First presented at GPD 2017
After removing the constraints, the laminate holds its curved geometry because of the shear coupling from the polymeric interlayer. Curved panels so obtained are called “warm bent” to distinguish them from “cold-bent” panels, where flat glass is forced into a curve on site and restrained by a frame. An analytical study is presented to describe how, after removal of the constraint, the laminate maintains the curvature only partially, suffering an initial spring-back followed by a long-term relaxation.
The model problem considered here is that of two Euler-Bernoulli beams coupled by a thin viscoelastic adhesive layer. Within a variational approach, we analytically describe the relationship between the initial constrained shape and the shape of the curved beam, which is time-dependent due to the viscosity of the interlayer. Localized contacts and stress concentrations may occur, depending upon the type of profile that is initially imposed. Comparison of the cases of instantaneous or gradual release of the contact with the mould evidences a remarkable reduction of the transient state of stress in the second case.
Introduction
Glass has been used for building purposes since the early nineteenth century, yet this is still a dynamic product that has far from exhausted its potential. The use of curved laminated glass, produced through either hot-bent or cold-bent, is constantly growing and represents the leading feature of a modern architectural trend. Traditional hotbent laminated glass is produced, first, by heating glass sheets up to the softening point and curving them against a negative form; secondly, by performing the lamination process in autoclave.
A crucial issue in this process consists in obtaining glass plies that fit together perfectly, with curvatures only slightly different one another. Coldbending consists in forcing in the desired position initially-flat glass, laminated with the standard process in autoclave, so that the curvature is produced through elastic straining. It allows to construct low-cost freeform glazed surfaces, being the expensive negative forms not necessary, but it requires a strong structural frame to withstand the constraining forces necessary to elastically bend the element, forces without which the glass would return to be straight.
A recent and promising technique to obtain curved laminated glass, that combines the benefits of the aforementioned process, is Warm-Bending, also known as ColdLamination-Bending.
This process consists in three different phases [1, 2], schematically shown in Fig. 1.
Phase I, distortion. The yet-not-coupled package composed by glass plies and polymeric sheets is elastically deformed into the desired shape by means of provisional constraints. In this phase, schematically represented in Fig. 1a, there is a relative shear-slip between the glass plies and the polymeric interlayer. The lamination process in autoclave, at high pressure and temperature, is performed in this deformed configuration.
Phase II, release. When lamination is completed, the constraints are released (Fig. 1b), either instantaneously or gradually, but the now coupled laminated package partially maintains the deformed shape through the interlayer. However, the curved laminate suffers an initial springing back and a relaxation due to the viscosity of the interlayer. Because of this, the state of stress may strongly depend upon the history of the release process.
Phase III, final placement. Finally, the laminated glass panel is fixed in situ in the desired location (Fig. 1c). Again, the viscoelastic behavior of the interlayer causes a redistribution of stress in the glass plies, and the state of stress may further vary because there might be an interaction with the final constraints to the underlying structure, if such constraints are such to prevent the free deformation of the panel.
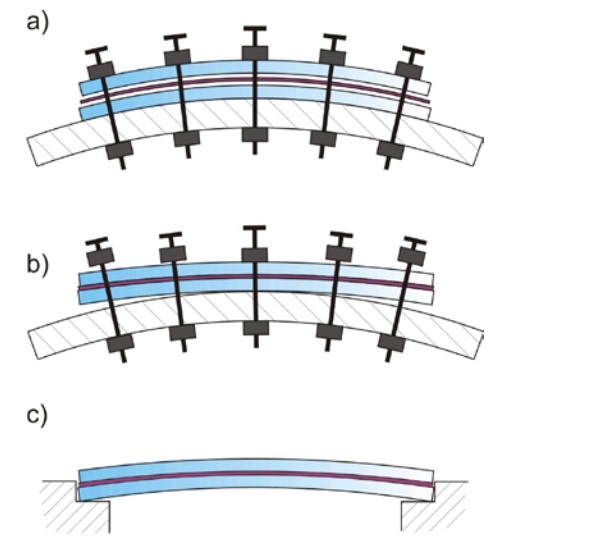
a) Phase I: cold bending of the uncoupled package;
b) Phase II: gradual release after lamination;
c) Phase III: final placement.
In such a way, much of the curvature is preserved, so that the result is similar to a hotbent glass, because no constraining forces are needed, but the production cost is much lower, because the process at high temperature is skipped.
A major issue in the warm-bending process that still needs clarification is how to precisely model the phase when bending takes place and the successive transient relaxation. Here, a simple analytical model is proposed, that can contribute to the understanding of the importance of the various parameters to achieve an optimal design, with particular regard to the prescribed geometry and the kind of release (instantaneous or gradual).
Second, as confirmed later on, stress concentrations may arise in some cases, but this information gets lost in standard finite element analyses, because the use of regular shape functions smears the critical states on the size of the finite element (mesh dependence).
The single-curvature warm-bending of a laminated glass panel is here analyzed by using sandwich beam theory, developing for this particular case a method originally proposed by Newmark et al. [2]. The proposed approach allows finding the relationship between the prescribed deformation in Phase I and the time-evolution of the deformed shape of the panel, and the consequent indication of the spatial and temporal distribution of the stress in both glass plies and interlayer.
Here, we will focus on the first and second phase only. The two paradigmatic cases of circular (constant-curvature) and sinusoidal profile are considered and, for both of them, the transient state during either an instantaneous or a gradual release of the element from the constraining mould is analyzed in detail. Comparisons are made between “stiff” interlayers (like IonoPlasts IP) and “soft” interlayers (like PVB).
Analytical model for Warm-Bending of laminated glass
Let us consider the laminated glass beam schematically shown in Fig. 2a, of length L and width b, composed by two glass layers with elastic modulus E, bonded by a thin polymeric interlayer with shear modulus G(t), which is time-dependent due to the viscoelasticity of the polymer. Let H denote the distance between the centroids of the two glass panels.
By denoting by v (x) the prescribed vertical displacement of the beam in the distortion phase, i.e. the mould shape, the shear distortion due to the relative slip between the faces of the glass plies in contact with the interlayer can be modelled as a distributed shear dislocation in the interlayer, denoted by Ý(x) and highlighted in Fig. 2b.
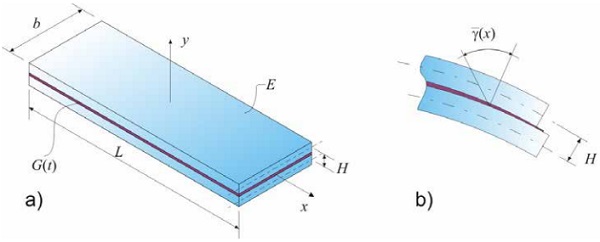
As discussed in [1, 2], the equilibrium equation in y direction of the beam takes the form
where ' denotes differentiation with respect to x,v (x,t) is the vertical displacement of the beam in Phase II and M (x,t) is the applied overall bending moment, related with the constraint reaction forces per unit lenght of the constraints (that is null in case of instantaneous release, but time-decreasing in the case of a gradual release of the laminate).
The time-dependent shear stress in the interlayer, τ(x,t), which provides the shear coupling of the glass plies, is related with the shear strain due to the springing back and relaxation, represented by the difference between the actual shear strain γ(x) and, Ý(x) i.e.,
where Itot represents the moment of inertia of the cross sections of the laminate at the monolithic limit (shear-rigid interlayer).
By expressing γ(x) as a function of v(x,t) and M(x,t) (see [1] for the details), and by substituting (2) into the equilibrium equation (1), an analytical relationship can be found among the prescribed shape in Phase I and the time-evolution of the deformed shape of the beam. Once v(x,t) is known, the shear stress trasmitted scross the interlayer may be evaluated through eq. [2], as illustrated in [2,3]. In the sequel, different shapes for the warm-bent panel and different kind of release, gradual and instantaneous , will be considered.
Furthermore, a comparison is made between the most common commercial polymetric films, i.e., PolyVinyl Butyral [PVB] and Ionoplastic Polymers [IP], which represent paradigmatic examples of a "soft" and a "stiff interlayer", respectively. Their viscoelastic properties are accounted for by evaluating the typical values of their secant shear modulus G8t) at 20°C, for different durations of the load according to the Prony's series recorded in [4].
Effect of the mould shape
As well known, the most common shape for warm bending of laminated glass is the constant curvature one (circular bending). Here, the most common shape for warm bending, i.e. the constant curvature one (circular bending) and the (co)sinusoidal one, i.e.,
respectively, are now considered. Comparison will be made in terms of both time-dependent evolution of the panel shape and of stress arising both in glass plies and interlayer.
Remarkably, for standard geometric parameters, the difference between these two configurations cannot be appreciated with the naked eye, and consequently the aesthetics is not compromised.
Let us consider, as an illustrative example, the cold-bending of a beam of lenght L=2400 mm, width b=800 mm, composed by two glass pliesof thickness 6 mm bonded by an interlayer of thickness 1.52 mm whose the time-dependent shear modulus G(t) is calculated according to [4]. The beam is warm-bent with a mould shape given by eq. [3] with Vmax=144 mm, and then instantaneously released. Both stiff [IP] and soft [PVB] interlayers are analyzed.
Figure 3 Vertical displacement of the beam at various times, for constant-curvature Warm-Bending.
Fig.3 shows the vertical displacement of the beam, as a function of x, in Phase II, i.e. its deformed shape, at different times after the forcing of the beam in the desired position for the case of constant-curvature Warm-Bending, and for PVB and IP interlayers. Fig.4 is its counterpart for (co)sinusoidal Warm-Bending.
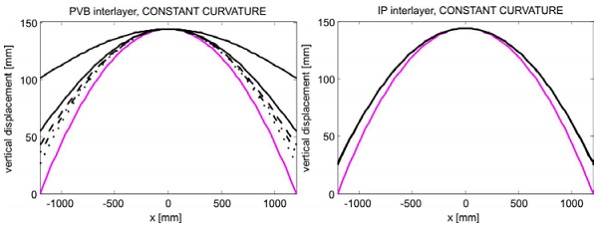
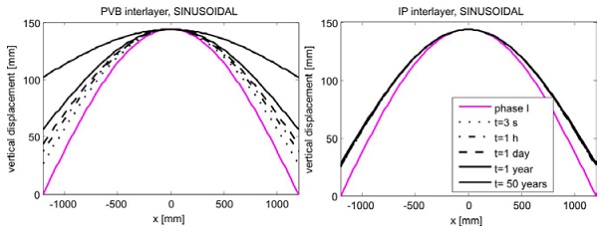
It is evident that the time-dependentdeformed shape of beams subjected to constant-curvature and sinusoidal are very similar. Observe the immediate elastic springing-back and the curvature that is maintained due to the shear coupling offered by the interlayer. Afterwards, the viscosity of te interlayer leads to an overall relaxation of te beam, until the long-term equilibrium configuration is reached.
It is evident that the shear modulus of a IP interlayer is high enough to maintain the deformation in practice for the whole lifetime of the laminated glass element (50 years). On the other hand, much of the initial curvature is lost if one uses a PVB interlayer.
Figures 5 and 6 show the shear stress transmitted by the interlayer, as a function of x, at various times after the removal of the provisional constraints, for PVB and IP interlayers, respectively, for Warm-Bent beams with constant and sinusoidal curvature, respectively. Observe that the stress state is more critical and that the time-decay of the shear stress is slower for stiff (IP) than for soft (IP) interlayers.
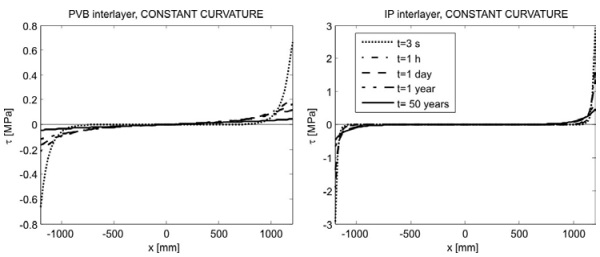
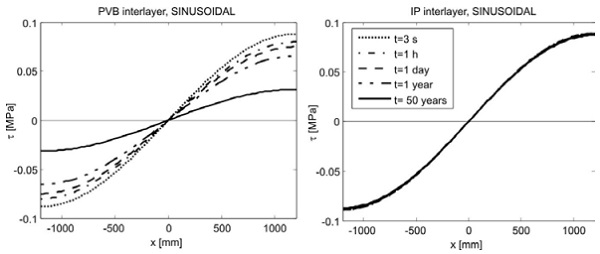
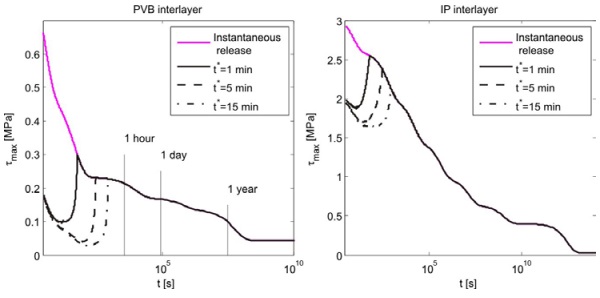
Notice that, in the former case, the shear stress tends to concentrate in the neighbourhood of the beam ends. This may represent a risk of delamination, as sometimes observed in practice.
On the other hand it is evident that, in the latter case, the stress peaks are smoothed out with respect to the case of constant-curvature, even when the shear modulus of the polymer is high. In particular, from comparison of Figures 5 and 6, notice that the sinusoidal WarmBending produces a decrease in terms of maximum shear stress of more than one order of magnitude for PVB interlayers, and of about two orders of magnitude for IP interlayers. It may be verified [3] that the maximum axial stress in the glass plies is in general slightly higher in the case of sinusoidal WarmBending with respect to constant curvature one, but the difference is not relevant.
For example, changing the prescribed deformed shape from constant-curvature to sinusoidal, for the previously defined glass beam with IP interlayer, 3 s after the releasing of the beam, the obtained axial stress increases approximately 20% higher, but, on the other hand, the maximum shear stress in the interlayer is less than 5% of the previous case. Indeed, the most remarkable advantage consists the reduction of the shear stress in the interlayer.
Accurate comparisons between numerical and analytical results [2] have confirmed the accuracy of the proposed model for the evaluation of both the time evolution of the beam shape and of the shear stresses.
Effect of the type of release
As discussed in [3], noteworthy advantages in terms of stress state can be obtained not only through the optimization of the mould profile, but also by designing a gradual release of the laminated beam.
In the framework of the proposed model, the gradual release may be modelled by means of time-decreasing external constraining forces pressing the beam on the mould, that are supposed to linearly decrease from the initial value to zero in a time t*, producing a progressive decrease of the beam-mould contact area, until the laminate is completely released.
Figure 6 shows the maximum shear stress in the interlayer, as a function of time t, in correspondence of the beam’s extremities, for a warm-bent laminated glass beam with PVB and IP interlayer, for the case of constantcurvature mould shape. Comparison is made among the case of instantaneous release and gradual release performed in 1, 5 and 15 minutes.
Obviously, the graphs corresponding to instantaneous and gradual release link up on to each other at t=t*, i.e. at time at which the element gets free of constraints, while for t<t*, the maximum shear stress in the interlayer is always lower in the latter than in the former case.
In other words, the gradual release allows to bypass the initial phases in which the polymer is quite stiff,allowing the viscoelastic effects to soften the material and mitigate the peak stress, while it has no effect in the long- and mid-term stress state. For this reason, it may be noticed that in the PVB case the beneficial effect of the gradual release is more relevant, because the time-decrease of the shear modulus G(t) of PVB is faster than of IP and, hence, the relaxation occurring in the first minutes is higher.
For example, a gradual release performed in 5 minutes leads to a reduction, with respect to the case of instantaneous release, of the maximum shear stress of more than 60% and of the order of 20% for PVB and IP interlayers, respectively, with no considerable increase of the axial stress in the glass plies. Obviously, the beneficial effect is more noticeable for high values of the release duration. However, since the stress is much higher in IP than in PVB, the major advantages are for IP cold-lamination-bent glass beam.
Of course, also in the case of sinusoidal Warm-Bending the shear stress can be further reduced with a gradual release, but since there are no critical states of stress, the polymer viscosity has a weaker influence than in the circular case, and the benefit is less relevant.
Conclusions
Warm-Bending is a promising technique to obtain curved glazed surfaces. It consists, first, in the elastic deformation of packages made of glass plies and polymeric interlayers and, afterwards, in producing the bond in autoclave between glass and polymer. It allows to obtain permanently bent shapes due to the shear coupling of the glass plies through the polymeric interlayer. Due to the polymer viscoelasticity, the laminated element suffers an initial spring-back, followed by a long-term relaxation, whose effects needs to be evaluated for a proper design.
An analytical approach is here proposed, which accounts for the distributed shear dislocation produced by laminating the beam in the deformed configuration. It allows to evaluate the relationship between the design shape and the time-dependent state of stress in both glass and interlayer, that are strongly dependent upon the prescribed warm-bent shape, as well as on the viscoelastic properties of the interlayer and on the kind of release of the beam from the mould.
A comparison between “soft” and “stiff” interlayers has demonstrated that the latter are able to maintain the beam in the deformed shape also in the long term, for the whole lifetime of the element (50 years).
Remarkably, this study demonstrates that the constant-curvature shape, indeed the most used, is perhaps one of the worst that could be selected, because it produces shear stress concentrations at the end of the laminated glass element, which may possibly be a source of delamination. The higher is the shear modulus of the polymer forming the interlayer, the most critical is the corresponding state of stress, and hence the risk is higher for beams with Ionoplastic interlayers.
A very effective way to reduce the peak stress in the interlayer is to slightly change the shape of the mould. Remarkably, the sinusoidal shape, which for typical values of the deformation only slightly differs from the circular one, seems to be optimal for distributing and smoothing the shear stress in the interlayer. In general, for the same sag of the laminated glass beam, the shear stress in the interlayer is consistently lower than in the aforementioned cases.
It has been also demonstrated that another way to mitigate the delamination risk is to perform a gradual release of the laminated glass from the mould, bypassing the initial critical states occurring when the release is instantaneous, which are the most critical in terms of stress. The relevance of this effect depends upon the viscoelastic properties of the interlayer.
References
[1] L. Galuppi, G. Royer-Carfagni, 2014. Rheology of cold-lamination-bending for curved glazing, Eng Struct 61, pp. 140-152.
[2] L. Galuppi, G. Royer-Carfagni, 2015. Coldlamination-bending of glass: sinusoidal is better than circular. Compos Part B - Eng 79, pp. 285-300.
[3] L. Galuppi, G. Royer-Carfagni, 2015. Localized contacts, stress concentrations and transient states in bent-lamination with viscoelastic adhesion. An analytical study. Int. J Mech Sci 103, pp.275–287.
[4] S.J. Bennison, I. Stelzer, 2009. Structural properties of laminated glass. Short Course, Glass Performance Days, Tampere (Finland).