Article Information
- Digital Object Identifier (DOI): 10.47982/cgc.9. 638
- Published by Challenging Glass, on behalf of the author(s), at Stichting OpenAccess.
- Published as part of the peer-reviewed Challenging Glass Conference Proceedings, Volume 9, June 2024, 10.47982/cgc.9
- Editors: Christian Louter, Freek Bos & Jan Belis
- This work is licensed under a Creative Commons Attribution 4.0 International (CC BY 4.0) license.
Authors:
- Marcel Reshamvala - Bollinger+Grohmann Consulting GmbH / FKG - Fachverband Konstruktiver Glasbau e.V.
- Kathrin Rauh - seele GmbH / FKG - Fachverband Konstruktiver Glasbau e.V.
- Philipp Kießlich - TU Dresden / FKG - Fachverband Konstruktiver Glasbau e.V.
- Isabell Ayvaz - TU Darmstadt / FKG - Fachverband Konstruktiver Glasbau e.V.
- Julian Länge - knippershelbig GmbH / FKG - Fachverband Konstruktiver Glasbau e.V.
- Michael Elstner - AGC Glass Europe / FKG - Fachverband Konstruktiver Glasbau e.V.
- Daniel Pfanner - Bollinger+Grohmann Consulting GmbH / FKG - Fachverband Konstruktiver Glasbau e.V.
- Miriam Schuster - TU Darmstadt / FKG - Fachverband Konstruktiver Glasbau e.V.
Abstract
Glass is an energy intensive material that is essential to buildings and their energy consumption. Its transparency allows for natural daylighting and the use of solar heat gains. In the context of the refurbishment politics of the EU as a result of the Paris Agreement on climate goals, significant amounts of glass waste in form of windows and façades are to be expected. In order to minimize the environmental impact of glass by preserving the embodied carbon and substituting newly produced glasses, the reuse of glass is considered to be of the highest potential. When reusing panes, energy and raw material can be saved that otherwise would be consumed for the production of new glass. This way, the common principles of sustainability - sufficiency, efficiency and consistency - can be realized for the life cycle of flat building glass. The following case study estimates the potential of differentscenarios for circular waste treatment of glass panes by applying the 9R Framework to insulating glass units (IGUs). The scenarios are defined and presented. A life cycle assessment (LCA) using identical system boundaries for these scenarios was executed and the results are compared to producing IGUsentirely with new glass. Finally, the feasibility of the strategies is evaluated and recommendations for the processing of glass in stock are derived.
1.Introduction
1.1. Motivation
As consequence of the Paris Agreement in 2016 the European Green Deal has been initiated with the aim of climate neutrality in 2050. It includes a strategic approach to decrease carbon emissions of the industry and in particular of the residential building sector which is accountable for 40% of energy consumption as well as 36% of C02 equivalent emission (UN environment programme, 2019). A particularly strong leverage on reducing carbon emissions can be utilized by managing the operative energy of buildings which is not only being affected by technical equipment but the physical properties of the building envelope. Transparent components in the building envelope are designed to fit the energetic needs of a building by determining the solar gains as well as energy losses throughout dynamic climate conditions. Since most buildings are older than 20 years, the energetic standard of these windows is low and replacing them can save significant amounts of energy and carbon emissions (Bakker, 2019). That is why exchanging these windows is an important part of the renovation wave in Europe as part of the European Green Deal.
As a result, old windows will enter the waste management system. Solely in Germany 251.000 t of glass waste are to be expected annually (Conversio Market & Strategy GmbH, 2023). With glass being an energy intensive product mainly due to the melting of minerals at around 1600°C, considerable amounts of embodied carbon are entering the waste management system. Glass maintains its functional state for the building sector when unbroken. Once broken the same energy has to be reinvested to remelt and manufacture panes anew. Supplementing a production batch with cullets can save up to 2,5 % of fuel and 3,6 % to 5,3 % of carbon dioxide per 10 % cullet, which is the amount of energy that is needed for melting and heating gases in the furnace (Beerkens, Kers, & van Santen, 2011; ift-Rosenheim, 2019). It also saves 1,2 kg raw materials per 1 kg float glass, which is the mass of raw materials before chemical reduction to glass. Despite this, it is rarely stated that breaking glass to recycle as cullet renders all of the embodied carbon except the just stated benefits useless. Taking into account that currently pre-consumer glass cullets and rarely post-consumer cullets contribute to the production of glass for the building sector due to furnace compatibility and contaminations, it is questionable if investing energy to produce cullets that need to be reheated in contrast to invest energy to use whole glass panes is the most sustainable way (Rota et al. 2023; Geboes et al 2022).
Intuitively, the reuse of glass panes as substitute to freshly produced glass occurs to be the most promising strategy to minimize the environmental impact in the lifecycle of float glass products (Hartwell & Overend, 2019). However, in practice there are a series of challenges to be addressed before reuse can be considered or rejected as a viable option. Same logic accounts for other recycling strategies besides reuse, like remanufacturing or repurposing that have to be investigated and characterized.
The investigation focuses on the possibilities of extending the lifetime of existing glass panes or façade elements. The goal of the study is therefore to identify and assess potential ‘R-’scenarios (compare section 2 and 5) that can be of interest for the glass industry. On top, through applying life cycle assessment (LCA), possible missing data is to be identified and discussed. The results provided in the course of the paper are to be considered within the boundary conditions and limitations which are given in section 2. This study intends to provide a first estimate on the feasibility of possible ‘R’-scenarios and their saving potentials and not a general statement for all types of façades. The study is part of the investigation currently performed in the working group ‘climate and sustainability’ which is part of the German Association for Glass in Construction (‘Fachverband Konstruktiver Glasbau (FKG)’). The work complements the current investigations on the technical feasibility as well as determination of legal possibilities the group is also working on in parallel.
1.2. Sustainability and R-Strategies
The Brundtland-Report (1987) states that Sustainability is defined as “meeting the needs of the present without compromising the ability of future generations to meet their own needs”. It refers to the exhaustive usage of finite resources such as raw materials but also air quality and fertility of the soil which is to be considered the biggest challenge of our time. Establishing the Circular Economy which aims to be an “industrial economy that is regenerative by intention and design” (Ellen McArthur Foundation, 2013) is part of the solution to this challenge. The transition from a rather linear economy to the circular economy is a complex and difficult process. Different principles and strategies are applied that are part of the ongoing research and part of modern policies. These principles are also guidelines that help to understand how to intentionally design an industrial process to be regenerative and therefore shape our common future.
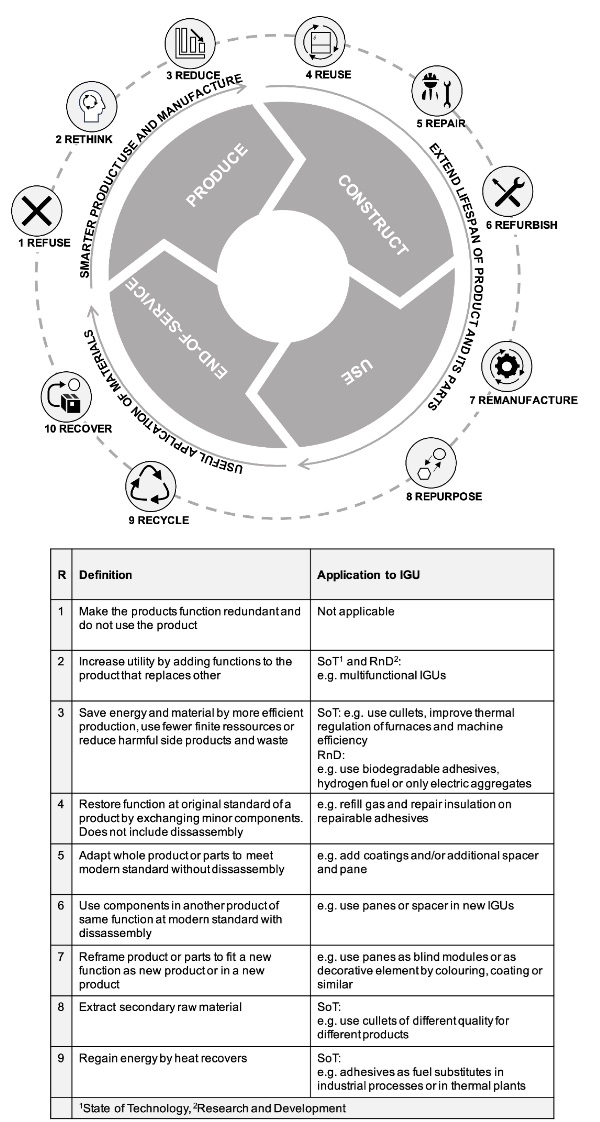
The transition to a circular economy can be achieved by designing and establishing new routes within waste management which is the interface between the life cycles of different products. More specifically, these routes are implemented by so called ‘recycling’ strategies (‘R’-strategies) that are based on the principles of Sufficiency, Efficiency and Consistency and are to some extent applied by directives such as the European Directive (European Commission, 2008). A defined group of strategies is called a Framework and has a higher order the more strategies it differentiates (e.g.: 3R-Framework with the strategies Reduce, Reuse, Recycle). Orders range from R0 to R9 and the higher the order the more sustainable implementation can usually be achieved. Depending on a material and its life cycle there can be exceptions (Potting, J., Hekkert, Marko, Worrell, & Hanemaaijer, 2017).
Figure 1 presents the R9-Framework which consists of the strategies R0 Refuse, R1 Rethink, R2 Reduce, R3 Reuse, R4 Repair, R5 Refurbish, R6 Remanufacture, R7 Repurpose, R8 Recycle and R9 Recover. Also brief definitions for the strategies are given, which follow interpretations of (Kirchherr, Reike, & Hekkert, 2017) and (Morseletto, 2020). In addition, examples are given in figure 1 on how the strategies are already applied or can be applied to Insulating Glass Units (IGUs).
In this case study the strategies are applied on existing IGUs at their usual end of service life to possibly extend the service life or refurbish or remanufacture them to make products, that have a full service life from anew. 5 different scenarios (R3 Reuse (Scenario 1&2), R5 Refurbish (Scenario 3), R6 Remanufacture (Scenario 4) as well as R7 Repurpose (Scenario 5)) will be investigated. The derived scenarios are schematically shown in figure 2 and are further addressed in section 2.3.
2. Methodology
The following section describes the use of data, calculation assumptions or requirements, the conception of scenarios based on circular strategies and construction details of the given case. The authors deliberately chose less complex constructions and transportation cases to increase the transparency of the following calculations with the primary goal to identify gaps in data and to emphasize the difference in potential when applying different R-strategies.
2.1. LCA
In order to compare the different scenarios, which will be described in section 2.3, data in the form of Type III - Environmental Product Declarations (EPDs) from Life Cycle Analyses (LCA) is used as calculation basis. Type III declarations such as the EPDs for float glass products that were used in this study provide objective data without demanding the fulfilment of benchmarks. Since buildings are products made up from other products, benchmarking takes place in form of certification processes such as DGNB, LEED, BREEAM and others. Because of the complexity of economy and environment as well as data in general, a series of standards is necessary to define the process of collecting data, relating them to models of industrial processes or environment and to generate useful data. In the following their structure is shortly explained.
The methodical approach of data collection and their assessment are specified in ISO 14040 and ISO 14044. The data retrieved in conformity to these standards are the basis for Type III - EPDs that are specified in ISO 14025 in means of data quality, environmental categories and verification. This standard also defines the Product Category Rules (PCR) which deepen the methodology on modelling with LCA data to guarantee comparability between products that are otherwise left to matter of interpretation. DIN EN 15804 and DIN EN 15978 are standards that set specific requirements for the environmental assessment of building products and buildings. They define the life cycle stages of products displayed as modules (A1 to D) (see Figure 2). In an EPD, environmental indicators based on the declared environmental model (usually IPCC 100 years “Baseline”-Model) are described for the given modules.
![Fig. 2: example for data structure of an EPD [EPD AGC - Solar control magnetron coated glass (ipasol, Stopray)].](/sites/default/files/inline-images/Fig2_422.jpg)
System boundaries and chosen Indicator
Not all environmental impacts of the scenarios under consideration can be quantified with sufficient accuracy due to the availability of data. In order to make the LCA results comparable, system boundaries must be defined. Temporal system boundaries indicate which life cycle modules are to be taken into account in the life cycle assessment of the corresponding component.
In the following assessments, the system boundary cradle to practical completion (A1 to A5) and disposal phase (C1 to C4) was defined. As this study focuses on carbon emissions, the ecological indicator “global warming potential (GWP)”, given as kg CO2 equivalent, was chosen to compare the potential of the different scenarios.
Data base
When comparing and calculating data from EPDs, the subtype of the data set and the status of the norm have to be declared and chosen evenly to account for comparability. Standard DIN EN 15804 has been updated in 2020 and includes a series of changes to calculation methods, indicators and their relation. These are defined as 15804+A2, formerly 15804+A1. Data between these versions is not comparable. In this study data from format 15804+A2 is used.
The different data subtypes are shortly explained in Table 2. As the system limits of the different subtypes differ greatly, data between different subtypes is not compared. Only specific EPDs from glass manufacturers are used in this case study.
Table 2: general subtypes of datasets.
For the carbon assessment of the glass. panes, EPDs of different suppliers were compared, as the values for carbon emissions vary. As the focus of this study is on the glazing, EPDs of different manufacturers for the same type of product (e.g. annealed glass, coated) were used and average values calculated (see appendix). So, the calculation does not display emissions associated to a single manufacturer but more the current state of the industry. For all other components of the façade, such as aluminum, substructure, insulation, thermal break, etc., EPDs were selected that reflect current market production. No low-carbon options for glass were taken into account so far.
A major data gap emerged when the individual process steps were examined. Usually, in EPDs the data sets for modules (A1 – A3) regarding the process from raw material extraction to the finished product are summarized. This includes secondary manufacturing processes as required in the production of an insulating glass pane e.g. cleaning the glass pane, transportation within the factory, cutting the glass panes, edge treatment etc. They are typically accounted for in one combined value and not listed separately, making it impossible to derive data necessary to estimate the contribution of specific steps that need to be considered in case of circular scenarios (compare section 2.3). As shown in table 1, some of these process steps are currently considered negligible. In order to improve the information content and accuracy of the calculations, values were determined by combining various EPDs. One example of this is the assumption for the CO2 footprint of a coating used on a pane, which is within this study determined by calculating the difference between the GWP of a coated and an uncoated pane (compare data in appendix).
Emissions in Process Steps
Emissions were neglected for some process steps (see Table 1), either because there is insufficient data available, the process is yet non-existent or because the emissions are considered low compared to the production of the individual components (assumption). It is important to emphasize that a detailed consideration and evaluation of circular scenarios is necessary. The smaller processes shouldalso be taken into account. Yet, their overall scope could not be estimated at the moment due to missing data.
In order to adequately consider these individual process steps, it is necessary to obtain information from the manufacturer on the percentage breakdown of the individual secondary manufacturing steps in relation to the specified emission values, particularly for modules A1-A3.
The removal, cleaning, cutting and installation of the glazing largely uses energy in the form of manpower. The associated emissions are considered negligible (see table 1) as no large machines are required. Additionally, emissions during removal and installation depend largely on the complexity of the installation situation. The debonding of IGUs is not currently a practical application, which is why no data is currently available. Processes as the latter are currently under the investigation of the working group ‘climate and sustainability’ of the FKG to help provide information on the processes and their impact, e.g. for an analysis as the LCA in the future.
2.2. The Reference Façade
In order to investigate possible scenarios, a realistic but rather simple reference project was chosen to determine emissions and compare them.
The reference project is a planned building in Berlin. It is assumed that a building in Munich, that is to be demolished, can provide components which are fully or partially useable as components for the façade of the reference project in Berlin. The choice primarily should allow to estimate the transportation impact that could reasonably occur in Germany. A thermal transmittance (Ug-value) of 0.6 W/m2K was defined for the reference façade, which leads to a glass buildup of a triple insulated glazing unit (triple IGU) with 4 mm float glass panes and 14 mm spaces containing Argon and having a coating on surface 2 and 5 (where surface 1 represents the outer surface of the outer pane and surface 6 the inner surface of the inner pane). Besides transparent areas, a ventilated façade with glass cover elements (thermally toughened and rear side fritted) is considered. A scheme of the reference facade as well as the defined functional requirements is given in Figure 3.
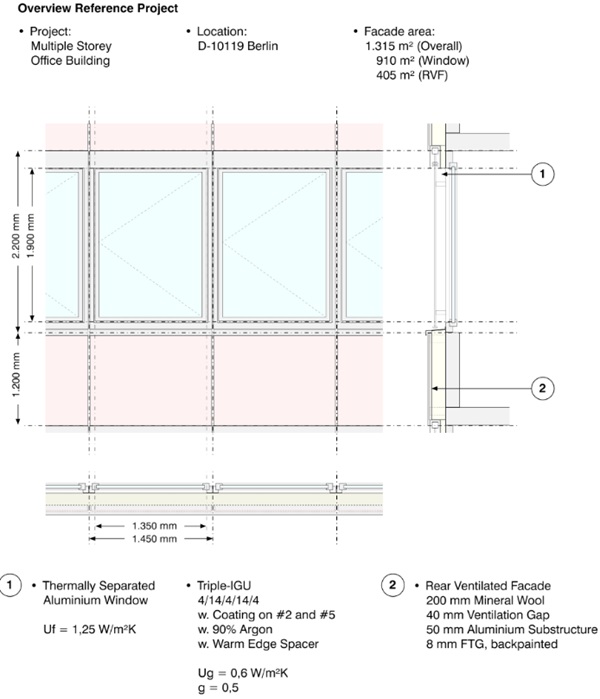
A reference case, ‘scenario 0’ was considered. It represents a fully new façade. In a first step, the carbon emissions of all relevant façade components for that reference scenario are calculated. All results of possible ‘R’-scenarios (chapter 2.3) are then to be compared to the emissions of the reference scenario to allow a statement on the effectiveness of the chosen scenario.
Considering not only the glass panes but also the façade systems as a whole allows to determine how high the proportion of emissions from the IGU and single glazing is in relation to the other façade components as well (aluminum profiles, aluminum sheets, insulation, substructure, sun shadingsystem, etc.). It should be noted that all calculations are only valid for the example presented and can only provide a rough estimation of the scenarios’ potentials.
2.3. R-scenarios
Following the R-strategies defined in section 1.2 different scenarios arise from conceptualizing the possible applications of strategies to IGUs, which will be described in more detail below. The derived scenarios represent the experience from the members of the sustainability working group of FKG (i.e. planners, manufacturers, researchers) that have collected which scenarios are currently asked for in practice.
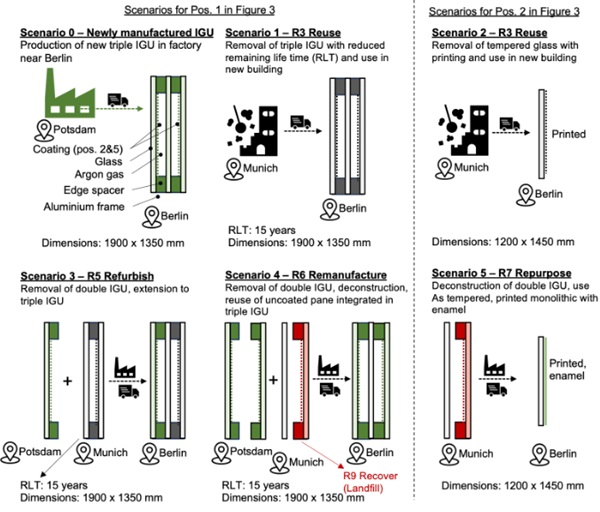
In Figure 4, scenario 0 is the reference façade (described in section 2.2) which corresponds to a possible newly produced façade. In scenarios 1 and 2, components are removed from an existing building, transported to the new construction site and reinstalled without any change of the components itself (Re-use). This investigation allows a statement on the extent of the impact of transportation compared to the production of a glazing. In scenario 3 an existing double insulating glazing unit is extended to a triple insulating glazing unit using one freshly produced, coated glass pane. R-strategy Remanufacture is applied in scenario 4. In this scenario an existing insulating glazing unit is separated and the uncoated glass pane is reused as the internal pane of a triple insulating glazing unit. The other two glass panes are freshly produced, coated glass panes. The existing coated panes in this scenario cannot be further used as the coating gets damaged when the insulating glazing unit is separated. The two new panes and the reused pane are assembled to form a new insulating glazing unit. In the final scenario 5 the R-strategy R7 – Repurpose is applied. An existing insulating glazing unit is separated and the uncoated pane is thermally toughened and fritted and being reused as part of a curtain wall.
All of these scenarios are hypothetically possible circular scenarios. The technical feasibility will be determined in a parallel study by Fachverband Konstruktiver Glasbau (FKG).
In order to use secondary materials in the refurbishment of the described reference façade, industrial processes are necessary to achieve the defined properties for the secondary products. This requires additional process steps to implement the use of second life panes for the production of IGUs.
In the following the process steps are presented for the reference façade, i.e., the façade in which a completely new product is installed.
Scenario 0 (reference): production and transportation of newly produced triple IGU
- Raw material extraction
- Raw material transport to production site
- Processing of individual components (cleaning, cutting, coating, assembly of IGU, gas filling)
- Packaging
- Transport to production site. It is assumed that all materials and processes relevant for the IGU production are provided by companies within 400 km from the construction site.
- Installation on site
Compared to the reference façade additional processing steps and transportation steps need to be considered for circular scenarios 1-5. Those steps and the assumptions in this case study are summarized in Table 3. Waste was only considered as already taken into account in the used EPDs.
Table 3: Considered life-cycle modules for each scenario and basic assumptions.
These process steps are to be considered as proposals by the authors and need to be redefined once a process for re-using IGUs is implemented.
3. Calculation Results
As described in the previous sections, the individual scenarios have been evaluated in terms of their carbon emissions. The results of these Life Cycle Analyses are shown in Figure 5 and 6.
The calculation results of the carbon emissions of the reference façade (scenario 0, see figure 3) are displayed in Figure 5. It shows that the proportion of emissions caused by the glazings of the façade is 28 % (highlighted in blue) and therefore makes a significant contribution to the emissions of the façade. Transport has a share of 8% with 8.2 kgCo2eq/m2. Although optimizing components such as window frames, metal cladding, substructures or insulation has a high potential to reduce embodied carbon emissions, the focus in this study is the re-use of insulating glazing and single glazing units. The following scenarios (S1 to S5) therefore concentrate on the share of glazing within the reference façade.
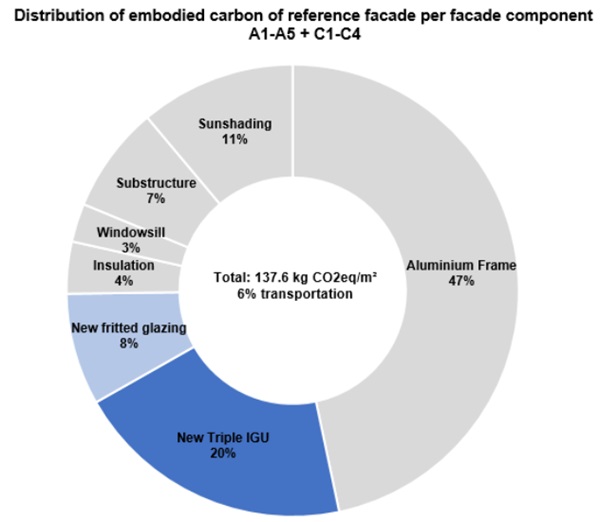
Figure 6 shows the calculated values of embodied carbon for the different scenarios. In contrast to figure 5, figure 6 only displays the results for the glazing units (upper part of the façade) or thermally toughened and fritted safety glazing (rear ventilated façade) and not the complete reference façade. The first bar in dark blue and the first bar in light blue show the carbon emissions for the new produced triple IGU respectively thermally toughened and fritted safety glazing considered in scenario 0. These two results represent the values to be reduced and against which the results of the other scenarios are compared. The following three dark blue bars show the results for the different scenarios S1, S2 and S4 for the insulating glazing unit. The last two bars in light blue show the results of scenario S2 and S5 for the monolithic pane of the rear ventilated façade.
Figure 6 shows that scenario 1 leads to a reduction of carbon emissions for the insulated glazing unit of 93% and scenario 2 leads to a reduction of 94%. This result is plausible as only the transportation from the construction site ("removal site") to the installation site was taken into account. However, it should be noted that the reduced service life of the elements was not included in the calculation.Parallel studies by Fachverband Konstruktiver Glasbau (FKG) on building law issues, loss of quality and shortened remaining service life of the glass have not yet influenced these results.
Scenarios 3 and 4 lead to a reduction of carbon emissions of around 45 % (scenario 3) and 10 % (scenario 4), which confirms the high potential of applying R-strategies "Refurbish" (S3) and "Repurpose" (S4) to insulating glazing units and single glazings. Scenario 4 in particular is assessed as the easiest to implement in technical and legal terms, as the existing pane is used as the new internal pane of the triple insulating glazing unit and in principle has a longer remaining service life than scenario 3.
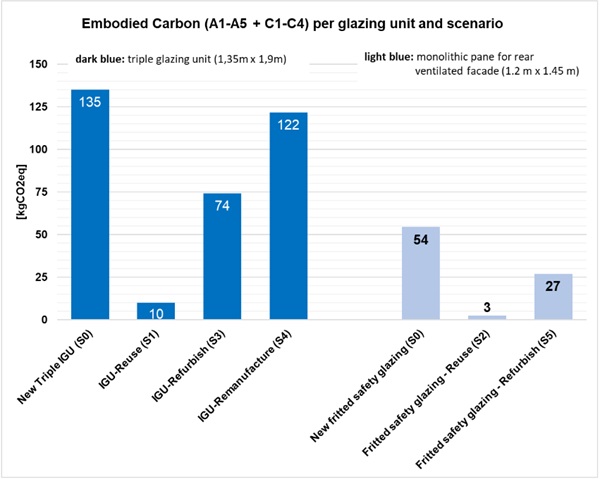
The Refurbish-Scenario for the fritted glazing of the rear ventilated façade (scenario 5) also leads to a reduction of the embodied carbon of 50 %. In this case it needs to be especially considered that glass panes with the required thickness might not be available on site, but possibly in the future. Compared to scenario S2 the scenario is less effective which is plausible due to the energy intensive process of thermally toughening the glass.
4. Discussion
In principle, the results demonstrate the significant potential to make use of embodied carbon byreusing glass panes. It is evident that the greatest advantage is attained when minimizing the need for additional processing steps. This is shown in scenarios 1 and 2. Even if it still needs to be clarified what effect the shortened remaining service life will have, this result shows above all that the emissions from transportation within Germany are low compared to the emissions from production of new glass panes, which should encourage considering reuse-cases.
Technically and in legal terms, scenario 4 is probably the easiest to implement, as the existing glass-pane is used as an internal pane of the insulating glazing unit and combined with two newly produced coated panes. The quality of the insulating glazing unit might therefore be nearly the same as a completely new produced IGU. Although the potential saving here is the lowest at 10%, this scenario could be a valid option as there are further optimization options.
One possible optimization of scenarios 0, 3 and 4 is the use of low-carbon glass, a glass that is produced with renewable energy resources and has a high content of recycled resources, for the necessary newly produced glass panes. As the use of low-carbon glass is not yet standard, attention must also be paid to the availability of this glass. With low-carbon glass, the study shows that a reduction in emissions of up to 50% can be achieved in the production of a new glass product, whereby the process steps for processing the individual panes into multi-pane insulating glazing remains unaffected. Realistically, the availability of cullets to meet the quantitative demands of flat glass by using low-carbon glass only is doubtable. But as it is currently not possible to reuse the coating on existing panes (Glass for Europe 2023), as the coating gets damaged when the insulating glass pane is separated, these coated panes could be remelted and used for the production of low-c -glass. The great advantage of the remanufacturing strategy is the quality of the product achieved while still saving a considerable amount of carbon emissions.
Another option is to remove uncoated panes from several insulating glass units to form a new insulating glass unit. For this purpose, it must be investigated whether it is technically reproduceble to coat existing glass in sufficient quality.
The R-s trategy Refurbish delivers significantly better results with savings of up to 50%. However, the quality of the product is technically difficult to evaluate as the quality of the existing insulating glazing units must first be assessed and can vary greatly. This implies a high dependence on the quality of the existing product.
Another important point is that many individual processing steps such as cleaning and cutting have not yet been specified as individual process steps in EPDs. As these processes are still being developed for the reuse-scenarios of glass, this is not possible yet. Nevertheless, it is an important information for comparing the scenarios and should be provided in future.
Furthermore, it is difficult to estimate the influence of the installation of the façade on the overall emissions. According to current estimates, these influences are minor, which is why they have been neglected in this case study. Depending on the complexity of the façade, however, this proportion may be greater and should be examined more closely in further studies.
Finally, the indicator of embodied carbon does not account for resource availability. This means that even if in the future different process steps for various R-strategies are more costly in consumption then still natural resources are spared (addresses sufficiency). Also, the increase in cullet quality as additional benefit of improved handling of flat glass can have a great impact on emissions in glass manufacturing.
5. Conclusions and Future Work
The study performed by the working group Sustainability of FKG demonstrated that the reuse of glass panes presents a significant potential to reduce embodied carbon emissions in the glass industry. This can especially be achieved by minimizing additional processing steps. Scenarios 1 and 2 highlight the advantage of reducing emissions through reuse, despite uncertainties about the shortened remaining service life of the glass. It was shown that transportation emissions within Germany are minimal compared to the production of new glass panes, encouraging reuse considerations.
The results for the individual scenarios can now form the basis for decisions on the direction in which further technical investigations should be carried out, that provide information on the strength of used glass, the possibility of recoating and laminating used glass.
The study was based on several assumptions. The base assumption is that a glass from a IGU in stock has the technical quality to be used for remanufacturing right away. This study does not take into account that further industrial processes might be necessary to improve the technical properties suchas bending strength of used flat glass, enabling Refurbish, Remanufacturing et cetera. Some process steps like work force or the impact of the IGU edge seal and processing steps like disassembly on the former site or cleaning were neglected. More data needs to be collected in order to decide in the future if those assumption remain valid.
In the future, more complex studies that account for RLT and its impact on the emissions of a building throughout a given lifespan have to be considered, to evaluate the benefit of postponing obsolescence on the building scale.
In order to better assess the applicability of R-strategies to IGUs, further studies on technical feasibility and legal issues will be carried out by Fachverband Konstruktiver Glasbau (FKG). For the presented case study further ecological indicators, such as the energy consumption or environmental pollutionshould be taken into account in order to be able to assess the sustainability of the individual scenarios more detailed. In combination with the results of the other working groups of the FKG, a recommendation for action will be drawn up on how to deal with the re-use of existing glazing.
References
Bakker, L. G. (2019). Potential impact of high Performing Glazing on Energy and Savings in Europe: TNO-Report 2019 R10442.
Brundtland, G.H. (1987) Our Common Future: Report of the World Commission on Environment and Development. Geneva, UN-Dokument A/42/427
Beerkens, R., Kers, G., & van Santen, E. (2011). Recycling of Post‐Consumer Glass: Energy Savings, CO 2 Emission Reduction, Effects on Glass Quality and Glass Melting. In C. H. Drummond (Ed.), Ceramic Engineering and Science Proceedings. 71st Conference on Glass Problems (pp. 167–194). Wiley.
Conversio Market & Strategy GmbH (2023). Abfallpotenziale des Altfensterrecycling. Retrieved February 19, 2023, from Conversio Market & Strategy GmbH: https://rewindo.de/fensterbranche-will-wiederverwertungspotenziale-von-altfenstern-erhoehen/
Ellen McArthur Foundation (2013). Towards the circular economy.
European Commission (2008). DIRECTIVE 2008/98/EC.
Geboes, E., Galle, W., de Temmerman, N.: Make or break the loop: a cross-practitioners review of glass circularity. Glass Struct. Eng. (2022). https://doi.org/10.1007/s40940-022-00211-y
Glass for Europe (2023): Reuse, remanufacturing, recycling: the case of glass for buildings. https://glassforeurope.com/wp-content/uploads/2023/12/Finalpaper_Reuse_remanufacturing_recycling_PDF.pdf
Hartwell, R., & Overend, M. (2019). Unlocking the Re-use Potential of Glass Façade Systems. Glass Performance Days Conference Proceedings.
ift-Rosenheim (2019). Recycling von Flachglas: Analyse des Ist-Zustandes und Ableitung von Handlungsempfehlungen. ift-Rosenheim; Fraunhofer ISC.
José Potting, Marko Hekkert, Ernst Worrell and Aldert Hanemaaijer. CIRCULAR ECONOMY: MEASURING INNOVATION IN THE PRODUCT CHAIN.
Kirchherr, J., Reike, D., & Hekkert, M. (2017). Conceptualizing the circular economy: An analysis of 114 definitions. Resources, Conservation and Recycling, 127, 221–232.
McDonough, W., Braungart, M.,(2001) The Next Industrial Revolution. In Sustainable Solutions: Developing Products and Services for the Future. Greenleaf Publishing Ltd, Sheffield, United Kingdom.
Morseletto, P. (2020). Targets for a circular economy. Resources, Conservation and Recycling, 153, 1–12.
Potting, J., Hekkert, Marko, Worrell, E., & Hanemaaijer, A. (2017). Circular Economy: Measuring Innovation in the Product Chain.
Rota et al 2023: Towards a quality protocol for enabling the reuse of post-consumer flat glass. Glass Struct. Eng. (2023) 8:235–254. https://doi.org/10.1007/s40940-023-00233-0
UN environment programme (2019). Emissions Gap Report 2019.
Von Houwald, Wortner, Kreißig, Peters (2012) Entwicklung von Umweltproduktdeklarationen für transparente Bauelemente – Fenster und Glas – für die Bewertung der Nachhaltigkeit von Gebäuden
Appendix
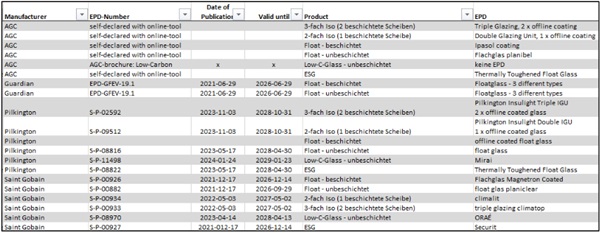
