We’ve all heard the jarring crack of a pebble or piece of road debris hitting our car windshield. We may see an immediate pinhole or crack and know this will inevitably spider-web its way across the glass and cause the windshield to break if left untreated.
That a tiny impact can cause significant glass damage isn’t limited to our vehicles. Similar issues happen with commercial glazing.
Minor edge damage during glass handling, a scratch or nick during installation, a design flaw, or a natural imperfection in the glass could all result in spontaneous breakage – the seemingly unprompted shattering of glass.
For design and construction professionals, understanding how and why glass breaks can be key to prevention.
SAFETY GLAZING
In general, glass is made by fusing silica (a component of sand), sodium carbonate (or soda ash, which lowers the melting point of silica), and calcium oxide (or lime, which adds chemical stability) together at a high temperature.
The glass is then cooled, shaped, and cooled further (a process called annealing) to stabilize and strengthen it.
Standard annealed glass can be used for windows in low-traffic areas, but most codes mandate safety glazing instead. If broken, annealed glass will shatter into sharp shards and pieces.
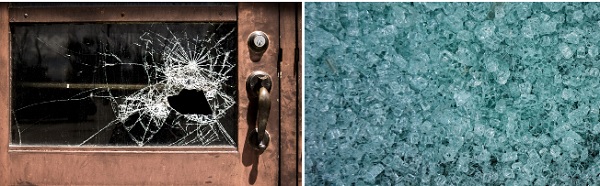
Safety glazing reduces injury potential from breakage. The glass is treated to strengthen and change its breakage properties. There are two main types of safety glazing: tempered glass and laminated glass.
Heat-strengthened glass provides more stability than annealed but cannot be considered safety glazing because it has the potential to form large shards when broken.
Both tempered and heat-strengthened glass are heat treated to 1200 degrees F (650 degrees C) and force-cooled to create surface or edge compression.
Tempered glass is cooled very quickly, creating higher surface and edge compression.
Heat-strengthened glass is cooled slower for lower surface and edge compression than tempered glass, but still higher properties than annealed glass.

Also called toughened glass, tempered glass has been heat treated for a minimum surface compression of 10,000 PSI and impact resistance four times stronger than annealed glass.
The fast cooling – or quenching – process puts the surfaces and edges of glass in compression while the center remains in tension.
The process changes the break characteristic of the glass, so that when shattered, it breaks into tiny pebble-size pieces and reduces the injury potential of sharp shards.
Tempered glass cannot be cut. Heat-strengthened glass has been heat treated for a surface compression of 3,500-7,500.
At twice the surface compression of annealed glass, heat-strengthened glazing is used in place of general glazing where additional thermal and wind protection are desired.
Another safety glazing option, laminated glass uses a combination of heat and pressure to sandwich one or more layers of polyvinyl butyral (PVB) between two or more layers of glass.
The laminated glass layers hold the panel together in case of breakage while increasing strength and edge stability.
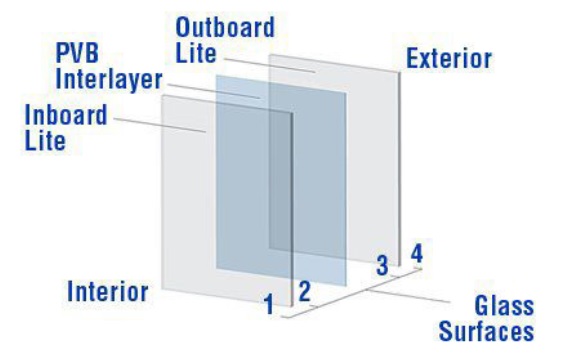
CAUSES OF BREAKAGE
An inherently fragile building material, glass always has the potential to break.
While manufacturers produce safety glazing and self-healing coatings, and develop new methods to make glass stronger and safer, design and construction professionals must be mindful of common causes of breakage and preventive measures.
HANDLING DAMAGE
The most common cause of glass breakage comes from edge or surface damage during handling.
Even the slightest nick or chip in the glass during packaging, shipping, or installation can – over time and natural expansion and contraction through temperature changes and subtle building movement – build up a stress concentration around the imperfection, which can lead to future breakage.
Although seemingly spontaneous, these types of breaks have a natural cause. Proper handling by trained professional glaziers is a primary means to help avoid these types of breaks.
FRAME-RELATED BREAKAGE
If the gaskets, setting blocks, or edge blocks in a metal window or curtain frame are missing, damaged, or not sufficient to cushion the glass against glass-to-metal contact caused by temperature changes and building movement, stresses can accumulate that eventually lead to breakage.
Building or framing system movement due to wind or environmental conditions may also contribute to glass-to-metal contact.
An improperly engineered glass pane that is too large or thin for its location can be damaged by wind or weather.
Careful design review, proper engineering, and professional installation can prevent frame-related spontaneous breakage.
THERMAL STRESS BREAKAGE
With increased emphasis on natural daylighting and passive solar design, thermal stress-related glass breakage should be a concern.
When the center of a pane of glass becomes hotter than its edge, expansion of the heated glass center can create tensile stress around the edge.
If the thermal stress exceeds the edge strength, the glass can break.
Large insulated glass units (IGUs), particularly in combination with solar control coatings, require thermal analysis to avoid stressrelated breakage.
Thermal modeling and design adjustments can be made during the design phase to reduce thermal stressrelated spontaneous breakage.
INCLUSION BREAKAGE
It’s relatively rare, but during the tempering process, nickel contaminants in the float glass can cause nickel sulfide stones to form.
Over time, when the installed tempered glass is exposed to natural temperature changes, the tiny stone may expand, causing the glass to shatter.
Nickel sulfide stones can be present in annealed and heatstrengthened glass, but are not subject to spontaneous breakage because the slower cooling cycle either halts the stones’ phase change or traps them before they can expand volumetrically.
There’s no known technology to eliminate nickel sulfide stones and they can be so small – 0.003 to 0.015 inches in diameter – that there’s also no way to visually inspect for their presence in float glass.
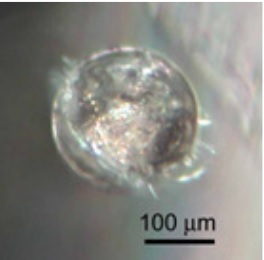
ASTM guidelines permit blemishes, including nickel sulfide stones, of between 0.020 and 0.1 of an inch, but this is much larger than the typical stone size. Refer to ASTM C1036 Standard Specification for Flat Glass for full details.
Some manufacturers take precautions for nickel-sulfide stone presence.
PPG and other North American glass manufacturers do not use nickel in any primary batch formulations, ban nickelbearing metals from operations, and employ magnetic separators.
PPG also recommends heat-strengthened glass when heat-treated glass is needed, except where codes mandate safety glazing.
Industry consultant Bill Coddington, cited in a 2008 Glass.com article stated, “The primary glass plants in the United States do an excellent job selecting the raw materials and production equipment used in order to minimize the chances that nickel could be introduced into the float glass batch.”
From top: two examples of glass edge damage (top image courtesy Bruening Glass Works); tempered glass breakage - note the glass remains within the frame; possible inclusion break identified by “butterfly-wing” break pattern at center
HEAT SOAKING
Heat soaking is often used in high-demand applications such as point-supported walls, or when reducing probability of spontaneous breakage is a priority.
Examples include railings, doors, heavy tempered glass, and insulating glass units.
During heat soaking, a sample batch or full lot of tempered glass panels is exposed to temperatures of 288 to 316 degrees C (550 to 660 degrees F) for up to four hours in order to test for and mitigate inclusions.
The process prompts any inclusions to change phase and break the glass before it is shipped.
The industry disagrees about heat soaking’s “break-now-notlater” approach. The process reduces the probability of inclusionrelated breakage, but can’t prevent or guarantee other inclusions might not change and spur breakage in the future.
In fact, the process can cause small, stable inclusions to begin phase change during heat soaking and potentially complete the transformation after the glass is installed.
Heat soaking can also negatively affect surface compression and inherent strength properties, and the added process – and its associated handling – can create more chances for edge damage, scratches, or changes to surface coating properties.
Heat soaking after fabrication may destroy some flawed glass panels, but is a costly, time-consuming process that will not eliminate all nickel sulfide inclusions.
JE Berkowitz offers heat soaking to reduce the incidence of spontaneous breakage due to nickel sulfide inclusions and fabrication damage in tempered glass, adhering to the international standard EN 14179-1:2005 (HST).
The standard, officially Glass in Building - Heat Soaked Thermally Toughened Soda Lime Silicate Safety Glass, defines the heat soak process system together with tolerances for flatness, edgework, fragmentation, and physical and mechanical characteristics of monolithic flat heat soaked thermally toughened soda lime silicate safety glass for use in buildings.
In the JE Berkowitz heat soaking process, fully tempered glass is stacked in a specially constructed and certified oven, heated to 550 degrees F, and gradually cooled.
The total process takes about six hours: two hours to ramp up the temperature, approximately two to four hours of dwell time, and another two hours to ramp down the temperature.
Thermal cupples are placed on the glass to monitor temperatures. Yet, the process only reduces probability of breakage from a standard eight lites in 1,000 to five lites in 1,000.
BEST PRACTICES
Michael L. Rupert, PPG Industries’ director of technical services, wrote in a December 2013 Construction Specifier article:
“A laminated glass interlayer in combination with tempered or heatstrengthened glass may offer the optimal blend of characteristics for applications where the risk of injury from glass fallout is a primary concern.
For non-safety glass applications, where strength and resistance to spontaneous breakage is desired, nonlaminated heat-strengthened glass should be considered due to its lower costs.”
As with any design specification, glazing requires consideration of many factors, safety included. In most cases, “spontaneous” breakage has a root cause that can be traced to design, manufacturing, or installation.
When design and construction professionals and manufacturers collaborate and communicate, problems can be prevented and breakage can be avoided.
MORE INFORMATION
Technical Document TD-138: Heat Treated Glass for Architectural Glazing, PPG Glass
Cracked Up: Experts Share Insights on the Heat-Soaking Process, Glass.com, June 2008
Spontaneous Glass Breakage: Why it happens and what to do about it, Construction Specifier, December 2013
Nickel Sulfide Inclusions: Important Issues for the Designer, 2003
Comments
Hi
Great article on exploding glass will come in useful for our semi framed shower screens