First presented at GPD 2017
General description of Vacuum Insulating Glass
Vacuum Insulating Glass (VIG), illustrated in Figure 1, is simply conventional insulating glazing (IG) with an evacuated space between the two glass sheets [1, 2, 3]. (Note: Due to space limitations, most of the references in this paper are to review papers, which contain source references.)
VIG achieves high levels of thermal insulation using the same principles as the Dewar flask – the vacuum eliminates heat transfer between the two glass sheets due to gaseous conduction and convection, and radiative heat transfer is reduced to a low level by one or two internal transparent low emittance coatings.
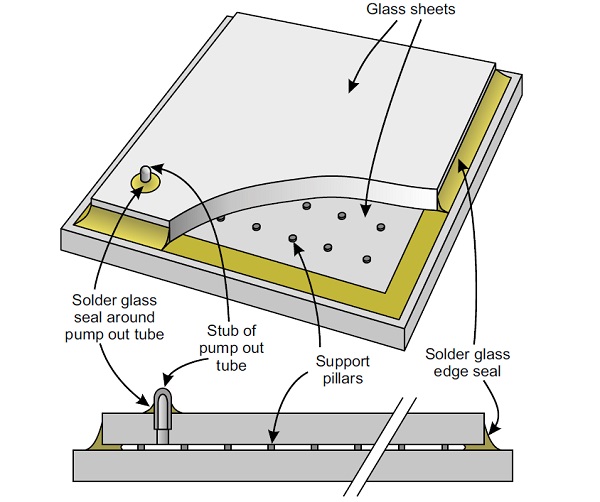
Highly insulating VIG must incorporate several features, including:
- A hermetic (leak free) seal around the edges of the two glass sheets;
- A high and stable thermally insulating internal vacuum (pressure below ~106 atmosphere);
- An array of support pillars to maintain the separation of the glass sheets under the large forces due to atmospheric pressure (10 tonnes/m2);
- An internal transparent low emittance coating to reduce radiative heat flow to a low level; and
- An acceptable design compromise between the heat flow through the pillars and the mechanical stresses in the glass sheets near the pillars due to atmospheric pressure. The VIG concept offers several significant attractive possibilities:
- Very high levels of thermal insulation can be achieved, in principle;
- The vacuum space is very thin, so the overall thickness of the structure is only slightly greater than the combined thickness of the two glass sheets;
- VIG should exhibit negligible degradation in the field due to gas permeation through the hermetic edge seal. VIG therefore has the potential to achieve very high reliability in practical installations.
History
1913 - 1988
The concept of VIG was first described in a 1913 German patent by Zoller [4] only 20 years after the invention of the Dewar flask.
This patent claims structures with multiple glass sheets, and internal supports consisting of “ribs, grooves, prisms, projections on the glass sheets, spheres or blocks made of thermally insulating material, and line supports crossing at an angle”.
During the following 75 years, many attempts were made to develop this concept, virtually all of which were published only in the patent literature [3]. The claims in these patents relate to many aspects of the design and manufacture of VIG, including:
- Support pillars of many different designs and materials;
- Pillar arrays of various geometries;
- Flexible and rigid edge seals made with solder glass and metal;
- Edge seals made by direct fusion of the two glass sheets;
- Ports and tubes for evacuating the internal volume;
- In-vacuum sealing of the edges;
- Contoured glass sheets;
- VIGs with multiple glass sheets; and
- VIGs with internal low emittance coatings.
1988 - 1994
Despite this extensive work over many decades, the first practical thermally insulating sample of VIG was not made until 1989 [5]. This was achieved in work that followed on from a 1988 Senior undergraduate project by Stephen Robinson, supervised by the author, at the University of Sydney School of Physics. These first experimental samples were made using two heating steps, as shown in Figure 2.
In the first step, a rigid edge seal was formed between the glass sheets by melting solder glass at a temperature above ~450°C. During this step, solder glass was also melted to form the support pillars, and to seal a small, in-plane pump out tube to the edges of the glass sheets. After cooling, the sample was suspended from the pump out tube and evacuated. The internal surfaces of the sample were then outgassed during the second heating step at a much lower temperature.
After cooling to room temperature, the pump out tube was melted and sealed. The existence of a thermally insulating vacuum was demonstrated using a rudimentary guarded hot plate apparatus [3, 5].
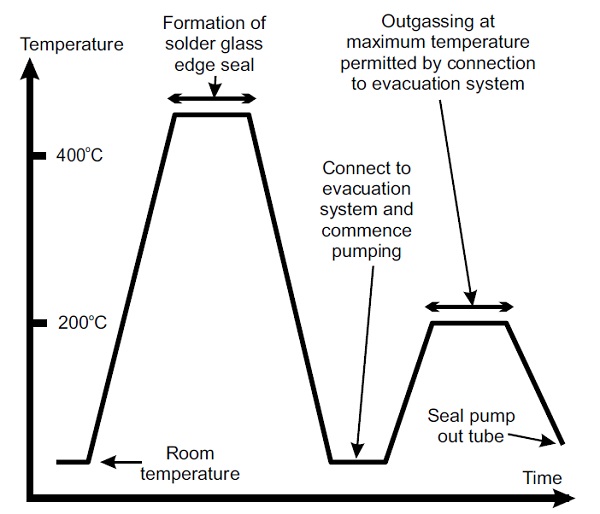
This achievement stimulated an extensive research and development program on VIG at the University of Sydney, involving several staff members and many students. During this program, which continues to this day, over 1000 laboratory VIG samples up to 1 m x 1 m in size were made, with centre-of-glazing Uvalues as low as 0.8 W m-2 K-1. The innovations in VIG science and technology developed in this program were reported in many papers and patents.
New developments in production technology during this period include:
- Metal pillars, including designs that automatically orient correctly when placed on the glass sheet;
- A stepped edge around the periphery of the sample for deposition of the solder glass (Figure 1);
- A procedure for evacuating and sealing the sample using a cup that is sealed with an O-ring to the surface of one glass sheet around a pump out tube ([2] and Figure 3).
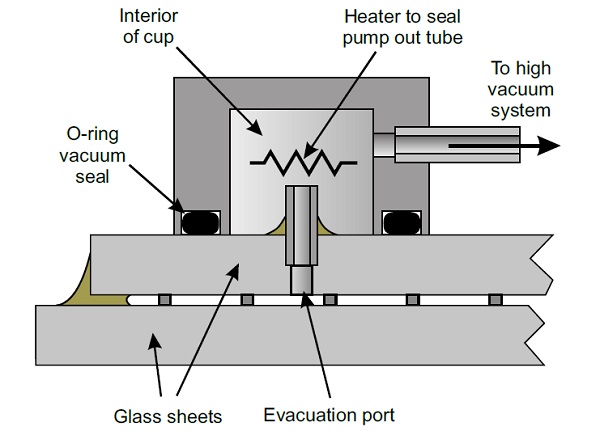
Achievements in VIG design and modelling over the whole research program include:
- Determination of the nature and magnitude of the stresses in the glass sheets due to atmospheric pressure and temperature differences, and experimental validation of these data [1, 2, 3 and 6];
- Development and validation of methods for calculating the heat flow through the VIG due to thermal conduction through the support pillars, gas conduction, radiation and edge effects [1, 2];
- A procedure for designing the pillar array that quantifies the tradeoffs between heat flow through the pillars and the stresses in the glass sheets near the pillars due to atmospheric pressure [2]; and
- Demonstration that the time necessary to evacuate the internal volume of a VIG through a small pump out tube or aperture need not be a limiting factor in the production process [2].
The program also developed several innovative measurement methods including:
- A small area (~1 cm2) guarded hot plate (GHP) apparatus for making accurate and absolute room temperature measurements of the separate heat flows due to the different relevant processes [7];
- Confirmation of the GHP data by measurements on large area samples at other laboratories [2].
- A method for measuring the overall thermal conductance of samples at elevated temperatures [2];
- Direct, non-perturbing measurement of the internal pressure in experimental VIG samples [8];
- Measurement of the outgassing rates of relevant gas species [8]; and
- Long term and accelerated ageing measurements that identified the physical processes and gas species that can cause vacuum degradation, and enabled vacuum degradation rates to be related to manufacturing procedures [8];
The program also included significant fundamental science:
- Measurement of extremely slow rates of the growth of cracks in glass under relatively low stresses, leading to the confirmation of the existence of a subcritical limit of such growth [9];
- Extension of glass failure models to account for the sub-critical limit of crack growth [10]; and
- Development and validation of methods of calculating radiative heat flow between surfaces that incorporate the dependency of emittance on angle and wavelength [11].
From its inception, the University of Sydney took the view that it did not have the capability or resources to commercialise VIG, either in-house, or by a spin-off entity. The University’s VIG research program therefore sought to understand the relevant science and technology, and to develop productioncompatible designs and fabrication processes that would be useful to a potential commercial partner. The University also sought patent protection for relevant innovative concepts [3].
Finding a commercial partner proved to be very challenging, for many reasons. It was not known whether several of the necessary procedures for making highly insulating VIG could be realised in a production environment.
In addition, because the VIG concept had been the subject of several previous unsuccessful development attempts, many thought that this new approach was also unlikely to succeed. Equally importantly, it was clear that commercial VIG technology would be expensive to develop, and that a manufacturing plant would require significant capital investment. Put simply, commercialisation of VIG appeared to be a high cost and high risk enterprise.
1994 to 2000
The first serious industry interest in the University of Sydney’s VIG technology occurred in 1993 from Nippon Sheet Glass Group (NSG) in Japan. Around that time, Hideo Kawahara, Director of NSG Architectural Glass R&D Division, was considering the development of thin, moderately insulating glazings for the Japanese retrofit market. The VIG concept was directly relevant to that initiative. In 1994, the University and NSG entered into licensing and collaborative research agreements with the aim of developing a commercial VIG product.
This commercial VIG development occurred at a time when the University’s understanding of many of the relevant technical issues was quite incomplete. Several critical decisions relating to the design and method of manufacture of the product were therefore made on the basis of very limited information.
Important matters in this category included the dimensions of the pillar array, particularly the pillar separation, and the level of bakeout required to achieve a stable internal vacuum. The decision to develop a batch manufacturing process, rather than a continuous one, was made because it provided more flexibility to implement any changes needed as a result of these uncertainties.
After an intensive period of technology transfer and collaborative work, NSG built a pilot VIG production line at its Kyoto manufacturing plant. Most of the post-assembly part of the initial manufacturing process was modelled on the laboratory procedures developed at the University.
The process involved two separate heating steps (Figure 2), and the samples were evacuated and sealed utilising a cup that was sealed around the pump out tube with an O-ring (Figure 3). The process also incorporated sophisticated glass handling techniques, and an innovative pillar placement technology that was specially developed by NSG for this application.
The first commercial VIG product, Spacia, was launched by NSG in 1996. This was immediately followed by an expansion of the capability of the Kyoto production line. Shortly afterwards, NSG established a second, purpose-built VIG manufacturing plant at Ryuagasaki, near Tokyo.
Over the following few years, the design of the NSG product and its method of manufacture evolved significantly. Some of the changes were made to improve the yield of the manufacturing process, as normally occurs in the early stages of any new production technology.
Some changes were major, and were a direct consequence of the earlier limited understanding of important technical issues. At one stage, the entire post-assembly part of the production process was redesigned and rebuilt, reducing the number of heating steps in the process from two to one (Figure 4).
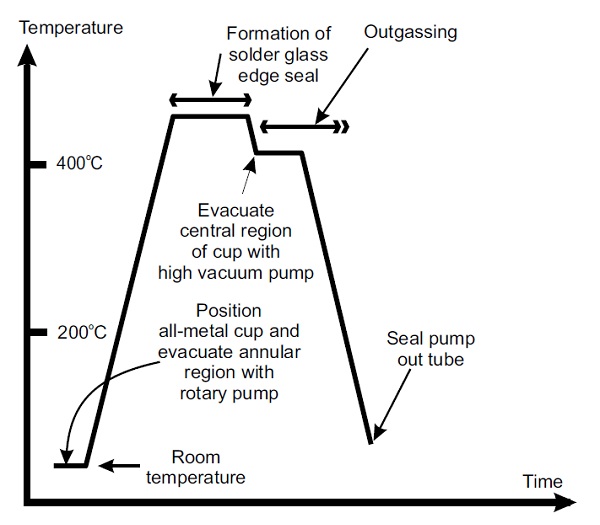
This became possible through the development of a method for making a high temperature vacuum seal around the pump out tube using a demountable all-metal evacuation cup ([12] and Figure 5). Although very costly and time consuming, these changes greatly improved the viability of the technology by halving the post-assembly manufacturing time and significantly simplifying the manufacturing process.
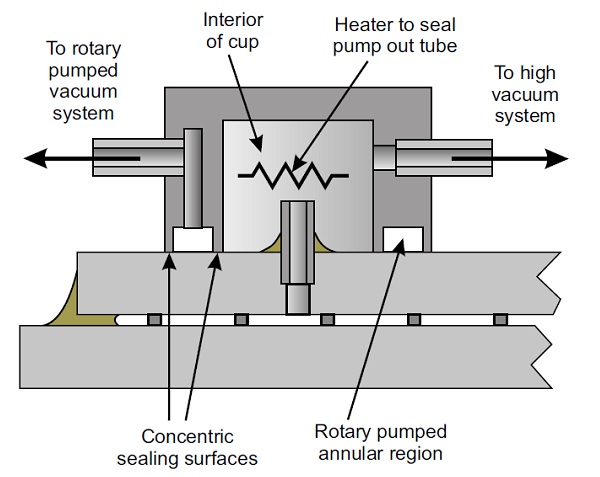
A feature of this commercial development was the effectiveness of the interactions between NSG and the University. Both parties in the collaboration were completely open to each other about the information that was generated and the issues that needed to be addressed. The University’s research program continued to provide new information of relevance to the product development at NSG.
Much of the University’s work was stimulated by issues that emerged from the production process. For its part, NSG was unshakable in its resolve to make the project succeed, even when significant technical challenges arose that required major changes in production processes.
In hindsight, the decision by NSG to commercialise a VIG product must be regarded as very courageous. NSG committed to this goal at a time when many other companies took the view that commercial development of the VIG concept was too risky and costly.
As it turned out, the costs involved were much larger than originally anticipated, and the technological challenges were also much greater. Despite concerns about the viability on this enterprise, NSG chose to work these issues through, and over time this technology has become one of the company’s premium products.
The demonstration of the technical and commercial feasibility of VIG stimulated several other organisations to commence work on VIG, leading to many publications and patents.
2001 to present
The past 16 years have been a period of consolidation of VIG technology. Several million VIG units have been manufactured by NSG, and have shown excellent reliability in many types of building, Several major research studies have been undertaken at other academic institutions, in government laboratories and by other companies. VIG products made by other manufacturers are in the market or under development. There has been extensive relevant publication and patenting.
Current commercially available VIGs using annealed glass can have centre-of-glazing Uvalues as low as 0.6 W m-2 K-1 in a structure 10 mm thick. VIGs are also being used in hybrid glazings and laminated assemblies. The International Standards Organisation (ISO) is developing Standards for this technology.
This work is being undertaken by Working Group 10 (Glass in building – Product considerations – Vacuum glass) of ISO Technical Committee 160, Sub-committee 1. Part 1 of a draft Standard for measurement of the thermal insulating properties of VIG is in the process of ratification. Work has commenced on Part 2 relating to temperatureinduced effects in VIG.
Future prospects
Although VIG is now a well established technology, there is considerable scope for further development on many aspects of its design, manufacture and marketing. Several of these are listed below. Those currently under active development or consideration are indicated by an asterisk (*)..
Design
- VIG made with tempered glass* offers the prospect of higher levels of thermal insulation, and broader areas of application. A major challenge for this design approach is the development of a relatively low temperature edge seal. Departures from planarity of the tempered glass sheets need to be accommodated so that the mechanical load due to atmospheric pressure is uniformly distributed over the pillars.
- Performance improvements are also likely with innovative pillar designs, including pillars made from thermally insulating materials*, high strength materials*, and by melting small areas on the glass sheets*. Pillars are under development with low friction bearing surfaces*, and different geometries*, that facilitate a small amount of relative lateral movement of the glass sheets.
- It is likely that the pillar separation in current VIGs with annealed glass can be increased*, resulting in improved thermal insulation,
- VIGs with a flexible edge seal* would experience very low stresses and bending under temperature differentials. However, in such designs the pillars must slide repetitively across the glass. Because of the high stresses in the glass sheets near the pillars, the author considers it unlikely that this type of edge seal will prove viable.
Production technology
- There are many alternative possibilities for making the edge seal, including low temperature solder glass *, lead free solder glass*, and metal*. All currently available polymer materials are far too permeable for this application. In the author’s opinion, this is unlikely to change.
- There are also many different design possibilities for the evacuation port of the device*.
- VIG production technology is sufficiently well understood that a continuous manufacturing process can now be implemented*. Although relatively capital intensive, such an approach would enable larger numbers of VIGs to be made, and this could result in significant cost reductions in the product.
- In principle, it is possible to form the edge seal in the VIG within a highly evacuated space, eliminating the need for a pump out port. Challenges in this approach include bubbling of the molten solder glass, vacuum degradation due to outgassing of the hot internal surfaces after sealing, and avoiding bending of the glass sheets in the edge region.
Conclusion
The history of VIG is quite unusual for a technological development. There was an extraordinarily long period (75 years) between the initial patent describing the concept and its first realisation in the laboratory. This was followed by a relatively short period (8 years) of research, development and technology transfer, leading to the launch of the first commercial VIG product.
Over the subsequent 20 years, the development of the technology has continued, although most currently available products have much in common with early commercial designs. In addition, although sales of VIG have steadily increased and the product has exhibited high reliability in practical installations, only a few manufacturers are currently active in the field.
NSG is in the process of completing a significant expansion of its VIG manufacturing capability. In addition, there is currently a high level of interest in the technology, both at the research level, and in product development programs by other manufacturers.
It is therefore not unreasonable to expect that the next few years will see more manufacturers entering the VIG market, and substantially increased sales volumes. Should this occur, new and possibly better performing VIG products made using different processes will become available, and the cost of VIG will decrease.
The capital investment for a VIG manufacturing facility will always be greater than for a conventional IG plant of comparable capacity. The unit area cost of VIG is therefore always likely to be greater than for conventional IG. In large volume manufacture, however, materials cost should dominate, and the cost differential between the two technologies need not necessarily be large.
The capability of VIG to achieve high levels of thermal insulation, the high reliability afforded by the hermetic edge seal, and the very small thickness of the structure, are likely to make VIG technology an increasingly attractive choice in the market for high performance thermally insulating glazing.
Acknowledgments
VIG would not exist as it is today without the many contributions by the author’s students at the University of Sydney, and his colleagues in the University’s School of Physics, at NSG, and in other research laboratories. The author dedicates this paper to Stephen Robinson, whose student project led to the first practical VIG samples, and Hideo Kawahara, whose vision, dedication and tenacity enabled this technology to be commercialised successfully. Sadly, neither is alive today to reflect on the significance of their achievements.
References
1. R E Collins, A C Fischer-Cripps and J-Z Tang, Solar Energy 49, 333-50 (1992)
2. R E Collins et al., Building and Environment 30, 459-92 (1995)
3. R E Collins and T M Simko, Solar Energy 62, 189-213 (1998)
4. A Zoller, German Patent No. 387655 (1913)
5. S J Robinson and R E Collins, ISES World Congress, Int. Solar Energy Soc., Kobe, Japan (1989)
6. T M Simko, A C Fischer-Cripps and R E Collins, Solar Energy 63, 1-21 (1988)
7. C J Dey et al., Rev. Sci. Instr. 69, 39-2947 (1998)
8. N Ng, R E Collins and C So, J. Vac. Sci. Tech. A21, 1776-83 (2003)
9. C Kocer and R E Collins, J. Amer. Ceram. Soc. 84, 2585-93 (2001)
10. A C Fischer-Cripps and R E Collins, Building and Environment 30, 29-40 (1995)
11. Q-C Zhang et al., Int. J. Heat Mass Transfer 40, 61-71 (1997)
12. N Ng, R E Collins and M Lenzen, J. Vac. Sci. Technol. A20, 1384-9 (2002)
Comments
The vacuum installation has over the past been of tremendous impact to us.