This paper was first presented at GPD 2023.
Link to the full GPD 2023 conference book: https://www.gpd.fi/GPD2023_proceedings_book/
Authors:
- Enrico Cutri - Dow Gmbh, Switzerland
- Valérie Hayez - Dow Silicones, Belgium
- Jona Vetterli - Luechinger+Meyer
- Philippe Willareth - Luechinger+Meyer
Abstract
Recently, a global effort of the construction industry has been observed to achieve more sustainability and circularity in design, aligned with legislative requirements such as the ESPR or the EU Green Deal. This paper will review the impact of silicones at various levels of a sustainable design. It is well known that the use of silicone sealants strongly contributes toward a durable air and water tight building envelope and enables energy saving multi pane glazing. Both applications significantly contribute to improving energy efficiency and hence reducing the operational carbon of a façade.
The benefit during the lifetime of the building outweighs several times the carbon emissions required during the production of these silicones, especially when using the DOWSIL™ Carbon-Neutral Silicones Service for façade applications. Furthermore, silicones can also contribute at other levels of a sustainable design, such as material efficiency. Silicone bonding can help reduce resource use, such as aluminium used for frames. Silicones as bonding system are easier to disassemble at end of life compared to more rigid assembly methods. But silicones also have the potential to enable the reuse of glass in refurbishment projects.
1. Introduction
The current focus of builders and designers is to respect the principle of sustainable construction (Fig1). Silicones and the use of structural glazing (bonding) in façades have been identified as a key contributor to a more energy efficient building envelope [1].
Silicones enable the sealing of energy saving multi pane glazing elements (double or triple insulating glass units). The bonding of these units on a metal frame combined with the use of long lasting weatherseals ensure a durable, water and air-tight building skin with high energy efficiency that reduces operational carbon. Unlike organic chemistries, the durability of the silicone versus organic chemistries limits the need for replacement during the lifetime of the façade [1]. Besides durability and energy efficiency, silicones also help ensure good indoor air quality thanks to their low VOC [2].
The main focus of this paper considers how silicones can increase sustainability of building materials when choosing low embodied carbon silicone or even carbon neutral silicone services. The second focus of this paper is on sustainable design, whereby the contribution of silicones to material efficiency and respecting the inverted waste hierarchy pyramid (fig 2) will be examined, focusing more specifically on how the use of silicones can reduce the requirement for other materials (such as aluminium) and allow reuse of materials such as glass. Both aspects contribute to reducing the embodied carbon of a design.
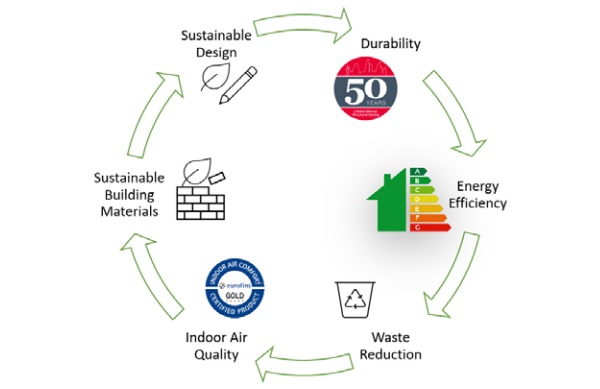
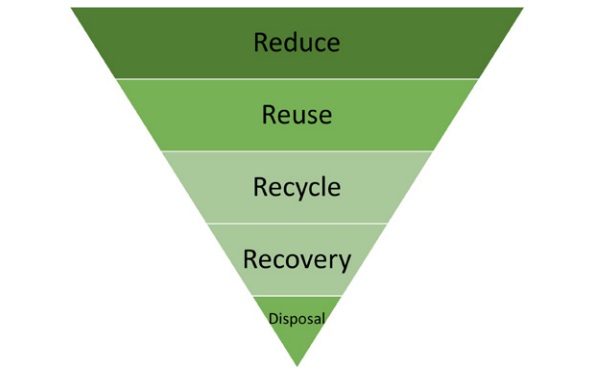
2. Journey from low embodied to carbon neutral silicones for façades
The main contributor to the embodied carbon balance of a silicone lies in the production of its main ingredient, silicon metal which accounts for more than 60% of the total balance (fig 3).
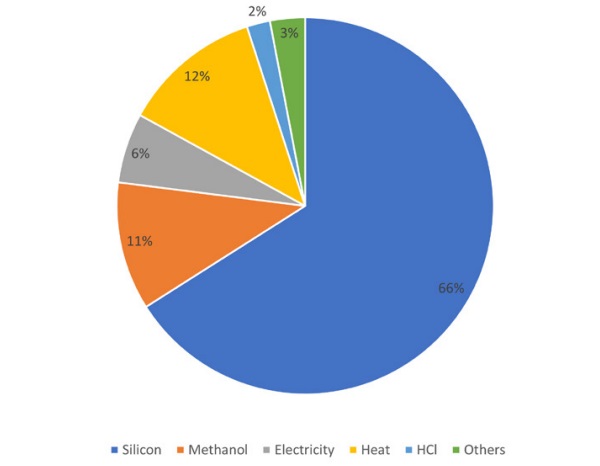
This energy intensive process has been significantly decarbonized by using renewable energy, mainly hydro power and photovoltaic. The other elements required for the production of silicon metal such as sand SiO2, wood chips or charcoal are all sustainably sourced. The intermediate plants for the production of polymers and the finishing plant where the silicone sealant is eventually manufactured also benefit from the introduction of clean energy. These combined efforts allow a significant reduction in the Greenhouse gas emissions (GHG) of Dow’s silicone sealants for structural glazing (SG), insulating glazing (IG) and weathersealing (WS) [3], compared to the global industry average [1] or European values [4]. To achieve PAS2060 certification for our DOWSIL™ Façade silicones, Dow has committed to continuous annual reductions of embodied carbon by 1% [5].
As we wait to achieve full carbon neutrality, a verified carbon neutrality program following PAS2060 has been set up to compensate for the residual embodied carbon using carbon insets obtained from Dow’s own eucalyptus plantation and value chain. The process of compensation for the residual emissions is tracked and audited annually, whereby used carbon insets are retired from the available pool. A Certificate of carbon neutrality is attributed to a façade of a building depending on the volume and type of silicone used. Thanks to these efforts, Dow silicones can be considered as sustainable building materials and their use can enable more benefits such as material efficiency.
3. Material efficiency
3.1. Reduce
Several studies [6, 7, 8] have compared captive systems to SG systems. Ensuring comparable thermal and structural performance by selecting frame profiles with similar sightline and depth and identical IGU, it is possible to quantify how much additional aluminium a captive system uses versus an SG system. The benefit adds up quickly and is not only limited to the saving of aluminium from the capped profiles. It is well known that bonding a rigid element such as glass into a more flexible profile can transfer the rigidity of the glass to the profile.
This benefit is especially pronounced in residential PVC windows, due to the opening and closing functions. For these types of systems, the use of metal reinforcement bars can be avoided in larger pane dimensions when bonding the units [9]. Today, a clause in the EN13830 [10] also enables façade designers to prove the composite effect through advanced calculation methods and avoid the use of more rigid aluminium profiles in specific loading cases, such as high load areas of corners. This typically reduces aluminium material use. Additionally, wet applied weathersealants do not need replacement unlike EPDM gaskets during the façade lifetime which further saves on material.
3.2. Remanufacturing and Reuse
Façade experts, such as engineers, designers, architects and specialist contractors, and more broadly the whole supply industry, are all used to working with highly engineered materials. These materials are combined in hybrid design solutions to achieve optimal performances. Energy for heating and cooling systems has been significantly minimized in recent decades, thanks to increased equipment efficiency and thermal insulation, as well as low air permeability of building envelopes. The building service energy field has limited potential for further reductions.
To align with current sustainability targets, further reduction of the global warming potential (GWP) and minimization of material resources is required, shifting focus from an optimal performance to a fit-for-purpose adequate design. For example, wider critical viewing distances as well as comfort cuts are more easily accepted nowadays than before. The next major steps for reducing the GWP are the materials used for erecting and renovating buildings.
Unlike the times, when material costs were high and labor costs were low, new sustainable design must be optimized by selecting materials assessed for minimal kilogram usage of carbon dioxide per function and expected service years. For the building envelope, this function is simplified using a representative area of 1m², considering that the required performance for the building envelope is reached. This leads to the expression of kg CO₂-eq /m² y.
The current mission of engineers is to minimize the materials required and to use materials with a minimum GWP. Today’s designs must consider reusing, remanufacturing and constructing for circularity. As façade experts, this is our chance and opportunity to use our skills as engineers and designers to find or create solutions.
It is a fact that we are part of a very CO2 and resource intensive building industry, that provides the essential design, engineering and infrastructure for the human well-being. As a player in this process, we also have the privilege and responsibility to positively impact the continuing efforts to develop sustainable solutions by cutting the GWP and minimize the used resources.
Alongside other potential ways such as using organically grown materials, reusing and remanufacturing are two similar and very effective strategies for finding and enabling sustainable solutions. The described remanufacturing and reusing initiatives, in execution and in the design stage, show how reusing and remanufacturing can be done, not curated but on an industrial level. Not curated but industrial means, that the almost artistic individual and therefore repetitional architectural assessments and positioning on the building can be avoided. Instead, the reused or remanufactured components can be treated after “one” principal selection and accepted as industrial building parts.
To achieve the principal acceptance and, more importantly, the technical sign off (such as the serviceability and safety) the from the first live cycle marked or worn-down building parts need to be cleaned, renewed or combined with enabler materials to reach specific criteria. Reaching the acceptance and sign-off means that we can “harvest” from the built environment, which is a tremendous urban mine. The reuse and remanufacturing process as well as the chosen enabling materials and processes energy need to be unproblematic, clean and efficient.
In the case of our remanufacturing and reuse projects, the energy intensive glass used as cladding material for spandrels or opaque wall build built ups are the mined materials. Many windows, window façades or curtain walls from the 1940s to the 1970s are currently replaced or the whole buildings are deconstructed. The established dismantling and deconstruction process demands a component separation. Windows are taken away in containers and the majority of the glazing remains unbroken in the frames. The formats vary from small window sizes to shopfront sizes. Most of this glass is monolithic and in an annealed state, typically 3mm to 8mm thick.
In Switzerland, we have been able to recover approx. 61’000 tonnes of recorded flat glass per year which is fed into the recycling process. The recovered figure does not include the glass from large industrial enterprises. Once taken away from site or works, a substantial part of the glass is shredded out of the frames and processed to foam-glass as compression resistant insulation or road fill. By avoiding the downcycling and activating the urban glass mines for reuse and remanufacturing, the containers must be replaced by glass cradles. The safe storage and transport in the glass cradle and the cutting to size are the only steps to be carried out prior the industrial reuse und remanufacturing processes.
3.3. Recycle
Optimizing material and energy efficiency is crucial to ensure a sustainable design. However, one aspect which should not be overseen is the end of life consideration and ensuring reuse and recycle can take place. In this regard the façade industry is focussed on assessing how bonded units can be dismantled and their high value components, such as glass or metal, can be reused. Silicone sealants should enable and facilitate, not prevent this step. At first sight, there may seem to be a contradiction between the durability of silicone bonded assemblies and the need for disassembly for repair or at end of life.
However, silicone bonding has specific advantages over other adhesives that enable maintenance, reuse and recycling. In contrast to more rigid bonding solutions (eg PU) silicones have good potential for disassembly at end of life. The method developed for the dismantling of bonded glazing can further benefit from over 50 years of expertise in façade inspection, deglazing and repair exercises. Thanks to the durability of DOWSIL™ Silicone, it is possible to leave a layer of silicone on the substrate which can be used to bond again on the frame, for more efficient glazing provided that the origin of the original silicone and compatibility with the new silicone can be confirmed.
If a reuse of glass or frame is not desired the silicone can be mechanically removed from the disassembled substrates. In the pursuit of full façade circularity from glass, to frame up to silicone sealants, Dow’s ambitions is to take a leading role in supporting the development and implementation of more circular economy, taking into account a product’s lifecycle from creation to use and disposal – in everything we do and create. Finally, successful implementation requires industry collaboration, to enable a reverse supply chain, dismantlement ecosystem, in a sustainable and economically feasible way.
4. Technical validation of reuse and remanufacturing
The current paper aims to develop the concept of reuse and remanufacturing through two case studies, Hero strasse and Lagerstrasse. On the project Herostrasse in Zurich, we do mine the glass directly onsite. For further derived projects as Lagerstrasse or Badenerstrasse in Zurich, we use the deconstruction of windows as mine for old flat glass.
4.1. Remanufacturing the Spandrel Glass Panels of the Herostrasse Project
The, for the construction time very typical, office building is today used as a vocational college. Since taking the building into service in 1973, no significant servicing or refurbishment work has been carried out. Therefore, the condition of the façade varies a great deal. The façade consists of floor to ceiling height elements in timber, steel and glass. The balustrade zone consists of a timber chipboard, 30mm mineral wool, a fiber cement board, a ventilation gap and enameled glass sheet as cladding. A timber-aluminium window and venetian-blinds are integrated above the balustrade build up.
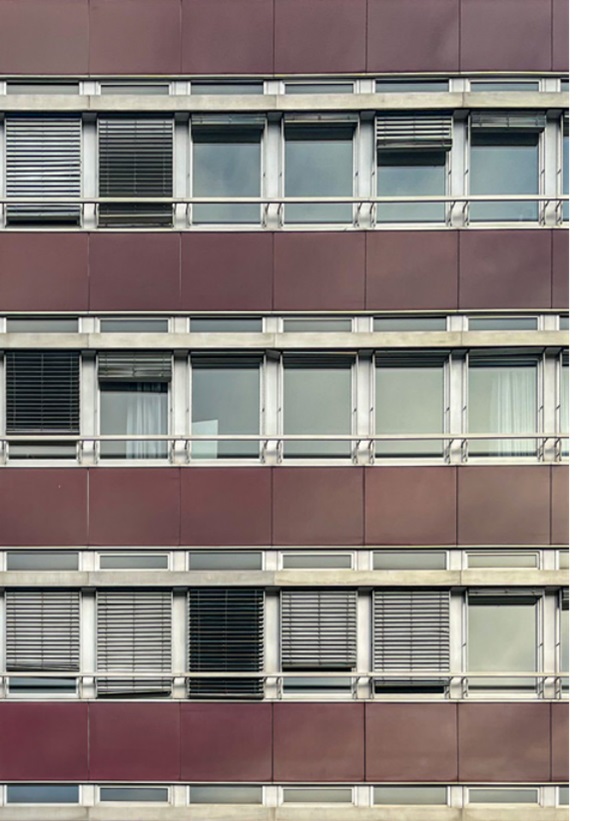
In 2021, the city of Zürich decided to refurbish the façades without taking the building out of service, and therefore without touching the interior surfaces and other building components. In a competition entry with Ekinci Architekten GmbH, the chosen concept proposed to maintain the balustrade timber buildup on the inside. Therefore, the interior buildups such as floors, ceiling, partition walls, cabling channels, require none or only a minimum of adjustment work. To meet the compulsory energy and acoustic targets, the insulation layers and the windows should be replaced with state of the art components, including a sound dampening ventilation hatch. As a key part of the competition proposal, the characteristic red enameled glass cladding was proposed to be conserved. In summary, the proposal was to reuse the inner, structural active balustrade buildup and the glass as cladding material.
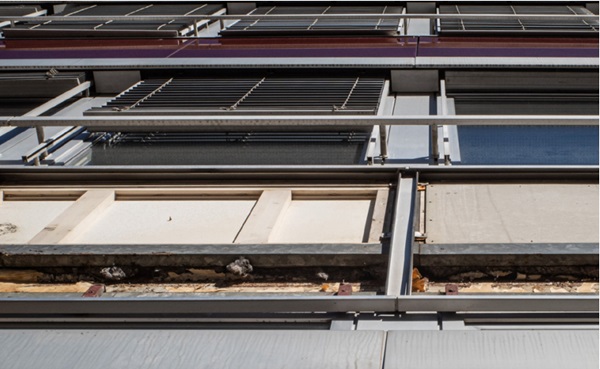
As expected, 50-year-old building parts were not necessarily meeting today’s requirements, including the glass cladding. New glass not improve the appearance but would meet all relevant regulations. On the Herostrasse, the building perimeter is accessible and highly frequented. For glass cladding, a safe failure mode and post failure resistance are demanded. Therefore, a new glass cladding would consist of laminated safety glass. Early dismantling allowed investigation of the technical buildups and time to analyze the glasses. The optical stress assessment, carried out by the Competence Centre Facade Engineering of the Lucerne University, evidenced a pre-stress in the glass. The variation of the stress readings indicated that the glass had been thermally prestressed.
The level of the prestress lies between a heat strengthened and a fully toughened glass. After the technical and visual assessment, it became clear that the glass could be reused visually without any negative effects. A life span of another 40 to 50 years was deemed to be possible. Nevertheless, the technical investigation showed that the glass was lacking the required impact performance consistent with safe failure mode and a post failure resistance. A reuse by simple cleaning and reapplication was therefore not possible. A remanufacturing process was required to meet state-of-the-art performances. In case of the Herostrasse cladding, we had to provide a robust mounting system and a post failure resistance.
As post lamination is not possible yet, and as it would increase the GWP due to the new glass pane and energy required for the lamination, alternative solutions were investigated. Laminar bonding based on silicone has been identified as a possible enabler technology and material. Besides the technical benefits for application and services, the possible and simple material separation at the endof-life span has been an important factor for choosing the solution. Eventually, using carbon neutral silicone for the coating and recycled metal for the rack (or alternatively a material which can easily be recycled) will avoid increasing the GWP.
For the project, silicone has been used to bond a perforated back sheet in aluminium to the glass. The composite buildup of the architectural inspired enameled glass, silicone and the perforated back sheet ensures the required performance such as invisible fixation, unchanged glass color and glass haptic, safe failure mode and post failure resistance. During the early stages of the project, sample applications, first bonding and compatibility tests were carried out.
The application trials with GYSO AG and Dow’s testing proofed that remanufacturing works efficiently and is safe. For the Herostrasse project, remanufacturing is ready for the execution. Therefore, the glass cladding will be dismantled and, as soon as the glass pieces are stored in cradles, the aspired industrial based remanufacturing process can start. Once glass is cleaned, laminar bonding is applied and the back sheet is embedded into the silicone. Silicone can be dispensed in several ways adapted to the selected back sheet, to ensure full coverage. Silicone choice is determined by project needs such as available dispensing equipment, time to deliver etc. Its thickness is optimized to ensure full embedding whilst minimizing material use. The correct thickness is obtained using cast silicone distance holders. Finally, the glass pieces can be delivered back on site.
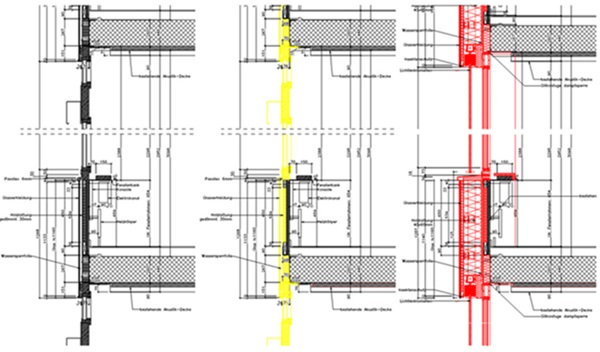
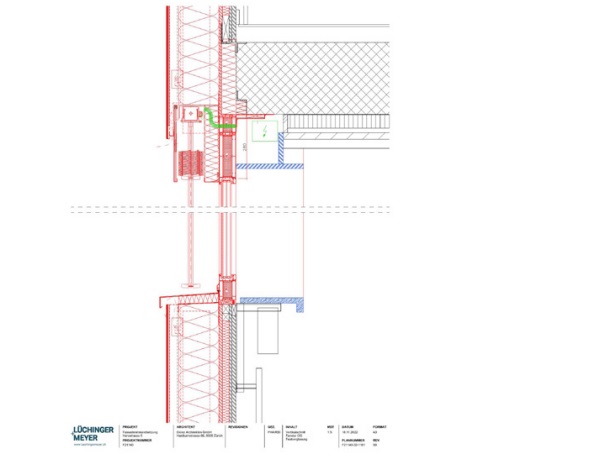
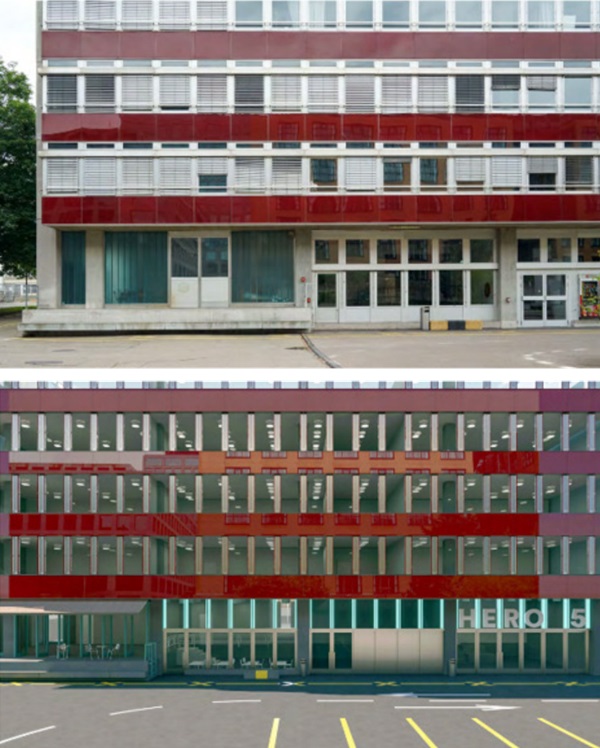
4.2. Reusing Generic Window Glass
For the projects Lagerstrasse and Badenerstrasse with Michael Meier Marius Hug Architekten AG and further upcoming projects, the idea of reused glass cladding has been developed more generically. Similar to the project presented above, glass should be used to clad the opaque façade buildups, providing an almost maintenance free building skin for an approx. 40 to 50 years life span. As a base material, old window glasses are available. For the application, annealed glass with a thickness between 4mm and 6mm are expected. As an addition to the Herostrasse project, the enabler silicone material must also match the color of the reused glass cladding. The clear glass pieces appear with back coatings that look like enameled glass. With silicone application, strong, glossy colors are achievable. Besides coloring, texturing of the surface by blasting (homogeneously or patterned), kiln structuring, shaping by gravity or cold bending are some of the possible design options.
To draw on the enormous potential of the urban glass mine, the application industry, such as specialist façade contractors or glass processors, need to recognize the benefits. Currently, a series of different samples are manually produced by Dow, Lüchinger+Meyer, Gyso and Glassolutions Switzerland to investigate design options, and, even more importantly, to test and document some of the required application steps. The motivation is to create a teaser to show architects that reusing materials offers more than just curating old components. Furthermore, the industry should recognize the potential to establish simple and efficient reuse processes to create sustainable façades and secure a prosperous future for their business.
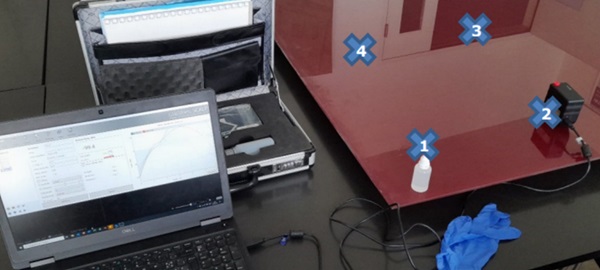
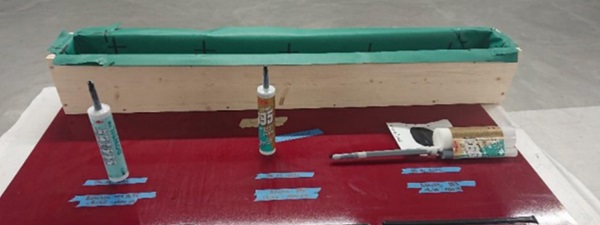

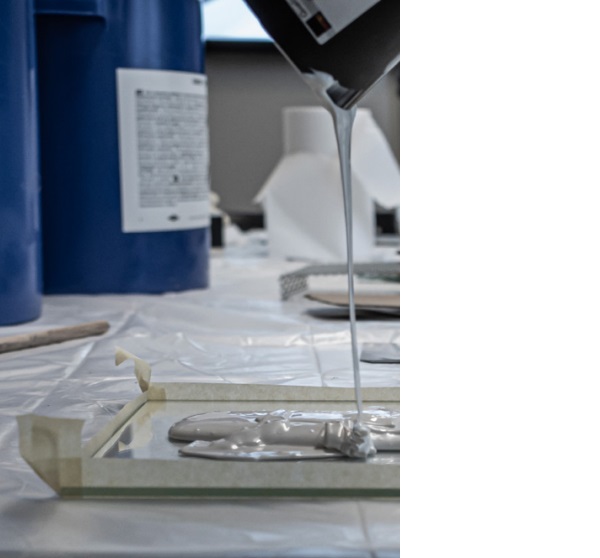
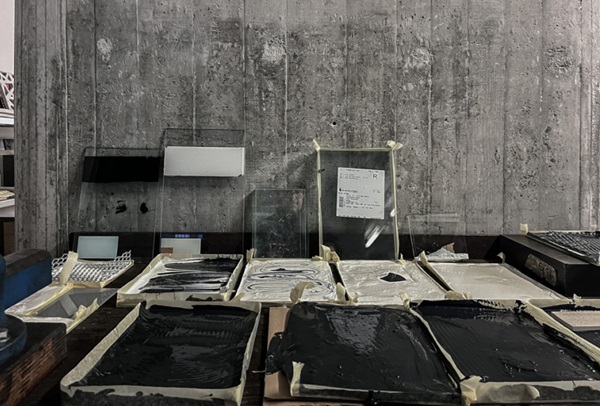
5. Conclusion
Silicones are a material of choice when it comes to respecting the inverted waste hierarchy pyramid and achieving a circular design for façades. Not only can they contribute to material efficiency when building new, they can also enable reuse and remanufacturing. Whether this is the best solution for a project depends on many, sometimes opposing factors. The reused and remanufactured building parts need to suit the projects over the whole life span, need to be economically competitive and need a proven lower GWP than conventional primary or recycling sourced building parts.
The tables show the GWP of the described reuse and remanufacturing solution. At the moment, we assume that the back sheets are from recycling or prime sources. As they do not have any visual criteria, further reuse and more substantial cuts in the GWP are possible. The remanufactured glass cladding of the Herostrasse project is 2 times more beneficial as a similar looking new glass cladding. The proposed reused glass cladding for the Lagerstrasse and Badenerstrasse projects show in comparison to other cladding materials a very low GWP. In both projects, specifying carbon neutral silicone from Dow for the remanufacturing options would further significantly decrease the GWP versus choosing for new glass. This is beneficial to increase the attractiveness of remanufacturing.
The current focus on cladding of opaque façades is due to the fact that these façades are taking larger shares of the building envelope to control overheating with less technical effort. Furthermore, the current development of IGU made of low carbon glass and the use of thin glass leaves can lead to a possible GWP cut of more than 50% already. When assessing the built environment, it becomes clear that there is a gap between the new energy efficient state of the art buildings and the existing majority of buildings with poor energy performance ratings. Making our built environment future-proof, the existing buildings or the building envelopes, need to be upgraded. Reusing and remanufacturing are important techniques to do so with minimal carbon dioxide emissions. The number of suitable buildings for remanufacturing or urban mining are significantly high.
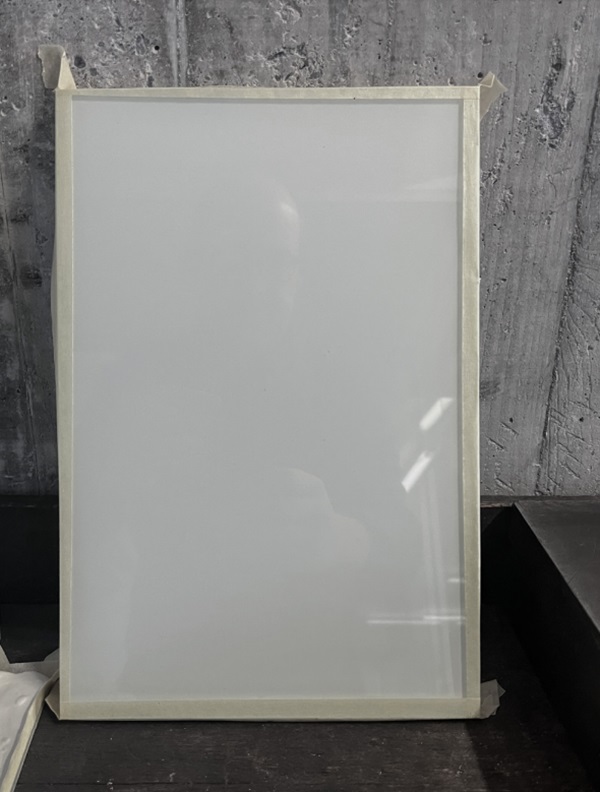
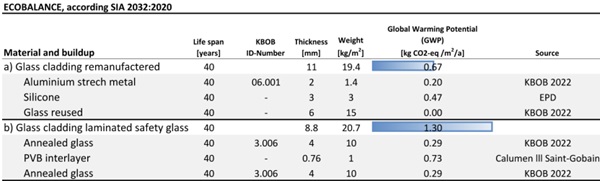
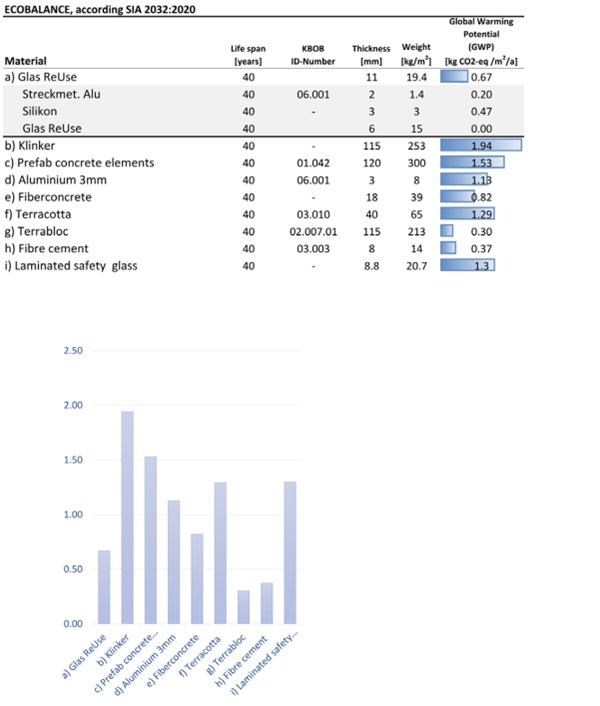
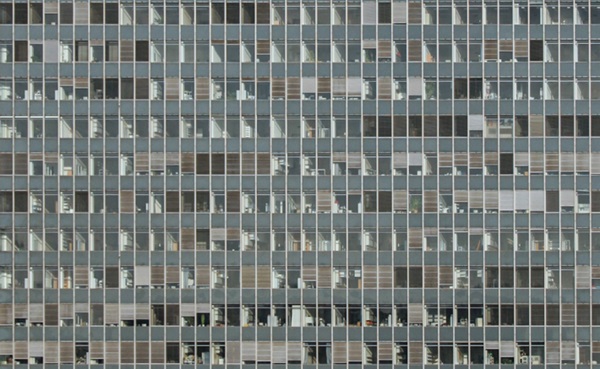
6. References
[1] Global Silicones Council, Silicon-Chemistry Carbon Balance, An assessment of Greenhouse Gas Emissions and Reductions, https://www.silicones.eu/wp-content/uploads/2019/05/SIL_exec-summary_en.pdf, accessed 25/2/2022
[2] VOC, Dow
[3] LCA Dow
[4] Feica EPD, www.feica.eu accessed 27/04/2023
[5] QES Dow
[6] Design and Engineer with less impact, carbon neutral silicones in façades – a window of opportunity, Intelligent Glass Solutions, Spring 2022
[7] Carbary L.D., Albert F., A Thermal Modeling Comparison of Typical Curtainwall Glazing Systems, in Proceedings of Glass Performance Days (2007)
[8] Carbary L.D., Hayez V., Wolf A.T, Bhandari M., Comparisons of Thermal Performance and Energy Consumption of Facades Used in Commercial Buildings, Proceedings of Glass Performance Days (2009)
[9] Wolf A.T., Stiell J., Plettau M., Structural Bonded (Adhered) Window Systems, Conference Paper
[10] EN 13830:2015+A1:2020, Curtain WallingProduct standard