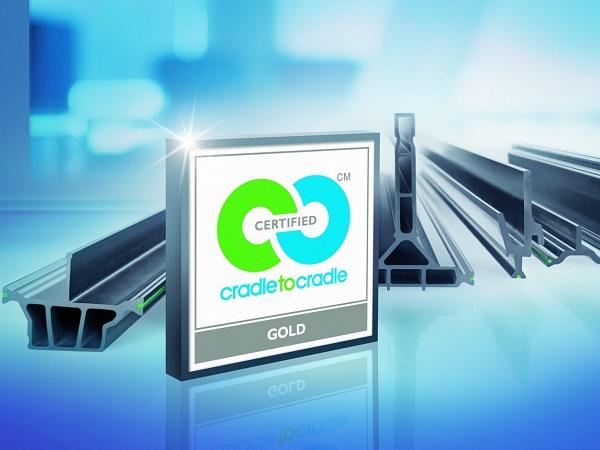
Date: 19 December 2017
Saving energy, reducing CO2 emissions, conserving resources – Ensinger was early to recognize the signs of the times. By 2013, the plastics specialist was the first manufacturer to launch a recycled insulating profile for the thermal separation of aluminum windows, doors and façades.
Since then, insulbar RE has been providing additional points for the certification of buildings worldwide with its Environmental Product Declaration. Its outstanding sustainability is now additionally confirmed by a Cradle to Cradle Material Health Certificate in gold.
“With this certification, we are sending out a further signal that the ecological footprint of our products and the conservation of resources are of great importance to us. We only have this one planet," says Jan Danger, division head for insulbar at Ensinger.
"We were the first to go into series production with an insulating profile for metal frames in 1977. With insulbar RE made of pure recycling material, we combine energy efficiency and sustainability and once again support the building industry as a pioneer in climate protection."
Doubly climate-friendly
During product evaluation by testing institutes such as EPEA, the entire value-added chain is considered in accordance with the principles of the Circular Economy - from cradle to recycling.
The verified sustainability and the eco-balance of the product, which is certified with the Cradle to Cradle Material Health Certificate and the EPD, pays off with building certification, be it according to DGNB, LEED, BREEAM or country-specific regulations such as HQE in France or GBCe in Spain.
With insulbar RE, we offer our partners in window, door and façade construction a strong differentiating feature, an added value that we want to further expand together", says Jan Danger of Ensinger.
"The manufacturing process is clean, the solution has been tried and tested millions of times and the transition is easy. Existing tools can be reused unchanged and without additional costs. We offer our customers a wide variety of standard designs and individual profiles."
Sustainable quality
Ensinger has more than 50 years of experience in compounding and precision processing of specialty plastics. For the production of insulbar RE, pure polyamide recyclate from reliable sources is upgraded in a special upcycling process so that its properties are directly comparable with new material (suitability tested according to DIN EN 14024 by the ift Rosenheim, certified by CSTBand SKZ). The service life of the high-quality material is thus extended by a further product life cycle.
The use of recycled material in the production of insulbar RE reduces the consumption of fossil fuels by 89 % compared to the conventional polyamide profile, CO2 emissions are 84 % lower and 32 % less water is consumed.
The material properties are checked in every phase of the process and documented according to DIN ISO 9001:2008. That is why insulbar RE has the same high quality, durability and functional reliability as known from classic insulating profiles.
Find more information about insulbar RE here.


Add new comment