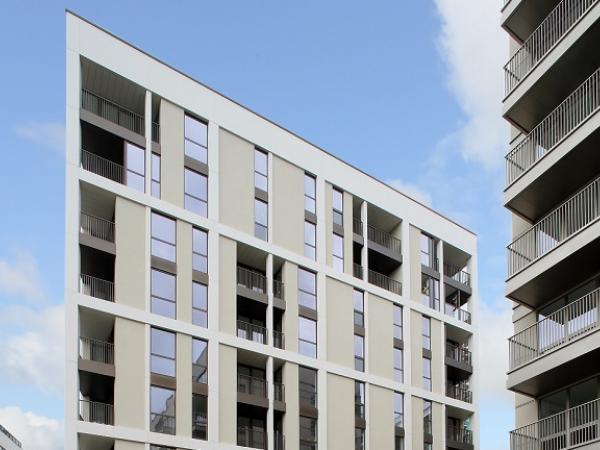
Date: 22 February 2017
Called The Fulmar and Teal, the project is a residential-led mixed use development on the Lower Riverside district of Greenwich Peninsula, a major redevelopment area close to the iconic Millennium Dome – now the O2 Arena – and Canary Wharf.
It includes 139 homes in a mix of private, intermediate and social rent tenures across the three buildings, plus 218m2 of retail/commercial space, a car park and bicycle storage area.
Working to a design by architects DSDHA, GLASSOLUTIONS was appointed by main contractor Kier Construction to deliver all curtain walling, windows and doors for the external envelope of The Fulmar’s three blocks, the tallest of which is ten storeys.
The Fulmar is part of a collection of buildings within an extensive project by property developer Knight Dragon who are seeking to create a new and vibrant district on the peninsula.
GLASSOLUTIONS played an important role is developing the fenestration specification after a revised approach was sought by the architect.
In proposing a combination of Wicona aluminium systems integrating with high performance insulating glass units (IGUs), spandrels and sandwich panels, GLASSOLUTIONS was able to meet the brief to provide superb aesthetics whilst meeting a number of key design factors.
These included a maximum pressure in ‘general wind zone’ of 1,200 kN/m2 and air permeability of 3m3/hr/m2 at a test pressure of 600 Pa.
The ‘stick’ curtain walling was fabricated using the range of Wicona Wintec 50 systems, which provide a slim 50mm face width and ensure excellent thermal insulation through the incorporation of a uPVC thermal break.
Integrated with the curtain wall structure are windows created using the Wicline 75 Evo concealed sash system.
This slim profile helped to maximise natural light transmission into individual properties and outward views, without compromising thermal performance thanks to a polyurethane insulator and an innovative glazing bead design.
A variety of door types were required, with Wictec 50 and Wicstyle 75 evo systems applied to manufacture hinged doors and swing doors accordingly.
Ground floor doors were designed to comply with the RC2 European security standard. Lifting sliding doors feature throughout the development which GLASSOLUTIONS manufactured using the Wicslide 160 system. All the doors are fully complementary in terms of aesthetics and performance.
GLASSOLUTIONS’ IGU specification accommodates the requirements for safety, security, thermal insulation and solar control. It also addresses sound reduction to help keep homes quieter, with enhanced acoustic insulation delivering a maximum Rw rating of 36dB (weighted noise reduction).
The outer pane is 6mm SGG Securit, a thermally toughened safety glass, with the inner pane being an 8.8mm combination of SGG Stadip Protect and Planitherm One.
The units feature a 90% argon fill 16mm cavity with a black warm edge spacer bar and polysulphide seals. This delivers a U-value of 1.0 W/m2K and a g-value of 0.49 or 0.51 for those units featuring a satin finish.
Spandrels are configured in a 6-16-6 unit, with 6mm SGG Security glass again used on the outer pane and the same cavity, fill and spacer bar and the vision units.
The inner pane is a 6mm SGG Emalit glass with 60mm foil backed insulation, a configuration that delivers a U-value 0.45 W/m2K.
The building’s design also required sandwich panels with a bronze anodised finish and punched mesh in matching colour for specific elements – all of which were installed by GLASSOLUTIONS too.
GLASSOLUTIONS’ external envelope project took 11 months to complete with The Fulmar handed over on 21.10.16.
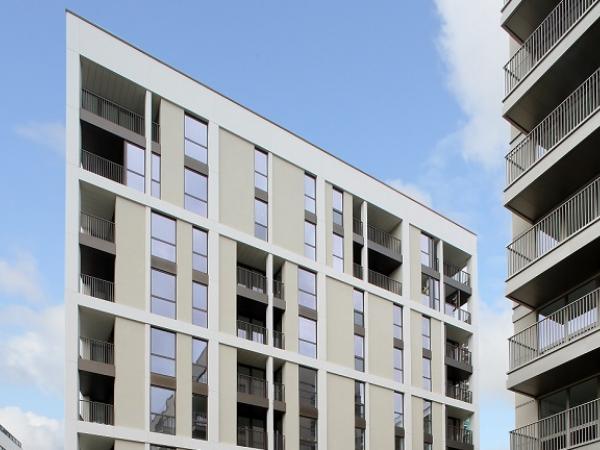

Add new comment