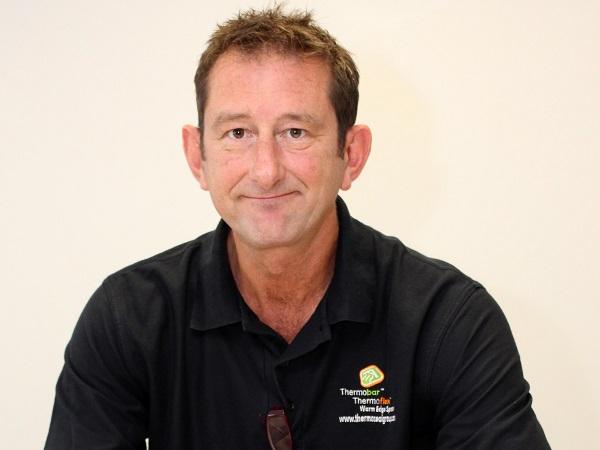
Date: 23 March 2022
The quality, performance, and application of molecular sieve desiccant in the manufacture of an insulated glass (IG) sealed unit is vital in helping to prevent its premature failure. Thermoseal Group, the UK’s leading manufacturer and supplier of IG sealed unit components offers its technical guidance in relation to the selection and use of molecular sieve desiccants.
Thermoseal Group’s Sales Director, Mark Hickox, explains: “The primary role of a desiccant in the manufacture of a sealed unit is to adsorb moisture that may be unavoidably trapped within the unit cavity during manufacture. The amount of moisture is dependent upon the relative humidity at the time that the double-glazed unit is sealed and so will vary from day to day. Desiccant is also there to adsorb the moisture which passes through the edge seal throughout its lifetime.
“When constructing IG units using tube spacer systems, the spacer should be filled with a quality 3Å desiccant. Whilst there is a general assumption that if a desiccant is tested by a notified body (for Moisture capacity) and the factory where the desiccant is manufactured has a recognised quality system (i.e. – ISO 9000) that the desiccant is of a high quality. This is not necessarily the case.
“We’d urge our customers to ensure that they read through our ‘7 Steps to Selecting a Quality Desiccant’ document and consider these indicators of a quality desiccant, including: 3 Ångstrom Pore Size; Good Delta T Performance; Low Initial Moisture Content; Good Moisture Adsorption Capacity; Low Dust Content; Very Low Gas Desorption and High Bulk Density.
“If there are any sealed unit manufacturers who are concerned that the desiccant could be causing premature failure of units, then we’d be happy to test any products on request, and with anonymous samples if required.
“I’d also like to remind sealed unit manufacturers that many warm edge spacer tube systems have a smaller internal dimension than traditional Aluminium spacers, so rather than filling two sides of the spacer, warm edge spacers must be filled on 3-4 sides if a 10 year warranty is being given.”
Download Thermoseal Group’s ‘7 Steps to Selecting a Quality Desiccant’ document now at: https://www.thermosealgroup.com/contentfiles/downloads/7%20Steps%20to%20selecting%20a%20quality%20desiccant%2015.03.22.pdf
Contact Thermoseal Group on 0845 331 3950 or Intl: +44 (0) 121 331 3950. Alternatively, visit www.thermosealgroup.com or e-mail us on sales@thermosealgroup.com.
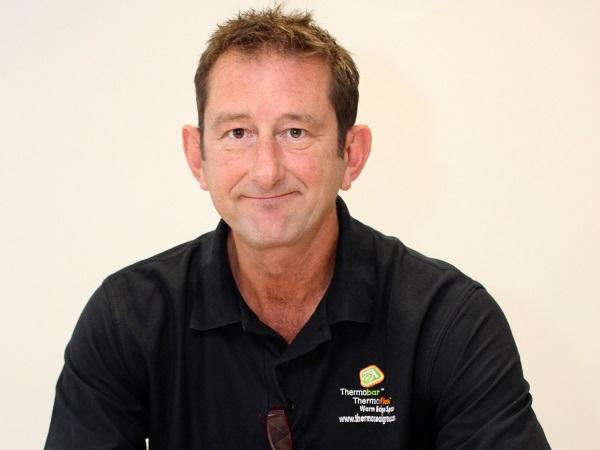

Add new comment