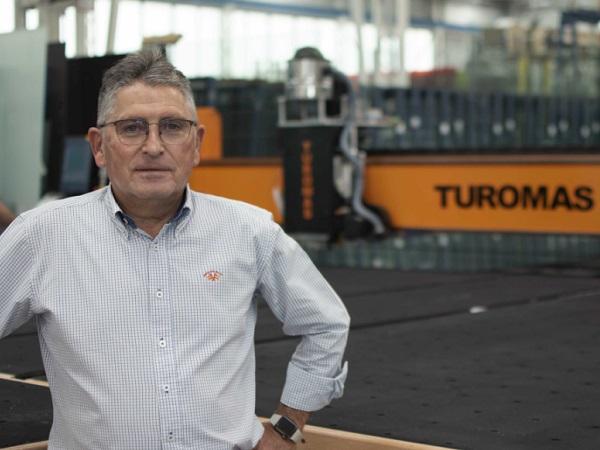

Add new comment