This paper was first presented at GPD 2023.
Link to the full GPD 2023 conference book: https://www.gpd.fi/GPD2023_proceedings_book/
Author: Mikko Rantala | Glaston Oyj Abp
Abstract
In a flat glass laminating oven, the aim is to heat interlayer film between glasses to a certain temperature depending on the film type before the glass-film sandwich enters a nip roller after the oven so that the interlayer film will adhere well with the glass. The measured surface temperatures after the oven are typically between 60 and 90 ˚C, increasing with sandwich thickness. The difference between that temperature and the film temperature is notable. So, it is fully unknown what the temperature of the film is. This makes it difficult to choose the heating parameters of the oven. The glass's initial temperature before heating varies during the working day, which causes variation in the measured surface temperature and the film temperature, which causes quality costs.
To ensure that the selected process parameters for heating are successful, a theoretical calculation method can be used to predict the development of the thickness-wise temperature profile of a glass-film sandwich before it is conveyed to the laminating oven.
The thermodynamics-based method presented in Glass Performance Days 2017 is applied to form a computer code with which glass-film sandwiches can be heat-treated virtually in a selected lamination oven model. The paper compares the results predicted with this code with the experimental data from the full-scale laboratory tests and data collected from laminating ovens in production use. It also discusses how the prediction method can be utilized in the future in machine automation and responds to actual problems existing in laminating ovens.
1. Introduction
In the lamination process, a plastic interlayer film is placed between two glass sheets, and a sandwich structure sheet comprising glass and plastic layers is formed. The interlayer film is polyvinyl butyral (PVB), ethyl vinyl acetate (EVA), or SentryGlas™, for example. Common interlayer thicknesses are 0.38, 0.76, and 1.52 mm. The thickness of the glass sheets is typically 3–12 mm. The glass-film sandwich is heated in a lamination oven to a temperature of 60–90 °C depending on the thickness and composition of the sandwich structure sheet, which temperature is measured from the surface of the sandwich immediately after the oven. The temperature of the interlayer film is then considered to be at the target temperature which is 60-65 °C for PVB film, for example.
After heating sandwich structure sheet passes between a pair of rollers pressing it and forcing air out of its material interfaces. The lamination oven with its nip rollers is also called a de-airing conveyor and aim in using it is to discharge air from between the material layers and to stick the layers together into a tight sandwich structure sheet. Usually, successful lamination is confirmed by an autoclaving process following the lamination oven treatment, which can help dissolve the remaining air evenly in the interlayer film.
Heating in a lamination oven is arranged with conventional heating resistors located near the ceiling and roof in a heating chamber. So-called quartz tube heaters, emitting near and mid-infrared radiation, are also used in some ovens. In the ovens mentioned above, heating is based on the radiation heat transfer. In some ovens, the heating is based on forced convection. Different heating methods have some advantages over others. The advocates of radiation ovens maintain that radiation heating helps because the film absorbs the radiation penetrating the glass. The statement that clear and low-e coated glass-film sandwiches can be processed with the same speed is claimed as an advantage of convection heating. However, the following problems or development targets could be listed for every kind of laminating oven on the market.
1. The aim is to heat the laminating film to a certain temperature before it enters the nip rollers, but the only data given by online quality monitoring is the surface temperature of the sandwich exiting the oven. It is therefore unknown what the temperature of the interlayer is. As shown in [1], the difference between the temperatures of the surface and the innermost interlayer of the thick multiinterlayer is very clear in all kinds of laminating ovens.
2. The selection of the heating recipe is often based on a standardized practice, which means that the first recipe leading to successful results is always used. This recipe varies by customer, even though the oven is identical. This secures success in heating common glass-film sandwich structures, but not of extraordinary ones. It is also very possible that the recipe used will heat the sandwich more than necessary, resulting in higher electricity bills.
3. The interlayer film is placed between glass sheets in a so-called laminating room, where the air temperature is controlled to 18–20 °C. The temperature of the glass sheets transferring from the factory hall to the laminating room varies depending on the location of the factory, the weather, and the water temperature in the glass washing machine preceding lamination, among other things. Washed glass sheets waiting longer in the factory hall for lamination typically cool close to the temperature of the factory hall. For the reasons described above, there is considerable variation in the temperatures of the glass sheets to be laminated conveyed to the lamination oven. This temperature variation is transferred almost completely to the temperature at which the sandwich structure sheet passes between the pair of pressing rollers after the oven. The temperature variation thus causes quality variation. A pressing temperature that is too high disturbs air removal; if it is too low, it disturbs the formation of a strong bond between the glass and the interlayer.
This paper focuses on providing answers or ideas for solving the problems above. The ability to predict interlayer and glass temperatures in the glass lamination process is the key factor for success. The predicting method developed is based on theoretical and practical expertise in heat transfer in laminating. Its accuracy as well as the possibilities it offers for developing the lamination oven control are examined in the paper.
2. Heat transfer in glass laminating oven and theoretical solving method
In the flat glass laminating oven in Fig. 1 studied now, the heating is based on forced convection, which means that fans circulate hot air inside the oven, and hot air jets are blown from the holes in convection pipes toward the glass-film sandwich, which is also heated by the radiation emitted by the oven’s inner surfaces. The temperature of the oven is typically set at about 180 ˚C. According to the calculations based on the experimental data, the portion of the convection heating is between 85 and 92%, depending on the glass film sandwich.
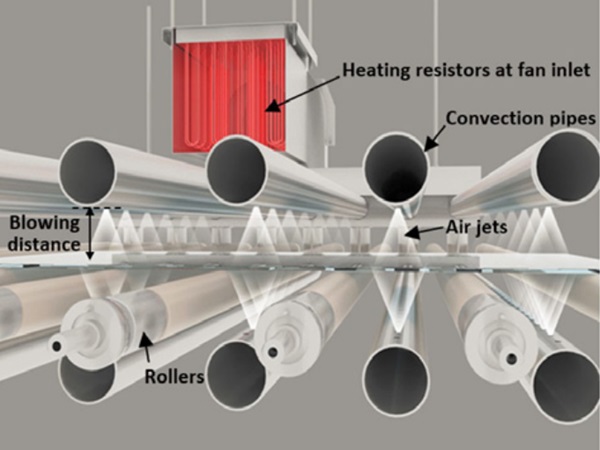
The method for solving a temperature distribution over the thickness of a glass-film sandwich is already given by [1] in GPD2017. For the oven above, it can be significantly simplified because of the absence of short wavelength radiation penetrating directly more deeply into the sandwich structure sheet.
More research has been undertaken since 2017. Forced convection heat transfer has been experimentally examined by heating an aluminum plate in the oven in Fig.1 and measuring its temperature curve over the heating time. More about such a method to solve the convection heat transfer coefficient is given by [2, page 99], for example. The blowing pressures, i.e., the overpressures inside the convection pipes, are also measured, as well as the effect of oven size on them. The aim of the new research above has been to develop the accuracy of the prediction method. The heat transfer coefficient solved is average for the top and bottom together. The next measurements in 2023 will focus on solving side-specific averages and studying the effect of blowing distance (see Fig.1) on the top value. The top blowing distance decreases with the increasing thickness of the sandwich, and with thick sandwiches, it differs significantly from the blowing distance on the bottom.
As a result of the work, a tool with which glass film sandwiches can be heat-treated virtually in a Glaston ProL laminating oven is developed. Fig. 2 shows its operating panel. In it, the heat-treated glass-film sandwich is defined by selecting thicknesses for the glasses and interlayers (this menu is not shown in Fig. 2), as well as material for interlayers and possible coating on the top surface of the first glass. The width and length of the oven must also be given. A heating recipe is then selected as in a real oven by setting values for line speed and oven temperature. A different fan motor speed 50Hz can also be used, which is not impossible in a real oven. The tool solves the development of temperatures for glasses and interlayers in the sandwich in the defined process. The predicting method can thus be utilized in a laminating oven. This is discussed in chapter 5.
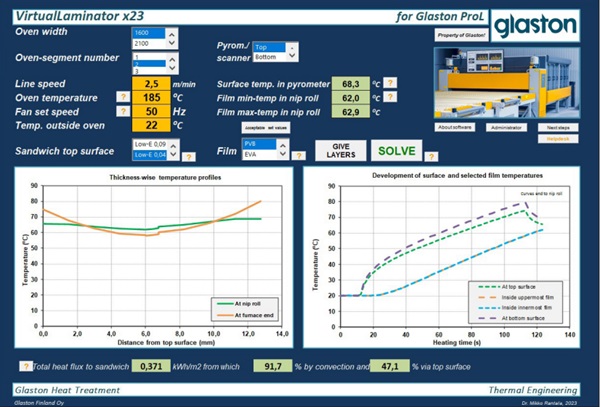
3. Measured and theoretically solved glass and interlayer temperatures
The predicting method can be helpful only when its accuracy is sufficient. Currently, the target for accuracy has been that the difference between realization and prediction is finally inside ± 3 ˚C in the end temperature of the glass surface and the interlayer. Such an accuracy is easily enough, and due to error marginals in measuring the realizations, the best possible provable accuracy cannot be much less than ± 2 ˚C.
The material properties needed for the prediction are thermal conductivity, specific heat, and density. For soda-lime glass, these are well known, and the variation between different manufacturers and glass types (clear, green tint, low-iron) is small. The values used for interlayers can still be sharpened if the exact interlayer type and manufacturer are known. The radiative properties needed for a clear glass surface are also well known, as well as for common low-e coatings. The radiative properties of clear and low-e coated glass are dealt with extensively in [2]. The radiative properties of the inner surfaces in the oven can only be estimated based on the experience and literature values for different materials. Fortunately, the share of radiation is low, which diminishes the effect of any errors in them on predictions.
The most important value for predictions is the convective heat transfer coefficient. As given above, it is solved experimentally, which is the only method that achieves sufficient accuracy. Theoretical equations in the literature can quite accurately predict the effect changes of blowing pressure, for example, on the convection heat transfer coefficient when the exact value for it is first solved experimentally.
The accuracy of the predictions was studied by heating several glass-film sandwiches with the full-scale lamination oven. As seen in Fig. 3 below, the sandwiches were equipped with thermocouples on the top surfaces and in the interlayers between glasses. During the measurements, the set values were copied down, and their realization was confirmed.
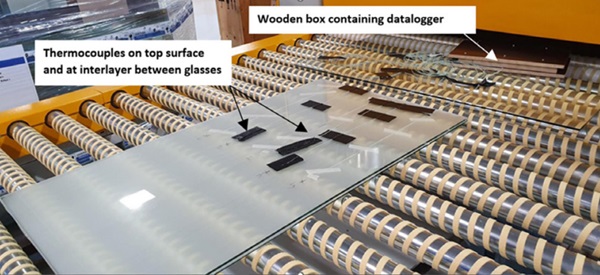
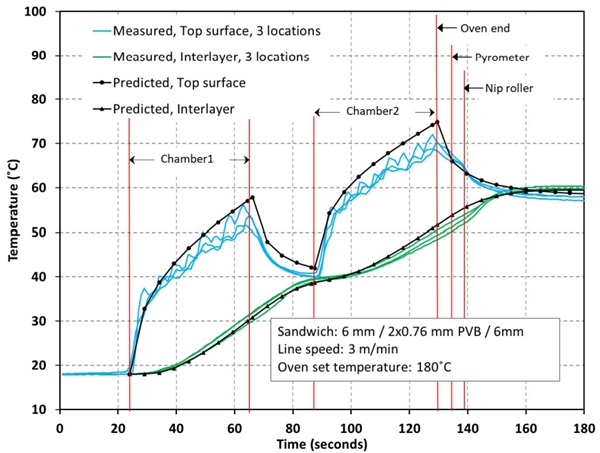
The results of the measurement are temperature curves for the measuring points over the heating cycle. The equivalent curves were solved theoretically by using the same set values, as well as the thicknesses for different glasses and interlayers. Fig. 4 shows measured and predicted temperature curves for 6 + (2 x 0.76 PVB) + 6 mm sandwich with a line speed of 3 m/min in a 180 ˚C oven.
The oven consisted of two separate heating chambers and a nip roller between them, as well as after the last chamber. Due to the nip roller between the chambers, the layout differs from the typical ones on the market. The layout is a little more challenging for predictions because the ambient cooling between chambers must be considered. This was taken into account by changing the convection heat transfer coefficient from the oven value of about 50 to 5 W/(m2K), which should be a fairly accurate value for free convection on a horizontal surface moving slowly in slightly colder ambient air. During the test, the nip rollers did not squeeze the sandwich. The data in Fig. 4 contain three measured curves for both the top surface of the upper glass and the interlayer, which were measured from different locations inside the area of the sandwich.
The correspondence of measured and predicted temperatures in Fig. 4 is quite clear. As can be seen, the measured surface temperature curves contain eight wave crests in both heating chambers, which are caused by local convection peaks under the convection pipes. The prediction method cannot consider them because it uses an average heat transfer coefficient over the chamber length. The effect of this difference on the heating speed of the sandwich is very small as long as the average s accurate. As a detail from Figure 4 can be seen that the temperature of the interlayer increases after the oven, pyrometer, and even after the nip roller. Such a slow flattening of the thickness-wise temperature profile is generated by the low thermal conductivity of both materials in the sandwich.
4. Data collected from lamination ovens in production use against theoretically solved glass exit temperatures
The data collected automatically from the lamination ovens in production use contain sandwich-specific information, including the total thickness and length of the sandwich, the set values for line speed, the measured oven temperature, which was quite near the set temperature in all cases, and the measured average surface temperature of the sandwich exiting the oven. These data are useful for the validation of the prediction method. In this case, the prediction method is coded to predict the equivalent surface temperature, as the data above contain with the same oven settings. The comparison for thousands of samples can be made in a few hours, mostly spent forming the result figures.
The data for Fig. 5 are filtered so that only sandwiches with a total thickness of 8.5 mm are selected. The total thickness is the value recorded from the heating recipe used. The thickness does not give the thicknesses for glasses and interlayers in the sandwich, which is needed as initial data for the prediction. To overcome the problem, the prediction method assumes that all sandwiches are composed of two glasses with equal thicknesses and of one 0.76 mm PVB-interlayer, which can be called as a symmetrical composition. For the 8.5 mm above, this assumption concerns a sandwich of 3.87 + 0.76 + 3.87 mm, which is believable because it matches the typical exact thickness of 4 mm glass.
It is also important to consider that the values in the data used contain some error marginals. The line speed is not necessarily exactly 2.8 m/min, for example. The measuring accuracy of the thermal scanner measuring the glass exit temperature is about ±1 ˚C if its lens is not dusty. Moreover, some dimensions used in prediction like the distance from the oven exit to the scanner may differ a little from that in the layout drawings.
Fig. 5 contains data from 265 loadings (= separate sandwiches), consisting mostly of many sequentially laminated sets of similar loadings from different days, between which some other total thicknesses are laminated.
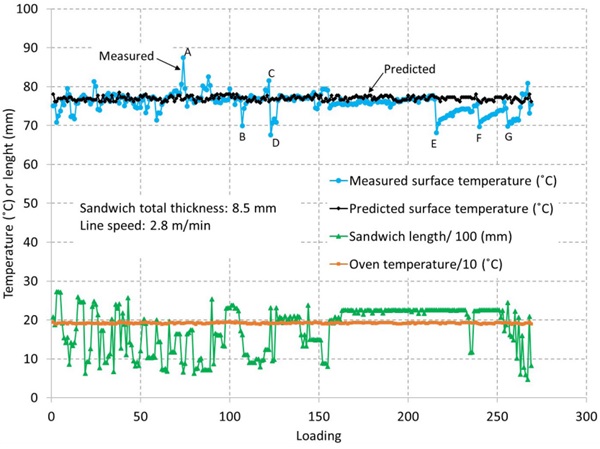
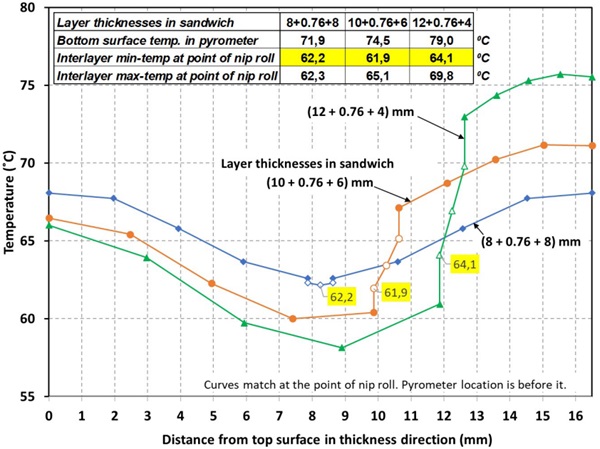
Some individual loadings or short sets of them are also included. Note that oven temperature and loading length are divided by a given number to form a more illustrative figure. The oven set temperature was between 185 and 195˚C for all loadings, as well as the loading length was between 450 and 2750 mm.
As Fig. 5 shows, the correspondence between the measured and predicted surface temperature of the sandwich is mostly quite satisfactory, but there are also some significant differences. The most interesting differences are marked with letters in the figure. It was attempted to identify the reasons for them in the data. Difference A was caused by a mistake in the data based on the unbelievable time gap between the next loading. Difference B appears for the sixth loading in the working day, before and after which the thickness and line speed were changed. The set oven temperature was also increased by 4 ˚C before this. Difference D appeared for the third (difference G for the 20th) loading in the working day, before which the thickness and line speed were changed. The set oven temperature was also increased by 4 ˚C before this.
Differences E and F matched the first loadings in the working day and the first loadings in the long series. As Fig. 5 shows, after loadings E and F the difference slowly decreased for the next loading. So, some kind of possible explanation was found for all the marked differences in Fig. 5 expect for difference C, which appeared for the last loading in the series, after which line speed increased, and the thickness decreased. The explanations were as follows: The line speed was probably changed when the loading was already in the oven, which changed its actual heating time from what can be calculated from the line speed and oven length. The set oven temperature was changed just before the loading, but it took time for the change to be seen in the actual oven temperature. This especially concerns the beginnings of the working days before which the oven was waiting for the production in maintenance mode.
A similar comparison to that in Fig. 5 was also made for many other total thicknesses with equivalent results, expect for a total thickness of 16.5 mm, for which the predicted temperatures were commonly about 6 ˚C lower than the measured ones. Later, it was understood that this was because of the significant thickness-wise asymmetry in the 16.5 mm sandwich laminated by the customer from which the data were recorded, which significantly affect the temperature profile of the sandwich, as Fig. 6 shows. In Fig. 6, the difference in the bottom surface temperature at the point of the pyrometer is as much as 7.1 ˚C, but at the interlayer, the minimum temperature at the nip roller is only 2.3 ˚C. The assumption for the symmetrical sandwich is not always valid, which disturbs the comparison between the predicted and measured surface temperatures. However, the effect of the asymmetry on the interlayer temperature at the location of nip roller is quite small if the sandwich contains only one interlayer.
The data also contained unbelievable variations in the measured end temperatures, even though the sandwich and the recipe seemed very similar. This may be explained by the low-e coating or the painting on the outer surface of the sandwich, because appearing of them cannot be seen from the data. Moreover, the shape or size of the sandwich may still have an effect on the measured average temperature which is formed by computer code based on the data from the thermal scanner.
An important assumption not yet mentioned is that the glass and interlayer initial temperatures were set at 20 ˚C for all loadings in solving the predictions. This works well for the interlayer, but for glass, there can be a significant difference for the reasons given in the introduction. The initial glass temperature is an important input value for the prediction, so the prediction accuracy increases if the measured value for the initial glass temperature is available. Its online measuring presented in [3] is the answer for this. In [3], the effect of the variation in initial glass temperatures on variation in the temperature of the glass-film sandwich in the nip roller is eliminated by measuring the glass temperature before the oven and adjusting the line or fan impeller speed based on this, which is an answer to the third problem in the introduction.
Above reasons are comprehensively listed for why the data collected automatically from the lamination lines are still quite incomplete to use as a base for the validation of any prediction method. Future work will focus on developing the increase in the validity of the data.
5. How prediction method can be utilized in machine automation?
As a first answer to the second problem in the introduction, the prediction method is already in a form that enables the reliable solving of heating recipes, which especially helps in laminating extraordinary sandwiches of which the operator lacks efficient experience. This offers possibilities for savings in working time and quality costs. Some savings in electricity bills can be found in all sandwiches, while prediction exposes if the interlayer is heated to an unnecessarily high temperature with the current recipes.
The first step in the utilization of the prediction method is that it could be offered as an auxiliary tool for the operator for solving the heating recipes. For example, it could be located on its own page behind the main control panel page and equipped with the ability to transfer with a click the solved recipe as the adjustment values for the oven.
An increasingly useful utilization would require the coding of the method fully inside the oven’s control system. In this case, in the first instance, a method could be created that warns of an incorrect recipe selection or simply displays the temperature of the interlayer on the display terminal beside the measured surface temperature. The method could get the total thickness of the sandwich from the automatic thickness measuring device or from the selected recipe and use the previously mentioned assumption of the symmetry of the sandwich. The success in predictions could be monitored and ensured based on the measured surface temperature of the sandwich used, as expressed in chapter 4. The answer to the first problem listed in the introduction is therefore that the interlayer temperatures can be exposed by adding an accurate prediction method to the oven controlling system.
It is clear, that the recipe selection could be fully automated with the predicting method if the heating result before a sandwich is conveyed to the oven is known. Then, only the target temperature for the interlayer would then be given as a set value, and the oven control would handle the rest automatically by adjusting the line speed, fan impeller speed, or oven temperature. However, such a control would be incomplete as long as only the total thickness is given as initial data for it. This is problematic because automatic thickness gauges can measure only the total thickness. The thicknesses for different layers should therefore be given manually, which is a slightly time-consuming extra assignment for the operator, and it reduces the degree of automation. Fig. 7 shows an example of unique process information the intelligent control knowing the composition of a sandwich could show on the screen which monitors the production.
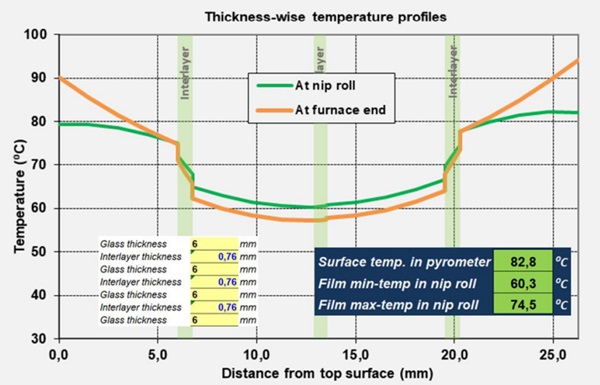
A significant advantage of the machineintelligence based on the thermodynamicsbased prediction method used above is that it makes it possible to quickly consider the changes in the design of a new oven in heating recipes. The oven length, fan, or nozzle array in the convection system may change. Based on the work already done and with the heat transfer coefficient equations, it will then be possible to solve heating recipes for the new design quite accurately immediately before any glasses have been laminated with it. This is also a significant advantage over pure mathematical methods based on the collected data, with which the required line speed to obtain a certain surface temperature after heating can be solved statistically for the common sandwich compositions.
It is also possible to develop a thermodynamicsbased prediction method for the laminating ovens equipped with quartz tube heaters, emitting shortwave IR radiation. However, the prediction accuracy for them would probably never reach the same level as in the convection oven studied now, because in general, heating with IR -radiation based ovens is more complicated and more sensitive to mistakes. In the invention [4] related to convection ovens, the heating blowing onto the tail end of the sandwich is reduced to slightly reduce its temperature, which improves and guarantees air removal from the sandwich via its tail edge in the nip roller. Future work will define whether the control of this local convection reduction can be handled based on thermodynamics-based modeling.
6. Conclusions
Lamination ovens aim to heat an interlayer film between glasses to a certain temperature before it enters the nip roller, but the realized temperature is unknown. This problem can be solved by coding an accurate thermodynamicsbased, or more accurately, the said thermal engineering-based prediction method inside the oven control code, and by setting it to solve the temperature of the interlayer. The reliability of the method is improved when the temperature of the surface of the sandwich is also solved and monitored online against the corresponding measured value.
The variation of initial temperatures of the glasses to be laminated causing quality costs can be easily and accurately considered in the line speed with a thermodynamics-based prediction method receiving information about the measured initial temperature of the glasses.
With an accurate prediction method, the operation with a laminating oven could even be automated so that the oven would be given the task of heating the interlayer film to the desired temperature, which would be implemented by the oven control.
The main shortcoming in the utilization of any prediction method in lamination oven control is that only the information about the total thickness of the sandwich is currently available automatically, which limits the use of the method in automating the selection of the heating recipe. The method is forced to assume that the sandwich always consists of two glasses with equal thicknesses and a typical interlayer thickness between them, which causes inaccuracies and, with sandwiches containing several films, a significant error in the solved recipes and interlayer temperatures.
The thermodynamics-based prediction method tailored for the Glaston ProL laminating oven is ready. Future work will further secure and improve its accuracy, which is already quite satisfactory. After this, there is a choice to be made about how to start using the method more widely to help customers. The paper brought out some options. The potential benefit comes in the form of a reduction in working time costs, electricity bills, and quality costs.
References
[1] Rantala, M., Thermal radiation compared with forced convection heating in a flat glass laminating oven, Proceedings of Glass Performance Days 2017 Conference, 2017.
[2] Rantala, M., Heat Transfer Phenomena in Float Glass Heat Treatment Processes, Tampere University of Technology, PhD Thesis, Tampere, 2015, URN:ISBN:978-952-15-3692-2
[3] United States Patent, US11485128B2, Glaston Oyj Abp, Priority day 15.12.2020.
[4] European Patent Application, EP396748