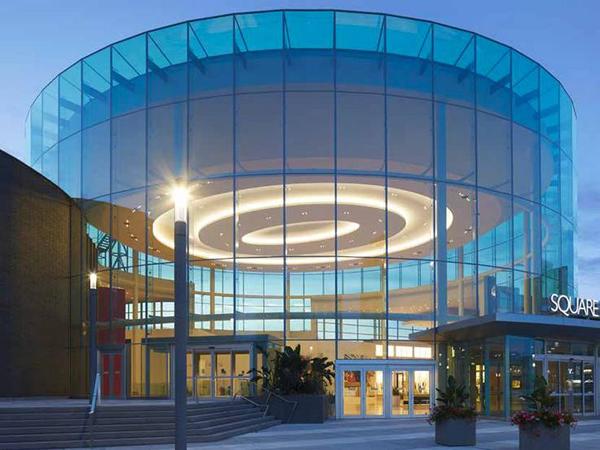
Date: 7 November 2019
Laminated Glass News speaks to John Kooymans, principal at Read Jones Christoffersen Ltd. (RJC Engineers), to discuss his history and uncover his ideas and predictions for glazing in aesthetic and structural applications.
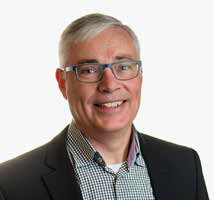
With over 30 years of experience in Building Design, at RJC Engineers, one of North America's leading engineering firms, with a staff of more than 600 in 12 locations across Canada, John leads both its Retail Group and its Structural Glass and Façade Engineering groups.
He offers an enviable track record to his involvement in the creation of some truly amazing glass structures and, sharing his wealth of knowledge with the next generation, he has taken a seat at the university of Waterloo since September 2019, as an adjunct professor, teaching Canada’s first Structural Glass engineering course.
Q. Can you give us an idea of your career to date?
It’s been a long road. I graduated in 1986 and took an instant liking to cultural and retail buildings because of the variety they offer, which I found new and exciting. My first foray into the world of structural glass was in 2002, due to a couple of jobs we were involved in. One was for a skylight for a retail structure, while the other was a staircase for an opera house. Both fascinated me and it was then that I realised that there was a bright future for structural glass.
Following these initial projects, I started researching the discipline and ended up heading to Europe, where I sought out and undertook training from my various industry contacts. Even in these earlier days I realised that glass had a lot to offer. I saw that I could enable the creation of unique applications, in terms of both structure and design.
Q. What’s your role within RJC?
I am a principal, in a 600+ employee company, leading a group that handles retail and cultural work as well as our structural glass and façade engineering group. This group was formed when I brought structural glass to RJC Toronto office and created a talented team, which has now been working together for quite a few years.
Q. Can you describe your company’s primary activities?
We have two distinct divisions within RJC: Structural and Building Science & Restoration (BSR). We specialise in structural engineering, building science, structural restoration, structural glass and façade engineering and parking facility design and restoration.
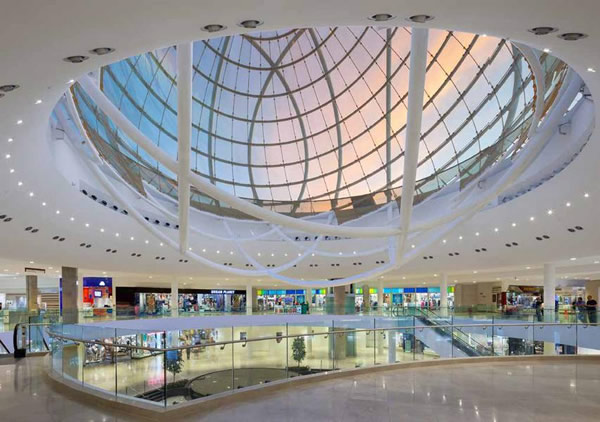
Image © Read Jones Christoffersen Ltd
Q. What’s the uptake and market like for structural glass?
Even though it is well established in Europe, there is still a lot of untapped potential in North America, which is one of the reasons I have chosen to teach structural glass at the University of Waterloo. Simply put, we need to bring more engineers up to speed on what can be achieved with these amazing material combinations.
Traditionally, glazing choices are normally left to the contractor, who makes decisions based on costs, supply and timescale. Consultants often don’t have any control over what could be done or said. Similarly, the lack of knowledge and application experience means that many decisions go unchallenged. That’s not to say that there hasn’t always been an interest in creating feature elements − it’s just that too many contractors start to value engineer them out due to “fear factors” or cost. It is my hope that better education and consulting up front will mitigate this. We need to remove this climate of automatic decision making.
It is clear to see that we need a bigger market, and not just in North America. Once the processing of laminated structures is simplified and the perceived risks are countered effectively and removed, more companies will come on board, which, in turn, will create a broader, more accessible and more competitive market.
Q. What flagship projects stand out for you?
In terms of structural glass, we have deployed both SentryGlas® ionoplast and Trosifol® PVB interlayers in some.
The Ledge on the Willis Tower in Chicago uses SentryGlas® in the floor panels, giving visitors an amazing view downwards. The Four Seasons Centre for the Performing Arts, in Toronto springs to mind, too, with its glass staircase – one of my first true structural glass projects. We also had a major role in the development of the huge rotunda at the Square One Shopping Centre, which deploys glass fins with minimal supports. The Erin Mills Town Centre Shopping Mall, is another interesting concept, which exhibits an amazing double-curved skylight that looks like a globe. This relied very heavily on the strength and resilience of SentryGlas®. And finally, we can’t leave out the Glacier Skywalk, a 35 m (115 ft) cantilevered glass-floored observation platform some 280 m (918 ft) above the Sunwapta Valley in the Canadian Rockies.
Q. As a structural engineering and building science firm, how has the development of ever more capable interlayers changed your design capabilities/visions?
A lot of it has to do with a greater range of options, especially stiffness. This gives us an opportunity to go thinner, while still achieving more comfort regarding higher temperatures and load duration. Therefore, for walkways and overhead structures, we regularly specify SentryGlas® or stiffer interlayers, as we want to make sure we have redundancy.
These capabilities allow us to produce better and safer designs − especially in terms of postbreakage − even in balustrades without top rails. We won’t do projects like this without using SentryGlas® from Kuraray, as we need the stiffness in case of breakage. It also allows us to push the envelope with our designs.
Q. Do you find that architects are now more aware of the capabilities of structural glass?
There is still a learning curve in North America. Many of them have used structural glass but will depend entirely on the glazing contractor. Others want consultants on board, while others know about it, but don’t understand the complexities, possibilities or budgeting − this is the growth curve and a good opportunity for us to step in.
Q. Are they using more in their designs?
This journey is twofold. Sometimes we get approached by the developer and are asked to step in as part of the design process. As a result, a broad team is involved in the design process at an early stage. Other times an architect may approach us and say: “I don’t know what I want, but it needs to be transparent. What are my options? What can I do?” In these instances, a lot comes out in the wash, so to speak. We get an understanding of budgets, visions, framing preferences, etc. and we are able bounce ideas off each other.
As you can imagine, a lot of the decisions are driven by budget, which dictates where designs end up.
Do we go laminated or not? What are the safety implications? Questions that are often answered by our commitment to engineering codes. The building codes in Canada are not particularly strong for structural glass design, so good engineering judgement is critical. You need to get people involved who understand structural glass!
In many cases, the codes might only call for the adjustment of one thing, but there are still multiple other factors to consider. We get in a lot of battles with local authorities, especially regarding balustrades. As a result, we have to create a lot of proofs and undertake testing, just to show that the designs meet the code’s intent.
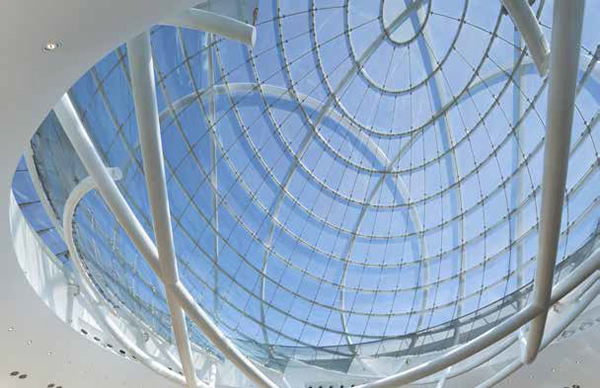
Image © Read Jones Christoffersen Ltd.
Q. What sort questions do you need to ask architects when they present you with their glazing visions?
Quite often they will have a vision or references to other projects. The basics comprise asking about the vision and the project criteria. As you can imagine we are very quickly into budgets, as this will define many things. If you don’t have money to start with, you don’t go far. Budgets are great at eliminating some of the options presented.
After this we normally ask: “what can be altered and what has to stay?” This gives us flexibility to evolve designs within predetermined constraints. Then, quite often, we need to discuss tendering. Do we go A to Z as design consultants, or do we stop at design development? How we approach design and milestones is often defined on how they want the tender process to be. In some cases, we do very customized designs, such as stairs and bridges, where we will design and detail everything, but in others, the contractor will have some flexibility in using their connection details, as long as the design intent is preserved.
We have a lot of contacts in the industry, so whenever we get to a certain stage, I will send the designs to four or five glazing contractors to get an idea of budget insights, as general contractors often have difficulty pricing these jobs. We are sort of testing the market, so we don’t go too far down the road before budgets start closing in. Getting these contacts involved early is also beneficial, as our friends regularly deliver honest opinions… which really help.
Q. Are you seeing any trends based around glazing?
Big glass is really starting to hit the market a lot more. People like the idea of using fewer splices and no longer being confined to certain designs.
A lot of developers don’t want to pay for big glass, but what we do see a lot more in North America are factories upping their machinery game in order to compete more against Europe and Asia in the supply of large glass. It’s not going mega, like Sedak & North Glass, but it’s certainly going bigger.
In most cases we find the European market is often more competitive. Big glass will be fully tempered/strengthened, but there is still a hesitancy in the North American market to heat soak, because if they have the capacity to temper, they might not have heat soak capabilities. In Europe heat soaking is pretty much automatic. Generally, it’s not just the ability to create the panels, it’s also about the post processing… and the capability to do it economically.
Q. If you had a wish list, what would the next generation of interlayers offer?
I would still like to get increased performance regarding stiffness at higher temperatures and load durations. The big issue, of course, is that stiffer interlayers are harder to post process and some companies have trouble creating good edges. In the case of balustrades, finish is critical, so a tool or some other way to help educate manufacturers on tricks of the trade would be of real benefit.
Many of our customers also want to see graphics, so a printable stiff interlayer would be popular. There’s also been a lot of research into transparent adhesives. They’ve certainly come a long way and are very close to in-field deployment, we just need more cases and data. These will result in fewer obstructions and more hidden connections, which can be glued together on site.
A lot of this future development relies on a greater number of in-field applications. It goes back to the need for more and more people to work with the products. The industry needs to get more projects into the marketplace and more suppliers on board in order to reduce costs and instill greater confidence. Indeed, confidence is still a big issue. People are worried that there may be failures and high replacement costs, or that a fancy crew may be required to install the panels. This is of course far from the truth, but wider use will certainly counter these myths and will bring overall costs down, which can only be a good thing for all parties.
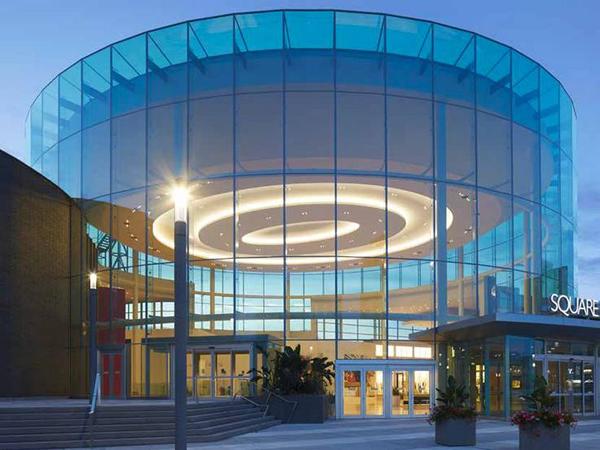

Add new comment