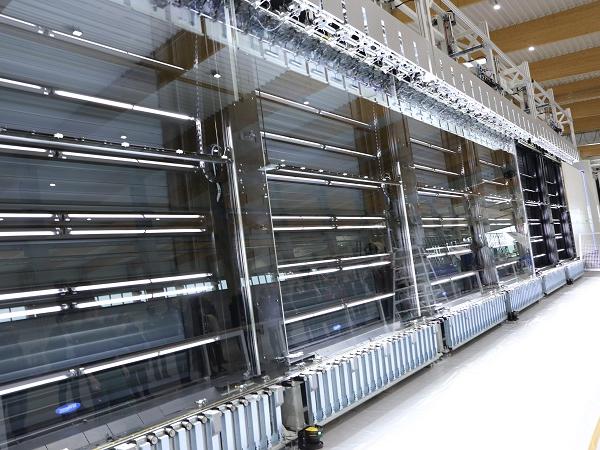
Date: 31 May 2018
Bystronic glass will be exhibiting at GlassBuild America at Booth 1127.
Longer – Heavier – Bigger! The B’JUMBO XXL insulating glass production line from Bystronic glass can be described using these three attributes where were inspired by the motto that was coined by Pierre de Coubertin for the Olympic Games.
With this line, Bystronic glass is setting new benchmarks in architectural glass production: The production line measuring 165 metres in length is used to automatically produce insulating glass up to 18 metres in length, a globally unique size.
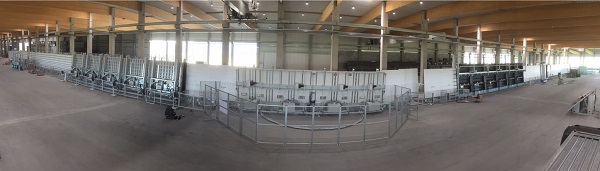
© Bystronic glass
Consequently, it is the longest insulating glass production line in the world and recently entered service at the famous German manufacturer Thiele Glas, based in Wermsdorf, Saxony. Thiele Glas has achieved an excellent reputation in recent decades, particularly in terms of creating unusual façades in industrial buildings.
Bystronic glass is addressing the future of insulating glass technology in an innovative way that is also opening up completely new opportunities in the field of façade design.
The B’JUMBO XXL is able to produce insulating glass or façade glass in new dimensions: With maximum dimensions of 3.30 metres in height and 18 metres in length and a maximum processable glass weight of up to 10 tonnes, the B’JUMBO XXL is the ideal solution for the current trend and demand for ever-larger architectural glass.
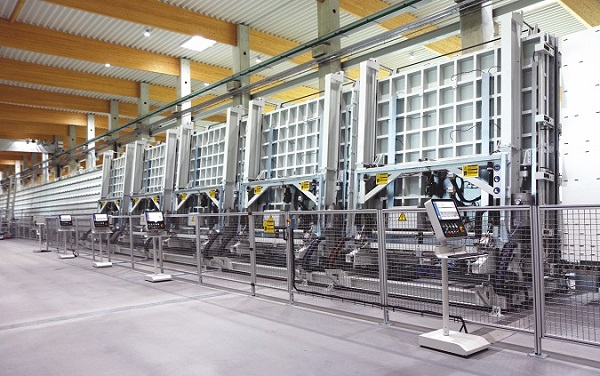
© Thiele Glas
"This production line is an enormous unique step that is previously unheard of and offers the glass processing industry comprehensive new options. We are proud to combine our experience in innovation with our glass processing machine understanding which dates back over 50 years and subsequently can launch lines such as the B’JUMBO XXL onto the market", explains Stephan Kammerer who, as the Product Engineering Manager, is responsible for the design and construction of this machine.
Machine components
Equipped with an edge deletion robot, a glass plate washing machine, a turning station, six inspection and frame positioning stations, five assembly, gas-filling and press robots, a sealing robot and numerous conveyor belts, the B’JUMBO XXL is an imposing complete line.
The world record-breaking machine length or the maximum glass dimensions are not the only characteristics of this production line; it is also characterised by many other features:
- The maximum individual glass thickness of 60 mm
- The package thickness of the double or triple I.G. units of 150 mm
- The maximum I.G. unit weight that can be transported is 600 kg per running meter
- The integrated turning station can turn glass measuring up to 12 metres in length
- The semi-automatic framepositioner can be used to position spacers measuring
- 18 metres in length onto the glass
- In addition to rectangular formats, the machine is also able to produce all shaped formats as well as free shapes in accordance with the Bystronic glass shape catalogue
- Despite its dimensions, the line can be installed on a standard industrial floor so that special foundations are not required in the hall floor
Obviously, the B’JUMBO XXL can also be used to produce up to 4-sided stepped double or triple insulating glass units. In doing so, the maximum frame setback on the 4th step is 250 mm, measures up to 1,000 mm on the 1st step on the front edge of the glass and there are no dimension limits whatsoever on the 2nd and 3rd step.
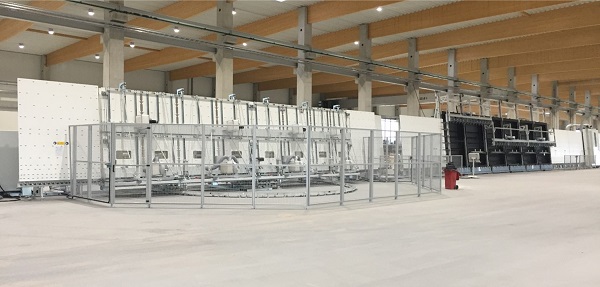
© Thiele Glas
Energy-efficient and sustainable production
"However, sustainability is also extremely important to us", explains Stephan Kammerer. "Despite all over-dimensions, extreme importance was attached to energy efficiency and sustainable production during the design of the line."
"Green Production" consists of comprehensive and optimised energy efficiency and energy recovery mechanisms: For instance, kinetic energy generated during braking processes is transformed into electrical energy. This recovered energy is fed back into the system and is distributed to the axles that currently require energy via a motor-management module.
In this way, production on the B’JUMBO XXL enables a resource-efficient and sustainable production of the insulating glass or facade units.
Manual frame positioning is a thing of the past
A further highlight is the semi-automatic framepositioner. Previously, the manual positioning onto the glass was associated with a significant amount of human effort and also took a long time, especially when dealing with large format spacer frames.
The framepositioner is able to quickly perform this task as the spacer frame is automatically positioned in the station and the grippers belonging to the upper bar automatically press the upper edge of the frame onto the glass.
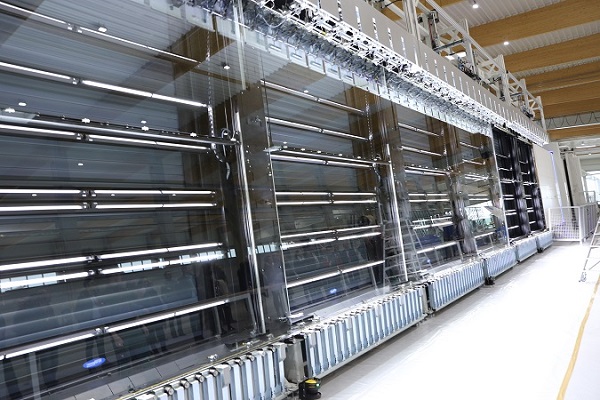
© Thiele Glas
Precise dosing technology
The core of the jumbo’sealer XXL sealing robot is its dynamic mixing system. In contrast to the static mixing system that is very common in the sector, the dynamic mixer works with a significantly reduced material pressure. With a flow rate of up to six litres per minute, it also makes the utmost material volume available.
As a result, the jumbo‘sealer XXL is able to seal even deep spacer setbacks of rectangular units and shaped formats considerably quicker than other robots that are common in the sector, even with the current maximum size of
3.30 m x 18 m.
"What also sets it apart from other sealing robots in the glass industry is its automatic material changing system that allows operator-free changing of the sealing material – from polysulphide to silicone for instance – inside two minutes", explains Stephan Kammerer. "Furthermore, there are several undergripping options in the discharge area that support the removal of the fully sealed Jumbo units."
If, back in 1894, Pierre de Coubertin knew what technical opportunities would arise in the field of modern glass processing in the 21st Century, maybe he would have added "Longer – Heavier – Bigger" to his classic Olympic motto.
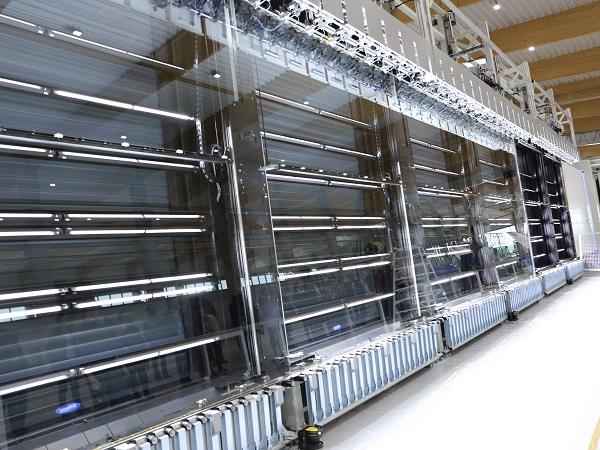

Add new comment