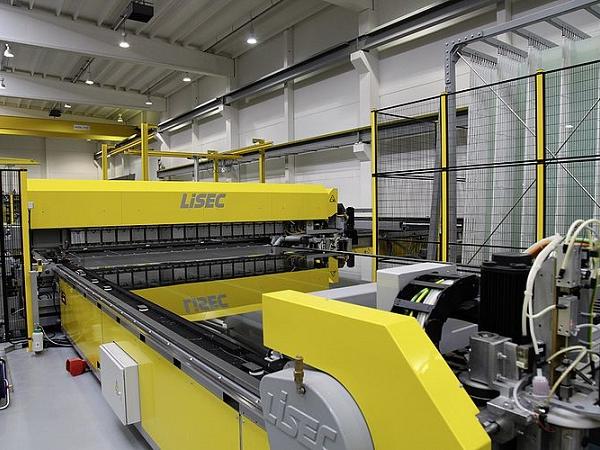
Date: 25 June 2018
With 30 employees, Heylen-Geerts Glasindustrie nv processes around 120 different glass types into high-quality products for indoor use.
Managing Director Marc Vermeulen and his wife are still active in the company, but the next generation, namely the fourth, is already ready to take over. Their daughter Diny Vermeulen is in charge of sales and administration and her brother, who is five years younger, is responsible for technology and leads the production.
HG-glas was founded in 1900 by Mr. Heylen and his wife (née Geerts) and initially specialized in glass products and painting tools. Since 1981, the company has been located on the current premises of approximately 17,500m² (1,500m² of which are offices) in Herentals, a town on the banks of the Albert Canal, some 50 kilometers southwest of Brussels. The main sales market is Belgium, about 20% of the products are exported to the Netherlands.
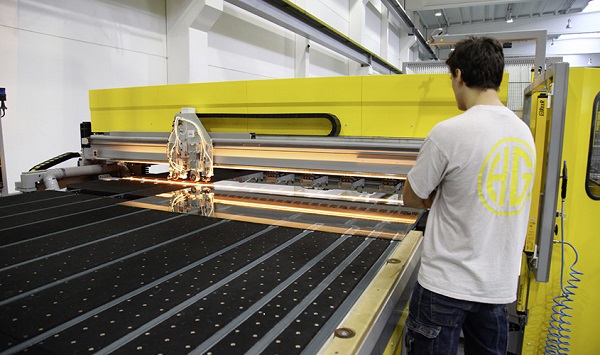
The first sensory perception when entering the production hall of the successful glass processor in Belgium: amazingly high degree of cleanliness, bright yellow machinery (combined with subtle gray) and the hiss of LiSEC shuttles that accelerate.
HG-Glas where quality is writ great, attaches great importance to cleanliness, the production halls are extremely tidy. Diny Vermeulen: "Our distinguishing feature in the market are very high-quality products and our punctual deliveries. In order to produce quality products and to be able to deliver them on time, a clean and technically perfect environment is required“.
The two companies, HG-glas and LiSEC, have been working together since 1993. The first joint project was a cutting table with an overhead loading device. Ten years later, two more LiSEC cutting lines were added. The third machinery project which HG-glas implements together with LiSEC is in the final phase.
This is a completely integrated and highly automated project. From unloading jumbo glass sheets via sorting, cutting and all intermediate buffers to packaging. Possible due to sophisticated machinery and logistics solutions but also thanks to integrated software from LiSEC.
PROJECT FEATURES - QUALITY, EFFICIENCY AND SPACE REQUIREMENTS IN A NUTSHELL
A special feature of the project is based on the quality standards of HG-glas: Each glass sheet is cleaned and scanned before it is cut and, if necessary, it is automatically re-optimized to have any defects left in the remnant plate or in the smallest unit of waste sheets.
Space is an important issue for the Belgian glass processor. So it was an indispensable objective to develop a storage site despite limited space in which more than 150 glass types are permanently available; thus glass sheets can be removed directly from inloaders.
Furthermore, a shuttle system was developed specifically for HG-glas, which brings glass sheets from horizontal to vertical position during transport or vice versa - thus avoiding a hall extension of 30 meters.
This solution made it possible to set up the packaging machines in the hall as well. Another special development in this project is the rotating table in the cutting area: The rotating table ensures that subplates can be rotated 90 degrees - the standard solution would take much more space.
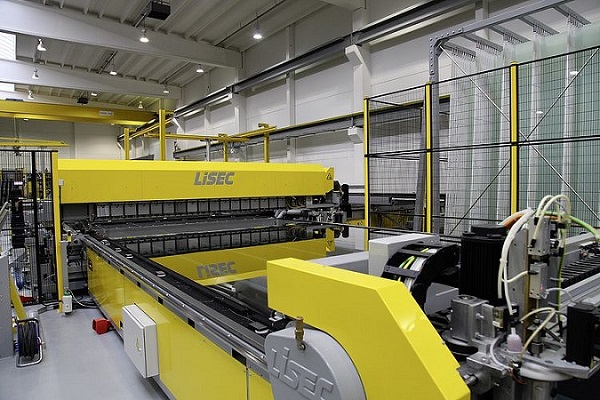
We have opted for LiSEC because, in addition to the price and the hall layout, we were really impressed by their individual technical solutions. For us, LiSEC means reliability, high quality, technical stability and, most importantly, excellent customer service. Every time we call, a specialist for machinery and software is available - that makes LiSEC unique and only in this way a company can develop from a small supplier into a main partner in the project business.
DINY VERMEULEN, HEYLEN GEERTS
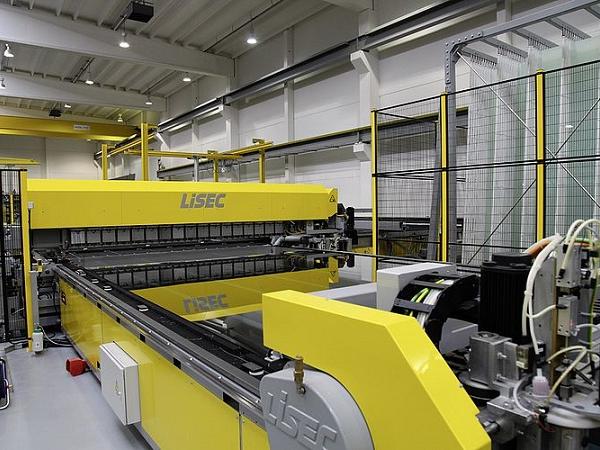

Add new comment