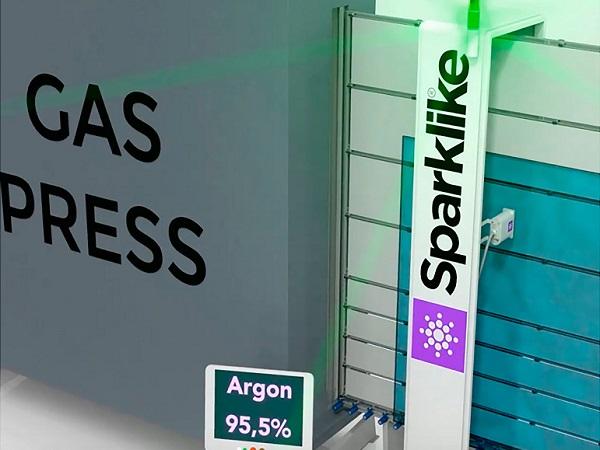
Date: 8 June 2018
All Sparklike Laser™ devices are developed and manufactured in Finland.
Sparklike Laser™ Online device was developed by Mr. Kai Niiranen, who has held the position of Sparklike’s R&D Engineer since 2011. The devices are based on Sparklike’s patented and proprietary technology. This laser based technology (TDLAS) means that the devices measure oxygen, and the results are converted to argon, krypton and other insulating gases.
Mr. Niiranen developed the Sparklike Laser™ Online device since the customers were looking for a way to conduct
automated quality control. The online version is a custom-made solution, where Sparklike Oy delivers measuring components that are integrated directly into the insulating glass line.
“The ever-growing popularity of Sparklike devices™ is due to the fact that they offer the IG and window manufacturers, as well as test laboratories the possibility to analyse the gas concentration of IG units in a fast, economic and non-destructive way. Furthermore, with Sparklike devices™, the IG manufacturers are able to confirm the proper functioning of the gas press, in an automated way. Something that was not possible before. This, on the other hand, ensures that the end-user receives an IGU with the gas concentration that complies with industry norms, regulations, as well as customer expectations,” Mr. Niiranen says.
The equipment itself consists of three different parts: a 16-kilo main unit, a 6-kilo measuring head, as well as of a handy 10,1” touch screen display that comes with a pen.
Furthermore, every device comes with the Laser Software by Sparklike, which is run in the Windows 10 IoT Enterprise operating system. “To enhance the device's user-friendliness, there are several language options available for the software: English, German and French. Other language options, such as Spanish and Italian, will soon be available,” Mr. Niiranen continues.
What makes Sparklike Laser™ Online an automated analysis device, is the possibility to create an integration between the device and the IG line. This communication is done by using an Ethernet port. The communication itself is HEX coded ASCII text.
The system developed by Mr. Niiranen is reading the port and sending data back according to the communication protocol. To ensure an easy-to-use protocol, all the commands and replies have pre-determined lengths.
In addition, specific commands enable the measurement of the IGU in sync with the production line. This, on the other hand, allows a much shorter measurement cycle. In this way, the measurement time can be reduced even down to 9 seconds when measuring double glazed units, and all the way to 15 seconds when analyzing triple glazed IGU's.
In other words, the measurement time depends on the settings and the nature of the IG structure. Finally, the data logging capacity is SSD Storage (15 GB), USB/Network transfer. Therefore, the data logging capability of the devices is virtually unlimited.
For more info on Sparklike Oy and their devices, please visit www.sparklike.com.
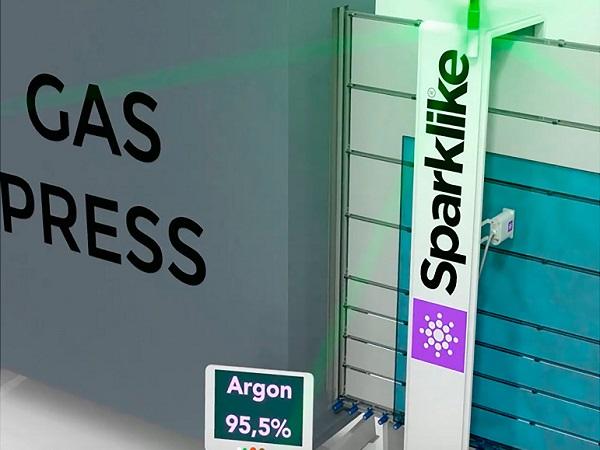

Add new comment