Large series for the automotive and furniture industries are today made almost without exception on horizontal tempering machines. Smaller runs for special vehicle manufacturers and the construction industry are still made on older, vertical machines, but with developments in batch bending and tempering technology, these sectors are also increasingly switching to horizontal tempering.
Tempering that uses a glass bending furnace gives unbeatable advantages in the production of large pieces of architectural glass with high optical quality requirements.
The bending and tempering process creates the properties desired for glass, such as strength, using controlled heat processing. Heating the glass to 615-650 ºC, followed by rapid cooling, creates residual compressive stress on the surface of the glass and a corresponding residual tensile stress in the interior. The resulting stress balance gives glass the desired properties. Tempered, bent glass withstands mechanical strain 4-5 times better than bent annealed glass. This load-bearing ability makes tempered glass suitable for many places that require mechanical strength. Tempered bent glass can also withstand much greater variations in temperature than normal glass. This capability makes bent tempered glass more suitable for facades than laminated glass, for example. Another benefit is increased safety. Tempered glass shatters into small pebble-like pieces rather than larger sharp pieces.
Tempered, bent glass can be further upgraded, by laminating or building insulated glass units, for example. Silk screen printing gives added value and can be combined with bent tempered glass. All pyrolytically coated (hardcoat) glasses can be bent and tempered. Some soft coated glasses can also be bent and tempered.
Bending and tempering furnaces can also be used to make heat strengthened glass. Heat strengthened glass is not as strong as tempered glass, but it has other properties that make it more suitable in certain usage.
Whatever the method, the bending and tempering process always consists of the following stages:
a) loading (in moulds or on a conveyor)
b) preheating and heating (620-640ºC)
c) bending to the required form
d) tempering and chilling
e) unloading
The glass is loaded onto a roller conveyor or, if bending takes place inside the furnace, into a mold or tooling system.
In the furnace the glass is heated sufficiently so that it can be bent and tempered (615-650 ºC). In tempering machines where bending takes place in the furnace, the glass is heated on the mold or compound tooling system and can then be bent in the furnace. In most cases electric heating is used, so most of the heat energy is transferred to the glass by radiation.
With the roller hearth furnace, bending takes place in a separate bending section, and in practice the glass needs to be overheated to compensate for the cooling that takes place during bending. On the other hand, bending outside the furnace makes it possible to build complex adjustable molds
Rapid cooling (tempering) follows bending, and this creates the desired tension in the glass. Air is blown at a chosen pressure onto the surface of the glass through nozzles, so that the glass cools down in the required manner. To ensure even cooling, the glass oscillates between the nozzles during tempering. The speed of cooling, in other words the pressure, is chosen mainly according to the thickness of the glass. After tempering, once the temperature of the glass has fallen sufficiently, the final cooling can take place at full pressure.
Following cooling the glass is taken to the unloading area, in the mold or on the conveyor, depending on the type of machine.
Choose the right machine for the right task
No universal machine or concept exists for bending and tempering. Where the glass is to be used, and the properties required, determine the method to be used. Because of this, several different types of machine are available on the market, carrying out the stages in the process mentioned above in different ways. However, all these machines have a common basic structure: they all have a furnace, for heating the glass, a mould, in which the glass is bent, and a quenching section, in which the bent glass is tempered. The machines can be divided into two main types, according to their structure and method of working:
a) Roller hearth furnaces
b) Bending and tempering furnaces
Horizontal Roller Hearth Furnaces
This technology derives originally from the flat tempering furnace. The system is built round a roller conveyor, that conveys the glass from the loading area through the furnace, the bending section and the quenching section to the unloading area. Once a batch is ready in the loading area it is conveyed into the heating chamber. As soon as the glass reaches the required temperature it is taken to the bending section for shaping and then to the quenching section for tempering and cooling. The shape can be obtained either by gravity or by pressing between two molds. Gravity benders can be further divided into two categories: moldless systems for cylindrical bending and bending in one direction, and mold systems for spherical bending and compound bending.
Initial investment costs for horizontal roller hearth furnaces are usually high, but their output is also high. For this reason they are mainly used in long series production for OEM automotive glass, furniture, shop fixtures, shower doors, domestic appliances etc.
Horizontal Bending and Tempering Furnaces
This is another new technology, derived from bending and annealing furnaces. The glass is loaded in a mold or a molding system, and then the mold and the glass are heated and bent in a bending oven and then taken to the chiller for tempering and cooling. Gravity bending on a mold or a special tooling system is used to give the shape.
The horizontal bending and tempering furnace requires a relatively low initial investment. Since it has a low to medium rate of output, it is mainly used for short and medium runs, for façades, skylights and interior architecture. Bending the glass inside the furnace eliminates the need for overheating, so the optical quality is very high. This gives clear advantages when bending large pieces of glass for buildings where optical quality is a key issue.
Rainbowmaker, new batch horizontal tempering machine with a bending furnace
The Rainbowmaker TSF CombiT is the first horizontal tempering machine with a bending furnace that can make glass of sufficiently high optical quality for buildings. The design criteria set for the machine were as follows: ability to make as wide a range as possible of architectural glass; low investment costs and low mold costs; and an operating method suitable for small series. The machine was originally developed back in 1993, but it is only in the past two years that it has been upgraded to completely meet market demands for glass size and capacity.
Market requirements formed basis for design
A careful study was made of the markets for architectural glass, to ensure that the choice of operating principle for the machine and its development were based on correct information. This study showed that a machine designed for architectural glass should meet the following minimum requirements:
• Glass size at least 2000x3000 mm
• Glass thickness 6-12 mm, 15 mm and 19 mm desirable
• Shape mostly cylindrical
• Bending radius 400 mm - 25 000 mm
Production runs for architectural glass are mainly small and medium-size series, from batches of a few pieces to batches of a few hundred items. This places strict demands on changeover times; a fast changeover time for the radius is essential if small series production is to be profitable.
The end product has to comply with international standards. Since separate standards have not been drawn up for bent architectural glass, the standards for flat tempered glass are applied where possible. In most cases tests for the degree of tempering and for shattering are carried out in accordance with these standards, precision of shape is defined in accordance with factory norms, and optical quality is defined either in accordance with factory norms or on an individual case basis. The Heat Soak test follows the same practice as for flat tempered glass.
During the market study it was observed that glass was not available with sufficiently good optical quality and in sufficiently large sizes. So particular attention was paid to optical quality. Selecting a design that utilized the bending furnace removed a typical problem of the roller hearth furnace, that the glass has a wavy appearance. This design also does away with the roller marks on the surface of the glass, another typical problem with the roller hearth furnace, caused by the rapid preheating of the glass. A third problem with methods that have the bending section outside the furnace (roller hearth furnaces, upright machines) is that, to compensate for the glass cooling down during bending, it is necessary to overheat the glass in the furnace. This overheating generally weakens the optical quality of the glass so much that it is no longer acceptable to the architects. The Rainbowmakers method of bending the glass in the furnace does away with this problem and gives outstanding optical quality.
Advanced technology in every respect
The Rainbowmaker TSF CombiT is a horizontal tempering machine that bends in the furnace and meets the criteria listed above. The standard machine is extremely compact and simple and can be installed on the floor without any extra foundations. It consists of a heating and bending furnace, a mobile quenching section, and a mold in which the glass is taken into the furnace, formed to the required radius and then taken to the quenching unit for tempering. During loading the chiller is moved back so that the glass can be loaded into the mold with a hoist. The mold with the glass is then moved into the furnace, where it is heated and bent. When the bending is completed and the tempering temperature has been reached, the glass in its mold is moved into the chiller for tempering and cooling. The chiller is then moved back again, so that the mold can be emptied and reloaded.
It is possible to optimize the heating and cooling times to achieve a typical total run time, for 6 mm glass for example, of less than 20 minutes. The capacity of the standard machine is limited by the heating time. The furnace can be built as a throughput model, so that the glass is moved into the furnace at one end and out into the chiller at the other end. It is then possible to have three pieces of glass simultaneously in the process, which doubles capacity, with one piece in the furnace, one in the chiller and one being loaded.
The furnace is heated electrically, so controlling the heating and bending is simple and precise. The heating of the glass can be controlled in bands from both top and bottom. The operator chooses the appropriate heating profile and heating curve and makes sure that these suit the glass being processed. For tempering to be successful it is essential that the glass has an even temperature when it enters the chiller. An automatic power control system ensures that the surface of the glass has an even temperature, balancing the temperature of the furnace in accordance with measurements taken and given parameters.
A mold is always necessary in a bending furnace. The mold can be a fixed, compound tooling or adjustable mold. In in-furnace bending processes the complete mold enters the furnace, so both fixed and compound tooling molds can be used. For the Rainbowmaker, using a patented compound tooling mold cuts mold costs to a minimum. When the radius changes it is not necessary to change the entire mold, only the form giving bows. This has resulted in a simple, reliable and low cost bending tool.
The chiller has to be set for each radius separately. This task has been made fast and simple with the use of guiding curves and quick fasteners in the nozzle section. Rainbowmakers fitted with a drive-through furnace are supplied with an automatically adjusted chiller, making it possible to run different radiuses continuously, without separate changeover times.
The Rainbowmaker is a fully automated furnace. The Windows-based interface is graphical and extremely easy to learn and use. Particular attention has been paid to the choice of materials and components, to make the machine as easy to service as possible.
Glassrobots Oy is supplying several bending and tempering machines this year to the worlds leading glass bending companies in the USA, Europe and the Far East. Some of these deliveries also include bending technology transfers and maintenance agreements.
Period of change in the use of bent, tempered architectural glass
Rather little use is still made of bent tempered glass in construction, and what is used is mainly produced on vertical tempering machines. This method has its weaknesses, however, and these machines will in the near future be replaced by new horizontal machines. Since even in the future roller hearth machines will be financially viable mainly for making large series, it will be necessary in smaller runs, in places that require good optical quality (facades, large display windows etc) to use bending and tempering machines.
The use of bent tempered glass is however increasing rapidly. Increasing the availability of the glass and development of related items and systems (frames, bent insulating glass, glass with bolted on fittings) will make this option even more competitive. The work on standards is advancing all the time; draft and factory standards already exist for bent glass.
In many cases in the past tempered glass was replaced by laminated, because it was much more readily available. But the availability of bent tempered glass is constantly improving. On the other hand, tempering and laminating are not mutually exclusive techniques; instead they rather complement each other. There are places where it is necessary to use tempered glass (with bolted structures, for example), and places that require laminating (eg. skylights). An increasing number of structures are being specified that require tempered and heat strengthened glass that is laminated.
Large items of tempered architectural glass have been available from established companies supplying bent architectural glass, since they have tried to retain their markets by offering a full range of glass: bent annealed, bent laminated, bent tempered and combinations. A second group that is asked to supply bent architectural glass is companies that temper flat architectural glass; these are also increasingly selling the full range of glass, to ensure they win orders.
by Juha Karisola, Director, Sales & Marketing at Glassrobots Oy
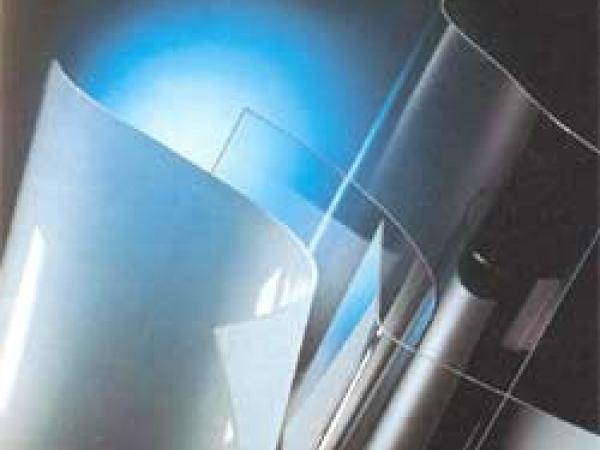
Date: 29 June 2008
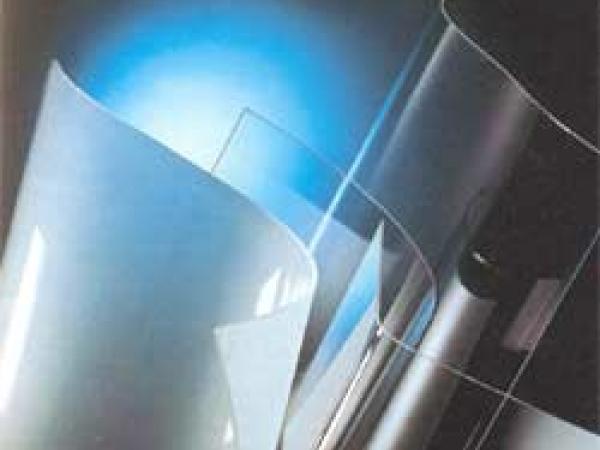
