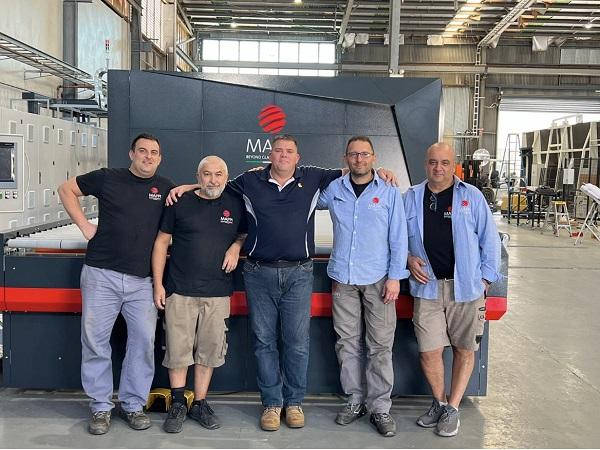
Date: 6 September 2022
Mappi has customers in 50 different countries around the world, and is committed to being close to each of them, at every stage of the life of a furnace, from choosing the best solution for their needs, during assembly and installation, through routine maintenance, technical assistance and beyond.
It is a relationship that has continued over the years, without interruption, in which one of its most important moments is during assembly, testing and technical training. It begins with the assembly, several weeks that take our guys away from home, allowing them to live and work side by side with the customer. The machine, which arrives disassembled and divided into different containers, is assembled piece by piece. It is a job that is done accurately, and on which the efficiency and quality of the hardening depend, a quality that must remain constant over the years.
Then we move on to the testing phase: everything must work perfectly, everything must comply with the quality standards that characterize every Mappi furnace. Week after week, the relationship with the customer is consolidated, not only by working side by side, but also through leisure opportunities which present themselves outside working hours. It is a journey that really makes it possible to "team up", creating a single team between Mappi and the Customer. It is no coincidence that one of the things that always happens is the exchange of t-shirts with each other’s logos, just like what happens on a football field between players of different teams at the end of a game!
The third and last phase is that of the passing on of technical training: it is necessary to instruct the staff of the glassworks on how to make the new furnace work at its best. This is perhaps the simplest job, because a Mappi tempering furnace, thanks to a large number of cutting-edge solutions and exclusive patents, is the most user-friendly of its kind that can be found on the market today. Sometimes it is precisely the understanding this incredible ease of use that represents the greatest difficulty for the customer... actually realizing that things can be done in a simpler and faster way!
Anyone who has used a tempering furnace knows that every tempering process is different, because each stage requires the definition of a large number of parameters, all of which depend on the characteristics of the plates to be tempered. These parameters are what in jargon is called "the recipe". Generally, a certain number of recipes are provided together with the furnace, based on the main and most common situations.
Mappi, on the other hand, does much more, it does not just give 1, 2 or 10 recipes, it gives the customer something much more precious: the ability to create the "recipe" they may need by themselves, a number that is potentially infinite. This makes the customer aware of how the tempering process works, and how to adapt it to their needs, allowing for the tempering of new types of glass that arrive on the market every month (at least 20 every year). Within a week of specific training, our technicians are able to make the customer independent.
The training is completed by showing how to deal with ordinary maintenance, which in many cases, as with the ATS 4.0 or with the brand new MTH, is extremely simple, thanks to solutions such as "heating chamber extraction", which allows access with extreme ease to the most hidden areas of the machine, easily maintaining it in perfect working order.
Of course, even after 10 or more years from assembly, each Mappi customer knows that he can ask for specific assistance, and will always find someone who will take care of his problem, providing each with the solution they need. Those who choose Mappi know they will never be alone. Mappi furnaces are famous because they can be switched off instantly. The one thing that can never be turned off is the bond we form with each of our customers!
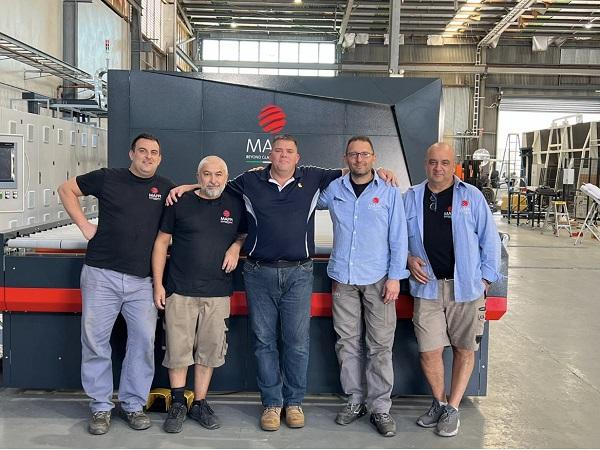

Add new comment