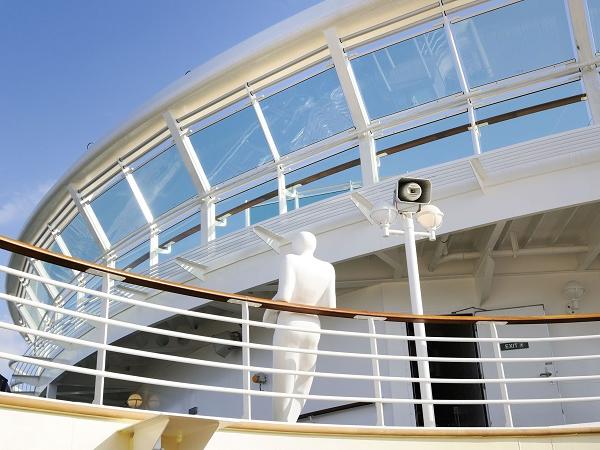
Date: 25 August 2017
The adoption of laminated glass as a structural material in architecture is growing almost exponentially, as architects, designers and engineers are beginning to realise the added potential offered by modern interlayers.
Traditionally adopted for its aesthetics, materials such as Trosifol PVBs and SentryGlas® ionoplast interlayers, have significantly expanded the applications for glass, especially where support needs to be minimal or postbreakage safety is a concern.
However, with this expanded uptake in newer, more demanding applications, additional testing has to take place to create the peace of mind that architectural glazed panels can endure the same environmental conditions as the structural elements surrounding or supporting them. It therefore makes sense that if the metal components are subject to rigorous testing then the glazed elements should be, too.
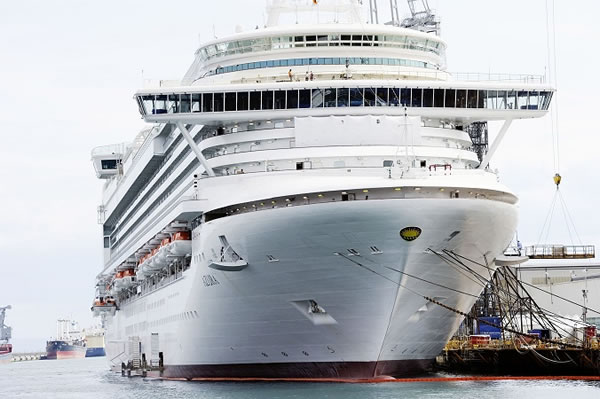
One avenue of testing is measuring the adverse effect of environmental conditions, especially in salt-laden coastal applications. The salt spray test is one of the most widespread and long established corrosion tests.
ASTM B117 Standard Practice for Operating Salt Spray (Fog) Apparatus was the first internationally recognized salt spray standard, originally published in 1939.
Other standards, including the American Architectural Manufacturers Association standard AAMA 2604-05, requires all coated architectural metal components to demonstrate corrosion resistance through a Salt Spray Test for 3,000 hours exposure.
In addition, the Centre for Window and Cladding Technology CWCT-Guidelines in the UK recommends the use of salt water proof materials up to 50 miles from the coast line.
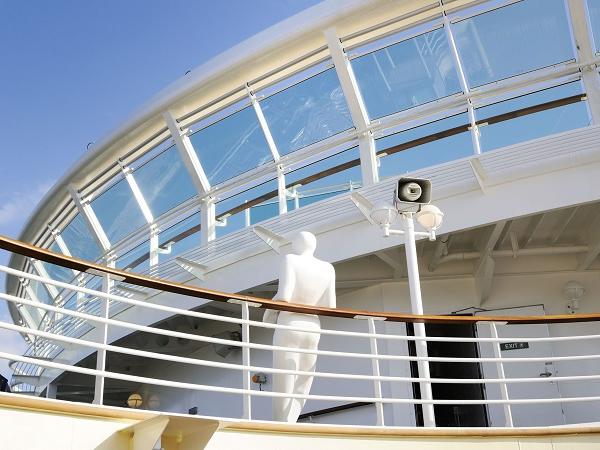

Add new comment