
Date: 4 December 2018
An Optimax cutting table complete with a fully automated Rapidstore system was recently installed to ensure the company could work at full capacity. Laser technology was also required to simplify the manufacturing process and to optimise the cutting equipment, with Jotika software incorporated for shaped products in the range.
During 2016 and early 2017 the company’s production capacity had been analysed, and with over 30 different glass types manufactured for the glass industry it was evident that bottlenecks were being created with substantial downtime restricting manufacturing time.
With demand increasing for the Custom Glass range across both commercial and domestic sectors, it was essential that production methods were simplified. Operations Manager, Andy Vint was familiar with the HEGLA brand and that the team were customer focused, knowing they could provide the right solutions for the company’s output.
After evaluating the glass machinery market HEGLA UK were invited to provide solutions that would increase productivity for the company that now produces on average 13,000 IG units per week.
Initially CAD drawings were created after site visits to Custom Glass by Steve Goble and his team, which allowed the limited area in front of arrissing to be opened up. For Jeff Hooson it was clear that the HEGLA engineers were driven to provide the right equipment for the allocated space on the factory floor, without the need to move any of the other equipment. Two cutting tables were removed from site and replaced with modern equipment from HEGLA.
Since installation, the large glass selection now can be fed automatically from the Rapidstore to ensure that the cutting machine is continuously fed. Faster cutting also means that the toughener can be kept well fed. With approximately 19 shuttle positions and 5 bolt positions, more racks can be added to this modular installation should customer demand and product diversity require it.
Progressive and Reliable
Custom Glass has achieved steady and consistent growth since 1982 when the company first opened its doors. Today, it is now firmly established as one of the UK’s leading manufacturers of domestic glass and toughened safety glass in the North West.
With more than 40 years experience in the sector, Managing Director Jeff Hooson bought Custom Glass 10 years ago, recognising the potential the company had in the marketplace. Having a product portfolio that comprises various types of coated glasses senior management knew that investment in state-of-the-art equipment that would take the company forward was vital.
This second phase of investment came after the installation of a fully automatic Bystronic glass Comfort’Line in 2016, which was purchased to cope with a more diverse product portfolio for both the commercial and domestic markets.
Larger batch sizes can now be cut more quickly and a broader product range can be delivered in a considerably shorter timescale.
Consequently, the new HEGLA system has further automated production methods and increased efficiency to provide consistently high quality products.
Based in Liverpool, Custom Glass has gone on to develop a range of quality engineered, specialist glazed products that meet and exceed current industry standards. Occupying a 68,000 sq.ft. manufacturing facility, the company is focused on customer satisfaction and develops products according to market demands and industry regulations.
The company’s ability to manufacture the best quality I.G. units with soft coat glasses and warm edge spacer as well as gas filling capabilities ensures that the range is manufactured in the most reliable and effective way.
Excellent Results
The HEGLA pedigree has already had a positive impact since installation with its speed and reliability having achieved excellent results. Consequently, the relationship with the HEGLA UK team is firmly established as a partnership rather than customer/supplier.
Jeff Hooson comments “It is vital with such a diverse product range that we get things right and to achieve this quickly. The Rapidstore ensures that we can store more specialist glass without downtime and this can be included without having to stop the production process.
The CAD designs allowed the production department to visualise how we could incorporate the Optimax and Rapidstore systems into the factory without the need for huge disruption. Carefully planned adjustments enabled us to create internal efficiency across all production departments.
The working partnership between HEGLA UK, Bystronic glass UK and Custom Glass provides us with clear advantages and we have never been let down by the engineering team since installing the equipment.
In an industry that has faced some challenging times we feel morally obliged to be decent and honourable - our suppliers are part of that obligation, and we consider HEGLA an exceptionally reliable business partner.”
For Paul Gibbs, Sales Manager HEGLA UK bringing together the best of both Bystronic glass and HEGLA brands at Custom Glass has created a shining example of technical superiority.
He comments, “This installation can be considered the ‘Jewel in the Crown’ in terms of efficiency, output and forward thinking production capabilities for Custom.”
With such a substantial increase in orders and the speed of production that is now achievable has meant that the national delivery run has now expanded considerably, which means a fleet expansion is imminent. 16 commercial vehicles that include Sprinter vans up to a 40ft. arctic lorry currently ensure that Custom Glass customers will receive what they need when they need it.
Steve Goble, Managing Director, HEGLA UK Ltd, “The installation of HEGLA’s Optimax and Rapidstore has really strengthened the entire production facility for Custom Glass, as the equipment provides many technical advantages that will yield a fast payback.
Working alongside customers ensures that any queries they may have are immediately resolved and as we tailor solutions to meet their individual needs, guarantees that we can help them continue to grow their business as and when they need.”
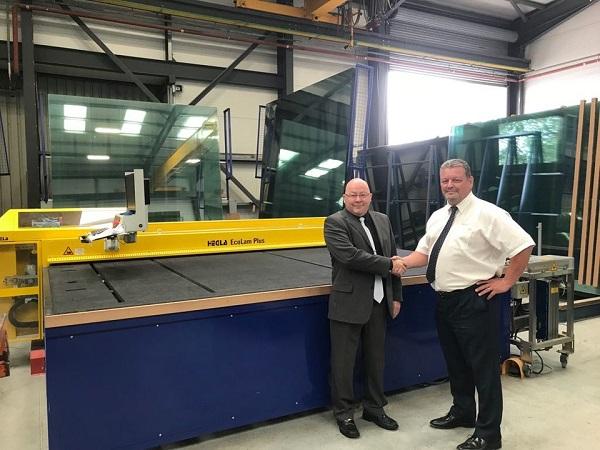

Add new comment