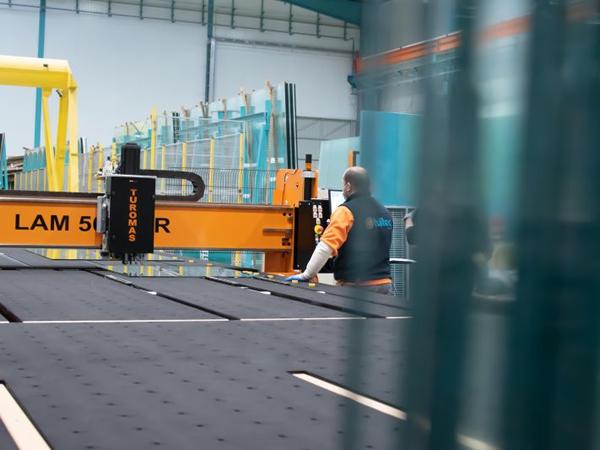
Date: 9 March 2021
The new equipment has been installed in the recently inaugurated manufacturing line for curved glass in León, Spain.
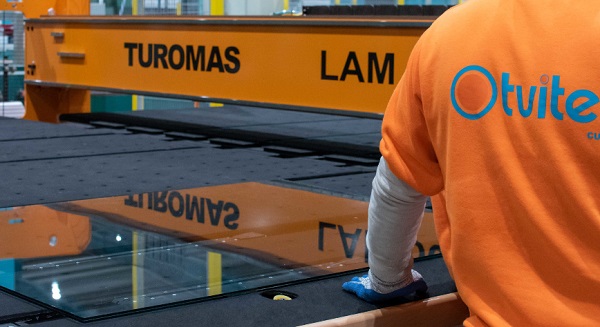
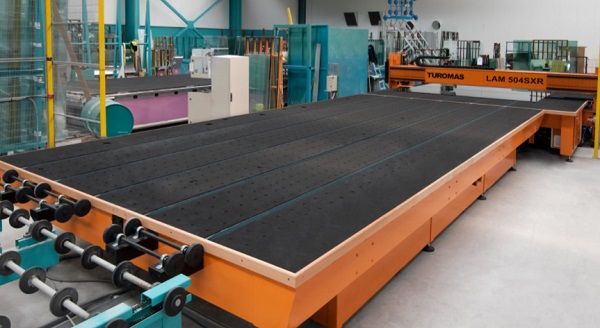
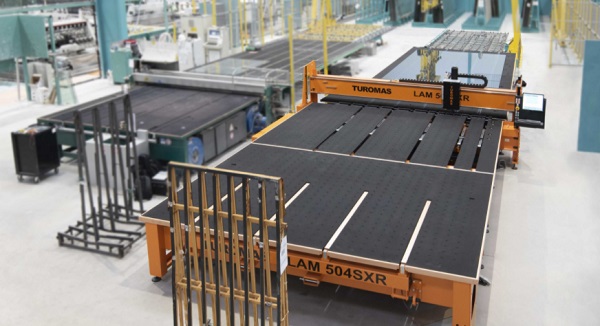
TVITEC, from 2008 to today
Tvitec (Técnicas de Vidrio Transformado), although founded in 2008, it has a long history and experience in the glass sector that has allowed and allows it to offer a comprehensive manufacturing system that includes flat glass and curved glass with the highest level of perfection.
Its processing centres, mainly located in Cubillos del Sil (León), in the northwest of Spain, have more than 200,000 square metres dedicated to the processing of high-performance glass.
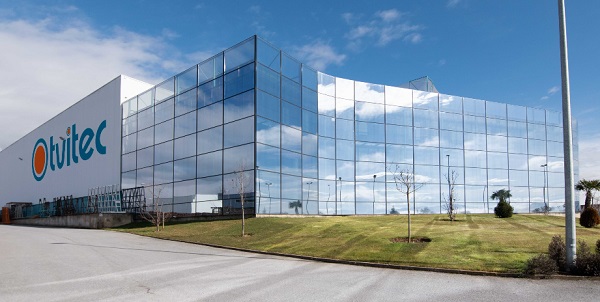
In production facilities, tempered, laminated, curved, screen-printed and double and triple glazing processes are carried out with the incorporation of coatings to control the transmission of heat, light, sound and maximise natural light.
All its facilities are equipped with state-of-the-art technology that provide maximum precision in all automated treatments, as well as having all the international quality certifications in the glass sector.
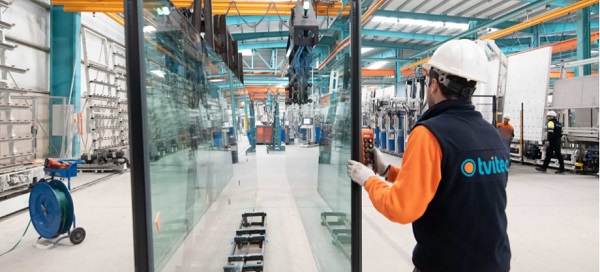
Today it is one of the largest processors of high-performance glass in Europe, having been involved in the most renowned international construction projects on all five continents.
Works such as the Karolinska University Hospital (Stockholm – Sweden), the Google Headquarters (Silicon Valley – California), the Lime Street skyscraper (London – United Kingdom), the new Santander Bank Headquarters (Madrid – Spain) and even the headquarters of the now famous pharmaceutical company Astra Zeneca (Cambridge – United Kingdom) have the TVITEC seal.
New laminated glass cutting line LAM504SXR
With the need to renew the laminated glass cutting line, together with the desire to improve the cutting process, the company from El Bierzo started a process of purchasing equipment that would satisfy two premises: efficiency and cutting quality.
It was precisely this, the cutting quality of the Spanish machine manufacturer, that was the differentiating factor that made the company TVITEC opt for the TUROMAS solution:
"We need to renew the machinery with the most efficient equipment and TUROMAS is at the forefront of this type of tooling that we need. In the cutting of laminated and monolithic glass, TUROMAS is a good player, a good bet to have a guarantee of success".
Javier Prado – Presidente TVITEC
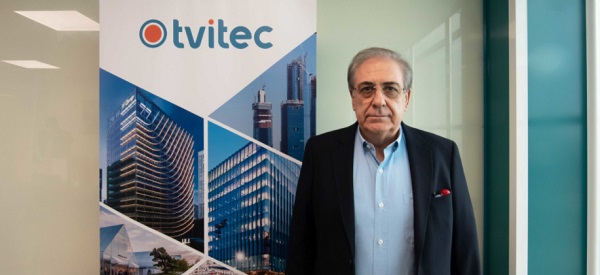
Along with the quality of the cut, another of the aspects that favoured the purchase decision was TVITEC’s confidence in the Spanish manufacturer. The business relationship between the two companies goes back more than 30 years and has always been nurtured by excellent service.
“TUROMAS has been with us as a supplier for 25, 30 years if not more and has always been there for us”
Javier Prado – Presidente TVITEC
The purchase of the new TUROMAS laminate line will allow TVITEC to meet and exceed the high quality and productivity demands of its customers – great façade designers, engineering firms, construction companies and architects who design and build unique buildings all over the world.
Characteristics of the new LAM 504SXR line
Throughout its 30-year history, Turomas has been working at the highest international level, developing and improving its range of laminated glass machinery. This has provided Turomas with a specific know-how that has enabled the Spanish company to position itself at the forefront of this type of cutting solutions.
In particular, the LAM 500 series is designed for companies that require maximum productivity and automation. It allows fully automatic positioning, rotating, stripping, cutting and separating of glass up to 12 + 12 mm, even on high-strength butyral glass.
The structural design of the range is assembled as a whole to gain in robustness and avoid stresses that compromise its performance. The surface of the table made of aluminium sheets, ensures the air flow and minimises possible air cushion losses.
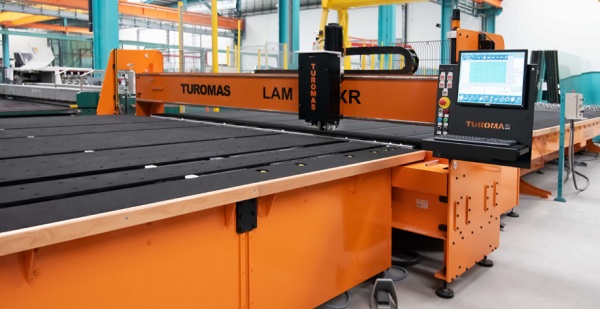
The glass is positioned using honeycomb belts with a non-slip texture and a traction system centred on the table structure. Thanks to this system, it is possible to move 12+12 mm glass sheets with a total anti-slip guarantee of and ensuring a perfect positioning with respect to the cutting bridge.
In addition, it incorporates an automatic rotation system patented since 2001. This system works by combining the movements of two independent suction cups that manipulate the lower face of the glass on the X and Y axes, offering rotation in safer conditions and avoiding contact at all times with the low emissivity layer of the glass in order to preserve all its qualities.
TUROMAS Cutting head
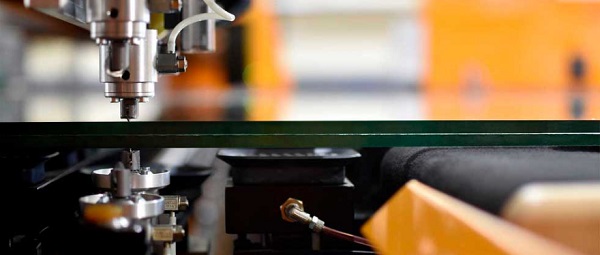
The cutting head that integrates the installed line consists of four tools, two upper and two lower. Each one acts independently and is dimensioned to exert the appropriate pressure for a specific range of glass thicknesses.
The tools are equipped with a height adjustment sensor and are offset from the vertical axis to ensure perfect alignment with the cut. To ensure the best cutting quality, the system actively monitors the pressure exerted by each tool and continuously stabilises and regulates it according to the thickness of the glass and the cutting speed.
The head has a constant lubrication system that favours the movement and penetration of the cutting wheel in the glass to obtain the perfect cut and ensure correct operation over time.
Cutting and breaking out system
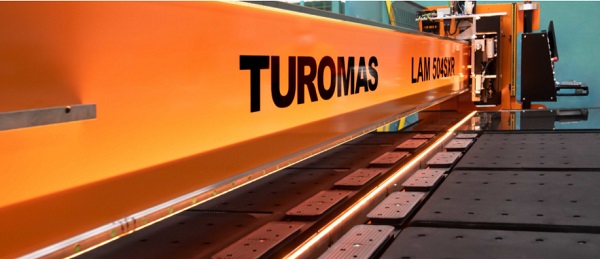
The upper cut is made by a nylon wheel that descends and moves along the glass to carefully perform the first operation. Next, a ruler parts the glass from the underside, both tools are fitted with sensors to control and ensure the ideal stroke and pressure for each glass thickness.
The PVB is heated by a specific infrared lamp and, at the same time, the two sides of the glass are separated by the traction exerted by two sets of independent suction cups at the bottom to allow the entry of a blade that cuts the PVB.
Interview to Javier Prado, TVITEC President
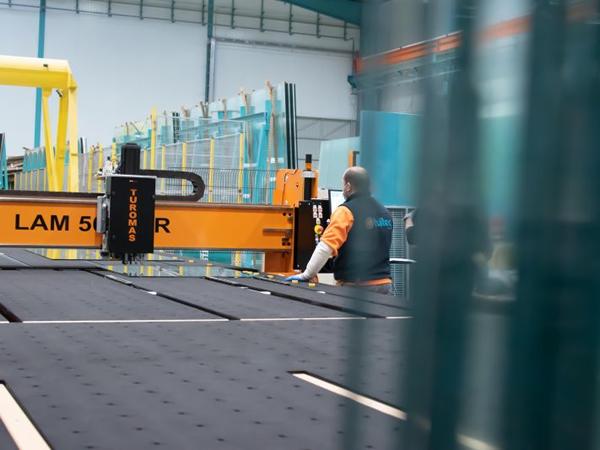

Add new comment