Architectural Glass Laminating Guide - Part 10
By Luc Moeyersons
Based on my request for subjects, one of the suggestions was to write about laminated glass recycling.
Not being a “real glass production specialist”, I took the time to read brochures and info I could find on the subject.
On PVB, I based myself on the information I had from a few years back.
I realize that the information might not be complete or fully up to date.
Consider this document as a discussion or thought provoker.
With the realisation that all raw materials are limited (even glass’ raw materials are limited: Sand (SiO 2 ), Lime or Calcium Carbonate (CaCO 3 ) and Soda Ash (Na 2 CO 3 )), recycling of finished products becomes more and more important and urgent.
Looking at laminated glass what are the major raw materials?
Glass
- Glass
- Ceramic ink (mainly automotive)
- Silicone/poly sulphates (Insulating glass unit)
- Separators (AL, “Warm Edge”)
- Silicagel (drying chemical agent)
- Coatings
PVB
- PolyVinylButyral
- Plasticizer (3GO – Tri-Ethylene glycol di-ethyl hexanoate)
- (Adhesion control ions/elements)
- (Additional additives)
Glass
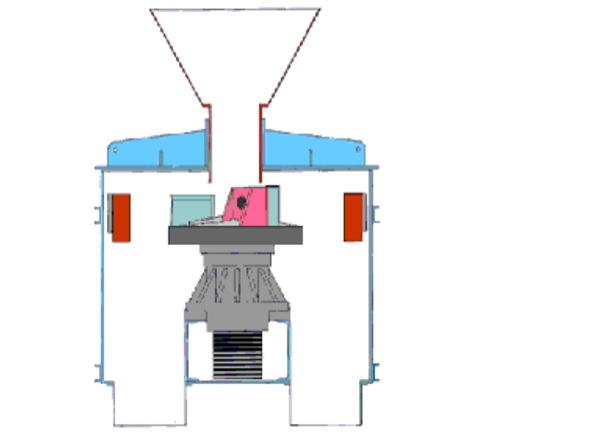
Glass can be recuperated (as “cullet’) after crushing the laminates.
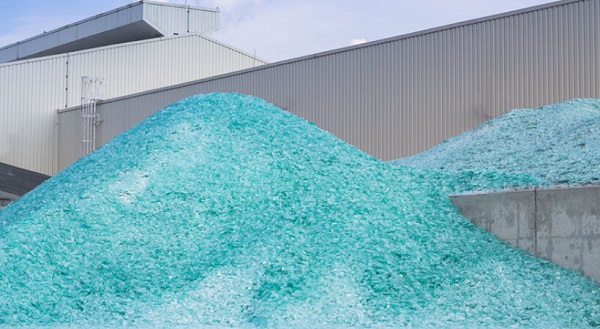
However, there are strong technical restrictions:
Pre-consumer material: (originated from processing or re-processing of glass before the final product reaches the consumer market (cut-offs, losses during lamination or bending, manufacturing of IG units or automotive windscreens)
Excluding re-introducible glass (“internal cullet”) in float process.
(Internal cullet is estimated to be around 20 %)) (data from Saint-Gobain Glass)
Pre-consumer cullet is estimated to be 11 - 13 % (data from Saint-Gobain)
Post-consumer material: all material coming from glass recycling collection: end-of-life vehicles, construction or demolition waste...)
Post-consumer cullet is estimated to be less than 1 % (data from Saint-Gobain), but increasing due to market evolution (circular economy). Landfill has been the most used “treatment”.
Challenge: Low Iron glass (using regular glass cullet will increase the colour of the low iron glass – reduction of use of cullet in Low Iron glass(?))
Proper recycling of all building glass waste could avoid 925 000 tonnes of landfilled waste every year and could save around 1.23 million tonnes of primary raw materials (873 000 tonnes of sand) and reduce carbon emissions by more than 230 000 tonnes annually (Economic study on recycling of building glass in Europe – Deloitte Sustainability).
One ton of cullet saves 1.2 tons of raw material, including 850 kilograms of sand, and reduces CO 2 emission by app. 300 kilograms. (Data from Glass for Europe)
On May 30th, 2018, the European Union published the 2018/851 Directive, urging member states to ensure that by 2030, no waste that can be recycled or recovered is allowed in landfill.
When renovation was reviewed of the Lloyd’s building in London (2012 – Lord Richard Rogers) chairman of Lloyd’s (Lord Levine) insisted that matrials should be re-used or recycled. The original “Sparkle (textured) glass” had been produced by Sain Gobain Glass and combined with Coollite Solar control coating. The “Sparkle Glass” units had to be de-glazed from the building, cut in half, edge worked and used in Insulated Glass units with one large glass pane at the back and 2 smaller panes at the front (one of “Sparkle glass”) for the same building. A first example of re-use/recycling.
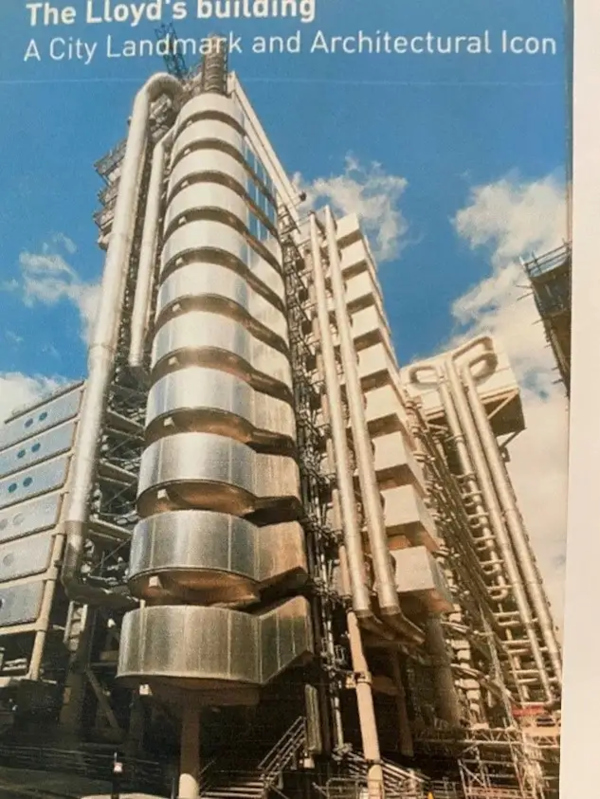
The Paris Climate agreement (2021) has forced the re-glazers to use more and more re-used/re-cycled glass. There are currently various reglazing building projects where the concept is to deglaze the building, glass units are dismantled, cullet is separated and reintroduced in the float oven when producing the new glass for that project.
Info on contacts:
https://youtu.be/-dljgJqj9H8 (movie: Cogelme)
https://www.youtube.com/watch?v=UAnzQl-EIs4 (movie: Viridor)
https://www.facebook.com/windshieldpvbrecycling/videos/188800659723236/
https://www.sibelco.com/en/materials/recycled-glass (Sibelco)
https://www.ferver.eu/en/members (Glass recycling in Europe)
https://www.maltha-glassrecycling.com/en/about-us (Maltha - Belgium-The Netherlands)
https://barnsley.cylex-uk.co.uk/company/northern-cullet-ltd-13738214.html (Northern Cullet - U.K.)
https://www.paprec.com/en/our-solutions/the-materials-we-recover/glass/ (Paprec - France)
https://www.solover.fr/en/flat-glass-recycling/ (Solover - France)
https://www.uusioaines.com/en/glass-recycling-services/float-glass-recycling/ (Finland)
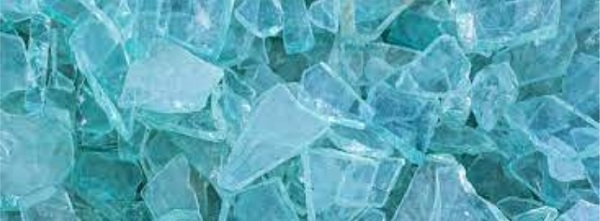
Cullet is used continuously in float ovens to reduce the oven bath temperature and emitted CO₂.
Adding 40 % cullet allows to reduce the oven temperature to 1150 °C
(From 1600 °C).
Melting pure glass cullet (1886 GH/Ton) requires some 30 % less energy/heat than melting pure glass raw materials (2671 GJ/Ton) (Science hub European commission)
In general, 10% extra cullet results in a 2.5 to 3% reduction of furnace energy consumption.
Restrictions:
- Flat glass float processes can only use flat glass cullet.
- Bottle glass processes can use flat glass cullet as well as bottle glass cullet.
- Glass wool processes can include flat glass and bottle glass cullet as well as glass wool.
- Other glass cullet (or contaminated cullet) can be used in “product recovery” (see further)
- ISO14021 defines the cullet types/origin.
Product Recovery:
- Cullet grain size: 20 X 20 mm maximum (if larger, can disrupt transport and fusion in furnace)
- Cullet should be separated by glass type (Simple glass, laminated glass, black enamelled glass (ceramic band), mirror glass, lacquered glass... .
- Cullet should be separated by colour: Extra clear, clear, tinted.
Contamination to avoid:
Metals:
- Aluminium (can create infusible particles on the glass ribbon, making it unfit for sale and non-recyclable in flat glass furnaces).
- Stainless steel (contains Nickel that can create “spontaneous” glass breakage (Nickel Sulphide (NiS) – tempered glass)
- Tungsten (can lead to deposits of tungsten – making the glass not sellable)
- Lead (can lead to deposits that can attack the glass)
Ceramic Glass:
High temperature resistance composite (oven doors, ceramic or induction cooking panels, fireplace inserts, ...)
Infusible:
glass making tools, abrasives, construction waste (stone, concrete,...)
Other types of glass (Quartz glass):
Laboratory glass ware, wine glasses, borosilicate glass, oven resistant dishes (Pyrex®,...) ...
Doubtful products:
- Digital printed glass
- Smart glass
- Electronic mirrors
To evaluate product quality and ensure good separation of the various contents, float glass producers use and prefer to use official recycle companies. They also prefer that full units (IGU) will be delivered.
Other materials.
Here enters the complexity.
To my knowledge, no systematic way has been set up/detected to remove/separate all the other materials.
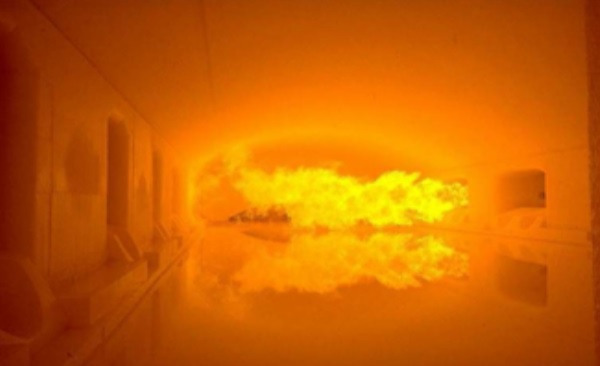
Ceramic band (mainly automotive)
Can be present at a limited % in cullet, will burn off in float oven. (10 – 200 gram/tonne?)
Silicone/poly isobutylene/polysulfide (Insulating glass unit)
Will burn off in float oven, threshold limit (350 gram/tonne?) (Volatile Organic Component level?).
Spacer (Al, “Warm Edge”)
Will need to be removed prior to glass recycling (maximum limit for non-magnetic metals: 0,5 gram/tonne).
Silica gel (drying chemical agent)
Needs to be removed (together with Al separator)
Coatings
No restriction/limit (?)
Adding additional features to the original glass product, will render separation even more difficult.
PVB
After crushing of laminated glass, still some 4 % of glass fragments (”Cullet”) remain on the PVB.
When glass fragments would be introduced in to a PVB extruder, they will (mechanically) damage the inside of the extruder and block the PVB melt filter.
As we know, increasing the moisture content of the PVB reduces the adhesion to the glass.
So, one could envision that these sheets of recuperated PVB (with glass fragments) could be increased in moisture content to allow the glass fragments to be easily removed afterwards.
One could imagine large pools of (clean, demin.) water with laminated glass or steam ovens where the moisture absorption would go much faster.
It is not very clear if this combined process (crushing and moisture increase) would be more economical than using virgin PVB.
Since one does not know the origin of each single PVB sheet, one was worried about mixing/blending all recuperated PVB sheets into one batch/process.
But the major global PVB suppliers (Eastman, Kuraray, Sekisui, Everlam,...) are all using the same plasticizer for the regular PVB, so the risk for Plasticizer contamination is now far less than some 20 years ago.
Adhesion of this recycled PVB should still be checked/controlled in view of the additive differences, but no compatibility issues are expected.
Currently, PVB (with limited % of glass fragments) is used in flooring and asphalt, but the total cost (product and recuperation) is still more expensive than the original raw material.
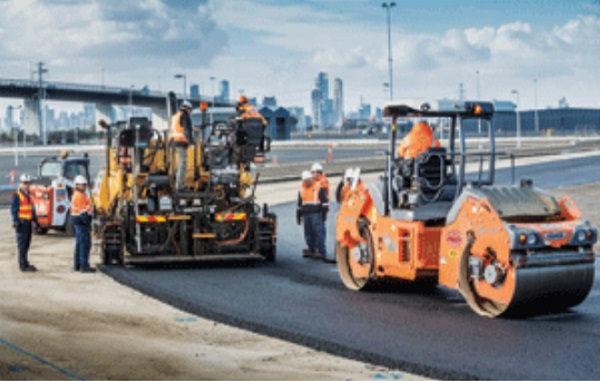
Other uses for recycled glass include (Wikipedia):
- Fiberglass insulation products
- Ceramic sanitary ware production
- As a flux in brick manufacture
- Astroturf
- Agriculture and landscape applications, such as top dressing, root zone material or golf bunker sand
- Recycled glass countertops
- As water filtration media
- Abrasives
Sources of info:
http://www.recycled-pvb.eu/descripcion_en.php (Lurederra - Spain)
https://www.interface.com/EU/en-GB/about/modular-system/PVB-en_GB (Interface Europe)
https://www.ferver.eu/sites/default/files/170511_pvb_presentation.pdf (Ferver - Federation Europeenne des recycleurs de verre – Brussels)
https://www.sibelco.com/news/sibelco-and-shark-solutions-expand-partnership-in-commercialising-recycled-pvb (Sibelco - Shark Solutions)
https://www.youtube.com/watch?v=ZG0Sqgfc7xA (Interface)
https://www.youtube.com/watch?v=CjD4QhgTW5w (Shark Solutions)
https://professionals.tarkett.com/en_EU/node/id-revolution-pvb-recycling-breakthrough-10210 (Tarkett)
This information has been collected from reading public brochures and literature, interviewing specialists.
This info, consequently, does not reflect the full knowledge that is around on this subject.
The author is not responsible for eventual misstatements in numbers or application/practice.
The used literature has been obtained from Glass for Europe, Saint Gobain, AGC, NSG, Sisecam, ift Rosenheim and various glass recyclers, Arup (Graeme DeBrincat),...